Горелка на отработке: чертежи, схема, принцип работы
При эксплуатации автомобильного и тракторного транспорта образуется значительное количество отработанного масла. Согласно экологическому законодательству, это масло нельзя выливать на землю или в канализацию, а необходимо утилизировать на специальных предприятиях, неся при этом ощутимые для бюджета издержки. Изобретение Роберта Бабингтона позволяет решить эту проблему, используя отработку для отопления помещений или для нагрева технологических установок. Его горелка, будучи несложной по конструкции и доступной для изготовления домашнему мастеру, отличается надежностью и высокой энергоэффективностью.
Горелка на отработкеЧто представляет собой горелка Баббингтона
Конструкция горелки Баббингтона на жидком топливе достаточно проста для того, чтобы ее можно было своими руками изготовить в домашней мастерской. Горелка на отработке имеет следующие основные узлы и детали:
- емкость с отработкой;
- топливопровод;
- топливный насос; включенный в разрыв топливопровода;
- полусфера с отверстием малого диаметра;
- воздушная форсунка, выходящая в это отверстие;
- поддон для стекающего топлива.
Схема устройства горелки
Топливопровод оканчивается на некоторой высоте над полусферой, отработка стекает по ней и испаряется, пары вовлекаются в воздушную струю, образуя топливную смесь. Не успевшее испариться топливо попадает в поддон, а из него по системе труб — обратно в топливную емкость.
Несмотря на кажущуюся простоту устройства, для его эффективной и, главное, безопасной работы требуется точно изготовить основные детали и правильно расположить их друг относительно друга. Поэтому лучше скачать готовые чертежи горелки Бабингтона и следовать указанным в них размерам.
Принцип работы
В большинстве известных масляных горелок масляно-воздушную смесь подается через жиклер под давлением. В отличие от них, в системе Бабингтона масло подается насосом малого давления и свободно стекает по поверхности, имеющей форму сферы или близкой к ней. Топливо образует тонкую пленку и испаряется, увлекаемое потоком воздуха, подаваемым под давлением в небольшое (до 0,3 миллиметра) отверстие в центре сферы. Пары масла и воздух перемешиваются, образуя факел топливной смеси. Этот факел поджигается и нагревает то, что следует нагревать — стенки печи или жидкостный теплообменник бойлера.
Принцип действия
Часть масла не успевает испариться и сгореть и стекает ниже отверстия, попадая в поддон для сбора топлива. Далее отработка перетекает из поддона в топливный бак и используется повторно.
Для повышения текучести и испаряемости отработки ее подогревают. Подогретая отработка распыляется на капельки меньшего объема, что также повышает качество топливной смеси и общую эффективность устройства.
Как сделать горелку на отработке
Для того чтобы сделать горелку на отработанном масле своими руками, потребуется:
- крестовина для водопроводных труб с внутренней резьбой, диаметром 2 дюйма;
- кусок двухдюймовой трубы с нарезанной внешней резьбой, длиной 15-20 см;
- медная трубка диаметром 10 миллиметров для подачи топлива;
- металлическая трубка для подачи воздуха;
- компрессор 2-4 бар;
- масляный насос;
- фитинги для присоединения топливопровода;
- вентиль для топливной магистрали для регулировки поступления топлива;
- полусфера — латунная мебельная ручка или сферическая гайка.
Детали для сборки горелки на отработке
Насос подойдет от любого легкового автомобиля или мотоцикла, его приводной вал надо будет соединить с электродвигателем. Компрессор лучше всего взять от хододильника- они приспособлены к продолжительной работе.
Трубка вкручивается в одно из отверстий крестовины, в противоположное ввинчивается заглушка с закрепленной на ней полусферой таким образом, чтобы она находилась в центре крестовины. Сзади через заглушку к полусфере подводится трубка подачи воздуха.
В верхнее отверстие крестовины крепят топливопровод, из которого отработка будет капать на полусферу. Нижнее отверстие выводят в поддон для сбора несгоревшего масла. Все основные узлы горелки на отработанном масле, собранной своими руками:
- крестовину в сборе;
- компрессор;
- топливный бак;
- насос;
- блок питания и управления;
закрепляют на раме, сваренной из стального уголка.
Горелка на отработке своими руками
Делаем форсунку горелки на отработке
Форсунка — самый ответственный элемент конструкции горелки для отработки, собранной своими руками. Точность ее изготовления определяет топливную эффективность и безопасность системы. Чем больше отверстие форсунки-тем мощнее получится горелка.
Кроме того, очень важно, чтобы канал поступления воздуха был ровным и гладким — тогда форма факела будет оптимальной. Наилучшим вариантом будет использование готового жиклера с отверстием нужного диаметра, например, от газовой плиты или карбюратора.
Но можно и просверлить отверстие на сверлильном станке. Использование ручной дрели не рекомендуется из-за трудности обеспечения соосности отверстия.
Форсунка
Полусферу можно сделать из мебельной ручки подходящего диаметра или из полусферической гайки. Форсунку надо смонтировать заподлицо с поверхностью полусферы. В самом крайнем случае используют просто выгнутую на правиле полоску металла с приваренным к ней жиклером.
Мощность получившейся горелки можно с известной погрешностью оценить заранее. Горелка с одним отверстием 0,3 мм сможет выдать примерно 16 квт тепловой мощности. Если требуется большая мощность, то лучше не увеличивать диаметр отверстия, а сделать их несколько, на расстоянии не менее 8 мм друг от друга. Практика показала, что из отверстия больше 0,3 мм воздушный поток становится турбулентным, хуже захватывает пары отработки, и тепловая эффективность устройства падает.
История появления горелок на отработанном моторном масле
Горелки на отработке получили массовое распространение в нашей стране во второй половине 20 века. Население искало недорогой способ обогрева помещений.
Использование отработки, которая не стоила практически ничего, было весьма выгодным по сравнению с покупкой угля, дров и даже торфа, не говоря об отоплении газом или электричеством. Из-под рук домашних мастеров выходили более или менее экономичные и безопасные устройства.
Принцип их действия напоминал широко известный керогаз, работавший на керосине. Керосин испарялся, а пары его сжигались в отдельной пиролизной камере.
Главной проблемой таких устройств была сильная копоть и резкий неприятный запах из-за неполного сгорания топлива. Чтобы избежать этого, топливо сначала разлагали на фракции при высокой температуре, а потом дожигали эти фракции по отдельности.
В 1969 году английский изобретатель Роберт Баббингтон получил патент на свою печь, первоначально предназначая ее для работы на солярке. По истечении срока действия патента конструкция стала доступна для повторения, как промышленными предприятиями, так и домашними мастерами. Самодельная горелка на отработанном масле конструкции Баббингтона намного экономичнее и безопаснее других конструкций горелок.
Достоинства и недостатки горелки на жидком топливе
Горелка на отработке конструкции Баббингтона имеет целый ряд преимуществ:
- Простота конструкции, отсутствие подвижных частей.
- Доступность для изготовления в домашних условиях.
- Доступность в Сети хорошо просчитанных и точных чертежей.
- Исключительная дешевизна топлива. Предприятия, владеющие большим парком автомобильной и тракторной техники, смогут существенно сэкономить на отоплении и одновременно на утилизации отработанного масла.
- Высокая энергоэффективность. Другие горелки на отработке тратят заметно больше топлива в расчете на один киловатт тепловой энергии.
- Малые габариты позволяют встраивать горелку в уже существующие системы отопления без их существенных переделок.
- Высокая степень пожарной безопасности.
Кроме указанных достоинств, горелка обладает и рядом недостатков.
- Чувствительность топливного тракта к загрязнениям. Отработку обязательно придется отфильтровать.
- Необходимость электропитания для работы топливного насоса и воздушного компрессора.
- Неприятный запах при работе. Горелку лучше не использовать в помещениях постоянного пребывания людей или сельскохозяйственных животных либо потребуется обеспечить надежный отвод продуктов горения.
Горелка на отработке в быту
В целом достоинства значительно перевешивают недостатки, и горелка Баббингтона приобретает все большую популярность.
Котел на отработанном масле с водяным контуром своими руками
Печи, сжигающие жидкое топливо, известны ещё с начала прошлого века. Правда, тогда они служили в основном для нужд промышленности. В быту же агрегаты, работающие на дизеле или мазуте, получили широкое распространение в 60–80 годы. Именно в то время продукты нефтепереработки можно было покупать за копейки или же вообще доставать бесплатно. Несмотря на значительное подорожание энергоносителей, так же дёшево отапливать свой дом можно и сейчас. Можно сказать, что горючее для этого лежит просто под ногами, а точнее, на каждом автосервисе. Слитое отработанное масло горит не хуже дизтоплива, к тому же владельцы мастерских отдают его практически даром. Кстати, котёл для его сжигания необязательно покупать. Простой и надёжный агрегат с водяным контуром можно построить своими руками, используя материалы, которые найдутся у каждого хозяина.
Устройство и принцип действия котла, использующего отработанное масло
Самодельный котёл отопления, работающий на отработанном автомобильном масле
Слитые автомобильные масла являются многокомпонентными, сильнозагрязнёнными веществами, которые к тому же ещё и плохо горят. Можно сказать, что как горючее отработка сама по себе «не очень», поскольку кислород просто не в состоянии окислить всё то химическое разнообразие, которое в ней находится. Если же расщепить масло на более простые составляющие, то сжечь их будет намного проще.
Метод разложения известен современной науке давно. Пламенное разделение, или, если говорить по-научному, пиролиз, применяется для получения простых легковоспламеняющихся веществ из любого топлива — нефти, угля, дров и т.
Процессы, протекающие внутри печи на отработке, обеспечивают высокую температуру и полноту сгорания топлива
В первом случае горючее поджигают в резервуаре, после чего оно начинает активно испаряться. Эффективное перемешивание и получение однородной газовоздушной смеси обеспечивается за счёт Кориолисовой силы, поэтому важен точный расчёт диаметра и высоты камеры сгорания. Пары топлива поднимаются по вертикальной трубе с многочисленными отверстиями, через которые насыщаются кислородом воздуха. В верхней части камеры сгорания находится перегородка, которая нужна, чтобы снизить скорость газа и отделить зону окисно-азотного дожигания. Именно в ней опасные химические соединения вступают в реакцию с оксидами азота и распадаются на безвредные вещества.
Так называемый метод саможога, бесспорно, обладает привлекательной простотой и надёжностью, однако, резервуар с горящим маслом не позволяет говорить о безопасности. Для того чтобы устранить этот недостаток потребуется усложнять конструкцию отопительного агрегата.
Эффективность сжигания отработки значительно повышается при использовании горелки специальной конструкции
Второй способ предусматривает образование зон пиролиза, сгорания и дожигания прямо в факеле пламени, а для этого нужна горелка специальной конфигурации. Чтобы топливо окислялось полностью, форсунка должна обеспечивать многоступенчатое образование газовоздушной смеси. В таком устройстве первичное движение потока топлива обеспечивается компрессором.
Читайте также нашу статью об изготовлении печки-буржуйки на отработанном масле: https://aqua-rmnt.com/otoplenie/bani-i-garazh/pechka-burzhujka-svoimi-rukami.html.
Типы конструкций на отработке
В зависимости от области применения, котлы, использующие в качестве топлива отработанное масло, можно разделить на три группы:
- бытовые печи;
- водонагревательные агрегаты;
- отопительные котлы.
Бытовые печи устанавливают в помещениях, которые по ряду причин нельзя оборудовать водяным отоплением.
Бытовая масляная печь
Водонагревательные агрегаты на уровне модуля для дожигания газов имеют специальную платформу, на которую опирается ёмкость с водой.
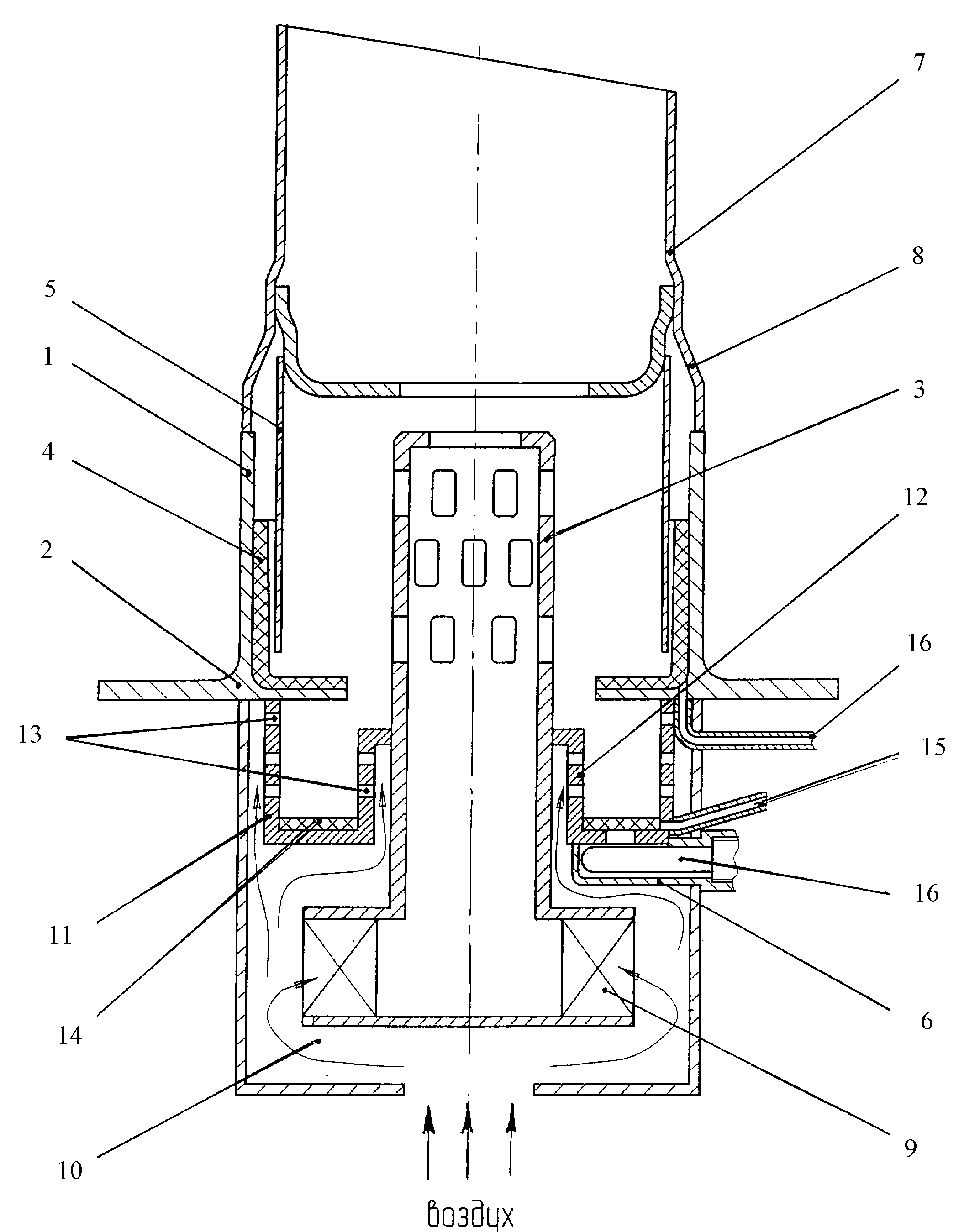
Ёмкость, установленная на уровне зоны дожигания, превращает печь на отработке в мощный водонагреватель
Отопительные котлы используются для подключения к водяным системам обогрева, поэтому оборудуются устройствами дожигания отработанных газов, фильтрами и устройствами безопасности. Несмотря на все меры предосторожности, оборудование для отопления отработанным маслом рекомендуется устанавливать в отдельных помещениях или пристройках.
Нагрев воды в отопительных агрегатах обеспечивает теплообменник, установленный в зоне горения топлива.
Котёл с водяным контуром спирального типа обеспечит работу отопительной системы загородного дома
Нередко агрегаты, работающие на слитом масле, дублируют устройствами, использующими электричество, газ или твёрдое топливо. Это обеспечивает функциональность инженерных систем в случае перебоев с доставкой отработки.
Обратите внимание на материал, в котором рассматриваются варианты обогревателей для гаража: https://aqua-rmnt.com/otoplenie/bani-i-garazh/kakoj-obogrevatel-luchshe-dlya-garazha.
html.
Изготовление котла, работающего на отработанном топливе
По описанным выше схемам разработаны и успешно эксплуатируются несколько типов котлов. Кроме того, для работы на жидком топливе можно приспособить любой твердотопливный или газовый отопительный агрегат. Расскажем о двух наиболее распространённых конструкциях, которые можно изготовить самостоятельно.
Чертежи отопительных агрегатов
Чертежи, которые мы предоставляем вашему вниманию, проверены на реально работающих печах, поэтому их уверенно можно использовать для собственных проектов.
Двухобъёмный
Эта конструкция состоит из двух цилиндрических камер, соединённых между собой отрезком толстостенной железной трубы с отверстиями для проникновения воздуха.
Чертёж двухобъёмного котла с прямоугольными рабочими камерами
Чертёж цилиндрического двухобъёмного котла
Нижний отсек одновременно является ёмкостью для горючего, испарителем и зоной первичного горения. Для заливки топлива, розжига и регулирования притока воздуха на его верхней плоскости вырезано отверстие, которое можно полностью или частично перекрывать при помощи лючка поворотного типа. Снизу печка оборудована ножками, которые обеспечивают устойчивость конструкции и создают зазор между её днищем и полом.
Схема котла с открытой камерой сгорания
В верхнюю плоскость топочного отсека вварена труба с отверстиями. Этот полый цилиндр представляет собой дожигающую камеру. В ней происходит пиролизное разложение и сгорание испаряющегося топлива (вторичное дожигание). На верхнем срезе перфорированной трубы смонтирована практически такая же ёмкость, как и снизу. Перегородка, которая разделяет её внутреннее пространство на две зоны, снижает скорость продуктов горения и обеспечивает полноту их окисления соединениями азота. Кроме того, верхняя камера является ещё и теплообменником, который работает как инфракрасный и конвекционный нагреватель.
Смонтированная на верхнем модуле дымовая труба создаёт необходимую тягу и отводит остаточные продукты сгорания наружу. Чтобы обезопасить процесс доливки отработки в нижний бачок, к нему приваривают трубку, соединённую с отдельной ёмкостью. Залитое в печку масло поджигают при помощи ветоши, смоченной в бензине или керосине. После этого лючком регулируют приток воздуха в зону первичного горения.
Установив на вертикальной трубе водяную рубашку или контур, получают котёл, который можно с успехом использовать в системах отопления или горячего водоснабжения. При этом важно оставить зазор до перфорированного цилиндра не менее 50–70 мм, чтобы обеспечить свободный приток воздуха в зону вторичного горения.
С пламенной чашей
Чертёж простого котла с пламенной чашей приведён ниже. Его размеры обеспечивают тепловую мощность около 15 кВт. При этом требуется не более 1.5 литра использованного автомобильного масла в час. Воздух в зону горения поступает с помощью небольшого вентилятора или турбины. Подача отработанного топлива происходит порционно, для чего бак с маслом оснащается вентилем, которым можно регулировать количество горючего или полностью прекратить его подачу.
Чертёж котла с пламенной чашей
Для дожигания паров отработки центральная труба оснащается системой отверстий и прорезей. Благодаря такой конструкции, вокруг пламенной чаши происходят такие же процессы, как и в двухобъёмной печи. Горючие газы удаляются через дымоход, установленный в верхней части камеры сгорания. При его обустройстве следует избегать резких поворотов и углов, а высота дымовой трубы должна составлять не менее 4 м. Это обеспечит тягу, достаточную для удаления продуктов горения и обеспечит безопасную эксплуатацию отопительного агрегата.
Схема котла, изготовленного из газового баллона
Печь с пламенной чашей представляет собой закрытое устройство с принудительной подачей воздуха. Это способствует безопасности эксплуатации, а также даёт возможность легко и просто обустроить водяную рубашку. На схеме показан рабочий проект описанного выше котла, в качестве корпуса которого можно использовать бытовой газовый баллон.
Необходимые материалы
Для изготовления водяного отопительного котла с пламенной чашей понадобится не только ёмкость для изготовления корпуса, но и другие материалы (позиции на представленной выше схеме и в списке соответствуют друг другу).
- Пропановый баллон объёмом 50 литров.
- Металлическая труба Ø100 мм толщиной 2–3 мм для изготовления дымовой трубы.
- Железная труба Ø100 мм толщиной 5–6 мм, которая понадобится, чтобы сделать горелку.
- Стальной лист толщиной не менее 5 мм для разделения камеры сгорания и испарительной зоны.
- Металлический лист толщиной 3–4 мм для изготовления козырька, предназначенного для снижения скорости газов.
- Тормозной диск диаметром не менее 20 см от любого автомобиля.
- Соединительная муфта (та же 100-мм труба, только разрезанная по всей длине) длиной 100 мм.
- Стальная труба Ø15 мм для подачи масла к чаше.
- Шаровой кран размером ½ дюйма.
- Топливный шланг из маслостойкого огнеупорного материала.
- Бак для отработки любого типа.
- Уголок или стальной профиль для изготовления ножек.
- Крышка из стали толщиной 4–5 мм.
- Стальной лист толщиной не менее 3 мм для изготовления водяной рубашки.
- Патрубки с резьбой Ø2˝ для присоединения котла к системе отопления.
Не забудьте и о том, что для защиты от коррозии и улучшения внешнего вида котёл необходимо будет покрасить, поэтому купите преобразователь ржавчины, грунтовку, растворитель и эмаль для работы по металлу. Кроме того, для герметизации соединений понадобятся уплотнительные материалы — сантехнический лён и специальная паста.
Форма, толщина и размеры газового баллона делают его отличной заготовкой для изготовления котла на отработке
Инструменты для работы
В процессе работы над котлом понадобится разнообразный электрический и ручной слесарный инструмент. Вот список того, что потребуется достать из закромов, приобрести, или занять у друзей:
- сварочный аппарат — лучше всего использовать трансформаторный агрегат постоянного тока или инвертор, поскольку предъявляются высокие требования к качеству сварных швов;
- электрическая дрель и набор свёрл для работы по металлу;
- угловая шлифовальная машина и два диска — отрезной и зачистной.
Разумеется, эти расходники должны предназначаться для резки стали;
- плашки для нарезания резьбы на трубах;
- электрический наждак;
- ключ газовый;
- рулетка;
- металлическая линейка;
- чертилка из высокоуглеродистой стали для разметки деталей перед их порезкой.
Поскольку придётся сверлить большое количество отверстий, обязательно надо подготовить ёмкость с водой для охлаждения инструмента. Кроме того, надо обеспечить безопасность сварочных работ, поэтому нелишне будет запастись огнетушителем.
Вам также может быть интересен материал, в котором описан процесс изготовления печи на отработке из газового баллона: https://aqua-rmnt.com/otoplenie/documents/pech-na-otrabotke-svoimi-rukami.html
Инструкция по изготовлению котла на отработке своими руками
- Поскольку даже в пустом газовом баллоне может оставаться взрывоопасная смесь из паров пропана и воздуха, резать его болгаркой или сверлить можно только после полного опорожнения.
Для этого необходимо газовым ключом отвернуть и снять вентиль. Затем ёмкость переворачивают вверх тормашками и сливают конденсат. Учтите, что эта жидкость отлично горит и обладает чрезвычайно едким запахом, поэтому работайте очень аккуратно. После вытекания жидкости заготовку возвращают в исходное положение и через верхнее отверстие наполняют водой — она полностью вытеснит остатки газа. После этого жидкость можно слить и проводить любые работы, не опасаясь возгорания или взрыва.
- При помощи угловой шлифмашины в баллоне вырезают проёмы шириной в треть диаметра. Если мерить по окружности, то их длина равняется 315 мм. Высота нижнего окна — 200 мм, а верхнего — 400 мм. Между проёмами необходимо оставить перемычку шириной 50 мм. Работу надо выполнять аккуратно, не допуская смещения диска, поскольку вырезанные металлические сектора пойдут на изготовления люков.
Подготовленные проёмы
Обратите внимание! Увеличенный размер верхнего окна нужен для того, чтобы в случае необходимости перевести котёл на твёрдое топливо.
Если же такой необходимости нет, то будет достаточно нижнего проёма. К слову, в этом случае облегчается монтаж кожуха водяной рубашки.
- К люку, который получился при формировании проёма теплообменника, приваривают петли и задвижку, после чего деталь возвращают на место.
- Из 4 мм стального листа по внутреннему диаметру баллона, который равняется 295 мм, вырезают кольцо. Отверстие, которое в нём надо сделать, должно соответствовать внешнему диаметру трубы для изготовления горелки (в нашем случае — 100 мм). Этот элемент послужит перегородкой между зоной горения и теплообменником.
Изготовление перегородки и её подгонка по месту
- От стальной толстостенной трубы Ø 100 мм отрезают заготовку длиной 200 мм.
- В нижней части детали делают сверления Ø12 мм на высоту 95 мм. Расстояния между отверстиями не должны превышать 40 мм — это позволит равномернее распределить поток газа на выходе из горелки.
Отверстия в горелке должны обеспечивать равномерный поток горящих газов во всех направлениях
Если кромки отверстий тщательно обработать напильником, то это даст возможность длительное время обходиться без их чистки.
Эта особенность связана с уменьшением шероховатости — частичкам сажи и грязи попросту не будет за что зацепиться.
- На горелку устанавливают вырезанное ранее кольцо и приваривают его непосредственно над отверстиями.
Установка перегородки на горелку
- Перегородку устанавливают между проёмами, на уровне верхнего среза камеры сгорания. Таким образом, в нижней части теплообменника будет сформирована ступенька, необходимая для удержания золы в случае работы котла на дровах.
Монтаж узла, разделяющего камеру сгорания и теплообменик
- Для изготовления чаши-испарителя можно использовать любую толстостенную ёмкость, желательно из жаропрочных сплавов. Как нельзя лучше для этих целей подходят чугунные тормозные диски от легковых автомобилей. Технологические отверстия в заготовке надо заварить. Для этого из стального листа вырезают две круглых детали, одна из которых будет дном, а вторая — колпаком. В крышке прорезают отверстие под соединительную муфту и окно для подачи отработки.
Отверстия в тормозном диске необходимо заглушить
- 150 мм отрезок стальной трубы разрезают «болгаркой» вдоль, после чего немного раздвигают стенки, увеличивая щель до 4–5 мм. Это позволит снимать чашу для очистки от остатков сгоревшего топлива.
Чаша с приваренным днищем
- К автомобильному диску приваривают днище, крышку и муфту, после чего узел устанавливают на горелку.
Муфта обеспечивает плотное присоединение чаши к горелке
- Из стального листа вырезают полосу размерами 400х640 мм, два полукольца с наружным диаметром 305 мм и внутренним — 299 мм и две полоски шириной 30 мм. С их помощью вокруг баллона формируют кожух водяной рубашки, обваривая всё сплошным швом.
Монтаж водяной рубашки
- В верхней и нижней части кожуха прорезают круглые отверстия диаметром не менее 40 мм и при помощи сварки монтируют патрубки подачи и отвода теплоносителя.
- Изготавливают крышку котла, в которую врезают дымовую трубу. Устанавливают крышку на котёл.
- В боковой стенке баллона делают отверстие, в которое под углом вводят трубу для горючего. Её нижний край срезают под углом, после чего получившийся излив устанавливают над окном подачи масла. После регулировки длины вылета, топливную магистраль необходимо приварить к котлу.
Установка топливной магистрали
- Нарезав на трубе для отработки резьбу, монтируют шаровой кран и присоединяют бачок для горючего.
Чтобы подсоединить к трубе шаровой кран, на ней нарезают резьбу
Выполнять проверку работоспособности котла можно не дожидаясь врезки в отопительную систему. Для этого в топливную ёмкость наливают отработку и открывают шаровой кран, пока масло не распределится тонким слоем по днищу диска. Сверху наливают небольшое количество керосина и поджигают. Подачу горючего регулируют, ориентируясь по скорости его вытекания и уровню в топочной чаше.
Видео: Изготовление отопительного котла из газового баллона
Обвязка. Дублирование печи на отработке электрическим агрегатом
Перед подключением котла следует продумать не только способ монтажа и точки размещения дополнительных устройств и запорно-регулировочной арматуры, но и способ вывода дымовой трубы наружу. Если она будет проходить через потолок, построенный с использованием легковоспламеняющихся материалов, то в нём устанавливают металлический пенал вдвое большего диаметра. Свободное пространство между трубами заполняют асбестом или другим негорючим материалом с хорошими теплоизоляционными свойствами.
Учитывая высокую опасность отопления жидким горючим, монтаж котла лучше всего выполнять в отдельном помещении с хорошей вентиляцией. Подиум под агрегат бетонируют или укрывают металлическим листом, который будет выступать за его контуры не менее чем на 1 метр. После установки котёл выравнивают по отвесу и только после этого приступают к подключению.
Простейшим способом обвязки котла является интеграция в гравитационную систему отопления. Несмотря на простоту, его надёжность очень высока, поскольку в этом случае отпадает потребность в циркуляционном насосе и устройствах автоматики. Тем не менее использование дополнительного оборудования позволяет ускорить доставку теплоносителя к потребителям и выровнять температуру во всех точках системы, что даёт экономию топлива и повышает комфорт. В этих целях на обратной магистрали перед самым входом в котёл устанавливают центробежный насос и расширительный бак мембранного типа. Он необходим для того, чтобы система не разгерметизировалась при повышении температуры и давления. К верхнему патрубку подсоединяют напорную магистраль, а для регулировки температуры потребителей перед каждым радиатором устанавливают термостатическую головку или другое регулирующее устройство (трёхходовой клапан, вентиль для уменьшения сечения подающей трубы и т. д.). Для удаления воздушных пробок в верхней точки системы монтируют воздухоотводчик.
Схема обвязки котла, работающего на отработанном масле
Обвязка агрегата, работающего на отработке, требует учитывать инерционность этого вида оборудования. Другими словами, изменение температуры теплоносителя происходит постепенно, поэтому агрегат обязательно оснащают предохранительным клапаном. Он позволит сбросить давление при его повышении до критического уровня. Неплохим способом обезопасить и выровнять температуру является последовательное подключение водонагревателя косвенного нагрева. Он послужит тем самым буфером, который возьмёт на себя лишнее тепло в случае избыточного роста температуры.
Выполняя подключение котла, на обратной и подающей магистрали устанавливают запорные вентили. Это даст возможность снять агрегат для ремонта без необходимости удаления теплоносителя из системы.
Когда хотят подстраховаться на случай нехватки отработанного масла, рядом с самодельным котлом устанавливается электрический. Подключить дополнительный агрегат можно двумя способами — последовательно или в параллель. Достоинство первого способа заключается в том, что нагретый с помощью пламенной чаши теплоноситель будет поступать в электрический котёл, который можно настроить на определённую температуру срабатывания. При уменьшении пламени горелки он будет включаться и повышать температуру воды до нужного значения. Недостатком подобного способа является увеличение длины магистрали, а также полная неработоспособность системы в случае демонтажа одного из котлов для ремонта.
Параллельное включение подразумевает независимую работу двух отопительных агрегатов и характеризуется отсутствием указанных недостатков. К сожалению, и этот способ не лишён минусов, один из которых — необходимость монтажа гидрострелки и точного согласования режима работы и подачи обратной магистрали. К тому же фитингов, труб и арматуры при параллельном включении пойдёт намного больше, что непременно приведёт к увеличению стоимости и усложнению монтажа.
Несмотря на все минусы, в любом случае включение котлов в каскад способствует повышению надёжности системы. Если же учитывать, что один из агрегатов будет периодически или регулярно работать на отработанном автомобильном масле, то это позволит ещё и неплохо сэкономить.
Видео: Автоматизированная работа агрегата с водяным контуром
Сегодня сжигание отработанного автомобильного масла является наиболее дешёвым и доступным способом утилизации. К сожалению, этот метод является не самым безопасным для окружающей среды, особенно при неполном сгорании топлива. Дело в том, что присадки и добавки, которые производители используют для повышения ресурса силовых агрегатов, являются вредными канцерогенными веществами. Котёл, который мы предлагаем к изготовлению, спроектирован с учётом сжигания отработки при максимальной температуре. Это способствует полному распаду химических составляющих на безопасные вещества. Поэтому, приступая к работе, будьте внимательны в расчётах и прислушивайтесь к советам и рекомендациям специалистов.
Благодаря разносторонним увлечениям пишу на разные темы, но самые любимые — техника, технологии и строительство. Возможно потому, что знаю множество нюансов в этих областях не только теоретически, вследствие учебы в техническом университете и аспирантуре, но и с практической стороны, так как стараюсь все делать своими руками. Оцените статью: Поделитесь с друзьями!Котел на отработке своими руками: руководство, схемы и чертежи
Устройство и принцип работы котла на отработке
Любые котлы, работающие на отработанном масле, функционируют по одному принципу. Внизу топки, находится масло, которое нагревают до момента появления пара. Легкие испарения стремятся подняться наверх, где смешиваются с воздухом и сгорают, при этом выделяя тепловую энергию. Она и идет на нагрев водяной рубашки, через стенки камеры сгорания.
Есть немаловажный нюанс – в отработанном масле всегда содержатся тяжелые металлы, различные присадки и другие элементы. Чтобы тепло не уходило в дымоход, необходимо соблюдение условия, чтобы температура внутри котла было около 600 °С. Только тогда, произойдет полное окисление всех элементов.
Существует три варианта котлов на отработке. Они представлены на рисунке ниже.
Выбор приемлемого варианта зависит от того, какие поставлены задачи для котла отопления.
Делаем котел своими руками
Потребуется сделать горелку на отработке, потому что прибор работает, за счет сгорания масла, подаваемого на разогретую чашу сгорания.
Материалы
Для работы понадобится:
- Труба диаметром 50 см
- Трубка диаметром 20 см
- Лист стали толщиной от 4 миллиметров
- Трубка металлическая для подачи воздуха
- Четыре прута арматуры с диаметром 8-10 мм
- Расширительный бак
- Полотно из асбеста
Инструменты
Минимальный набор инструментария включает:
- Сварочный аппарат
- УШМ (болгарка)
- Гаечные ключи
- Электрическая дрель (или шуруповерт с насадками)
Инструкция
Суть предстоящей работы в том, чтобы сделать котел своими руками на отработке, с водяной рубашкой, трубкой, по которой будет поступать отработка и каналом, по которому будет поступать воздух. Около днища будет расположена дверца для обслуживания чаши сгорания – ее очистки и поджигания масляных паров.
Пошаговая инструкция:
- Из более толстой трубы делаем цилиндр длиной примерно метр. Используем болгарку
- Из менее толстой трубки делаем цилиндр около двадцати сантиметров
- Из листа стали вырезаем две пластины, диаметром чуть больше толстой трубы
- В первой пластине вырезаем отверстие диаметром 20 см, а во второй – соответствующее диаметру дымохода
- Закрываем большой цилиндр пластинами и обвариваем. Зачищаем заусенцы и неровности болгаркой.
- Пластина с большим отверстием должна располагаться сверху
- К нижнему отверстию привариваем второй цилиндр и закрываем его дно аналогичной стальной пластиной.
- Крепим к низу конструкции ножки из арматуры.
- В нижней трубе просверливаем вентиляционные отверстия.
Самодельный котел на жидком топливе
Поскольку стоит задача сделать прибор своими руками, то должен получиться корпус цилиндрической формы с резервуаром внизу. В большом цилиндре вырезаем болгаркой дверцу (в нижней его части). Сверху устанавливаем трубу дымохода.
Чтобы разжечь прибор, следует открыть дверцу, налить в нижний цилиндр масло и поднести горящий фитиль или бумагу. Это самый примитивный вариант самодельного котла, но вполне работоспособный и не требующий особых финансовых затрат.
При желании можно легко усовершенствовать полученное устройство – установить расходную емкость для топлива, воздушный компрессор, насос для подачи масла и сделать водяной контур.
Самодельный котел из кислородного баллона
Для самостоятельного изготовления котла из кислородного (или газового) баллона, оптимально выбирать баллон, емкостью 50 литров.
Понадобятся инструменты:
- Сварочный аппарат
- УШМ (болгарка)
- Газовый резак
Вначале следует обрезать баллон в верхней части, из которой впоследствии можно сделать крышку. Затем вверху баллона нужно проделать отверстие, к которому потом будет подсоединен дымоход.
Согласно схеме, сбоку вырезаем дверцу для загрузки топлива. Дымоход может быть разных размеров, главное, чтобы он обеспечивал наилучшую тягу. Тогда можно получить стабильный пиролизный процесс на протяжении дня. Это удобно потому, что топить придется лишь один раз в сутки, что имеет существенное значение в отопительный сезон.
Схема котла из кислородного баллона
Такой самодельный котел на отработке, имея небольшие габариты и вес всего около 10 кг, выдает 5-6 кВт тепла, при расходе масла около 0.5 литра в час. Можно растопить его и сильнее, но не стоит, поскольку он может взорваться.
Можно усовершенствовать данную конструкцию и сварить конуса, как указано на рисунке. Для их изготовления следует брать конструкционную сталь толще 4 мм. В трубе будет перемешиваться топливно-воздушная смесь, что повысит эффективность работы. Можно установить масляную горелку, еще более усовершенствовав аппарат.
Длину дымохода не следует брать больше 3,5 метра, поскольку из-за существенно увеличившейся тяги, топливо будет уходить в трубу. В результате снизится теплоотдача и повысится расход топлива.
Оптимальные размеры и принцип работы
На правом рисунке расположен водогрейный вариант устройства из баллона. Суть его в том, что из стальной трубки делают несколько витков, располагая их в верхней части зоны, где находится устройство дожигателя котла. В деталях, можно экспериментировать на месте, исходя из пожеланий.
Для сохранения температуры, змеевик снаружи лучше закрыть защитным кожухом. Снизу в него подается холодная вода, которая нагревается по мере прохождения по спирали, и уходит в водяную систему отопления.
Предлагаемая схема котла на отработке из кислородного баллона настолько хороша, что ее давно используют в промышленном производстве, например, выпускается котел, под названием «Рицца», полностью повторяющий чертежи, по которым делают такие котлы самостоятельно.
Схема котла типа «Рицца»
Уход при эксплуатации
Поскольку рассматриваемый котел на отработанном масле, работает по принципу сжигания масляных продуктов, то в процессе его работы, выделяется достаточно много гари и копоти. Его нужно периодически чистить, особенно следить за дымоходом.
О выборе заводского котла отопления на отработанном масле читайте в статье по ссылке: https://boilervdom.ru/kotly/problemy/vybor-luchshego-kotla-na-otrabotannom-masle-obzor-modelej.html
Предлагаем Вашему вниманию видео о самодельном котле на отработке:
Экономичная печь на отработке своими руками
Очень часто в хозяйских постройках или домах, где проживают периодически, требуется установить экономичную печь. Доступным и бюджетным вариантом является печь – буржуйка на отработанном топливе. Настоящие хозяева быстро придумали, как пустить масло в дело и придумали отопительную систему, работающую на энергоемком топливе. Данное сырье сгорает, отдавая много тепла и отдает минимум сажи или копоти в помещение. Печь и способ отопления – максимально удобный вариант для обогрева многих хозяйственных построек, как гаражи, сараи, теплицы или загоны для животных.
Оглавление:
- Печь на отработке своими руками
- Положительные и отрицательные стороны использования отработки топлива
- Печь на отработке своими руками, чертежи
- Печь на отработке из газового баллона, выполненная своими руками
- Печь для гаража на отработке своими руками
- Печь на отработке капельного типа своими руками
- Печь на отработке и дровах своими руками
Печь на отработке своими руками
Конструирование данной печки несложное и при наличии инструментов и материалов можно изготовить ее за несколько часов. Что касается сырья, то у автомобилистов утилизация отходов солярки, переработанного масла и других горючих материалов, является большой проблемой. Решение применять отходы переработки из автомобиля для отопления того же гаража или других построек является прекрасным решением, которое принесет двойную пользу. Дармовой материал, являющийся к тому же и практически безопасным для окружающей среды – идеальное решение. Осталось только сделать печь и применять топливо дважды, по назначению и как вторсырье. Взять использованное сырье можно в большом количестве на станциях техобслуживания и автопредприятиях. Там порой даже оплачивается утилизация переработанного сырья.
Положительные и отрицательные стороны использования отработки топлива
Самым главным преимуществом работы печки на отработке, сделанной своими руками, есть высокая экономичность. Отработка – практически бесплатное топливо, приобрести которое можно за чисто символическую сумму. Коэффициент полезного действия котельной установки не менее семидесяти пяти процентов. Это не самые высокие показатели, но и не маленькие. Среди преимуществ отопления при помощи экономичных печей на отработке, можно выделить такие параметры:
- теплоотдача данного типа обогрева соизмерима с электрическим обогревателем, мощностью пятнадцать киловатт. Средний расход топлива – один литр в час;
- за пятнадцать минут нагоняется высокая температура и прогревается помещение среднего размера;
- в ход пойдет любая отработка, это может быть трансмиссионное, амортизационное или моторное масло;
- конструкцию можно использовать при любых температурных режимах, низкая температура не повлияет на качество работы печи;
- чтобы сделать такую отопительную систему не нужны особые навыки, достаточно владеть сваркой и слесарными умениями;
- плоский верх печи позволяет готовить пищу на ней;
- сооружение достаточно мобильное и может быть перемещено в любое удобное место;
- сжигание отходов топлива можно назвать условно экологичными, но вред для окружающей среды минимальный;
- печь можно врезать в отопительную систему.
Что касается минусов данного варианта, можно выделить такие:
- чтобы исключить попадание угарного газа и дыма в помещение, необходимо изготовить достаточно длинный дымоход и хорошо изолировать его;
- следует заниматься чисткой котельной установки и дымохода не реже, чем каждые десять дней;
- вопрос хранения масла в зимний период требует заблаговременного решения, чтобы отработка не замерзла, его необходимо хранить в теплом месте или закапывать в грунт ниже полосы промерзания;
- тепло не накапливается, в помещении комфортная температура пока топится печь;
- для соблюдения техники безопасности необходимо приобрести огнетушитель и хранить его недалеко от выполненной собственноручно печи.
Печь на отработке своими руками, чертежи
При принятии решения соорудить отопительный прибор на отработке собственноручно, необходимо продумать, какой тип сооружения будет. Известны три варианта отопительной системы на использованном масле:
- Пиролизная горелка – изготавливается из листов металла или уже готовых трубок, баллонов, из себя такая система представляет два закрытых резервуара, соединенных между собой с помощью трубы. В нижний резервуар заливается отработанное масло, которое выделяет пары, те в свою очередь горят, распространяя тепло. Температуру можно регулировать, увеличивая или уменьшая поступление кислорода.
- Конструкция с встроенной вентиляцией – специально приспособленный вентилятор подает воздух во второй отсек, это позволяет осуществлять процесс топки результативнее, тепло распространяется по всей комнате.
- Конструкция с капельной подачей отработки – такая модель идентична принципу работы дизельного двигателя и является наиболее экономичной, но в то же время и самой сложной в изготовлении. В продаже имеются заводские аппараты и лучше приобрести готовую конструкцию. Данный тип печи довольно требовательный к качеству топлива и к его температуре.
Вариантов изготовления печи много, но при любой вариации, необходимые части отопительной системы такие:
- топливный бак или камера сгорания;
- камера дожигания;
- воздушная заслонка;
- патрубок дымохода;
- подача первичного воздуха;
- отверстие для вторичного воздуха;
- ножки.
У печки на отработке есть положительные и отрицательные стороны. Из плюсов можно выделить такие моменты:
- экономичность – невысокий расход топлива;
- легкость в изготовлении – сделать такую конструкцию можно за день;
- энергетическая независимость – топить печь можно в любое время сколько необходимо, без привязки к газу или электричеству;
- многофункциональность – печь отапливает помещение, при помощи отработки можно нагреть воду или приготовить пищу.
Минусами таких конструкций есть то, что:
- трубы для дымохода должны быть установлены только строго горизонтально с высотой трубы не меньше четырех метров;
- необходимо регулярно очищать дымоход.
Но не следует забывать о мерах предосторожности при использовании самодельных отопительных конструкций:
- в кипящее масло не должна попадать вода;
- во время работы отопительной системы необходимо аккуратно совершать дозаправку топлива;
- не использовать такой вариант отопления в комнатах с затрудненным доступом свежего воздуха;
- не бросать прибор без контроля на долгий период времени.
Печь на отработке из газового баллона, выполненная своими руками
Если в хозяйстве есть газовый баллон, его можно применить для изготовления самодельной печи на отработке. Благодаря толстым стенкам баллона, печь сможет долго функционировать, не прогорая. Форма баллона является идеальной для конструкции котельной установки. Для изготовления печи, понадобится:
- Для этого необходимо взять любой баллон объемом в пятьдесят литров. Толщина материала не должна превышать полтора сантиметра, иначе стенки не могут полноценно прогреваться и печь будет работать неправильно.
- Понадобится лист металла такой же толщины –до полутора сантиметров.
- Дымоходная труба должна быть не короче четырех метров, диаметром от десяти сантиметров.
- Труба для горелки лучше всего диаметром десяти сантиметров и длинной до тридцати пяти сантиметров.
- Для ножек потребуется металлический уголок или трубка.
- Из инструментов понадобится рулетка, дрель, болгарка, сварочный аппарат, электроды.
До начала работы баллон нужно освободить от остатков газа и тщательно промыть на улице. Даже если баллон кажется пустым и долгое время не использовался, следует соблюдать технику безопасности.
Баллон фиксируется для удобства и начинается работа по изготовлению печи.
Низ баллона — нижняя камера сгорания, высота данной части конструкции – около двадцати сантиметров, верхняя камера будет примерно такого же размера. К нижней части привариваются ножки из подручных материалов: уголка, трубок.
К отверстию люка верхней камеры приваривают перегородку, варится она как можно ближе к месту расположения дымохода, ее задача – задерживать в резервуаре разогретый дым.
После этого, нужно вырезать два круга, для этого используют металлические листы. Пойдут круги для крышки нижней камеры и для дна верхней камеры. В каждой из крышек делают отверстия по десять сантиметров в диаметре. Для нижней камеры отверстие располагается по центру, для верхней – ближе к краю по диаметру трубки для горения. В нижней крышке необходимо сделать отверстие около шести сантиметров в диаметре, оно необходимо для заправки топлива. У отверстия должна быть заслонка наподобие дверного глазка, с возможностью отодвигаться и устанавливаться на место.
В соединительной трубке сверлится сорок восемь отверстий – это камера дожигания, в которой пары отработки смешиваются с кислородом. Чтобы внутри конструкции не собиралась сажа и копоть очень быстрыми темпами, нужно прошлифовать внутренние части агрегата.
В подготовленное заранее отверстие приваривают соединительную трубку.
В камере сверху делают отверстие для дымоходной трубы, важно, что она должна располагаться строго вертикально, иначе хорошая тяга не обеспечится.
Печь для гаража на отработке своими руками
К классической конструкции можно присоединить дополнительные фрагменты и усовершенствовать печь. Мастера советуют попробовать такие дополнения:
- Одним из недостатков такой печи, считается быстрое охлаждение после прекращения процесса горения, чтобы воздушный обогрев был эффективнее, специалисты советуют изготовить теплообменник. Такое инженерное решение повысит коэффициент полезного действия печи и сможет результативнее обогревать помещение.
- Если соорудить рефлектор и сделать отвод трубы с подачей теплого воздуха в соседнее помещение, можно обогревать дополнительные комнаты.
- Чтобы печь выполняла функции бойлера, необходимо приварить бак для воды, который будет прогреваться от печи.
- Дополнительный резервуар с автоподачей масла поможет продлить период работы печи.
Покрасить конструкцию можно с помощью смеси жидкого стекла и алюминиевой пудры.
В гараже такая система отопления будет настоящей находкой, это поможет решить вопрос утилизации отработанного масла и обогрева помещения без высоких материальных затрат.
Как изготовить печь на отработке своими руками, можно посмотреть в видео. Там подробно рассказано, как сделать печь на отработке своими руками.
Печь на отработке капельного типа своими руками
Печь на отработке капельного типа изготавливается так же, как и описанные выше. Отличительной чертой такой конструкции является капельная подача горючего. Из внешнего бака при помощи капельницы подается масло. Чаще всего печь такого типа изготавливается из фреонового баллона при условии целостности игольчатого клапана. Внизу баллона вырезается отверстие для заливания использованного масла, необходимо сделать его таким размером, чтобы залив отработки из канистры был удобным. Если над отверстием расположить мелкую сетку, она сможет отфильтровывать заливаемые материалы. Так как резервуар для масла расположен выше уровня отопительной системы, следует приварить приспособления для подвеса бачка.
Для печи капельного типа идеально подойдет баллон из под газа. Изготавливается такой тип печи аналогично другим, ранее описанным.
Для правильного изготовления печи на отработке своими руками, необходимо внимательно рассмотреть все чертежи. В них подробно и детально описан алгоритм действий и этапность работы.
Но изготовление печи капельного типа на отработке своими руками достаточно непростое и если нет навыков такой работы, нужно внимательно изучить видео и чертежи данного варианта отопительной системы. Если нет уверенности, что все получится или нет достаточного запаса материала инструментов, можно приобрести агрегат заводского изготовления. Все правильно рассчитать и сделать оборудование безопасным – непросто.
Печь на отработке и дровах своими руками
Печь на отработке и дровах своими руками или как ее называют – комбинированная – простое и высокоэффективное приспособление для отопления помещений. Комбинированные печи объединяют два важных принципа – высокую теплоэффективность и простое внутреннее строение. Такие печи – идеальный вариант для отопления нежилых помещений без больших экономических затрат.
Есть три способа изготовления устройства:
- самый простой способ – из стальных листов или баллонов;
- устройства с принудительным нагнетанием воздуха;
- устройство капельного типа.
Как уже отмечалось, изготовить последний вариант доступно только тем, кто обладает определенными навыками.
В комбинированной печи масло подается сверху, а дрова горят внизу.
Такой вариант печи – комбинированной – требует разумного использования. Грамотная эксплуатация должна проявляться в умении заправлять и разжигать отработку. При условии, что печь самодельная, необходимо особенно тщательно следить за правилами использования конструкции.
Дозаправка производится через приспособленное для этого отверстие, разрешено дозаправлять на две трети от нормы. Разжигается печь при помощи опилок, смешанных с отработкой. Для облегчения розжига используют бумагу.
Комбинированная печь становится все более популярной для отопления небольших хозяйственных построек. Это обусловлено дешевизной материала и высокой теплоотдачей. Но если говорить о сравнении печи на отработке и комбинированного варианта отопления, то первый вариант – дешевле и доступнее.
Изготовить печь на отработке под силу любому мастеру и если есть возможность покупать сырье, то данный тип отопления нежилых помещений экономически выгодный и удобный.
Котел на отработке с водяным контуром своими руками чертежи главная
Универсальная схема
Мы несправедливо обошли внимание ещё одну схему постройки котла, работающего на отработанном масле, – на основе горелки. Здесь мы можем использовать простую горелку Бабингтона, характеризующуюся высокой эффективностью и простой конструкцией
В ней используется металлический шар, по которому стекает отработка. В самом шарике имеется отверстие, через которое подаётся воздух. Он подхватывает мельчайшие частицы отработанного масла, распыляя его. Готовая воздушно-капельная смесь поджигается и образует устойчиво горящее высокотемпературное пламя.
Готовая горелка подключается к универсальному заводскому котлу, умеющему работать с горелками любого типа. Также она монтируется в обычные твёрдотопливные металлические и кирпичные печи. Достоинства получившейся сборки:
- Можно регулировать температуру, ограничивая подачу топлива в горелку на отработанном масле.
- Возможность автоматизации регулировки интенсивности горения.
- Возможность перевода на другой вид топлива – например, на пеллеты, на природный или сжиженный газ.
Выбирая для постройки самодельного котла горелку Бабингтона, потребители получают в своё распоряжение устройство, способное работать даже на загрязнённом отработанном масле. Главная задача – обеспечить подачу воздуха под большим давлением. Обычно для этого применяются компрессоры от холодильников.
В качестве основы для самоделки выбираем чертёж любого отопительного котла с традиционной схемой сжигания дров. Понять суть поможет небольшая иллюстрация:
Здесь мы видим котёл, который с одинаковым успехом может работать как на дровах, так и на отработанном масле – с помощью соответствующей горелки.
Работа протекает в несколько этапов. Первый – собрать горелку Бабингтона по данной схеме (или любой другой):
Схем сборки горелки Бабингтона существует великое множество. Мы решили использовать здесь самую распространенную.
Второй этап – сборка подходящей твёрдотопливной печи, которая впоследствии будет работать на отработанном масле. Выбирая чертёж и следуя ему, ни в коем случае не уменьшайте размеры камеры сгорания, куда вырывается пламя горелки – если завтра вам не хватит отработки, придётся мёрзнуть. А в большую камеру сгорания вы всегда можете накидать порцию дров и продолжить наслаждаться теплом.
Третий этап – подключение отдельных элементов. Горелка подключается к топливному баку, после чего вставляется в собранный своими руками котёл. Запускаем подогрев масла в баке, открываем вентиль, включаем компрессор, поджигаем топливно-воздушную смесь, контролируем работу водяного контура.
При необходимости, вы можете перейти с отработанного масла на сжиженный газ. Для этого приобретается газовая горелка (никаких самоделок с газом!) и устанавливается вместо жидкостной горелки. К ней подключается газовый баллон. В результате вы получите полноценное водяное отопление, хоть и несколько прожорливое.
Принцип работы котлов на отработке
Самодельный котёл на отработанном масле может работать по одной из двух схем:
- С горением топлива в одной ёмкости и его дожиганием во второй – своеобразная пиролизная схема;
- С воспламенением подогретого и испарённого топлива – крайне эффективная схема.
Если поджечь отработанное масло в какой-либо ёмкости, оно будет гореть жёлтым, слегка коптящим пламенем. Даже если отобрать получаемое тепло в отопительную систему, его будет недостаточно для обогрева помещений. К тому же в продуктах сгорания мы найдём кучу недогоревших и токсичных компонентов. Поэтому главная задача отопительного котла на жидком топливе заключается в обеспечении оптимальных условий сгорания отработанного масла. Полученное тепло отправляется в водяной контур.
Первая схема используется в самых простых печах, наподобие вот этой:
Горение при такой схеме осуществляется с забором воздуха через регулировочную заслонку.
Здесь мы видим бак с топливом и регулировочной заслонкой, дожигатель и вторичную камеру. В дожигатель, через ряды боковых отверстий, подаётся вторичный воздух. Отработанное масло заливается в бак, поверх него наливается немного керосина, после чего производится розжиг.
Пламя в дожигателе будет сначала жёлтым, так как печь холодная. По мере прогрева оно приобретёт бело-розовый оттенок, появится гудение, характерное для мощного потока пламени. Это значит, что агрегат вышел на рабочий режим. Увеличив размер верхней камеры и дополнив её трубчатым теплообменником, мы получим простую печь на отработке с водяным контуром.
Для рассмотрения второй схемы водогрейного котла на отработанном масле мы возьмём следующую схему:
Схема и принцип действия водогрейного котла на отработанном масле
Это не совсем то, что нам нужно, но принцип тот же. Представленный на рисунке агрегат включает в себя несколько важных узлов. Первый узел – это топливный бак, который обеспечивает подачу отработанного масла в котёл. Подача должна быть капельной. Отработка поступает в чашу, в которой разжигается пламя. По мере прогрева конструкции масло начинает поступать в чашу уже горячим, температура его горения возрастает.
Горение осуществляется во внутреннем объёме печи, ограниченном металлическим цилиндром. Это наша камера сгорания – сверху в неё поступает воздух, в верхней боковой части располагается отвод под дымоход. На представленном чертеже изображён агрегат с поддувом, что делает его работу более эффективной. Водяной рубашки здесь нет, но есть вентилятор обдува, который обдувает воздухом внутренний цилиндр с камерой сгорания. Горячий воздух можно отправить через воздуховоды в обогреваемые помещения.
При использовании воздуховодов их необходимо тщательно утеплить, чтобы снизить потери тепла.
Организовать отопление на отработанном масле своими руками поможет водяной контур. Для этого убираем из чертежа вентилятор обдува и сопло отдачи горячего воздуха, никаких отверстий на их месте не будет. Вместо этого привариваем к цилиндру с камерой сгорания змеевик, играющий роль теплообменника. Его можно сделать из трубы подходящего диаметры. Концы трубы выводятся наружу – к ним подключается контур отопления.
Таким образом, мы сделали отличную печь на отработанном масле с водяным контуром. Осталось поработать над увеличением эффективности. Для этого мы можем обернуть дымоходную трубу дополнительным теплообменником и соединить его с основным. Теперь оборачиваем наш водогрейный отопительный котёл в теплоизоляцию, после чего облачаем его в дополнительный корпус – это поможет снизить тепловые потери.
Необходимые инструменты и материалы
Такое устройство можно сделать любой формы. Можно изготовить его из металлического листа, но если его нет, то взять можно старый газовый баллон или металлическую трубу большого диаметра с толстыми стенками. Самую простую модель можно выполнить из основной трубы диаметром 0,5 м и двух дополнительных, диаметром по 30 см. Также потребуются две металлические пластины с толщиной минимум 2 мм.
Кроме этого, потребуются такие инструменты и материалы:
- металлические листы толщиной от 2 мм;
- труба для дымохода;
- 3 арматуры;
- насос;
- компрессор;
- расширительный бачок;
- сварка;
- асбестовое полотно;
- болгарка;
- герметик;
- переходники из термостойкой стали.
2 Принцип работы
В процессе горения бензина масло нагревается, закипает и начинает испаряться. Во время нехватки воздуха масляные пары слабо горят, поэтому их необходимо обогащать кислородом. Для этого используется перфорированная труба. При этом непосредственно в трубе и в верхней части печной конструкции происходит активное сгорание масляно-воздушного состава.
Температура камере, которая находится внизу, не превышает 400 °C, в то время как верхняя прогревается до 1000 °C. При ручной заливке горючего в нижней камере делают отверстие для топлива и розжига. При автоматической подаче в нее заводят патрубок, который соединяется с баком, находящимся снаружи. Также в этой камере необходимо выполнить отверстие с заслонкой, при помощи которой можно отрегулировать подачу кислорода, температуру и тягу.
Во время естественной циркуляции длину водяного контура проводят чуть больше, чтобы не допустить значительного перегрева. Принудительная циркуляция при помощи насосного оборудования дает возможность сделать меньше размер емкости для воды. Специалисты рекомендуют оборудовать отопительную систему манометром и термометром, чтобы была возможность контролировать параметры теплоносителя в контуре.
Принцип работы и преимущества самодельных котлов
Чтобы отапливать помещение или целое здание, используя тепловую энергию сжигания старых масел, котлы данного типа работают по принципу, отдаленно напоминающему пиролиз. Топливо, находящееся на дне камеры, сначала разогревается до тех пор, пока не появятся горючие испарения. Они поднимаются вверх, смешиваются с воздухом и сгорают, выделяя тепло. Оно передается непосредственно водяной рубашке агрегата через стенки камеры. Для понимания процесса ниже показана схема котла на отработанном масле.
Устройство котла
1 – верхняя крышка; 2 – шкаф управления; 3 – блок питания; 4 – вентилятор; 5 – насос; 6 — топливный бак; 7 – отработка масел; 8 – отстойник; 9 – кран для опорожнения; 10 – маслопровод; 11 – дверца для розжига и обслуживания; 12, 16 – соответственно, подающий и обратный трубопроводы, к ним присоединяется отопительная система; 13 – труба подачи воздуха в зону горения; 14 – водяная рубашка; 15 – жаровые трубы; 17 — камера сгорания; 18 – конденсатосборник; 19 – заслонка – регулятор тяги; 20 — дымоходная труба.
Чтобы понять, стоит ли заниматься этим делом, или лучше просто купить заводской готовый котел, надо проанализировать, какими преимуществами обладают самодельные агрегаты. Они довольно существенны:
- Низкая стоимость. Даже если вы поручите работу опытным мастерам, оплатите ее и купите все материалы, то самодельный котел на отработке обойдется вам вдвое дешевле, чем заводской.
- Сжигать можно любые виды отработанных масел, а в случае надобности и дизельное топливо.
- Всегда есть возможность усовершенствования конструкции или ее дополнения средствами автоматизации.
- Поскольку использование отработанного масла в качестве топлива предполагает небольшое количество золы после сгорания, то и обслуживание источника тепла не займет много времени.
- Качественно собранный агрегат с набором автоматики при работе не требует постоянного к себе внимания и частого посещения топочной, нужно лишь вовремя заливать топливо в бак.
Из недостатков можно выделить некоторую инертность, она заключается в том, что после прекращения подачи воздуха в зону горения процесс останавливается не сразу, для этого требуется некоторое время, в течение которого теплоноситель продолжает прогреваться. Далее, после затухания пламени котлы на отработке потребуется разжигать вручную, если не предусмотреть для этого специального устройства.
Самодельные котлы для отопления на отработке усовершенствованной конструкции наделены функцией «холостого хода», когда воздуха в камеру подается совсем немного. Это сделано с целью поддержания небольшого пламени, когда интенсивный нагрев теплоносителя не требуется. После его остывания подача воздуха возобновляется и теплогенератор выходит на рабочий режим.
Когда вы задумали сделать отопление отработкой, надо понимать, что в топочной не будет такой чистоты, как при использовании газа или электричества. Это неизбежный атрибут пользования отработанным топливом, как и присутствие специфического запаха. Кроме того, придется организовать фильтрацию масла от металлической стружки и прочих твердых включений, чтобы они не засоряли топливный тракт.
Подключение и эксплуатация
Самодельные и заводские котлы отопления на отработке могут использоваться только в закрытой системе теплоснабжения. Дополнительно учитываются меры безопасности – емкость с топливом и оборудование не должны находиться в одном помещении. Место установки котла не может иметь горючих материалов – пол и стены обрабатываются защитными составами. Монтаж рекомендуется делать на ж/б плиту или стяжку.
Общая схема подключения не отличается от стандартной. При выполнении работ должны быть соблюдены такие условия:
• Входной и выходной патрубок изготавливается из металла. Их минимальная протяженность – от 1,5 м.
• Установка групп безопасности. На обратной трубе — клапан, предотвращающий изменение направления движения жидкости и циркуляционный насос. На подающей магистрали – воздухоотводчик и спускной клапан.
• Для создания хорошей тяги монтируется дымоход длиной не менее 4 м.
Пробный запуск осуществляется при 30% от максимальной мощности оборудования. Потом этот показатель постепенно увеличивается до предельного уровня. Контролируется отсутствие протечек в системе и перегрев котла. Для этого необходимо установить манометры и термометры.
В видеоматериал можно ознакомиться с примером самодельного оборудования:
Продукция промышленного производства
Хотя по готовым чертежам котел на отработке своими руками сделать совсем не сложно, все же такие изделия выпускают и промышленные предприятия.
Подобное оборудование рекомендуется использовать для отопления таких помещений:
- загоны для животных;
- складские помещения и гаражи;
- производственные цеха и технологические линии;
- зимние сады и оранжереи;
- городские и частные бани;
- загородные домики.
Примечательно, что оборудование отопительного котла водяным контуром позволит использовать его более эффективно и обогревать большую площадь.
Среди наиболее известных марок котлов на отработке от промышленных производителей можно назвать несколько:
- Котел Kroll SKE 100 F, производство Германия. Универсальный агрегат, способный работать на любом виде отработки, в том числе, растительном масле, а также на дизельном топливе.
- Модель Kroll W401-L, производство Германия. Для этого прибора также подходит любой вид отходов. При этом не нужен дополнительный монтаж горелки.
- Финский котел DanVex B-30 и В-220 с одноступенчатой горелкой. Перерабатывает дизельное топливо, любой вид отработки и даже традиционное топливо для печей.
- Модель Тепламос НТ-320 и НТ-370, производства России, способны работать на любом жидком горючем, в том числе, керосине и дизтопливе.
В любом случае, такой котел можно собрать самостоятельно, и даже подключить к нему водяной контур.
Обвязка. Дублирование печи на отработке электрическим агрегатом
Перед подключением котла следует продумать не только способ монтажа и точки размещения дополнительных устройств и запорно-регулировочной арматуры, но и способ вывода дымовой трубы наружу. Если она будет проходить через потолок, построенный с использованием легковоспламеняющихся материалов, то в нём устанавливают металлический пенал вдвое большего диаметра. Свободное пространство между трубами заполняют асбестом или другим негорючим материалом с хорошими теплоизоляционными свойствами.
Простейшим способом обвязки котла является интеграция в гравитационную систему отопления. Несмотря на простоту, его надёжность очень высока, поскольку в этом случае отпадает потребность в циркуляционном насосе и устройствах автоматики. Тем не менее использование дополнительного оборудования позволяет ускорить доставку теплоносителя к потребителям и выровнять температуру во всех точках системы, что даёт экономию топлива и повышает комфорт. В этих целях на обратной магистрали перед самым входом в котёл устанавливают центробежный насос и расширительный бак мембранного типа. Он необходим для того, чтобы система не разгерметизировалась при повышении температуры и давления. К верхнему патрубку подсоединяют напорную магистраль, а для регулировки температуры потребителей перед каждым радиатором устанавливают термостатическую головку или другое регулирующее устройство (трёхходовой клапан, вентиль для уменьшения сечения подающей трубы и т. д.). Для удаления воздушных пробок в верхней точки системы монтируют воздухоотводчик.
Схема обвязки котла, работающего на отработанном масле
Обвязка агрегата, работающего на отработке, требует учитывать инерционность этого вида оборудования. Другими словами, изменение температуры теплоносителя происходит постепенно, поэтому агрегат обязательно оснащают предохранительным клапаном. Он позволит сбросить давление при его повышении до критического уровня. Неплохим способом обезопасить и выровнять температуру является последовательное подключение водонагревателя косвенного нагрева. Он послужит тем самым буфером, который возьмёт на себя лишнее тепло в случае избыточного роста температуры.
Когда хотят подстраховаться на случай нехватки отработанного масла, рядом с самодельным котлом устанавливается электрический. Подключить дополнительный агрегат можно двумя способами — последовательно или в параллель. Достоинство первого способа заключается в том, что нагретый с помощью пламенной чаши теплоноситель будет поступать в электрический котёл, который можно настроить на определённую температуру срабатывания. При уменьшении пламени горелки он будет включаться и повышать температуру воды до нужного значения. Недостатком подобного способа является увеличение длины магистрали, а также полная неработоспособность системы в случае демонтажа одного из котлов для ремонта.
Параллельное включение подразумевает независимую работу двух отопительных агрегатов и характеризуется отсутствием указанных недостатков. К сожалению, и этот способ не лишён минусов, один из которых — необходимость монтажа гидрострелки и точного согласования режима работы и подачи обратной магистрали. К тому же фитингов, труб и арматуры при параллельном включении пойдёт намного больше, что непременно приведёт к увеличению стоимости и усложнению монтажа.
Требования к пожарной безопасности
Печь на отработке раскаляется и становится пожароопасной, поэтому нужно соблюдать требования к её установке и эксплуатации:
- Поверхность пола должна быть несгораемой. Допускаются бетонные, из керамической плитки, металлические поверхности. Деревянный пол возле печи закрывают металлом.
- Если стенка, возле которой стоит печь, из дерева или другого не огнестойкого материала, то её надо закрыть асбестовым листом.
- Нельзя допускать сквозняков в помещении, где установлена печь. Пламя из перфорированной трубы может перекинуться на окружающие предметы.
- Запрещено складирование вблизи печи любых легковоспламеняемых материалов.
- Запасы отработки хранят в другом помещении.
- В процессе работы печи туда нельзя доливать топливо.
- В помещении нужно держать в удобном месте порошковый либо солевой огнетушители.
Печь на отработке — это экономичный и удобный обогревательный агрегат, который при правильной эксплуатации и монтаже водяного контура значительно улучшит микроклимат в помещении и будет незаменимым источником тепла в гараже или мастерской.
Как именно испаряется масло
Существует 2 основных способа сжигания горючего и испарения масла:
- Поджигание жидкого вещества. При этом выделяется пар. Для его догорания используется специальная камера.
- Обливание раскалившейся поверхности. Применяется раскалившаяся «добела» чаша, изготовленная из металла. На ее поверхность и капает отработка. Когда топливо контактирует с раскалившимся металлом, происходит его испарение. «Сотрудничество» воздуха и пара именуется «диффузией». Когда воздух поступает в бак, пар, вспыхнув, загорается. Результатом этого является образование тепла.
Расход горючего достаточно экономичен. В час задействуется от ½ до 1 литра.
Европейские котлы, несмотря на великолепный КПД, не позволяют сделать возможным такой принцип работы. Это актуально только в случае с котлами отечественного производителя.
Разогрев котлаПроще всего пропитать бензином фитиль, поджечь его и бросить в бак. Когда чаша хорошо прогреется, можно начинать подавать масло.
Важно, чтобы масло подавалось равномерно. Рекомендовано использовать капельный подход
Для обеспечения нужного уровня фильтрации отработки следует использовать автомобильный фильтр. Он надевается на трубку, один из концов которой должен быть опущен в емкость с отработкой.
Фильтр следует заменять не реже, чем 1 раз/30 суток. Если горючее нельзя назвать чистым, то делать это рекомендуется 1 раз/15 суток.
Количество масла, капающего на чашу, должно быть оптимальным. Самое главное – обеспечить ему равномерное прогорание. Чадить оно не должно.
Если владелец котла принял решение относительно замены горючего, частоту капель нужно регулировать каждый раз.
Также следует обеспечить установке максимальную защиту. Нельзя допускать закипания масла – это может привести к непредсказуемым последствиям. То же самое касается перелива горючего.
Если уровень горючего в резервуаре будет выше, нежели в самой печке, может возникнуть возгорание. Справиться с ним можно только при помощи огнетушителя.
Нельзя заливать масло в котел тогда, когда агрегат работает – это может быть очень опасно. Лучше всего монтировать дополнительную емкость. В нее можно будет помещать основной запас горючего.
Отопление на отработанном масле для частного дома
Отработанное масло для обогрева изначально применяли вместе с соляркой. Такой способ доказал свою эффективность и экономичность. Тогда решили удешевить средство еще больше и убрали солярку из состава. Отработанное масло по своим характеристикам напоминает дизельное топливо, но стоит на порядок дешевле.
Фото 1. Так выглядит отработанное масло, которое используется для отопления. Жидкость тёмно-коричневого цвета.
Особенности использования
Отработку в качестве топлива используют в специальном котле или в печи. Только это гарантирует полное сгорание продукта без образования чадного дома. Переоборудование системы отопления или установка нового контура окупается в первый год использования средства.
Виды топлива. Сколько получают тепла при сжигании одного литра?
Сжигание одного литра такого топлива дает 10—11 кВт тепла в 60 минут. Продукт, подвергшийся предварительной обработке, обладает большей мощностью. Его сжигание дает на 25% больше тепла.
Разновидности отработанных масел:
- моторные масла и смазочные средства, используемые в различных видах транспорта;
- индустриальные продукты.
Плюсы и минусы
Плюсы топлива:
- Экономическая выгода. Деньги на топливе экономят потребители, но наибольшую выгоду получают предприятия. Реализация отработки избавляет от затрат на хранении, транспортировки и утилизации средства.
- Сохранение энергоресурсов. Отказ от использования для отопления газа и электроэнергии препятствует истощению источников.
- Защита окружающей среды. Из-за высокой стоимости утилизации, владельцы предприятий и транспортных средств избавлялись от масла, сливая его в водоемы или в грунт. Это негативно сказывалась на состоянии окружающей среды. С началом применения отработки в качестве топлива такие манипуляции прекратились.
Минусы топлива:
- представляет опасность для здоровья, если продукт сгорает не полностью;
- большие габариты дымохода — 5 м в длину;
- сложность поджига;
- плазменная чаша и дымоход быстро засоряются;
- работа котла приводит к сжиганию кислорода и выпариванию влаги из воздуха.
Как отрабатывают масло?
Отработку получают при сжигании любого вида масла, но для отопления помещения обычно используют средства нефтепереработки из двигателей внутреннего сгорания.
Также из индустриальных механизмов, компрессоров и энергетического оборудования.
Что не относится к подобному топливу?
Перечень продуктов, не относящихся к отработке:
- переработанные масла растительного и животного происхождения, которые используются для бытовых нужд;
- твердые отходы с отработкой;
- растворители;
- продукты, которые не подлежат такой же переработке, как отработка;
- нефтетопливо природного происхождения из разлива;
- другие неиспользованные нефтепродукты.
Технология изготовления печи на отработанном масле
Ниже представлены чертежи наиболее распространенной печи на отработке. Она выполнена из остатков трубы Ø352 мм, листовой стали 4 мм и 6 мм, также понадобятся обрезки толстостенной трубы Ø100 мм и уголка для ножек.
Ее габариты позволят обогреть помещение со стандартной высотой потолков площадью до 80 м2, при большей площади следует увеличить размеры печи и диаметр трубы дымохода.
Необходимый инструмент:
- сварочный аппарат;
- болгарка с отрезным кругом;
- шлифовальный круг для зачистки швов;
- дрель или сверлильный станок, сверла;
- рулетка.
Также необходимы растворитель и кремнийорганическая термостойкая краска — она обычно продается в баллончиках и используется для окраски сильно нагреваемых поверхностей печей.
Последовательность изготовления своими руками:
- Подготавливают заготовки по чертежам. Все детали вырезают из указанного на чертеже материала и зачищают места среза для устранения заусенцев.
- Соединяют методом сварки детали нижнего бака: корпус из трубы Ø344 мм h=115 мм, дно из листового металла 4 мм, а также ножки из уголка произвольного размера. Вместо уголка можно использовать обрезки дюймовой трубы.
- В отрезке трубы Ø100 мм h=360 мм с помощью сверла выполняют перфорацию по эскизу — 48 отверстий диаметром 9 мм.
- Соединяют сваркой детали крышки нижнего бака: заготовку из трубы Ø352 мм h=60 мм, крышку из листовой стали 4 мм с двумя отверстиями и перфорированную трубу.
- Заслонку для отверстия подачи воздуха на крышке нижнего бака крепят на заклепку.
- Соединяют сваркой детали верхней камеры: заготовку из трубы Ø352 мм h=100 мм и дно из листовой стали 4 мм с отверстием для перфорированной трубы.
- К крышке верхней камеры приваривают дымовую трубу Ø100 мм h=130 мм, с внутренней стороны крышки — перегородку из листовой стали 4 мм с размерами 70х330 мм. Перегородка предназначена для отсекания пламени и увеличения эффективности нагрева верхней камеры. Располагать ее следует ближе к дымовому отверстию.
- Сваривают верхнюю камеру и крышку с дымовой трубой.
- Приваривают верхнюю камеру к верху перфорированной трубы, для увеличения жесткости конструкции можно сделать стяжки из прутка между крышкой нижнего бака и верхней камерой.
- Верхнюю часть печи надевают на нижний бак внатяг.
- Печь для продления срока эксплуатации покрывают кремнийорганической краской, предварительно зачистив сварные швы от окалины, а металл от ржавчины с помощью растворителя.
- Подсоединяют печку к дымоходу. Его высота должна быть не менее 4 метров для улучшения тяги. Поскольку дымоход придется часто очищать от сажи, нужно сделать его максимально прямым, без изгибов.
Аналогичную печь можно сделать из листового металла, в этом случае ее камеры будут квадратной формы. Подробная технология приведена на видео.
Изготовление печи на отработке: видео
Как подключить к печи на отработке водяной контур
Водяной контур подключают к котлу, установленному на верхнюю камеру. Его можно приварить прямо на поверхность печи, но более безопасно сделать отдельный бак: в случае прогорания дна бака вода попадет в камеру сгорания, что может вызвать выплеск горящего масла и резкое воспламенение.
Бак может быть произвольной формы и высоты, главное условие — плотное прилегание к верхней камере и дымовой трубе для более эффективного нагрева. В стенки бака врезают два штуцера: в верхней части для нагретой воды, в нижней — для остывшей обратки.
На выходе из бака устанавливают термометр и манометр. На обратной трубе в непосредственной близости от котла ставят циркуляционный насос и расширительный бак.
Пиролизный котел на отработанном масле
котел на отработке/
котел на отработке/Воздуховод в пиролизной камере.cdw
котел на отработке/воздуховод в горелке горизонтальный.m3d
котел на отработке/воздуховод в горелке.m3d
котел на отработке/Воздуховод в пиролизной камере горизонтальный участок.cdw
котел на отработке/воздуховод к подогревателю d57.m3d
котел на отработке/вход-выход воды d57.m3d
котел на отработке/Дымовые трубки в сборе.a3d
котел на отработке/Дымоход d133.m3d
котел на отработке/Дымоход.cdw
котел на отработке/Корпус (труба внешняя).cdw
котел на отработке/Котёл на отработке.a3d
котел на отработке/Котёл на отработке.jpg
котел на отработке/Котел на отработке в сборе.cdw
котел на отработке/Крышка котла верхняя.cdw
котел на отработке/Крышка котла нижняя.cdw
котел на отработке/Крышка котла нижняя.m3d
котел на отработке/Крышка котла.m3d
котел на отработке/Крышка пиролизной камеры.cdw
котел на отработке/Крышка пиролизной камеры.m3d
котел на отработке/Отвод d140.m3d
котел на отработке/Отвод.m3d
котел на отработке/Подогреватель воздуха.cdw
котел на отработке/стенка боковая топки.m3d
котел на отработке/стенка верхняя топки.m3d
котел на отработке/стенка нижняя топки.m3d
котел на отработке/Стенка топки боковая.cdw
котел на отработке/Стенка топки верхняя.cdw
котел на отработке/Стенка топки нижняя.cdw
котел на отработке/Труба в котле.cdw
котел на отработке/Труба внешняя.m3d
котел на отработке/Труба внутренняя (Пиролизная камера).cdw
котел на отработке/Труба внутренняя.m3d
котел на отработке/Труба подогревателя воздуха.m3d
котел на отработке/Трубка дымовая внутренняя d57.m3d
котел на отработке/Фрагмент.frw
Как сделать котел отопительный на дровах своими руками — Все о печи в доме
Тепло и уют в доме обеспечиваются хорошо налаженной системой отопления. Но в частном секторе электричество и газ зачастую бывают недоступны, а магазинные твердотопливные аппараты стоят достаточно дорого. Вот и стараются народные умельцы, кто как может, изготавливая кустарные системы отопления. Самодельные котлы набирают все большую популярность, поэтому стоит рассмотреть подробнее, как сделать котел отопительный на дровах своими руками.
Устройство котла на дровах.Классический вариант котла представляет собой специализированную камеру, куда закладываются дрова. Пиролизный агрегат имеет более высокое КПД, но состоит из двух камер. В нижнюю камеру помещаются дрова, а в верхнюю поступает тепло, которое находится там определенное время. Сделать его самостоятельно сложнее, схемы и чертежи должны быть выполнены с предельной точностью и тщательностью. Используя пиролизное устройство, нужно помнить, что этот котел может работать только на дровах с процентом влажности не больше 20 единиц.
Преимущества дровяного отопления и требования безопасности
Котлы под дрова обладают рядом преимуществ в сравнении с конструкциями, работающими на специальном топливе.
- Дрова — это экологически чистое топливо, не провоцирующее аллергические реакции и заболевания.
- Используемый для топки материал обладает приемлемой стоимостью и достаточно доступен.
- Эстетическая составляющая делает котлы под дрова востребованными даже в постройках элитного типа.
- Стопроцентная безопасность при самостоятельном проведении всех работ, хозяин сам контролирует все недочеты и может моментально их устранить.
- Котел на твердом топливе прост в эксплуатации и нагревает помещение за считаные минуты.
Для того чтобы отопительное оборудование обладало всеми вышеперечисленными характеристиками, требуется соблюдение определенных условий:
- Необходимо регулярно проветривать комнату, так как котлы имеют открытую горелку и сжигают кислород, находящийся в помещении.
- В непосредственной близости с агрегатом нельзя располагать никаких горючих и легковоспламеняющихся материалов.
- Для удобства использования котел нужно разместить так, чтобы в него было удобно добавлять топливо.
- Если вы захотите сделать котел более эстетичным, красить его можно только жаропрочной краской или лаком.
Вернуться к оглавлению
Изготовление дровяного котла своими руками
Устройство дымохода для твердотопливного котла.Для изготовления элементарной конструкции на твердом топливе своими руками потребуется металлическая бочка объемом около 200 л. С нее необходимо срезать верхушку. Приток воздуха сверху будет обеспечиваться крышкой с трубой, имеющей диаметр 10 см. Это поддувало даст возможность нижнему слою дров тлеть и давать дополнительное тепло. Для дымохода будет нужна наклонная труба с диаметром 15 см. Она приваривается в самом верху, с боковой стороны.
В верхней части бочки нужно сделать люк для закладки дров, а в нижней — отверстие для уборки отработанного топлива. Для увеличения времени горения одной загрузки дров применяется специальный груз, выполненный в виде диска с лопастями и отверстием диаметром 20 мм. Он сжимает сгорающее топливо, и доступ воздуха ограничивается этим 20-миллиметровым отверстием. После выполнения всех манипуляций котел следует подключить к отопительной системе. Сделать это можно с помощью 2-х способов:
- Врезать трубу с водой прямо в бочку. Вода будет горячей на этом участке, а радиаторы будут нагреваться за счет циркуляции воды.
- Врезать трубу дымохода в бак с теплоносителем. Тогда вода будет греться за счет продуктов горения.
Вернуться к оглавлению
Пиролизный котел: принципы работы, схемы, чертежи сборки своими руками
Схема подключения пиролизного котла.Работа твердотопливных пиролизных котлов под дрова основана на разрушении молекулярной структуры древесины под воздействием высокой температуры и низкой концентрации кислорода. Эта реакция ведет к распаду молекул на пиролизные газы и твердые отходы в виде угля. Если позволить воздуху циркулировать, то процесс будет происходить частично, и несгоревшие летучие вещества будут уходить в атмосферу. Примером этому служит обычный костер. И только изменив условия, можно достичь полного сгорания пиролизных газов и уменьшить выброс вредных веществ.
Пиролизная печь, работа которой основана на процессе сжигания не только твердого топлива, но и древесных газов, имеет ряд неоспоримых достоинств:
- более высокий КПД;
- минимальный выброс канцерогенных веществ;
- возможность утилизации отходов.
Недостатками магазинных пиролизных котлов под дрова является достаточно высокая цена, зависимость от электрических сетей и возможность применения только сухой древесины. Эти минусы и сдерживают спрос на данные агрегаты и ведут к тому, что все больше хозяев частных домов хотят изготовить пиролизный котел своими руками. Процесс сборки пиролизного котла элементарным не назовешь, и денег в него придется вложить достаточное количество, хотя, конечно, экономия в сравнении с промышленным агрегатом будет ощутимая. Возьмем за основу классическую схему изготовления.
Из расходных материалов понадобятся:
- Сталь толщиной не меньше 4 мм.
- Профили — 60х30 и 80х40.
- Стальные ленты шириной 20 и 80 мм.
- Трубы с диаметром в 32, 57 и 159 мм.
- Лювер.
- Термодатчик.
- Крепежи.
Не стоит забывать и про необходимый инструмент. Заранее стоит подготовить сварочный аппарат и электроды, дрель и шлифовальную машинку с дисками 125 и 230 мм.
На основании чертежа необходимо выполнить сборку пиролизного котла под дрова. Следует знать, что размеры внутренней камеры не должны подвергаться серьезным изменениям, это ухудшит работу всего оборудования. После сборки котла необходимо его правильно установить. При монтаже пиролизной конструкции своими руками особенно тщательно следует соблюдать правила пожарной безопасности, поэтому необходимо оборудовать специальную котельную, в которой и будет установлено оборудование.
Основанием для пиролизного котла под дрова может послужить бетонная стяжка или кирпичная кладка, а спереди топочных камер необходимо расположить стальные листы толщиной не менее 2 мм. Запрещено устанавливать конструкцию вплотную к предметам мебели и стенам. Котельную необходимо оборудовать вентиляционным отверстием площадью не меньше 10 см², дымоход лучше утеплить фольгированной минватой, чтобы предотвратить образование конденсата.
Вернуться к оглавлению
Пиролизный котел на отработке своими руками — чертежи
Чертеж пиролизного котла на отработке.Отопительные котлы применяются не только для обогрева жилых помещений. Их устанавливают в цехах, банях, гаражах и на других промышленных объектах. В целях экономии в качестве топлива для них применяется отработанное масло. Обоснованность повторного использования отработки очевидна — в качестве топлива используется продукт, за который уже когда-то заплатили. При таком преимуществе, как бесплатное топливо, КПД этих котлов тоже достаточно высок и достигает 95%. Но имеют пиролизные котлы на отработке и недостатки:
- 1. Для их установки нужны топливные емкости.
- 2. Они нуждаются в компрессоре для выработки сжатого воздуха.
- 3. Для них необходима регулярная очистка.
Собрать пиролизный котел на отработке своими руками можно на основании чертежей. Нужно учитывать, что для его сборки и установки потребуются такие компоненты, как
- 1. Компрессор.
- 2. Насос.
- 3. Горелка.
- 4. Расширительный бак.
Для монтажа будет необходим сварочный аппарат. Под пиролизный котел на отработке необходим дымоход, конструкция которого предполагает наличие трубы и кожуха, предотвращающего соприкосновение дымохода с потолочным перекрытием. Необходимой деталью является и заслонка, регулирующая поступление воздуха, предотвращающая охлаждение помещения в случае отключения котла.
Приведем пример изготовления элементарного пиролизного котла, работающего на отработанном масле. Эта конструкция имеет одну емкость, совмещающую в себе бак для топлива и камеру горения. К этому баку нужно приварить ножки для избегания прямого контакта с полом. Воздушная заслонка устройства одновременно служит люком для залива топлива и регулятором интенсивности поступления воздушных масс.
В бак необходимо вварить отрезок трубы с толстыми стенками 100-150 мм диаметром, в котором нужно просверлить отверстия. Труба будет представлять собой дожигающую камеру, в ней будут гореть масляные пары.
https://1popechi.ru/youtu.be/FtXkhN97uiU
Теплообменник будет представлен воздушной камерой, которую следует приварить сверху камеры дожига. В ней нужно сделать металлические перегородки, которые будут замедлять движение горячих продуктов горения и увеличивать теплообмен печи и отапливаемого помещения. Удаление газообразных продуктов горения будет происходить через вваренный в верхнюю камеру дымоход.
«Апгрейд» и повышение безопасности такого теплогенерирующего устройства можно провести путем установки дополнительного бака на одном уровне с нижней емкостью для дозаправки котла в процессе эксплуатации. Баки следует соединить трубой.
Надо учитывать, что такой пиролизный котел следует оберегать от попадания в него воды! В противном случае происходит вспенивание и возможен выплеск горящих масел из камеры сгорания. Также важно сохранять вертикаль дымохода на высоте не меньше 2 м.
https://1popechi.ru/youtu.be/8Z79Atu9wV8
Для превращения такой печи в водогрей или воздухонагревательный котел нужно снабдить верхнюю камеру водяной рубашкой или установить воздуходувный насос.
Пиролизное масло — Экология с открытым исходным кодом
Main > Energy > Biofuel
Пиролизное масло или «био-масло» является продуктом пиролиза различных материалов, таких как:
- При нагревании древесины или другой биомассы до достаточной температуры в среде с низким содержанием кислорода или без кислорода образуются летучие компоненты
- После охлаждения некоторые из них находятся в газообразном состоянии (водород, окись углерода, газообразные углеводороды), а другие находятся в жидкой форме, так называемое пиролизное масло
- Это масло является плотным источником топлива — для таких применений, как отопление и производство пара.
- Таким образом, это менее технологичный заменитель нефтяного топлива в некоторых приложениях с более низкой теплотворной способностью, чем дизельное топливо.
- В настоящее время не может заменить дизельное топливо в стандартных дизельных двигателях внутреннего сгорания из-за высокой вязкости и кислотности.
- Модернизация биомасла до дизельного топлива с помощью процесса Фишера-Тропша возможна, но не может быть практичной в малых масштабах
- Существуют также химические пути
- Недавно был обнаружен дешевый способ с открытым исходным кодом для улучшения биомасла с помощью Red Mud в качестве катализатора.
- Нужно найти какой-нибудь паспорт безопасности для него или, возможно, аналогичный продукт «креозит» / древесная смола?
- ВЕРОЯТНО не очень хорошо
- Не помешает использовать:
- Перчатки
- Вытяжной шкаф и респиратор и / или хорошая вентиляция в рабочем пространстве
- Пока он не превратится в конечное топливо / продукты, просто используйте:
- Хорошая вентиляция и мытье рук после воздействия
Примеры использования
Пиролизное масло чаще всего получают в результате пиролиза биомассы, но также возможны и другие источники, такие как пластиковые отходы и старые шины.Типичные промышленные применения пиролизного масла в качестве топлива:
- Котлы
- Печи
- Генераторы горячей воды
- Генераторы горячего воздуха
- Нагреватель теплоносителя
- Электрогенераторы (смешанные с 50% дизельным топливом)
- Дизельные насосы (смешанные с 50% дизельного топлива)
Методы использования
- Может использоваться напрямую (хотя и не так эффективно и более загрязняюще) как:
- В случае переработки его можно использовать в качестве соответствующих углеводородов.
- Фильтрация, водоотделение + химическая сушка и фракционная перегонка — это основной рабочий процесс
- Можно ли использовать его в качестве сырья для производства биодизеля?
- Реакторы, скорее всего, также будут производить следующие полезные продукты:
Производство
Постпроизводственная фильтрация
- Простая вакуумная фильтрация через фильтр
- Можно даже использовать мелкую металлическую сетку для повторного использования (кислотность может быть проблемой для этого, но, возможно, ткань / керамика?)
Водоотделение + сушка
Базовое разделение
- Разделительная воронка или аналогичное устройство (метод пипетки для небольших объемов, ведра с носиками для дешевых установок и т. Д.) Может отделять большую часть воды
- Может ли водоотделитель / сифон для дизельного топлива быть хорошим вариантом OTS?
- Может быть использовано автоматическое дозирующее устройство или непрерывный сепаратор масла и воды
Дальнейшая сушка
- Не требуется для прямого использования
- Это больше подходит для использования в химической очистке и модернизации
- Это можно сделать через:
- Молекулярные сита
- Вакуумная сушка (при условии, что масло сначала не выкипит, или это учтено)
- Фракционное замораживание (сублимационная сушка жидких смесей для разделения с помощью разностей сублимации) может работать (требуется исследование)
- Простые емкости для испарения / пруды в сухой / теплой среде? (требуется дополнительное исследование)
Постфильтрация + сушка Очистка / модернизация
- Не используется ни в каких случаях прямого использования масла
- Используется для производства синтетических углеводородов на том же уровне, что и разновидности био-сырой или невозобновляемой сырой нефти.
- Выполнено с использованием того же рабочего процесса, что и другие источники:
Великий эксперимент, который можно провести за семестр, — это создание простого дистилляционного аппарата для проверки процедуры с использованием древесных стружек или газет, а также для измерения чистоты и состава получаемого топлива. Обращайтесь: joseph.dolittle в gmail dot com для получения дополнительной информации.
Базовый эксперимент можно легко провести, нагревая биомассу в металлической бочке емкостью 55 галлонов. Может быть применен внешний огонь или установлен электрический нагревательный элемент. Выделяющиеся пары можно направить в другой барабан, погрузив его в холодную воду для образования конденсата. Во втором барабане размещается дренажное отверстие для сброса давления, и газы могут сжигаться или захватываться на этом выходе по мере протекания реакции.Когда вся биомасса будет дистиллирована, подача газа в факел прекратится.
Полученный продукт можно анализировать.
- Испытание на воспламеняемость
- Отопление для отвода воды
- Нагрев для удаления более легких фракций с получением мазута
- Дополнительный нагрев для получения более тяжелых масел или смазок
- Охлаждение на отдельные фазы
- Замораживание для разделения фаз или для разделения воды
- Использование кувшина для воды со встроенным краном позволяет легко отделить воду от топлива (аналогично разделительной воронке)
- Банку с краской в качестве реактора может быть даже проще сделать в небольшом масштабе и дешево
вот пиролизный аппарат в моем понимании:
1.вам нужна печь, вероятно, старая бочка для внешней стороны камеры сгорания, выложенная смесью шамота / песка / опилок внутри. У него будет крышка с умеренным выпускным отверстием (возможно, половина площади крышки будет удалена), которую можно было бы отлить из той же смеси шамота. Также внизу есть отверстие для топлива и воздуха. Вы могли бы запустить его на природном газе, так как в конечном итоге вы, вероятно, просто вернули бы древесный газ в более позднюю версию.
2. Камера для ввода пиролизуемого материала.можно было бы окружить дешевую камеру тонким защитным покрытием. тонкий, чтобы не препятствовать теплопередаче. огнеупорный раствор и, может быть, песок, раствор может стоить 20 долларов за все, что вам понадобится, я думаю. или вам может потребоваться труба большого диаметра и сделать для нее дно и верх из толстых (5/8 «-1/2», я думаю) металлических плит. он должен быть несколько толстым, потому что в противном случае он быстро окислится (гальванизация испарится; хром или эмаль должны будут выдерживать циклы теплового расширения / сжатия; тонкая нержавеющая сталь может быть вариантом) вверху есть отверстие для выхода, есть нет впускного отверстия.
3. тушитель. очевидно, что скорость гашения важна, так как образующиеся свободные радикалы быстро соединяются с образованием смолы и асфальта, а не более полезных веществ. Обычный способ сделать это — распылить большое количество охлажденного пиролизного масла в горячий поток внутри циклонного сепаратора (например, вашей мукомольной мельницы). Не знаю, насколько это практично. возможно, охлаждение стенок циклонного сепаратора и трубопроводов к нему также проточной водой из вашего холодного колодца подойдет.это будет нуждаться в экспериментах.
4. Газохранилище. масляная бочка, наполненная водой, перевернутая и погруженная в воду. Большая версия того, как собирают газ на уроке химии. пузыри газа через дно, и у вас есть клапан на открытой поверхности, чтобы выпустить газ на досуге. веса на вершине стержня определяют фунты на квадратный дюйм хранилища. в конечном итоге этот газ может быть просто перенаправлен обратно в печь, но сначала полезно знать, сколько газа вы получаете, а также вы можете использовать его в качестве газа для приготовления пищи, чтобы вытеснить пропан.
Сначала я говорю «пропустите 3» и просто позвольте пузырькам в воде в 4-м растворе стать закалкой. тогда вы сможете взвесить полукокс и газ и узнать, сколько нефти вы добываете. большая часть нефти, вероятно, будет в пленке на дне газосборника, но я не знаю, как влажность повлияет на нее (я думаю, что некоторые фракции полимеризуются с водой или образуют стабильную эмульсию). Теоретически это была бы лучшая закалка с точки зрения площади поверхности газа до теплоотвода, так что вы можете оценить, сколько нефти может произвести очень эффективное закалка.затем, когда у вас есть системные данные о расходах и все остальное, вы можете построить циклонный сепаратор и поиграть с некоторыми лучшими идеями гашения.
-эллиот
Реактор с циркулирующим псевдоожиженным слоем.Это видео от YouTube Г-на Теслоняна демонстрирует мелкомасштабную фракционную перегонку биомасла из дровяной печи. Очень чистый газ получают, пропуская его через микроперерабатывающий завод (с фильтрами и системой фракционной перегонки). После перегонки газ приводит в действие двигатель внутреннего сгорания, который запускает электрический генератор.
Реактор пиролиза — обзор
Газификация и пиролиз
При нагревании топливо из биомассы разлагается на ряд газообразных и конденсируемых частиц, оставляя после себя твердый углеродистый остаток, известный как уголь. Это ранняя стадия горения, и светящееся пламя, наблюдаемое при сжигании древесины и другой биомассы, является результатом окисления летучих соединений, выделяемых во время пиролиза и газификации сырья, и теплового излучения частиц сажи от пламени, дающего характерный желтый цвет. .
Когда отношение эквивалента топлива к воздуху, ϕ , в уравнении [6] существенно больше единицы (богатое топливо), топливо будет окисляться только частично из-за недостатка кислорода, и продукты реакции не будут состоять из только диоксид углерода и вода, но большие количества оксида углерода и водорода в дополнение к различным количествам газообразных углеводородов и конденсируемых соединений (смол и масел), а также полукокса и золы. Другие окислители, включая водяной пар, также могут использоваться вместо воздуха, и в этом случае набор продуктов реакции будет отличаться.Условия реакции могут быть изменены для максимального увеличения производства топливных газов, жидких топливных веществ или полукокса (как для древесного угля), в зависимости от предполагаемого энергетического рынка или рынков. Термин «газификация» применяется к процессам, которые оптимизированы для производства топливного газа (в основном, CO, H 2 и легкие углеводороды). При нагревании без добавления окислителя сырье подвергается пиролизу. Реакторы пиролиза обычно проектируются так, чтобы максимально увеличить производство жидкостей за счет быстрого, а не медленного нагрева, хотя растущий интерес к биоугля или сажи теперь меняет предпочтительную смесь продуктов.Катализаторы иногда используются для ускорения различных реакций, особенно крекинга высокомолекулярных углеводородов, образующихся во время газификации, а также в химическом каталитическом синтезе жидких углеводородов и других продуктов при производстве транспортного биотоплива.
Технология газификации была разработана более 200 лет назад (Kaupp and Goss, 1984), а в последнее время была усовершенствована в первую очередь с целью обеспечения доступа твердого топлива (биомасса, уголь и кокс) к некоторым из тех же коммерческих рынков, что и природные. газ и нефть.Газификаторы давно используются для преобразования твердого топлива в топливные газы для работы двигателей внутреннего сгорания, как с искровым зажиганием (бензин), так и с воспламенением от сжатия (дизели). Их также можно использовать для устройств внешнего сгорания, таких как котлы и двигатели Стирлинга. Наиболее распространенными типами являются газификаторы прямого действия, в которых частичное окисление сырья в топливном слое дает тепло для реакций пиролиза и газификации, которые в основном являются эндотермическими. В газификаторах непрямого действия и в реакторах пиролиза используется внешний теплообмен для обеспечения тепла, необходимого для пиролиза топлива.Тепло может быть произведено путем сжигания части исходного топлива из биомассы или путем сжигания выходящих топливных газов, жидкостей или полукокса. Аллотермические реакторы были разработаны для подачи тепла за счет внутреннего, но раздельного сжигания фазы полукокса после газификации сырья, в основном в системах с двумя реакторами (Wilk and Hofbauer, 2013). Газификаторы могут иметь меньше проблем с шлакованием золы из-за более низких рабочих температур по сравнению с камерами сгорания, хотя шлакование, засорение и агломерация слоя остаются проблемами с некоторыми видами топлива (например.г., солома).
Когда в газификаторы прямого действия подается воздух для реакции сырья, топливные газы будут содержать большое количество азота, а теплотворная способность или содержание энергии в газе будет низким (3–6 МДж м -3 ) по сравнению с природный газ (сравните метан на 36,1 МДж м -3 ) и другие более традиционные виды топлива. Двигатели без наддува, работающие на таком газе, будут иметь пониженную выходную мощность по сравнению с их работой на бензине или дизельном топливе (Jenkins and Goss, 1988).В случае дизельных двигателей газ нельзя использовать в одиночку, и для обеспечения надлежащего зажигания и выбора момента впрыскивается пилотное количество дизельного топлива. Для двигателей с искровым зажиганием выходная мощность двигателя примерно вдвое меньше, чем у того же двигателя на бензине, потому что объем воздуха в двигателе (количество воздуха, всасываемого в цилиндр двигателя во время такта впуска) уменьшается из-за большого занимаемого объема. топливным газом, и поэтому во время каждого цикла можно сжечь не так много топлива (Jenkins and Goss, 1988).Частично это можно преодолеть с помощью наддува двигателя. Для двухтопливных дизельных двигателей газ, как правило, может обеспечивать до 70% общей энергии топлива, не сталкиваясь с серьезным ударом, который возникает из-за длительной задержки зажигания, связанной с генераторным газом, тем же свойством, которое дает газу отличное октановое число ( Chancellor, 1980; Ogunlowo et al ., 1981). Те же свойства генераторного газа, которые приводят к позднему воспламенению и детонации в дизельном двигателе, делают его достаточно устойчивым к детонации в двигателе с искровым зажиганием, поэтому можно использовать степени сжатия значительно выше 10.При правильной конструкции головки блока цилиндров с увеличенной степенью сжатия эффективность двигателя может быть улучшена по сравнению с бензиновым двигателем, компенсируя некоторое снижение характеристик из-за уменьшения объема воздуха.
Если в реакторе газификации используется обогащенный или чистый кислород, полученный топливный газ или синтез-газ будет более высокого качества. Однако стоимость производства кислорода высока, и такие системы обычно предлагаются для более крупных масштабов или для производства более дорогостоящих товаров, таких как химикаты и жидкое топливо.Метанол, жидкое спиртовое топливо, CH 3 OH, образуется в каталитической реакции
[7] CO + 2h3 = Ch4OH
Этой реакции способствует низкая температура (400 ° C), но высокое давление (30– 38 МПа). Оксид цинка и оксид хрома являются общими катализаторами. Используя медь в качестве катализатора, можно снизить температуру и давление реакции (260 ° C, 5 МПа), но медь чувствительна к отравлению серой и требует хорошей очистки газов (Probstein and Hicks, 1982). Реакции Фишера-Тропша можно использовать для получения ряда химических веществ, включая спирты и алифатические углеводороды.Снижены требования к температуре и давлению, а выбор катализатора может быть получен с большей селективностью.
Жидкости, такие как бензины, могут производиться косвенными путями, включающими газификацию или пиролиз твердой биомассы для получения реакционноспособных промежуточных продуктов, которые можно каталитически улучшить (Kuester et al ., 1985; Prasad and Kuester, 1988; Kuester, 1991; Браун, 2011). Жидкости, произведенные непосредственно путем пиролиза, обычно являются коррозионными, страдают окислительной нестабильностью и не могут быть напрямую использованы в качестве моторного топлива.Многие продукты также являются канцерогенными. Как правило, для получения товарных соединений необходима какая-либо очистка. Несмотря на это, реакторы быстрого пиролиза, использующие биомассу и другие виды топлива, находятся в стадии коммерческого запуска для производства бионефти (Ensyn Corp, 2014). Жидкое топливо также можно производить прямыми термохимическими способами, такими как гидрирование в растворителе с присутствующим катализатором (Elliott et al ., 1991; Bridgwater and Bridge, 1991).
Одним из основных технических препятствий, особенно в малых масштабах, при применении газификаторов для целей, отличных от прямого сжигания сырого газа, является очистка и очистка газа.Удаление твердых частиц и смол из газа имеет решающее значение для последующего производства электроэнергии и синтеза топлива. Смолы представляют собой класс тяжелых органических материалов, которые особенно трудно удалить или обработать. Существуют системы для производства газа приемлемого качества, но, как правило, они полагаются на некоторую комбинацию влажной и сухой очистки и фильтрации и увеличивают расходы на систему конверсии. Маломасштабные газификаторы, используемые для удаленного производства электроэнергии, часто применялись без надлежащих процедур обращения с гудроном, отделенным от газа.Очистка газа и обработка гудрона остаются критическими инженерными задачами для более широкого внедрения технологии во всех масштабах.
Усовершенствованные варианты производства электроэнергии из биомассы включают использование газификатора биомассы для производства топливного газа для газовой турбины в интегрированной системе с комбинированным циклом газификации (Рисунок 17; Меерман и др. ., 2013). Эффективность этих систем может быть значительно выше, чем у традиционных систем выработки электроэнергии с циклом Ренкина. Основные технические задачи включают очистку горячего газа для получения газа надлежащего качества, чтобы избежать загрязнения турбины, а также разработку надежных реакторов или компрессоров высокого давления и систем подачи топлива.Считается, что использование газогенератора является преимуществом по сравнению с камерой сгорания с прямым сгоранием, поскольку потери тепла в системе газоочистки вызывают меньшее беспокойство, поскольку большая часть энергии топлива находится в форме химической энергии получаемого газа. Другие преимущества газификаторов перед камерами сгорания включают способность работать при более низких температурах и меньшие объемы газа на единицу преобразованного сырья, что способствует удалению соединений серы и азота для снижения выбросов загрязняющих веществ. Системы этого типа в настоящее время находятся в стадии разработки, и несколько крупномасштабных демонстрационных проектов были завершены, но эта технология еще не была внедрена в коммерческих целях для биомассы, хотя она применяется для угля в более крупных масштабах (Stahl and Neergaard, 1998).Фиг.17 также иллюстрирует возможное использование впрыска пара для уменьшения тепловых выбросов NO x и увеличения выходной мощности газовой турбины. Высокая теплоемкость пара по сравнению с продуктами сгорания приводит к увеличению мощности, а добавление пара снижает температуру пламени, что способствует снижению термического образования NO x (Weston, 1992). Многие другие варианты термохимической конверсии находятся в стадии разработки (Brown, 2011).
Рисунок 17. Передовая концепция выработки электроэнергии с комбинированным циклом с интегрированной газификацией. Показана газификация сжатым воздухом. Также показан вариант газовой турбины с впрыском пара (IG / STIG).
пластик для топлива проектов
Проекты по использованию пластика в качестве топлива начинают набирать обороты в энергетической отрасли, поскольку растущее понимание значительного экологического ущерба, наносимого одноразовыми пластиками, и недостаточных привычек людей к переработке отходов побуждает исследователей обращаться к альтернативным методам утилизации для растущего объема производства пластика.
В таких проектах для создания топлива используется химическая энергия, хранящаяся в углеводородной структуре материала. Этот метод получил высокую оценку за его экономические и экологические преимущества, но по большей части остался на стадии разработки.
Сейчас эти схемы начинают развиваться. Здесь Future Power рассматривает некоторые из наиболее инновационных примеров.
Зачем превращать пластик в топливо?По оценкам, менее 5% пластика, производимого каждый год, перерабатывается, при этом производство материала должно увеличиться на 3.8% ежегодно до 2030 года, добавляя к 6,3 миллиардам тонн, произведенным с момента начала производства 60 лет назад. Большинство из них попадает в наши океаны, нарушая морские экосистемы, и, по прогнозам исследователей, на биоразложение потребуется как минимум 450 лет, если вообще когда-либо.
Использование пластмассы в качестве топлива обещает не только в ограничении такого повсеместного загрязнения, но и в обеспечении значительной экономической выгоды для регионов. По оценкам Американского химического совета, только в США предприятия по переработке пластика в топливо создадут около 39 000 рабочих мест и обеспечат экономическое производство почти на 9 миллиардов долларов, что сделает глобальный рыночный потенциал такой отрасли огромным.
Топливо, полученное из пластмасс, также способно производить более чистое горючее, чем традиционные источники, из-за низкого содержания серы, учитывая, что большинство развивающихся стран используют дизельное топливо с высоким содержанием серы.
Из пластика в водородСовсем недавно исследователи из Университета Суонси открыли способ превращения пластиковых отходов в водородное топливо, которое, по их словам, однажды можно будет использовать для двигателей.
Команда добавила светопоглощающий фотокатализатор в пластмассовые изделия — материал, который поглощает солнечный свет и преобразует его в химическую энергию в процессе, называемом «фотореформирование».Затем комбинация пластика и катализатора была оставлена в щелочном растворе под воздействием солнечного света, что привело к разрушению материала и образованию пузырьков газообразного водорода в процессе.
Новый метод будет дешевле, чем существующие варианты переработки, так как любой пластик можно использовать без необходимости очистки. По данным The Balance Small Business, в настоящее время переработка тонны пластиковых пакетов стоит около 4000 долларов, что часто приводит к сжиганию или выбрасыванию пластиковых отходов на свалку, чтобы избежать расходов.
Тематические отчеты
Беспокоитесь ли вы о темпах инноваций в вашей отрасли?
В отчетеGlobalData по темам TMT за 2021 год рассказывается все, что вам нужно знать о темах подрывных технологий и о том, какие компании лучше всего могут помочь вам в цифровой трансформации вашего бизнеса.
Узнать большеДоктор Мориц Кюхнель из химического факультета университета сказал: «Ежегодно используется много пластика — миллиарды тонн — и только небольшая его часть перерабатывается. Мы пытаемся найти применение тому, что не перерабатывается.
Прелесть этого процесса в том, что он не очень требователен.Он может привести к разложению всех видов отходов ».
В настоящее время команда пытается расширить процесс с нынешних миллиграммов пластика на использование процесса фотореформирования для более крупных деталей.
Хотя могут пройти годы, прежде чем этот процесс превращения пластика в топливо можно будет внедрить на промышленном уровне, его развитие будет хорошо работать в тандеме с появлением водородных транспортных средств. В настоящее время таких автомобилей на наших дорогах нет, хотя у ряда компаний есть большие планы. Например, Toyota заявила о своей цели продать один миллион электрических и топливных автомобилей по всему миру к 2030 году, а в 2020 году она также планирует выпустить автобус на топливных элементах.
Пластмасса к дизельному топливуХимики из Калифорнийского университета , Ирвин (Калифорния), , в сотрудничестве с исследователями из Шанхайского института органической химии, разработали метод переработки пластика, который позволяет им растворять связи полиэтиленового пластика для создания нефти и других топливных продуктов. .
Хотя необработанный полиэтилен может быть разрушен, он требует либо значительного количества тепла, либо химически активных токсичных химикатов, что приводит к разрушению атомных связей непригодным для использования способом.В отличие от этого, процесс, разработанный исследователями, использует гораздо меньше тепла и позволяет превратить конечный продукт в новый источник топлива.
Команда, возглавляемая химиком из Калифорнийского университета в Ирвине Жибином Гуаном, использовала тип углеводородной молекулы, известный как алканы, которые обычно используются для производства полимеров, хотя здесь они использовались для разложения полимеров. Постепенно удаляя и добавляя связи между атомами углерода и водорода в материале, команда смогла преобразовать полиэтилен в жидкое топливо, которое можно использовать в автомобилях или других промышленных целях.
Используемые катализаторы также совместимы с различными типами полиолефиновых добавок, что означает, что пластиковые отходы, такие как бутылки, пакеты и пленка, могут быть превращены в химическое сырье без необходимости какой-либо предварительной обработки.
Пластмасса к сырой нефтиВ 2016 году исследователи Центра устойчивых технологий Иллинойса Б.К. Шарма и Кишор Раджагопалан в сотрудничестве с Министерством сельского хозяйства США успешно переработали пластиковые пакеты в топливо.
Команда использовала полиэтиленовые пакеты высокой плотности, полученные от местных розничных продавцов, и загрузила их в установку пиролиза, создавая при этом пластиковую сырую нефть (PCO).Затем они перегоняли PCO, чтобы получить бензин и два типа дизельного топлива. После добавления антиоксидантов полученные материалы оказались лучше обычных дизельных топлив с точки зрения смазывающей способности и производного цетанового числа, что демонстрирует качество воспламенения.
От пластика до серыАмериканская компания Plastic2Oil работает над превращением пластиковых отходов в серное топливо, используя выброшенный материал в качестве сырья для создания «дизельного топлива со сверхнизким содержанием серы», которое содержит 15 частей на миллион или ниже.
В настоящее время дизельное топливо со сверхнизким содержанием серы в основном производится из нефти, хотя Plastic2Oil представляет собой жизнеспособную альтернативу топливу, полученному из пластика. Обработчик фирмы принимает немытый и несортированный пластик, производя около одного галлона топлива из 8,3 фунта материала. В качестве топлива процессор использует собственные отходящие газы (примерно 10–12% от производительности процесса), что означает, что для работы машины требуется минимальное количество энергии. Произведенное топливо также может быть очищено и отделено без затрат на дистилляционную колонну.
Есть минусы?Отрасль по переработке отходов в топливо вызвала некоторое сопротивление со стороны природоохранных организаций: протесты привели к остановке запланированного объекта по переработке отходов в топливо в Ланкашире в прошлом году, а в Канберре, Австралия, после жалоб экологов было начато расследование.
Ларри О’Лафлин, исполнительный директор ACT Conservation Council, рассказал корреспонденту The Guardian об экологической угрозе, которую, по его словам, представляют свалки для переработки отходов в пластик.Он отверг представление о том, что промышленность — это форма вторичной переработки, поскольку пластмассы можно использовать только один раз, прежде чем они будут превращены в топливо. Он также утверждал, что широкое распространение этого метода может замедлить усилия по поиску альтернативных видов топлива, сказав: «В период сокращения выбросов углерода они вводят другое ископаемое топливо. ACT пытается перейти к нулевым выбросам к 2050 году. Как мы собираемся этого добиться, создав здесь нефтеперерабатывающий завод? »
Связанные компании
WEYTEC
Высокотехнологичные решения для энергетики
28 августа 2020
ESI Eurosilo
Расширенные решения для хранения сыпучих материалов
28 августа 2020
Изготовление Biochar для улучшения почвы
В прошлом году я совершил один из величайших грехов садоводства: позволил сорнякам прорасти.Осенью убираясь, я столкнулся с тонной семеносного лисохвоста, лопуха и злаковых трав. Конечно, я мог бы приготовить горячий компост, чтобы пропарить семена сорняков до смерти, но вместо этого я решил попробовать что-то другое. Я вырыл канаву, насыпал сорняки и много древесных обрезков и сжег ее, получив таким образом биоуголь. Это был мой новый способ улучшить почву — за исключением того, что этому методу не менее 3000 лет.
Что такое biochar? По сути, это органическое вещество, которое сжигается медленно, с ограниченным потоком кислорода, а затем огонь прекращается, когда материал достигает стадии древесного угля.В отличие от крошечных кусочков пепла, крупные куски древесного угля полны щелей и отверстий, которые помогают им служить спасательными плотами для почвенных микроорганизмов. Углеродные соединения в древесном угле образуют слабые химические связи с растворимыми питательными веществами для растений, поэтому они не так легко вымываются дождем и орошением. Сам по себе Biochar, добавленный в бедную почву, мало полезен для растений, но при использовании в сочетании с компостом и органическими удобрениями он может значительно улучшить рост растений, помогая удерживать питательные вещества в почве.
Темные земли Амазонки
Идея biochar пришла из дождевых лесов Амазонки в Бразилии, где цивилизация процветала 2000 лет, примерно с 500 г. до н. Э. до тех пор, пока испанские и португальские исследователи не представили разрушительные европейские болезни в середине 1500-х годов. Используя только свои руки, палки и каменные топоры, амазонские племена выращивали маниоку, кукурузу и многочисленные плоды деревьев на почве, богатой компостом, мульчей и тлеющими растениями.
Удивительно, но эти «темные земли» сохранились и сегодня как свидетельство древнего метода создания почвы, который вы можете использовать в своем саду.Ученые расходятся во мнениях относительно того, были ли почвы созданы специально, чтобы выращивать больше еды, или они были случайным побочным продуктом биочара и компоста, образующихся в повседневной деревенской жизни на берегах самой большой реки Земли. Как бы они ни возникли, нет никаких сомнений в том, что амазонские темные земли (часто называемые terra preta ) содержат питательные вещества для растений, включая азот, фосфор, кальций и магний, гораздо эффективнее, чем неулучшенная почва. Даже после 500 лет тропических температур и осадков, выпадающих в среднем 80 дюймов в год, темные земли остаются удивительно плодородными.
Ученые всего мира работают в лабораториях и на полевых испытательных площадках, чтобы лучше понять, как работает biochar, и разгадать множество загадок terra preta . В Корнельском университете в Итаке, штат Нью-Йорк, микробиологи обнаружили в почвах terra preta бактерии, похожие на штаммы, которые активны в кучах горячего компоста. Общие популяции грибов и бактерий также высоки в почвах terra preta , но присутствие большого количества углерода заставляет микроорганизмы жить и размножаться медленными темпами.В результате снижается скорость оборота органических веществ в почве, поэтому компосты и другие обогащающие почву формы органического вещества служат дольше.
В полевых испытаниях с кукурузой, рисом и многими другими культурами biochar повысил урожайность, сделав питательные вещества, уже присутствующие в почве, более доступными для растений. Результаты особенно впечатляющи, когда biochar добавлен в хорошую почву, которая содержит достаточное количество минералов и питательных веществ для растений. Исследования продолжаются (отслеживайте это в Международной инициативе по биочару), но на данный момент кажется, что биочар увеличивает выносливость как органического вещества, так и микроорганизмов в органически обогащенной почве.Выкопание кусочков биоугля — или добавление их в компост, поскольку он отложен на лечение — может замедлить вымывание питательных веществ и помочь органически обогащенной почве сохранять питательные вещества на десятилетия, а не на пару сезонов.
В поисках бесплатного Biochar
ТалантBiochar в области почвообразования может изменить способ очистки дровяной печи. В дополнение к сбору золы (и хранению ее в сухой металлической банке до тех пор, пока вы не будете готовы использовать ее в качестве обогащенной фосфором почвенной добавки, применяемой в виде легкой пыли), возьмите за привычку собирать обугленные остатки бревен.Отнесите их в свой сад, хорошенько ударите их лопатой, и у вас есть biochar.
Если вы живете недалеко от кемпинга, у вас может быть доступ к неограниченному запасу пригодного для сада биоугля из остатков частично сгоревших костров. Небольшие костры, горящие в дымоходах, также часто приводят к образованию биоугля, поэтому вам, возможно, придется искать стабильную поставку не дальше, чем колода вашего соседа.
Угольные брикеты, используемые для гриля, вероятно, не лучший выбор. Те, которые предназначены для светостойкости, часто включают парафин или другие углеводородные растворители, которым нет места в органическом саду.Обычные обугленные сорняки, древесина или коровьи пироги — лучшие материалы для использования этой многообещающей техники почвообразования, основанной на древней садоводческой мудрости.
Как сделать Biochar
Чтобы сделать biochar прямо в вашем саду, начните с рытья траншеи в грядке. (Используйте вилку, чтобы разрыхлить почву на дне траншеи, и вы получите дополнительные преимущества этой техники «двойного копания».) Затем насыпьте щетку в траншею и подожгите ее. Вы хотите, чтобы огонь начинался горячим, но быстро замедлялся за счет уменьшения подачи кислорода.Лучший способ узнать, что происходит в огне биоугля, — это наблюдать за дымом. Белый дым, образовавшийся на ранней стадии, в основном состоит из водяного пара. По мере того, как дым становится желтым, смолы и сахар в материале сгорают. Когда дым станет густым и станет серовато-синим, ослабьте огонь, накрыв его примерно на дюйм земли, чтобы уменьшить приток воздуха, и дайте ему тлеть. Затем, когда органические вещества превратятся в куски древесного угля, используйте воду, чтобы потушить огонь. Другой вариант — сделать древесный уголь из обрезков дерева в металлических бочках.(За подробностями обращайтесь в Twin Oaks Forge.)
Я принадлежу к поколению Smokey-the-Bear, воспитанному на таких фразах, как «научись не гореть», поэтому мне потребовалось время, чтобы разогреться до идеи использования полуоткрытого сжигания в качестве метода создания почвы. Безудержное открытое сжигание высвобождает 95 или более процентов углерода, содержащегося в древесине, сорняках или чем-либо еще, что попадает в дым. Однако при низкотемпературном контролируемом сжигании для создания биоугля, называемом пиролизом, на начальной стадии горения сохраняется гораздо больше углерода (около 50 процентов).Выбросы углерода сокращаются еще больше, когда биоуголь становится частью почвы, где он может снизить производство парниковых газов, включая метан и закись азота. Этот древесный уголь выделяет углерод в 10-100 раз медленнее, чем гниение органического вещества. Если это сделано правильно, контролируемое обугливание сорняков, обрезанных ветвей и других трудно поддающихся компостированию форм органических веществ, а затем использование biochar в качестве добавки для почвы или компоста, может привести к системе круговорота углерода с нулевым выбросом.
Ответственное сжигание требует простого здравого смысла.Проконсультируйтесь с местной пожарной службой, чтобы убедиться, что у вас есть все необходимые разрешения, подождите, пока не станет сыро и безветренная погода, и следите за огнем, пока он не потухнет.
Изображение большего размера
Если мы хотим замедлить глобальное потепление, мы должны найти способы уменьшить потери углерода в атмосферу. На темных землях Амазонки и в залежах древесного угля под Тихим океаном, которым уже миллион лет, древесный уголь доказал свою способность практически полностью прекратить выброс углерода.Если бы каждый из миллиона фермеров по всему миру внедрил биоуголь на 160 акров земли, количество углерода, заблокированного в почве Земли, увеличилось бы в пять раз.
Но это еще не все. Что, если вы генерируете энергию, сжигая урожай возобновляемой биомассы (например, дерево, кукурузу, скорлупу арахиса, бамбук, иву или что-то еще), производя при этом биоуголь, который затем прячут, используя его в качестве почвенной добавки? (Например, см. Статью в архиве «Мамина дровяная машина» о генераторах древесного газа.) Показатели извлечения углерода в такой системе делают ее единственной обнаруженной на данный момент моделью биомассы, которая может производить энергию без чистого выброса углерода. Исследовательские группы по всему миру изо всех сил стараются проработать детали этих изящно расположенных на Земле систем.
Еще многое предстоит узнать о том, как должны работать системы biochar, но некоторые из них могут быть такими же простыми, как установки на ферме, которые превращают навоз и другие отходы в крупицы черного углерода, которые помогают удобрениям продвигаться дальше, удерживая углерод в почве.
Как садовники, мы должны найти способы адаптировать эти новые знания к потребностям нашей земли. Чтобы максимально использовать свой костер из сорняков, я устроил сжигание в траншеи, вырытой в моем саду, а затем использовал выкопанную землю, чтобы потушить огонь. Слой biochar теперь покоится в почве. Через сотни лет он по-прежнему будет удерживать углерод, питая почвенную пищевую сеть. Это простое слияние почвы и огня, впервые обнаруженное древними людьми на Амазонке, может быть «новым» ключом к питанию и восстановлению здоровья нашей планеты.
Чтобы узнать больше об этой увлекательной теме, прочтите « Amazonian Dark Earths » Йоханнеса Леманна.
Сотрудник редактора Барбара Плезант сады на юго-западе Вирджинии, где она выращивает овощи, травы, фрукты, цветы и несколько счастливчиков. Свяжитесь с Барбарой, посетив ее веб-сайт .
Первоначально опубликовано: февраль / март 2009 г.
краткая история и развитие будущего
- В своей недавней книге я сказал, что, возможно, единственный инструмент, который у нас был для того, чтобы вернуть углекислый газ на доиндустриальный уровень, — это позволить биосфере перекачивать его из воздуха для нас.В настоящее время он удаляет 550 миллиардов тонн в год, что примерно в 18 раз больше, чем мы выбрасываем, но 99,9% уловленного таким образом углерода возвращается в воздух в виде CO2, когда что-то съедается. Что нам нужно сделать, так это превратить часть всех сельскохозяйственных отходов в древесный уголь и закопать их. Рассмотрите зерно, например, пшеницу или рис; большая часть растительной массы находится в стеблях, стеблях и корнях, и мы едим только семена. Поэтому вместо того, чтобы просто вспахивать стебли или превращать их в картон, превратите его в древесный уголь и закопайте его или погрузите в океан.Нам не нужны плантации или посевы для биоугля, нам нужен угольщик на каждой ферме, чтобы фермер мог превращать свои отходы в углерод. Что нам нужно сделать, так это превратить часть всех сельскохозяйственных отходов в древесный уголь и закопать их. Рассмотрите зерно, например, пшеницу или рис; большая часть растительной массы находится в стеблях, стеблях и корнях, и мы едим только семена. Так что вместо того, чтобы просто вспахивать стебли или превращать их в картон, превратите их в древесный уголь и закопайте его или затопите в океане … Между прочим, при производстве древесного угля таким способом получается побочный продукт биотоплива, который фермер может продать.Если мы хотим, чтобы эта идея работала, жизненно важно, чтобы она окупалась и не требовала субсидий. Субсидии почти всегда порождают мошенничество, и это верно в отношении большинства предлагаемых и используемых в настоящее время форм возобновляемой энергии. Никто не станет вкладывать средства в плантации для производства древесного угля без субсидий, но если мы сможем показать фермерам, что они могут использовать свои отходы для получения прибыли, они сделают это свободно и помогут нам и Гайе тоже.
Доктор Джеймс Лавлок
Biochar — древесный уголь, полученный путем пиролиза биомассы — в последние годы получил огромное внимание и поддержку и стал одним из потенциально наиболее полезных методов восстановления почвы и связывания углерода в современную эпоху.Несмотря на то, что множество инициатив в области исследования и применения biochar начали действовать, многие важные детали остаются неясными.
К счастью, влияние биочара на производство и почву имеет давний исторический прецедент, а также удивительную легкость глобального распространения. Эти факторы в сочетании с совместными базами данных biochar, онлайн-форумами и информационно-просветительскими проектами создают основу для того, что может быстро стать прорывной тенденцией в экологических исследованиях и восстановлении окружающей среды: самостоятельной адаптации к проблемам глобальных изменений 21 века.
Считается, что использование биоугля для сохранения и улучшения питательных веществ в почве возникло более 2000 лет назад в бразильской Амазонии. Археологические исследования показывают, что популяции коренных жителей Амазонки процветали в аграрных цивилизациях, поддерживаясь за счет изменения бедных питательными веществами тропических почв с применением древесного угля (также известного как biochar) и органических веществ. Эти популяции, по-видимому, процветали в период между 400 г. до н.э., пока не были истреблены пандемией, введенной испанскими экспедициями всего 500 лет назад.
Амазонки, как полагали, производили биоуголь, зажигая, а затем закапывая и тлея биомассу, чтобы создать условия с низким содержанием кислорода, необходимые для создания древесного угля. Этот метод известен как подсечно-огневое земледелие и приводит к улавливанию до 50% углерода, в отличие от методов подсечно-огневого производства, которые дают более высокий уровень золы и улавливание углерода только от 1% до 3%.
В середине 1500-х годов испанский исследователь Франсиско де Орельяна привел несколько сотен пехотинцев и всадников в дельты бразильской Амазонки (Шингу) с целью основать поселения в устье и внутри реки.Орельяна сообщил, что в то время в регионе Амазонки процветала развитая цивилизация. Свидетельства геоглифов и обширных измененных почв terra preta (biochar), датируемых периодом 0–1250 гг. Нашей эры, подтверждают утверждения Орельяны. Современные археологические исследования, проводимые Майклом Хеккенбергером и Эдуардо Гус Невесом, выявили остатки древних городов, «шоссе» шириной 60 футов и почвы, плодородные благодаря биоуглю, в регионах Амазонки, которые посетила экспедиция Орельяны. Считается, что население около 5 миллионов человек процветало в этом районе в 1500 году нашей эры, уменьшилось из-за пандемии до 1 миллиона к 1900 году и менее 200 000 к 1980-м годам.
В настоящее время тысячи гектаров антропогенных, богатых питательными веществами биоугля остаются в районе Шингу в Амазонии, в отличие от обычно истощенных тропических почв. Эти уникальные почвы предоставили ученым, садоводам и защитникам окружающей среды доказательства длительного положительного воздействия биоугля и подтвердили, что он является стабильной, изолированной формой углерода, способной влиять на современные концентрации парниковых газов.
На изображении слева вверху изображено большое фиговое дерево-душитель недалеко от Пуэрто-Хименеса, Коста-Рика.Многие деревья и растения тропиков нового мира адаптировались к типично бедным питательными веществами, сильно выветрившимся тропическим почвам, создав сложные корневые структуры и опоры, которые простираются на широких, но неглубоких участках вокруг центрального ствола. Поскольку подавляющее большинство доступных для растений питательных веществ в тропических лесах, как правило, находится в верхнем слое почвы, эти приспособления позволяют растениям поддерживать большие конструкции, не расширяя глубокие корни. Когда тропический лес разрушается или деградирует, потеря постоянного поступления свежей биомассы делает почвы бесплодными.Добавки Biochar для этих почв предлагают ряд долгосрочных преимуществ и в целом способствуют повышению урожайности. Изображение справа от инжира-душителя сравнивает типичную бедную питательными веществами красноватую тропическую почву (оксисол), контрастирующую справа с более темным, более плодородным оксисолом с добавлением биогара. |
Археологические открытия амазонских племен и почвы terra preta предполагают увлекательную связь между историческими применениями biochar в неиерархических, устойчивых сложных человеческих обществах, представляя убедительные возможности для современных моделей сетевых методов устойчивости.Автор и защитник биочаров Джеймс Брюгге признает связь между плодородными почвами и неиерархическими сложными человеческими обществами в своем тексте «Дебаты о биочаре». Брюгге комментирует наблюдения Ореллены: «В этом и других описаниях нет упоминания пирамид, как в цивилизации майя, ни крепостных валов, ни иерархии величественных зданий, окруженных лачугами. Разве это слишком много, чтобы предполагать, что обильное плодородие почвы устранило потребность в высокоцентрализованном авторитарном обществе? »
Так же, как стабильная плодородная почва могла укрепить структуру прошлых децентрализованных обществ, биоугля и усовершенствованные методы ведения сельского хозяйства полезны для отдельных лиц, небольших групп и устойчивых сообществ, стремящихся к продовольственной независимости.
Технический опыт, необходимый для создания и применения биоугля для улучшения почвы, биоремедиации и связывания углерода, минимален, и его можно легко изучить и проинструктировать через онлайн-форумы, общественные семинары и информационно-просветительские проекты. Современное человеческое население может использовать многие преимущества biochar, чтобы восстановить элементы свободы от неэффективных, неустойчивых промышленных и коммерческих методов ведения сельского хозяйства.
Прототип печи с биочагом UIRI с термоэлектрическим генератором. |
Применение Biochar было протестировано в различных почвах и климатических условиях, обычно демонстрируя положительный эффект в широком диапазоне глобальных экосистем. В деградированных почвах Среднего Запада Северной Америки, например, исследователи из исследовательских ферм сельскохозяйственного машиностроения Университета штата Айова сообщают о повышении урожайности сельскохозяйственных культур с использованием биоугля. Институт промышленных исследований Уганды (UIRI) совместно с Китайским исследовательским центром по бамбуку (CBRC) отметили положительные результаты в урожайности растений на бедных питательными веществами почвах с использованием биоугля из сельскохозяйственных отходов и избытка бамбука.В рамках проектов UIRI и CBRC в Уганде были разработаны печи на биоугле, способные вырабатывать электроэнергию и тепло, снижая при этом дымность и загрязнение, характерные для дровяных печей.
ПроизводствоBiochar предлагает широкий спектр экономических и экологических преимуществ по трем основным категориям:
- Снижение выбросов парниковых газов — многие детали способности биоугля удерживать углерод в неактивных поглотителях в течение тысяч лет и подавлять выбросы в почву сильнодействующих парниковых газов, включая закись азота и метан, были научно изучены и обоснованы.Однако сложный системный характер изменения климата требует гораздо более глубоких экспериментов и сотрудничества. Biochar может оказаться одним из наиболее полезных методов связывания углерода, но его необходимо сочетать с огромными усилиями по сокращению выбросов.
- Поправка для почвы — включает восстановление обедненных почв, удержание питательных веществ и биоремедиацию. Biochar показал положительные результаты в устранении токсинов тяжелых металлов, стока удобрений, разливов нефти, полициклических ароматических углеводородов (ПАУ) и различных процессов восстановления растительного покрова.
- Внешние эффекты и побочные продукты пиролиза — уменьшение загрязнения от дровяных печей, выработка тепла, производство биотоплива. Был разработан широкий спектр процессоров и прототипов biochar, чтобы использовать различные полезные побочные потоки производства. Большинство из этих проектов находятся в свободном доступе в Интернете, и их относительно легко построить.
Чтобы получить дополнительную информацию о применении biochar в развивающихся сообществах, я проконсультировался с соучредителем и президентом Seattle Biochar Working Group (SeaChar) Артом Доннелли.Доннелли обладает более чем 20-летним опытом работы с индивидуальным дизайном из металла, имеет степень бакалавра искусств Вашингтонского университета и степень MFA Школы дизайна Род-Айленда. Работая с фермерами, выращивающими кофе в Коста-Рике, SeaChar запустила проект Estufa Finca («Фермерская плита») в январе 2010 года. Кухонная плита Estufa Finca, производимая biochar, была первоначально разработана Доннелли для использования мигрантами-сборщиками кофейных зерен, живущими в лагеря сельскохозяйственных рабочих для мигрантов. Все печи проекта построены в Коста-Рике с использованием местных материалов.Последние два года идет постоянный процесс доработки печей. На сегодняшний день команда партнеров Estufa Finca участвовала в строительстве и продаже 260 кухонных плит Estufa Finca.
В связи с тем, что местная женская группа строит и раздает печи в кофейной стране, SeaChar сместила акцент на регион Таламанка на юго-востоке Коста-Рики.
Арт Доннелли из SeaChar подробно описывает детали проекта:
Сейчас мы работаем с местными фермерами, выращивающими какао и бананы Брибри в этой области.Возможность работать с постоянным населением, живущим в своих собственных домах, позволила нам провести более глубокие полевые испытания нашего инновационного подхода к продвижению печей, основанного на сообществе, как поддержать новых пользователей печей и повысить рыночную стоимость биоугля. печи производим. Грант от National Geographic 2011 года позволил нам нанять и обучить местных промоутеров печей продавать печи и обучать их соседей, как ими пользоваться. Нашим новым владельцам печей предлагается возможность принять участие в нашей программе обратного выкупа biochar.Некоторые из наших поваров зарабатывают дополнительно 30 долларов в месяц, сберегая и продавая нам свой biochar.
За первые 5 месяцев этой программы мы собрали более двух тонн высококачественного биоугля от пользователей печей. Biochar, который мы покупаем, используется на текущих участках и в горшках с нашим университетом и партнерами по коммерческим питомникам, некоторые из них были пожертвованы двум местным проектам школьных садов, с которыми мы работаем, и многое другое было использовано в нашей продолжающейся серии семинаров по biochar для фермеров.В настоящее время мы также продаем biochar небольшому количеству питомников и производителей органической продукции.
Недавно в один особенно приятный день в пуэбло Суретки я был в доме семьи, которая вскоре должна была проводить предстоящий раунд семинаров по обучению поваров. Дон Даниэль, дедушка семьи, занимается выращиванием какао почти 60 лет. Дон Дэниел посетил один из наших семинаров по биоугля для фермеров. Он увидел одну из наших барабанных печей для обжига биоугля на 55 галлонов. Дон Даниэль пригласил меня обратно в свой сад, где он с гордостью показал мне копию нашей печи, которую он построил на основе хорошей памяти и доступного лома.Обугленный в его приподнятых кроватях показал, что он извлекал из этого пользу.
SeaChar также работает с Центром исследований и образования в области тропического сельского хозяйства (CATIE) над многолетним исследованием влияния биоугля на выращивание бананов и какао. Бразильский аспирант Джуллиано Ходжа да Силва был ведущим исследователем в прошлом году. Среди гипотез, которые мы проверяем, является то, что нанесение biochar вокруг капельной линии деревьев может снизить заболеваемость
грибковое заболевание органического какао.Мы опубликуем данные Джулиано за первый год в середине декабря. Предварительные результаты выглядят многообещающими. Тестирование с использованием biochar и бананов начнется в 2013 году. Технология Biochar и biochar представляет собой новую мощную платформу для разработки. Однако для того, чтобы эти концепции стали реальностью, необходимо разработать и протестировать в реальном мире семейство простых, элегантных и надежных инструментов. SeaChar совместно с местными партнерами создает эту технологию на местах. Мы планируем как можно шире делиться извлеченными уроками.
Крупномасштабное производство биоугля через проекты когенерации представляет собой очень реальную инвестиционную возможность. Экономически важные высококачественные экспортные культуры Коста-Рики, такие как кофе, какао,
банана и ананаса нуждаются как в эффективных органических удобрениях почвы, так и в чистом сжигании тепла биомассы. Рост спроса на органическую продукцию премиум-класса превышает возможности производителей региона. Основным ограничивающим фактором является отсутствие эффективных органических удобрений и удобрений.Древесный уголь уже пользуется спросом для изготовления богатого ферментами компоста, известного как бокаши. Вызов будет к
отличает biochar, который нужно будет продавать по более высокой цене за килограмм, от штрафов, оставшихся от традиционного производства древесного угля.
В то же время меняющийся климат стимулирует рост спроса на тепловую энергию для сушки таких товаров, как кофе и какао-бобы. Для сельскохозяйственных производителей, таких как наш партнер APPTA (ассоциация производителей органической продукции из 1200 членов), отсутствие рентабельной и экологически устойчивой технологии сушки является основным препятствием для производства.
Интегративный подход SeaChar к biochar демонстрирует его полезность при проектировании систем с учетом социальных и экологических требований, сочетая восстановление почвы с научными исследованиями в области биоремедиации, улучшения сельского хозяйства, связывания углерода, экономических возможностей и огромного потенциала для дальнейшего развития.
Организации Biochar, предлагающие информацию о производстве DIY, можно найти по следующим ссылкам:
Статьи по теме
(PDF) Пиролиз пламегасителя Кон-Тики для демократизации производства биоугля
Ithaka Journal 2014 — под редакцией Института углеродной разведки Итаки — www.ithaka-journal.net 348
и инструкции по сборке с теми, кто готов разделить наши затраты на исследования и разработки
.
По мере того, как печь Кон-Тики ловит воздух по всему миру, мы
планируем поделиться фотографиями и историями из краев Кон-Тики —
мужчин от Амазонки до Замбии, от Швейцарии до
Непала и из Тасмания в Калифорнию: пришлите нам
ваших фотографий и впечатлений от Кон-Тики, чтобы они были включены в
карту мира Кон-Тики.
Комментарии рецензента
Ломас Бучели: Эта статья знакомит с ролизером Kon-Tiki py-
для производства высококачественного биоугля в местном масштабе
. Благодаря своей простоте, доступности и надежности,
имеет значительный потенциал применения для индивидуальных пользователей
во многих ситуациях по всему миру. На мой взгляд, способ написания статьи
является хорошим примером того, как
практические аспекты производства биоугля могут (и должны) сочетаться с тщательным и систематическим исследованием
процесса пиролиза, и полученный продукт, даже
(и особенно) на «низкотехнологичном» уровне.Такие системы
должны быть не только легкими и простыми в использовании, но и безопасными для операторов
, местного населения и окружающей среды. Хотя дальнейшая (количественная) характеристика и оптимизация
этого типа пиролизера и его biochar по-прежнему требуются
, мы решительно поддерживаем презентацию Kon-Tiki
сообществу biochar в форме этой статьи и мотивации читателей. мир, чтобы создать и передать
свой собственный опыт с ним.
Саймон Шекли: «Новаторская разработка печи
Kon-Tiki, разработанная Хансом-Петером Шмидтом и Полом Тейлором» — это
, значительный шаг вперед в сообществе biochar. Когда
было осознано негативное воздействие загрязняющих веществ, возникающих в результате традиционного производства древесного угля, мы все обратились к
более высокотехнологичным решениям. Расходы быстро росли, и
вышло далеко за пределы карманов большинства потенциальных производителей
и пользователей biochar.Гениальность Kon-Tiki
заключается в том, что ей удается сочетать низкие начальные затраты простой печи
с соблюдением требований чистого производства
при производстве чистого высококачественного материала. Испытания
Кон-Тики сейчас проходят во многих странах, и доказательная база
будет быстро накапливаться. Нашим
мы обязаны изобретателям за то, что избавили нас от жернова
чрезмерно сложной и слишком дорогой технологии пиролиза!
Список литературы
Бучели Т.D., Hilber, I., Schmidt, HP, 2015. Полициклические ароматические
углеводородов и полихлорированные ароматические соединения в
biochar, in: earthscan, London, U. (Ed.), Biochar for En-
vironmental Management: Наука и технология.
Carlowitz, H.C. von C., 2013. Sylvicultura oeconomica oder
Haußwirthliche Nachricht und Naturmäßige Anweisung
zur Wilden Baum-Zucht, oekom verl. изд. München.
Крискуоли, И., Альберти, Г., Баронти, С., Favilli, F., Martinez, C.,
Calzolari, C., Pusceddu, E., Rumpel, C., Viola, R., Miglietta,
F., 2014. Связывание углерода и фертильность после столетия
шкала времени внедрение древесного угля в почву. PLoS One 9,
e
.Eckmeier, E., Gerlach, R., Tegtmeier, U., Schmidt, MWI, 2008.
Обугленные органические вещества и фосфор в черноземах в
бассейне Нижнего Рейна (Северо-Западная Германия) указывают на до
исторических сельскохозяйственное сжигание.В: Fiorentino, G; Magri, D.
Древесный уголь из прошлого: культурные и палеоэкологические последствия
, in: Fiorentino, G., Magri, D. (Eds.), Charcoals
from the Past: Cultural and Palaeoenvironmental Implica-
tions. Оксфорд, стр. 93–103.
Фанг, Дж., Се, З., 1994. Вырубка лесов в доиндустриальном Китае:
Район Лёссового плато в качестве примера. Chemosphere 29,
983–999.
Gammage, B., 2012. Самое большое поместье на Земле.Аллен и Анвин,
Сидней, Мельбурн, Окленд, Лондон.
Gerlach, R., Baumewerd-schmidt, H., Borg, K. Van Den, Eck-
Meier, E., Schmidt, MWI, 2006. Доисторические изменения
почвы в бассейне Нижнего Рейна, Северо-Западная Германия — ar-
хеологический, 14 C и геохимический 136, 38–50.
Герлах, Р., Фишер, П., Экмайер, Э., Хильгерс, А., 2012. Темная почва
горизонта и археологические особенности в неолитическом поселении —
регион Нижнего Рейна, Северо-Западная Германия: Формирование, геохимия и хроностратиграфия.Quat. Int. 1,
191–204.
Глейзер, Б., Бирк, Дж. Дж., 2012. Состояние научных знаний о
свойствах и генезисе антропогенных темных земель в
Центральной Амазонии (terra preta de Índio). Геохим. Cos-
мохим. Acta 82, 39–51.
Kluepfel, L., Keiluweit, M., Kleber, M., Sander, M., 2014. Redox
свойства черного углерода, полученного из биомассы растений (biochar).
Окружающая среда. Sci. Technol. 48 (10), стр. 5601-5611, DOI: 10.1021/
es500906d
Родионов А., Амелунг В., Пайнеманн Н., Хаумайер Л.,
Жанг Х., Клебер М., Глейзер Б., Урусевская И., Зеч ,
W., 2010. Черный углерод в экосистемах пастбищ мира
. Global Biogeochem. Cycles, volume 24, issue 3,
DOI: 10.1029 / 2009GB003669
Schmidt, H.P., 2012. 55 применений biochar. Итака Дж. 1, 286–289,
www.ithaka-journal.net.
Шмидт, М.В.И., Ноак, А.Г., 2000.Черный углерод в почвах и отложениях
: анализ, распределение, последствия и текущие проблемы
. Glob. Biofeochem.Cy. 777–793.
Шекли, С., 2014. Shiing chars? Согласование с изменением климата, борьба с выбросами автомобилей, сельское хозяйство, землепользование и безопасность пищевых продуктов и политика безопасности
. Carbon Manag. 5, 119–121.
Уиллкокс, Г.Х., 1974. История обезлесения, показанная с помощью анализа древесного угля
на четырех участках в Восточной Анатолии.Анатолий.
Шпилька. 24, 117.
Wilson, K: http://www.backyardbiochar.net/
Укажите как:
Укажите как: Schmidt HP, Taylor P (2014): Kon-Tiki
печи — ame пиролиз колпачка для демократизации производства биоугля
, Ithaka-Journal для материалов биоугля,
экосистем и сельского хозяйства, Арбаз, Швейцария, ISSN
1663-0521, стр. 349-355, www.ithaka-journal.net/86
Границы | Каталитический пиролиз пластиковых отходов: переход к биоперерабатывающим предприятиям на основе пиролиза
Введение
Производство и потребление пластиковых отходов растет тревожными темпами в связи с увеличением численности населения, быстрым экономическим ростом, постоянной урбанизацией и изменениями в образе жизни.Кроме того, короткий срок службы пластика ускоряет ежедневное производство пластиковых отходов. Мировое производство пластика оценивается примерно в 300 миллионов тонн в год и с каждым годом постоянно увеличивается (Miandad et al., 2016a; Ratnasari et al., 2017). Пластмассы состоят из нефтехимических углеводородов с добавками, такими как антипирены, стабилизаторы и окислители, которые затрудняют биоразложение (Ma et al., 2017). Переработка пластиковых отходов осуществляется по-разному, но в большинстве развивающихся стран открытая или свалка является обычной практикой управления пластиковыми отходами (Gandidi et al., 2018). Удаление пластиковых отходов на свалки является средой обитания для насекомых и грызунов, которые могут вызывать различные типы заболеваний (Alexandra, 2012). Кроме того, стоимость транспортировки, рабочей силы и технического обслуживания может увеличить стоимость проектов по переработке (Gandidi et al., 2018). Кроме того, из-за быстрой урбанизации сокращается количество земель, пригодных для свалки, особенно в городах. Пиролиз — это распространенный метод преобразования пластиковых отходов в энергию в виде твердого, жидкого и газообразного топлива.
Пиролиз — это термическое разложение пластиковых отходов при различных температурах (300–900 ° C) в отсутствие кислорода до полученной жидкой нефти (Rehan et al., 2017). Различные виды катализаторов используются для улучшения процесса пиролиза пластиковых отходов в целом и повышения эффективности процесса. Катализаторы играют очень важную роль в повышении эффективности процесса, нацеливании на конкретную реакцию и снижении температуры и времени процесса (Serrano et al., 2012; Ratnasari et al., 2017).В процессах пиролиза пластмасс использовался широкий спектр катализаторов, но наиболее широко применяемыми катализаторами являются ZSM-5, цеолит, Y-цеолит, FCC и MCM-41 (Ratnasari et al., 2017). Каталитическая реакция во время пиролиза пластиковых отходов на твердых кислотных катализаторах может включать реакции крекинга, олигомеризации, циклизации, ароматизации и изомеризации (Serrano et al., 2012).
В нескольких исследованиях сообщалось об использовании микропористых и мезопористых катализаторов для преобразования пластиковых отходов в жидкое масло и полукокс.Uemichi et al. (1998) провели каталитический пиролиз полиэтилена (ПЭ) с катализаторами HZSM-5. Использование ХЗСМ-5 увеличило добычу жидкой нефти с составом ароматических углеводородов и изоалкановых соединений. Gaca et al. (2008) провели пиролиз пластиковых отходов с модифицированными MCM-41 и HZSM-5 и сообщили, что использование HZSM-5 дает более легкие углеводороды (C 3 –C 4 ) с максимальным содержанием ароматических соединений. Lin et al. (2004) использовали различные типы катализаторов и сообщили, что даже смешивание HZSM-5 с мезопористым SiO 2 -Al 2 O 3 или MCM-41 привело к максимальной добыче жидкой нефти с минимальным выходом газа.Агуадо и др. (1997) сообщили о получении ароматических и алифатических соединений в результате каталитического пиролиза полиэтилена с HZSM-5, в то время как использование мезопористого MCM-41 снизило количество получаемых ароматических соединений из-за его низкой кислотной каталитической активности. Использование синтетических катализаторов улучшило общий процесс пиролиза и улучшило качество добываемой жидкой нефти. Однако использование синтетических катализаторов увеличивало стоимость процесса пиролиза.
Катализаторы NZ могут использоваться для решения экономических проблем каталитического пиролиза, который связан с использованием дорогих катализаторов.В последние годы Новая Зеландия привлекла к себе большое внимание своими потенциальными экологическими приложениями. Естественно, NZ встречается в Японии, США, Кубе, Индонезии, Венгрии, Италии и Королевстве Саудовская Аравия (KSA) (Sriningsih et al., 2014; Nizami et al., 2016). Месторождение Новой Зеландии в КСА в основном находится в Харрат Шама и Джаббал Шама и в основном содержит минералы морденита с высокой термической стабильностью, что делает его пригодным в качестве катализатора при пиролизе пластиковых отходов. Sriningsih et al. (2014) модифицировали NZ из Сукабуми, Индонезия, отложив переходные металлы, такие как Ni, Co и Mo, и провели пиролиз полиэтилена низкой плотности (LDPE).Gandidi et al. (2018) использовали NZ из Лампунга, Индонезия, для каталитического пиролиза твердых бытовых отходов.
Это первое исследование по изучению влияния модифицированного саудовского природного цеолита на качество продукта и выход при каталитическом пиролизе пластиковых отходов. Саудовский природный цеолитный катализатор был модифицирован с помощью новой термической активации (TA-NZ) при 550 ° C и кислотной активации (AA-NZ) с помощью HNO 3 для улучшения его каталитических свойств. Каталитический пиролиз различных типов пластиковых отходов (ПС, ПЭ, ПП и ПЭТ) в виде отдельных или смешанных в различных соотношениях в присутствии катализаторов на основе модифицированного природного цеолита (NZ) в небольшом экспериментальном реакторе пиролиза проводился для первый раз.Были изучены качество и выход таких продуктов пиролиза, как жидкая нефть, газ и полукокс. Химический состав жидкой нефти анализировали с помощью ГХ-МС. Кроме того, были обсуждены возможности и проблемы биоперерабатывающих заводов на основе пиролиза.
Материалы и методы
Подготовка сырья и запуск реактора
Пластиковые отходы, используемые в качестве сырья в процессе каталитического пиролиза, были собраны в Джидде и включали продуктовые пакеты, одноразовые чашки и тарелки для сока и бутылки для питьевой воды, которые состоят из полиэтилена (PE), полипропилена (PP), полистирола (PS), и полиэтилентерефталатные (ПЭТ) пластмассы соответственно.Выбор этих пластиковых материалов был сделан на основании того факта, что они являются основным источником пластиковых отходов, производимых в КСА. Для получения однородной смеси все образцы отходов измельчали на более мелкие кусочки размером около 2 см 2 . Каталитический пиролиз проводился с использованием отдельных или смеси этих пластиковых отходов в различных соотношениях (таблица 1). Использовали 1000 г сырья, по 100 г катализатора в каждом эксперименте. Саудовский природный цеолит (Новая Зеландия), собранный в Харрат-Шама, расположенном на северо-западе города Джидда, штат Южная Австралия (Nizami et al., 2016), был модифицирован термической и кислотной обработкой и использован в этих экспериментах по каталитическому пиролизу. NZ измельчали до порошка (<100 нм) в шаровой мельнице (Retsch MM 480) в течение 3 ч при частоте 20 Гц / с перед модификацией и использованием в пиролизе. Для термической активации (ТА) NZ нагревали в муфельной печи при 550 ° C в течение 5 часов, а для кислотной активации (AA) NZ вымачивали в 0,1 М растворе азотной кислоты (HNO 3 ) в течение 48 часов и непрерывно встряхивают с помощью цифрового шейкера IKA HS 501 со скоростью 50 об / мин.После этого образец промывали деионизированной водой до получения нормального pH.
Таблица 1 . Схема эксперимента.
Эксперименты проводились в небольшом пилотном реакторе пиролиза при 450 ° C, при скорости нагрева 10 ° C / мин и времени реакции 75 мин (рис. 1). Полученный выход каждого продукта пиролиза рассчитывали по массе после завершения каждого эксперимента. Характеристика добываемой жидкой нефти была проведена для исследования влияния состава сырья на качество жидкой нефти, полученной в присутствии модифицированного NZ.ТГА проводили на сырье для получения оптимальных условий процесса, таких как температура и время реакции (75 мин) в контролируемых условиях. В TGA брали 10 мкг каждого типа пластиковых отходов и нагревали со скоростью 10 ° C от 25 до 900 ° C в непрерывном потоке азота (50 мл / мин). Авторы этого исследования недавно опубликовали работу о влиянии состава сырья и природных и синтетических цеолитных катализаторов без модификации катализатора на различные типы пластиковых отходов (Miandad et al., 2017b; Rehan et al., 2017).
Экспериментальная установка
Небольшой пилотный реактор может использоваться как для термического, так и для каталитического пиролиза с использованием различного сырья, такого как пластмассы и биомасса (рис. 1). В этом исследовании модифицированные катализаторы NZ были добавлены в реактор с сырьем. Реактор пиролиза может вместить до 20 л сырья, а максимальная безопасная рабочая температура до 600 ° C может быть достигнута при желаемых скоростях нагрева.Подробные параметры реактора пиролиза были опубликованы ранее (Miandad et al., 2016b, 2017b). При повышении температуры выше определенных значений пластиковые отходы (органические полимеры) превращаются в мономеры, которые переносятся в конденсатор, где эти пары конденсируются в жидкое масло. Для обеспечения температуры конденсации ниже 10 ° C и максимальной конденсации пара в жидкое масло использовалась система непрерывной конденсации с использованием водяной бани и охлаждающей жидкости ACDelco Classic.Добываемая жидкая нефть была собрана из резервуара для сбора нефти, и была проведена дальнейшая характеристика, чтобы раскрыть ее химический состав и характеристики для других потенциальных применений.
Аналитические методы
Пиролизное масло охарактеризовано с использованием различных методов, таких как газовая хроматография в сочетании с масс-спектрофотометрией (ГХ-МС), инфракрасная спектроскопия с преобразованием Фурье (FT-IR),
Бомбовый калориметр и TGA (Mettler Toledo TGA / SDTA851) с применением стандартных методов ASTM.Функциональные группы в пиролизном масле анализировали с помощью прибора FT-IR, Perkin Elmer’s, UK. Анализ FT-IR проводился с использованием минимум 32 сканирований со средним значением 4 см -1 ИК-сигналов в диапазоне частот 500-4000 см -1 .
Химический состав нефти изучался с помощью ГХ-МС (Shimadzu QP-Plus 2010) с детектором FI. Использовали капиллярную колонку GC длиной 30 м и шириной 0,25 мм, покрытую пленкой 5% фенилметилполисилоксана (HP-5) толщиной 0,25 мкм.Духовку устанавливали на 50 ° C на 2 минуты, а затем повышали до 290 ° C, используя скорость нагрева 5 ° C / мин. Температура источника ионов и линии передачи поддерживалась на уровне 230 и 300 ° C, а инжекция без деления потока применялась при 290 ° C. Библиотеку масс-спектральных данных NIST08s использовали для идентификации хроматографических пиков, и процентные доли пиков оценивались по их общей площади пика ионной хроматограммы (TIC). Высокая теплотворная способность (HHV) добытой жидкой нефти, полученной из различных типов пластиковых отходов, была измерена в соответствии со стандартным методом ASTM D 240 с помощью прибора Bomb Calorimeter (Parr 6200 Calorimeter), в то время как производство газа оценивалось с использованием стандартной формулы баланса масс. , учитывая разницу в весе жидкого масла и полукокса.
Результаты и обсуждение
ТГА-анализ сырья
ТГА был проведен для каждого типа пластиковых отходов в индивидуальном порядке, чтобы определить оптимальную температуру для термического разложения. Все типы пластиковых отходов демонстрируют сходное поведение при разложении с быстрой потерей веса углеводородов в узком диапазоне температур (150–250 ° C) (рис. 2). Максимальная деградация для каждого типа пластиковых отходов была достигнута в пределах 420–490 ° C. ПС и ПП показали одностадийное разложение, в то время как ПЭ и ПЭТ показали двухступенчатое разложение в контролируемых условиях.Одностадийное разложение соответствует присутствию углерод-углеродной связи, которая способствует механизму случайного разрыва с повышением температуры (Kim et al., 2006). Разложение полипропилена начинается при очень низкой температуре (240 ° C) по сравнению с другим сырьем. Половина углерода, присутствующего в цепи полипропилена, состоит из третичного углерода, который способствует образованию карбокатиона в процессе его термического разложения (Jung et al., 2010). Вероятно, это причина достижения максимальной деградации полипропилена при более низкой температуре.Начальная деградация PS началась при 330 ° C, а максимальная деградация была достигнута при 470 ° C. PS имеет циклическую структуру, и его деградация в термических условиях включает как случайную цепь, так и разрыв концевой цепи, что усиливает процесс его деградации (Demirbas, 2004; Lee, 2012).
Рисунок 2 . Термогравиметрический анализ (ТГА) пластиковых отходов ПС, ПЭ, ПП и ПЭТ.
PE и PET показали двухэтапный процесс разложения; начальная деградация началась при более низких температурах, а затем другая стадия разложения при более высокой температуре.Первоначальная деградация ПЭ началась при 270 ° C и медленно, но постепенно распространялась, пока температура не достигла 385 ° C. После этой температуры наблюдалась резкая деградация, и была достигнута 95% -ная деградация с дальнейшим повышением примерно на 100 ° C. Аналогичная двухэтапная картина разрушения наблюдалась для пластика ПЭТФ, и первоначальное разложение начиналось при 400 ° C с резким снижением потери веса. Однако вторая деградация началась при несколько более высокой температуре (550 ° C). Первоначальное разложение ПЭ и ПЭТ может быть связано с присутствием некоторых летучих примесей, таких как добавочный наполнитель, используемый во время синтеза пластика (Димитров и др., 2013).
Различные исследователи сообщают, что деградация ПЭ и ПЭТ требует более высоких температур по сравнению с другими пластиками (Димитров и др., 2013; Риццарелли и др., 2016). Lee (2012) сообщил, что PE имеет длинноцепочечную разветвленную структуру и что его разложение происходит посредством разрыва случайной цепи, что требует более высокой температуры, в то время как разложение PET следует за случайным разрывом сложноэфирных звеньев, что приводит к образованию олигомеров (Dziecioł and Trzeszczynski, 2000). ; Lecomte and Liggat, 2006).Первоначальная деградация ПЭТ, возможно, была связана с присутствием некоторых летучих примесей, таких как диэтиленгликоль (Димитров и др., 2013). В литературе сообщается, что присутствие этих летучих примесей дополнительно способствует процессу разложения полимеров (McNeill and Bounekhel, 1991; Dziecioł and Trzeszczynski, 2000). Различие в кривых ТГА различных типов пластиков может быть связано с их мезопористой структурой (Chandrasekaran et al., 2015). Кроме того, Lopez et al. (2011) сообщили, что использование катализаторов снижает температуру процесса.Следовательно, 450 ° C можно было бы принять в качестве оптимальной температуры в присутствии активированного NZ для каталитического пиролиза вышеупомянутых пластиковых отходов.
Влияние сырья и катализаторов на выход продуктов пиролиза
Было исследовано влияние термической и кислотной активации NZ на выход продукта процесса пиролиза (рис. 3). Каталитический пиролиз индивидуального ПС-пластика с использованием катализаторов TA-NZ и AA-NZ показал самый высокий выход жидкого масла 70 и 60%, соответственно, по сравнению со всеми другими изученными типами индивидуальных и комбинированных пластиковых отходов.О высоком выходе жидкой нефти при каталитическом пиролизе ПС сообщалось и в нескольких других исследованиях (Siddiqui, Redhwi, 2009; Lee, 2012; Rehan et al., 2017). Сиддики и Редхви (2009) сообщили, что ПС имеет циклическую структуру, что приводит к высокому выходу жидкой нефти при каталитическом пиролизе. Ли (2012) сообщил, что деградация полистирола происходит за счет разрывов как случайных цепей, так и концевых цепей, что приводит к образованию стабильной структуры бензольного кольца, которая усиливает дальнейший крекинг и может увеличивать добычу жидкой нефти.Более того, в присутствии кислотных катализаторов разложение PS происходит по карбениевому механизму, который далее подвергается гидрированию (меж / внутримолекулярный перенос водорода) и β-расщеплению (Serrano et al., 2000). Кроме того, разложение PS происходило при более низкой температуре по сравнению с другими пластиками, такими как PE, из-за его циклической структуры (Wu et al., 2014). С другой стороны, каталитический пиролиз PS дает более высокое количество полукокса (24,6%) с катализатором AA-NZ, чем с катализатором TA-NZ (15,8%).Ma et al. (2017) также сообщили о высоком производстве полукокса при каталитическом пиролизе полистирола с кислотным цеолитным (Hβ) катализатором. Высокие показатели образования полукокса были обусловлены высокой кислотностью катализатора, которая способствует образованию полукокса за счет интенсивных вторичных реакций сшивания (Serrano et al., 2000).
Рисунок 3 . Влияние TA-NZ и AA-NZ на выход продуктов пиролиза.
Каталитический пиролиз ПП дает более высокое содержание жидкой нефти (54%) с катализатором AA-NZ, чем с катализатором TA-NZ (40%) (рис. 3).С другой стороны, катализатор TA-NZ дает большое количество газа (41,1%), что может быть связано с более низкой каталитической активностью катализатора TA-NZ. По данным Kim et al. (2002) катализатор с низкой кислотностью и участки поверхности по БЭТ с микропористой структурой способствуют начальному разложению полипропилена, что может привести к максимальному выделению газов. Обали и др. (2012) провели пиролиз полипропилена с катализатором, содержащим оксид алюминия, и сообщили о максимальной добыче газа. Более того, образование карбокатиона во время разложения полипропилена из-за присутствия третичного углерода в его углеродной цепи также может способствовать образованию газа (Jung et al., 2010). Syamsiro et al. (2014) также сообщили, что каталитический пиролиз PP и PS с активированным кислотой (HCL) природным цеолитным катализатором дает больше газов, чем процесс с термически активированным природным цеолитным катализатором, из-за его высокой кислотности и площади поверхности по БЭТ.
Каталитический пиролиз полиэтилена с катализаторами TA-NZ и AA-NZ дает аналогичные количества жидкого масла (40 и 42%). Однако наибольшее количество газов (50,8 и 47,0%) было произведено из полиэтилена при использовании AA-NZ и TA-NZ соответственно, по сравнению со всеми другими изученными типами пластмасс.Производство полукокса было самым низким в этом случае, 7,2 и 13,0% с AA-NZ и TA-NZ, соответственно. В различных исследованиях также сообщалось о более низком производстве полукокса при каталитическом пиролизе полиэтилена (Xue et al., 2017). Lopez et al. (2011) сообщили, что катализаторы с высокой кислотностью усиливают крекинг полимеров во время каталитического пиролиза. Увеличение крекинга в присутствии высококислотного катализатора способствует образованию газов (Miandad et al., 2016b, 2017a). Zeaiter (2014) провел каталитический пиролиз полиэтилена с цеолитом HBeta и сообщил о 95.7% выход газа из-за высокой кислотности катализатора. Batool et al. (2016) также сообщили о максимальном производстве газа при каталитическом пиролизе полиэтилена с высококислотным катализатором ZSM-5. Согласно Lee (2012) и Williams (2006), PE имеет длинноцепочечную углеродную структуру, и его разложение происходит случайным образом на более мелкие цепочечные молекулы за счет случайного разрыва цепи, что может способствовать образованию газа. Во время пиролиза полиэтилена, который удерживает только связи C-H и C-C, первоначально происходит разрыв основной цепи макромолекулы и образование стабильных свободных радикалов.Далее происходили стадии гидрирования, ведущие к синтезу вторичных свободных радикалов (новая стабильная связь C-H), что приводило к β-разрыву и образованию ненасыщенной группы (Rizzarelli et al., 2016).
Каталитический пиролиз ПП / ПЭ (соотношение 50/50%) не выявил какой-либо существенной разницы в общих выходах продукта при использовании как AA-NZ, так и TA-NZ. Жидкое масло, полученное в результате каталитического пиролиза PP / PE, составляло 44 и 40% от катализаторов TA-NZ и AA-NZ, соответственно. Небольшое снижение выхода жидкого масла из AA-NZ могло быть связано с его высокой кислотностью.Syamsiro et al. (2014) сообщили, что AA-NZ с HCl имеет более высокую кислотность по сравнению с TA-NZ, дает меньший выход жидкой нефти и имеет высокий выход газов. Общий каталитический пиролиз PP / PE дает максимальное количество газа с низким содержанием полукокса. Высокая добыча газа может быть связана с присутствием ПП. Разложение полипропилена усиливает процесс карбокатиона из-за присутствия третичного углерода в его углеродной цепи (Jung et al., 2010). Кроме того, разложение полиэтилена в присутствии катализатора также способствует получению газа с низким выходом жидкого масла.Однако, когда каталитический пиролиз ПП и ПЭ проводился отдельно с ПС, наблюдалась значительная разница в выходе продукта.
Наблюдалась значительная разница в выходе жидкого масла 54 и 34% для каталитического пиролиза PS / PP (соотношение 50/50%) с катализаторами TA-NZ и AA-NZ, соответственно. Аналогичным образом наблюдалась значительная разница в выходе полукокса 20,3 и 35,2%, тогда как высокий выход газов составлял 25,7 и 30,8% при использовании катализаторов TA-NZ и AA-NZ, соответственно.Lopez et al. (2011) и Seo et al. (2003) сообщили, что катализатор с высокой кислотностью способствует процессу крекинга и обеспечивает максимальное производство газа. Кроме того, присутствие ПП также увеличивает газообразование из-за процесса карбокатиона во время разложения (Jung et al., 2010). Kim et al. (2002) сообщили, что при разложении полипропилена выделяется максимум газа в присутствии кислотных катализаторов.
Каталитический пиролиз полистирола с полиэтиленом (соотношение 50/50%) в присутствии катализатора TA-NZ дает 44% жидкого масла, однако 52% жидкого масла было получено с использованием катализатора AA-NZ.Kiran et al. (2000) провели пиролиз PS с PE при различных соотношениях и сообщили, что увеличение концентрации PE снижает концентрацию жидкой нефти с увеличением количества газа. Присутствие ПС с ПЭ способствует процессу разложения из-за образования активного стабильного бензольного кольца из ПС (Miandad et al., 2016b). Wu et al. (2014) провели ТГА ПС с ПЭ и наблюдали два пика, первый для ПС при низкой температуре, а затем деградацию ПЭ при высокой температуре.Более того, деградация PE следует за цепным процессом свободных радикалов и процессом гидрирования, в то время как PS следует за процессом радикальной цепочки, включая различные стадии (Kiran et al., 2000). Таким образом, даже с учетом явления разложения, PS приводил к более высокой деградации по сравнению с PE и давал стабильные бензольные кольца (McNeill et al., 1990).
Каталитический пиролиз ПС / ПЭ / ПП (соотношение 50/25/25%) показал несколько более низкий выход жидкого масла по сравнению с каталитическим пиролизом всех отдельных типов пластмасс.Выход масла для обоих катализаторов, TA-NZ и AA-NZ, в этом случае одинаков, 44 и 40% соответственно. Производство полукокса было выше (29,7%) с катализатором AA-NZ, чем (19,0%) с катализатором TA-NZ, что может быть связано с реакциями полимеризации (Wu and Williams, 2010). Кроме того, добавление ПЭТ с ПС, ПЭ и ПП (соотношение 20/40/20/20%) снизило выход жидкого масла до 28 и 30% в целом при использовании катализаторов TA-NZ и AA-NZ, соответственно, с более высокой фракции полукокса и газа. Демирбас (2004) провел пиролиз ПС / ПЭ / ПП и сообщил аналогичные результаты для выхода продукта.Аднан и др. (2014) провели каталитический пиролиз ПС и ПЭТ с использованием катализатора Al-Al 2 O 3 с соотношением 80/20% и сообщили только о 37% жидкой нефти. Более того, Yoshioka et al. (2004) сообщили о максимальном производстве газа и полукокса при незначительном производстве жидкой нефти при каталитическом пиролизе ПЭТ. Кроме того, о максимальном образовании угля сообщалось также при проведении каталитического пиролиза ПЭТ с другими пластиками (Bhaskar et al., 2004). Более высокое производство полукокса при пиролизе ПЭТ было связано с реакциями карбонизации и конденсации во время его пиролиза при высокой температуре (Yoshioka et al., 2004). Кроме того, присутствие атома кислорода также способствует высокому образованию полукокса при каталитическом пиролизе ПЭТ (Xue et al., 2017). Thilakaratne et al. (2016) сообщили, что образование свободных радикалов от бензола с двумя активированными углями является предшественником каталитического кокса при разложении ПЭТ.
Влияние катализаторов на состав жидкой нефти
Химический состав жидкого масла, полученного каталитическим пиролизом различных пластиковых отходов с использованием катализаторов TA-NZ и AA-NZ, был охарактеризован методом ГХ-МС (Рисунки 4, 5).На состав добываемой жидкой нефти влияют различные типы сырья и катализаторов, используемых в процессе пиролиза (Miandad et al., 2016a, b, c). Жидкое масло, полученное из отдельных типов пластмасс, таких как ПС, ПП и ПЭ, содержало смесь ароматических, алифатических и других углеводородных соединений. Ароматические соединения, обнаруженные в масле из ПС и ПЭ, были выше, чем ПП при использовании катализатора TA-NZ. Количество ароматических соединений увеличилось в масле из ПС и ПП, но уменьшилось в ПЭ при использовании катализатора AA-NZ.Мезопористый и кислотный катализатор приводит к производству углеводородов с более короткой цепью из-за его высокой крекирующей способности (Lopez et al., 2011). Однако микропористые и менее кислые катализаторы способствуют образованию длинноцепочечных углеводородов, поскольку процесс крекинга происходит только на внешней поверхности катализаторов. В целом, в присутствии катализаторов PE и PP следуют механизму разрыва случайной цепи, в то время как PS следует механизму разрыва или разрыва концевой цепи (Cullis and Hirschler, 1981; Peterson et al., 2001). Разрыв концевой цепи приводит к образованию мономера, тогда как разрыв случайной цепи дает олигомеры и мономеры (Peterson et al., 2001).
Рис. 4. (A, B) ГХ-МС жидкого масла, полученного из различных типов пластиковых отходов с TA-NZ.
Рис. 5. (A, B) ГХ-МС жидкого масла, полученного из различных типов пластиковых отходов с AA-NZ.
Жидкое масло, полученное в результате каталитического пиролиза полиэтилена, при использовании обоих катализаторов, давало в основном нафталин, фенантрен, нафталин, 2-этенил-, 1-пентадецен, антрацен, 2-метил-, гексадекан и так далее (рисунки 4A, 5A. ).Эти результаты согласуются с несколькими другими исследованиями (Lee, 2012; Xue et al., 2017). Получение производного бензола показывает, что TA-NZ усиливает процесс ароматизации по сравнению с AA-NZ. Xue et al. (2017) сообщили, что промежуточные олефины, полученные в результате каталитического пиролиза ПЭ, далее ароматизируются внутри пор катализаторов. Тем не менее, реакция ароматизации далее приводит к образованию атомов водорода, которые могут усилить процесс ароматизации. Ли (2012) сообщил, что ZSM-5 производит больше ароматических соединений по сравнению с морденитным катализатором из-за его кристаллической структуры.
Существует два возможных механизма, которые могут включать разложение полиэтилена в присутствии катализатора; отрыв гибридных ионов из-за присутствия сайтов Льюиса или из-за механизма иона карбения через добавление протона (Rizzarelli et al., 2016). Первоначально деградация начинается на внешней поверхности катализаторов, а затем продолжается с дальнейшей деградацией во внутренних порах катализаторов (Lee, 2012). Однако микропористые катализаторы препятствуют проникновению более крупных молекул, и, таким образом, соединения с более высокой углеродной цепью образуются в результате каталитического пиролиза полиэтилена с микропористыми катализаторами.Кроме того, в присутствии кислотных катализаторов из-за карбениевого механизма может увеличиваться образование ароматических и олефиновых соединений (Lee, 2012). Lin et al. (2004) сообщили о получении высокореакционных олефинов в качестве промежуточных продуктов во время каталитического пиролиза полиэтилена, которые могут способствовать образованию парафинов и ароматических соединений в добываемой жидкой нефти. Более того, присутствие кислотного катализатора и свободного атома водорода может привести к алкилированию толуола и бензола, превращая промежуточный алкилированный бензол в нафталин за счет ароматизации (Xue et al., 2017).
Жидкое масло, полученное каталитическим пиролизом ПС с ТА-НЗ и АА-НЗ, содержит различные виды соединений. Основными обнаруженными соединениями были альфа-метилстирол, бензол, 1,1 ‘- (2-бутен-1,4-диил) бис-, бибензил, бензол, (1,3-пропандиил), фенантрен, 2-фенилнафталин и т. Д. в добываемой жидкой нефти (Рисунки 4A, 5A). Жидкая нефть, полученная каталитическим пиролизом ПС с обоими активированными катализаторами, в основном содержит ароматические углеводороды с некоторыми парафинами, нафталином и олефиновыми соединениями (Rehan et al., 2017). Однако в присутствии катализатора достигается максимальное производство ароматических соединений (Xue et al., 2017). Рамли и др. (2011) также сообщили о производстве олефинов, нафталина с ароматическими соединениями в результате каталитического пиролиза полистирола с Al 2 O 3 , нанесенных на катализаторы Cd и Sn. Деградация ПС начинается с растрескивания на внешней поверхности катализатора, а затем следует риформинг внутри пор катализатора (Uemichi et al., 1999). Первоначально крекинг полимера осуществляется кислотным центром Льюиса на поверхности катализатора с образованием карбокатионных промежуточных соединений, которые в дальнейшем испаряются или подвергаются риформингу внутри пор катализатора (Xue et al., 2017).
Каталитический пиролиз полистирола в основном производит стирол и его производные, которые являются основными соединениями в добываемой жидкой нефти (Siddiqui and Redhwi, 2009; Rehan et al., 2017). Превращение стирола в его производное увеличивалось в присутствии протонированных катализаторов за счет гидрирования (Kim et al., 2002). Шах и Ян (2015) и Укей и др. (2000) сообщили, что гидрирование стирола усиливается с увеличением температуры реакции. Огава и др. (1982) провели пиролиз ПС с алюмосиликатным катализатором при 300 ° C и обнаружили гидрирование стирола до его производного.Рамли и др. (2011) сообщили о возможном механизме разложения PS на кислотных катализаторах, который может происходить из-за атаки протона, связанного с кислотными центрами Бренстеда, что приводит к механизму карбениевого иона, который далее подвергается β-расщеплению и позже сопровождается переносом водорода. Более того, реакции поперечного сшивания благоприятствовали сильные кислотные центры Бренстеда, и когда эта реакция происходит, завершение крекинга может в некоторой степени уменьшаться и увеличивать образование полукокса (Serrano et al., 2000). Кроме того, катализаторы оксид кремния-оксид алюминия не имеют сильных кислотных центров Бренстеда, хотя они могут не улучшать реакцию сшивки, но благоприятствуют процессу гидрирования. Таким образом, это может быть причиной того, что стирол не был обнаружен в жидком масле, однако его производное было обнаружено в больших количествах (Lee et al., 2001). Xue et al. (2017) также сообщили о деалкилировании стирола из-за задержки испарения внутри реактора, что может привести к усилению процесса риформинга и образованию производного стирола.TA-NZ и AA-NZ содержат большое количество оксида алюминия и диоксида кремния, что приводит к гидрированию стирола до его производного, что приводит к получению мономеров стирола вместо стирола.
Каталитический пиролиз полипропилена дает сложную смесь жидкого масла, содержащего ароматические углеводороды, олефины и соединения нафталина. Бензол, 1,1 ‘- (2-бутен-1,4-диил) бис-, бензол, 1,1’ — (1,3-пропандиил) бис-, антрацен, 9-метил-, нафталин, 2-фенил -, 1,2,3,4-тетрагидро-1-фенил-, нафталин, фенантрен и др.были основными соединениями, обнаруженными в жидкой нефти (Рисунки 4A, 5A). Эти результаты согласуются с другими исследованиями, в которых проводился каталитический пиролиз полипропилена с различными катализаторами (Marcilla et al., 2004). Кроме того, разложение ПП с помощью AA-NZ привело к максимальному образованию фенольных соединений. Более высокая продукция, возможно, была связана с наличием сильных кислотных центров, так как это способствует образованию фенольных соединений. Кроме того, присутствие высококислотного центра на катализаторах усиливает механизм олигомеризации, ароматизации и деоксигенации, что приводит к получению полиароматических и нафталиновых соединений.Dawood и Miura (2002) также сообщили о высоком уровне образования этих соединений в результате каталитического пиролиза полипропилена с высококислотным модифицированным HY-цеолитом.
Состав масла, полученного в результате каталитического пиролиза полипропилена с полиэтиленом, содержит соединения, обнаруженные в масле из обоих видов сырья пластикового типа. Miandad et al. (2016b) сообщили, что состав сырья также влияет на качество и химический состав нефти. Жидкое масло, полученное каталитическим пиролизом ПЭ / ПП, содержит ароматические, олефиновые и нафталиновые соединения.Основными обнаруженными соединениями были: бензол, 1,1 ‘- (1,3-пропандиил) бис-, моно (2-этилгексил) сложный эфир, 1,2-бензолдикарбоновая кислота, антрацен, пентадекан, фенантрен, 2-фенилнафталин и т. д. (Рисунки 4B, 5B) . Юнг и др. (2010) сообщили, что образование ароматических соединений при каталитическом пиролизе PP / PE может происходить по механизму реакции Дильса-Альдера с последующим дегидрированием. Кроме того, каталитический пиролиз ПП и ПЭ, проводимый отдельно с ПС, в основном дает ароматические соединения из-за присутствия ПС.Полученная жидкая нефть из ПС / ПП содержит бензол, 1,1 ‘- (1,3-пропандиил) бис, 1,2-бензолдикарбоновую кислоту, дисооктиловый эфир, бибензил, фенантрен, 2-фенилнафталин, бензол, (4-метил- 1-деценил) — и так далее (Фигуры 4А, 5А). Каталитический пиролиз ПС с ПЭ в основном дает жидкую нефть с основными соединениями азулена, нафталина, 1-метил-, нафталина, 2-этенила, бензола, 1,1 ‘- (1,3-пропандиил) бис-, фенантрена, 2-фенилнафталина. , бензол, 1,1 ‘- (1-метил-1,2-этандиил) бис- и некоторые другие соединения (Рисунки 4B, 5B).Miskolczi et al. (2006) провели пиролиз ПС с ПЭ с соотношением 10 и 90%, соответственно, и сообщили о максимальном производстве ароматических углеводородов даже при очень низком соотношении ПС. Miandad et al. (2016b) сообщили, что термический пиролиз ПЭ с ПС без катализатора приводит к превращению ПЭ в жидкое масло с высоким содержанием ароматических углеводородов. Однако термический пиролиз единственного полиэтилена без катализатора превратил его в воск вместо жидкого масла из-за его сильной разветвленной длинноцепочечной структуры (Lee, 2012; Miandad et al., 2016б). Wu et al. (2014) провели ТГА ПС с ПЭ и сообщили, что присутствие ПС способствует разложению ПЭ из-за образования стабильных бензольных колец.
Химический состав пиролизного масла по различным функциональным группам был изучен методом FT-IR. Полученные данные выявили присутствие в масле ароматических и алифатических функциональных групп (рисунки 6, 7). Очень сильный пик при 696 см -1 наблюдался в большинстве жидких масел, полученных с использованием обоих катализаторов, что соответствует высокой концентрации ароматических соединений.Еще два очевидных пика были видны при 1456 и 1495 см -1 для C-C с одинарными и двойными связями, соответствующих ароматическим соединениям. Кроме того, в конце спектра сильные пики при 2,850, 2,923 и 2,958 см -1 наблюдались во всех типах жидких масел, кроме PS, что соответствует отрезку C-H соединений алканов. В целом жидкое масло, полученное в результате каталитического пиролиза различных пластиковых отходов с использованием катализатора AA-NZ, показало больше пиков, чем образцы катализаторов TA-NZ.Эти дополнительные пики соответствуют ароматическим соединениям, алканам и алкеновым соединениям. Это указывает на то, что, как и ожидалось, AA-NZ имел лучшие каталитические свойства, чем TA-NZ. Различные исследователи сообщили о схожих результатах, что в жидкой нефти, полученной из PS, преобладали ароматические углеводороды. Tekin et al. (2012) и Panda and Singh (2013) также сообщили о присутствии ароматических соединений с некоторыми алканами и алкенами в результате каталитического пиролиза полипропилена. Kunwar et al. (2016) провели термический и каталитический пиролиз полиэтилена и сообщили, что полученная жидкая нефть содержит алканы и алкены в качестве основной функциональной группы.В целом, анализ FT-IR позволил лучше понять химический состав жидкого масла, полученного в результате каталитического пиролиза различных пластиковых отходов с использованием модифицированных NZ-катализаторов, и дополнительно подтвердил наши результаты GC-MS.
Рисунок 6 . FT-IR анализ жидкой нефти, полученной каталитическим пиролизом с TA-NZ.
Рисунок 7 . FT-IR анализ жидкой нефти, полученной в результате каталитического пиролиза с AA-NZ.
Возможное применение продуктов пиролиза
Жидкое масло, полученное в результате каталитического пиролиза различных типов пластмассового сырья, содержит большое количество ароматических, олефиновых и нафталиновых соединений, которые содержатся в нефтепродуктах.Более того, высокая теплотворная способность добываемой жидкой нефти находится в диапазоне 41,7–44,2 МДж / кг (Таблица 2), что очень близко к энергетической ценности обычного дизельного топлива. Самая низкая HHV 41,7 МДж / кг была обнаружена в жидкой нефти, полученной из PS с использованием катализатора TA-NZ, тогда как самая высокая HHV в 44,2 МДж / кг была у PS / PE / PP с использованием катализатора AA-NZ. Таким образом, жидкое пиролизное масло, получаемое из различных пластиковых отходов, потенциально может быть использовано в качестве альтернативного источника энергии. По данным Lee et al.(2015) и Rehan et al. (2016), производство электроэнергии возможно с использованием жидкого пиролизного масла в дизельном двигателе. Саптоади и Пратама (2015) успешно использовали жидкое пиролитическое масло в качестве альтернативы керосиновой печи. Кроме того, полученные ароматические соединения могут быть использованы в качестве сырья для полимеризации в различных отраслях химической промышленности (Sarker, Rashid, 2013; Shah, Jan, 2015). Кроме того, различные исследователи использовали добытую жидкую нефть в качестве транспортного топлива после смешивания с обычным дизельным топливом в различных соотношениях.Исследования проводились для изучения потенциала добываемой жидкой нефти в контексте характеристик двигателя и выбросов выхлопных газов транспортных средств. Nileshkumar et al. (2015) и Ли и др. (2015) сообщили, что соотношение смеси пиролитического жидкого масла и обычного дизельного топлива, равное 20: 80%, соответственно, дает аналогичные результаты по производительности двигателя, чем у обычного дизельного топлива. Более того, при том же смешанном соотношении выбросы выхлопных газов также были аналогичными, однако выбросы выхлопных газов увеличивались с увеличением количества смешанного пиролизного масла (Frigo et al., 2014; Мукерджи и Тамотаран, 2014).
Таблица 2 . Высокие значения нагрева (HHV) пиролизного масла из различного сырья с использованием катализаторов TA-NZ и AA-NZ.
Остаток (полукокс), оставшийся после процесса пиролиза, можно использовать в нескольких экологических целях. Несколько исследователей активировали полукокс с помощью пара и термической активации (Lopez et al., 2009; Heras et al., 2014). Процесс активации увеличил площадь поверхности по БЭТ и уменьшил размер пор полукокса (Lopez et al., 2009). Кроме того, Бернандо (2011) модернизировал пластиковый уголь биоматериалом и провел адсорбцию (3,6–22,2 мг / г) красителя метиленового синего из сточных вод. Miandad et al. (2018) использовали полукокс, полученный при пиролизе пластиковых отходов ПС, для синтеза нового наноадсорбента двухслойных оксидов углерода-металла (C / MnCuAl-LDOs) для адсорбции конго красного (CR) в сточных водах. Кроме того, полукокс также может использоваться в качестве сырья для производства активированного угля.
Ограничения ГХ-МС анализа пиролизного масла
Есть некоторые ограничения при проведении точного количественного анализа химических компонентов в пиролизном масле с помощью ГХ-МС.В этом исследовании мы использовали массовый процент различных химикатов, обнаруженных в образцах нефти, рассчитанный на основе площадей пиков, определенных с помощью колонки DP5-MS с нормальной фазой и FID. Идентифицированные пики были сопоставлены с NIST и библиотекой спектров банка масс. Соединения были выбраны на основе индекса сходства (SI> 90%). Дальнейшее сравнение с известными стандартами (CRM) позволило подтвердить идентифицированные соединения. Использованная колонка и детекторы ограничивались только углеводородами. Однако в действительности масло из большинства пластиковых отходов имеет сложную химическую структуру и может содержать другие группы неустановленных химических веществ, таких как сера, азот и кислородсодержащие углеводороды.Вот почему необходим более глубокий и точный качественный химический анализ, чтобы полностью понять химию пиролизного масла, с использованием расширенной калибровки и стандартизации и использования различных детекторов МС, таких как SCD и NCD, а также различных колонок для ГХ.
Возможности и проблемы биоперерабатывающих заводов на основе пиролиза
Заводы по переработке отходов привлекают огромное внимание как решение для преобразования ТБО и других отходов биомассы в ряд продуктов, таких как топливо, энергия, тепло и другие ценные химические вещества и материалы.Различные типы биоперерабатывающих заводов, такие как биоперерабатывающий завод на базе сельского хозяйства, завод биопереработки животных отходов, завод по биопереработке сточных вод, завод по биопереработке на основе водорослей, завод по переработке пластиковых отходов, биоперерабатывающий завод на базе лесного хозяйства, биопереработка промышленных отходов, биопереработка пищевых отходов и т. Д., Могут быть разработаны в зависимости от тип и источник отходов (Gebreslassie et al., 2013; De Wild et al., 2014; Nizami et al., 2017a, b; Waqas et al., 2018). Эти биоперерабатывающие заводы могут сыграть важную роль в сокращении загрязнения окружающей среды отходами и выбросов парниковых газов.Кроме того, они приносят существенные экономические выгоды и могут помочь в достижении циркулярной экономики в любой стране.
Биоперерабатывающий завод на основе пиролиза может быть разработан для обработки ряда отходов биомассы и пластиковых отходов с целью производства жидкого и газового топлива, энергии, биоугля и других более ценных химикатов с использованием комплексного подхода. Комплексный подход помогает достичь максимальных экономических и экологических выгод при минимальном образовании отходов. В биоперерабатывающих заводах на основе пиролиза существует множество проблем и возможностей для улучшения, которые необходимо решать и оптимизировать, чтобы обеспечить максимальную выгоду.Хотя пиролизное масло содержит больше энергии, чем уголь и некоторые другие виды топлива, сам пиролиз является энергоемким процессом, а нефтепродукт требует больше энергии для очистки (Inman, 2012). Это означает, что пиролизное масло может быть не намного лучше обычного дизельного топлива или другого ископаемого топлива с точки зрения выбросов парниковых газов, хотя для подтверждения этого необходимы более подробные исследования баланса массы и энергии в рамках всего процесса. Чтобы преодолеть эти технологические потребности в энергии, могут быть разработаны более передовые технологии с использованием интеграции возобновляемых источников энергии, таких как солнечная или гидроэнергетика, с пиролизными биоперерабатывающими заводами для достижения максимальных экономических и экологических выгод.
Доступность потоков отходов пластика и биомассы в качестве сырья для пиролизных биоперерабатывающих заводов — еще одна серьезная проблема, поскольку переработка в настоящее время не очень эффективна, особенно в развивающихся странах. Газы, образующиеся при пиролизе некоторых пластиковых отходов, таких как ПВХ, токсичны, и поэтому технология очистки выбросов пиролиза требует дальнейшего совершенствования для достижения максимальных экологических преимуществ. Пиролизное масло, полученное из различных типов пластика, необходимо значительно очистить перед использованием в любом применении, чтобы обеспечить минимальное воздействие на окружающую среду.Высокое содержание ароматических веществ в пиролизном масле является хорошим, и некоторые ароматические соединения, такие как бензол, толуол и стирол, можно очищать и продавать на уже сложившемся рынке. Однако некоторые ароматические углеводороды являются известными канцерогенами и могут нанести серьезный вред здоровью человека и окружающей среде. Поэтому в этом отношении необходимо серьезное рассмотрение.
Другие аспекты оптимизации биоперерабатывающих заводов на основе пиролиза, такие как новые появляющиеся передовые катализаторы, включая нанокатализаторы, должны быть разработаны и применены в процессах пиролиза для повышения качества и выхода продуктов, а также для оптимизации всего процесса.Рынок продуктов биопереработки на основе пиролиза должен быть создан / расширен, чтобы привлечь дополнительный интерес и финансирование, чтобы сделать эту концепцию более практичной и успешной. Точно так же необходимо больше внимания уделять проведению дальнейших исследований и разработок по обогащению концепции биопереработки и раскрытию ее истинного потенциала. Кроме того, очень важно провести подробную оценку экономического и экологического воздействия биоперерабатывающих заводов на стадии проектирования с использованием специализированных инструментов, таких как оценка жизненного цикла (ОЖЦ).LCA может анализировать воздействие биоперерабатывающего завода и всех продуктов на окружающую среду путем проведения подробных энергетических и материальных балансов на всех этапах жизненного цикла, включая добычу и переработку сырья, производство, распределение продуктов, использование, обслуживание и утилизацию / переработку. Результаты LCA помогут определить устойчивость биоперерабатывающих заводов, что имеет решающее значение для принятия правильного решения.
Выводы
Каталитический пиролиз — перспективный метод преобразования пластиковых отходов в жидкое масло и другие продукты с добавленной стоимостью с использованием модифицированного природного цеолита (NZ) катализатора.Модификация катализаторов NZ была проведена с помощью новой термической (TA) и кислотной (AA) активации, которая улучшила их каталитические свойства. Каталитический пиролиз PS дал наибольшее количество жидкой нефти (70 и 60%) по сравнению с PP (40 и 54%) и PE (40 и 42%) с использованием катализаторов TA-NZ и AA-NZ соответственно. Химический состав пиролизного масла был проанализирован с помощью ГХ-МС, и было обнаружено, что большая часть жидкого масла дает высокое содержание ароматических веществ с некоторыми алифатическими и другими углеводородными соединениями.Эти результаты были дополнительно подтверждены анализом FT-IR, показывающим четкие пики, соответствующие ароматическим и другим углеводородным функциональным группам. Кроме того, жидкое масло, полученное из различных типов пластиковых отходов, имело более высокую теплотворную способность (HHV) в диапазоне 41,7–44,2 МДж / кг, как и у обычного дизельного топлива. Следовательно, он может быть использован в различных энергетических и транспортных приложениях после дальнейшей обработки и очистки. Данное исследование является шагом к развитию биоперерабатывающих заводов на основе пиролиза.Биоперерабатывающие заводы обладают огромным потенциалом для преобразования отходов в энергию и другие ценные продукты и могут помочь в достижении экономики замкнутого цикла. Однако, как обсуждалось выше, существует множество технических, эксплуатационных и социально-экономических проблем, которые необходимо преодолеть для достижения максимальных экономических и экологических выгод от биоперерабатывающих заводов.
Доступность данных
Все наборы данных, созданные для этого исследования, включены в рукопись и / или дополнительные файлы.
Авторские взносы
RM провел эксперименты по пиролизу и помог в написании рукописи.HK, JD, JG и AH провели подробную характеристику продуктов процесса. MR и ASA проанализировали данные и письменные части рукописи. MAB, MR и A-SN исправили и отредактировали рукопись. ASA и IMII поддержали проект финансово и технически.
Заявление о конфликте интересов
Авторы заявляют, что исследование проводилось при отсутствии каких-либо коммерческих или финансовых отношений, которые могут быть истолкованы как потенциальный конфликт интересов.
Благодарности
MR и A-SN выражают признательность Центру передового опыта в области экологических исследований (CEES), Университету короля Абдель Азиза (KAU), Джидда, штат Калифорния, и Министерству образования штата Калифорния за финансовую поддержку в рамках гранта № 2 / S / 1438. Авторы также благодарны деканату научных исследований (DSR) КАУ за финансовую и техническую поддержку ОЕЭП.
Ссылки
Аднан А., Шах Дж. И Ян М. Р. (2014). Исследования разложения полистирола с использованием катализаторов на медной основе. J. Anal. Прил. Пирол . 109, 196–204. DOI: 10.1016 / j.jaap.2014.06.013
CrossRef Полный текст | Google Scholar
Агуадо, Дж., Сотело, Дж. Л., Серрано, Д. П., Каллес, Дж. А. и Эскола, Дж. М. (1997). Каталитическая конверсия полиолефинов в жидкое топливо на MCM-41: сравнение с ZSM-5 и аморфным SiO2 – Al 2 O 3 . Ener топливо 11, 1225–1231. DOI: 10.1021 / ef970055v
CrossRef Полный текст | Google Scholar
Александра, Л.С. (2012). Твердые бытовые отходы: превращение проблемы в ресурсные отходы: проблемы, с которыми сталкиваются развивающиеся страны, специалист по городскому хозяйству . Всемирный банк. 2–4 стр.
Батул, М., Шах, А. Т., Имран Дин, М., и Ли, Б. (2016). Каталитический пиролиз полиэтилена низкой плотности с использованием инкапсулированных цетилтриметиламмонийных моновакантных блоков кеггина и ZSM-5. J. Chem. 2016: 2857162. DOI: 10.1155 / 2016/2857162
CrossRef Полный текст | Google Scholar
Бернандо, М.(2011). «Физико-химические характеристики углей, образующихся при совместном пиролизе отходов, и возможные пути повышения ценности», в Chemical Engineering (Лиссабон: Universidade Nova de Lisboa), 27–36.
Бхаскар, Т., Канеко, Дж., Муто, А., Саката, Ю., Якаб, Э., Мацуи, Т. и др. (2004). Исследования пиролиза пластмасс PP / PE / PS / PVC / HIPS-Br, смешанных с ПЭТ, и дегалогенирование (Br, Cl) жидких продуктов. J. Anal. Прил. Пиролиз 72, 27–33. DOI: 10.1016 / j.jaap.2004.01.005
CrossRef Полный текст | Google Scholar
Чандрасекаран С. Р., Кунвар Б., Мозер Б. Р., Раджагопалан Н. и Шарма Б. К. (2015). Каталитический термический крекинг пластмассовых отходов постпотребительского производства с получением топлива. 1. Кинетика и оптимизация. Energy Fuels 29, 6068–6077. DOI: 10.1021 / acs.energyfuels.5b01083
CrossRef Полный текст | Google Scholar
Каллис, К. Ф., и Хиршлер, М. М. (1981). Горение органических полимеров. Т.5. Лондон: Издательство Оксфордского университета.
Давуд А. и Миура К. (2002). Каталитический пиролиз c-облученного полипропилена (PP) над HY-цеолитом для повышения реакционной способности и селективности продукта. Polym. Деграда. Укол . 76, 45–52. DOI: 10.1016 / S0141-3910 (01) 00264-6
CrossRef Полный текст | Google Scholar
Де Вильд, П. Дж., Хьюджген, В. Дж., И Госселинк, Р. Дж. (2014). Пиролиз лигнина для рентабельных лигноцеллюлозных биоперерабатывающих заводов. Биотопливо Биопрод.Биорефайнинг 8, 645–657. DOI: 10.1002 / bbb.1474
CrossRef Полный текст | Google Scholar
Демирбас А. (2004). Пиролиз муниципальных пластиковых отходов для утилизации углеводородов бензиновой марки. J. Anal. Прил. Пиролиз 72, 97–102. DOI: 10.1016 / j.jaap.2004.03.001
CrossRef Полный текст | Google Scholar
Димитров, Н., Крехула, Л. К., Сирочич, А. П., и Хрняк-Мургич, З. (2013). Анализ переработанных бутылок из ПЭТ методом пиролизно-газовой хроматографии. Polym. Деграда. Stab. 98, 972–979. DOI: 10.1016 / j.polymdegradstab.2013.02.013
CrossRef Полный текст | Google Scholar
Dziecioł, M., and Trzeszczynski, J. (2000). Летучие продукты термической деструкции полиэтилентерефталата в атмосфере азота. J. Appl. Polym. Sci. 77, 1894–1901. DOI: 10.1002 / 1097-4628 (20000829) 77: 9 <1894 :: AID-APP5> 3.0.CO; 2-Y
CrossRef Полный текст | Google Scholar
Фриго, С., Сеггиани, М., Пуччини, М., и Витоло, С. (2014). Производство жидкого топлива путем пиролиза отработанных шин и его использование в дизельном двигателе. Топливо 116, 399–408. DOI: 10.1016 / j.fuel.2013.08.044
CrossRef Полный текст | Google Scholar
Гака, П., Джевецка, М., Калета, В., Козубек, Х., Новинска, К. (2008). Каталитическая деструкция полиэтилена на мезопористом молекулярном сите МСМ-41, модифицированном гетерополисоединениями. Польский J. Environ. Stud. 17, 25–35.
Google Scholar
Гандиди, И.М., Сусила, М., Д. Мустофа, А., Памбуди, Н. А. (2018). Термико-каталитический крекинг реальных ТБО в био-нефть. J. Energy Inst. 91, 304–310. DOI: 10.1016 / j.joei.2016.11.005
CrossRef Полный текст | Google Scholar
Gebreslassie, Б. Х., Сливинский, М., Ван, Б., и Ю, Ф. (2013). Оптимизация жизненного цикла для устойчивого проектирования и эксплуатации заводов по биологической переработке углеводородов с помощью быстрого пиролиза, гидроочистки и гидрокрекинга. Comput. Chem. Англ. 50, 71–91.DOI: 10.1016 / j.compchemeng.2012.10.013
CrossRef Полный текст | Google Scholar
Херас, Ф., Хименес-Кордеро, Д., Гиларранц, М.А., Алонсо-Моралес, Н., и Родригес, Дж. Дж. (2014). Активация полукокса изношенных шин путем циклического жидкофазного окисления. Топливный процесс. Технол . 127, 157–162. DOI: 10.1016 / j.fuproc.2014.06.018
CrossRef Полный текст | Google Scholar
Юнг, С. Х., Чо, М. Х., Кан, Б. С., Ким, Дж. С. (2010). Пиролиз фракции отработанного полипропилена и полиэтилена для извлечения ароматических углеводородов БТК с использованием реактора с псевдоожиженным слоем. Топливный процесс. Technol. 91, 277–284. DOI: 10.1016 / j.fuproc.2009.10.009
CrossRef Полный текст | Google Scholar
Ким, Х. С., Ким, С., Ким, Х. Дж. И Янг, Х. С. (2006). Тепловые свойства полиолефиновых композитов с наполнителем из биомки с различным типом и содержанием компатибилизатора. Термохим. Acta 451, 181–188. DOI: 10.1016 / j.tca.2006.09.013
CrossRef Полный текст | Google Scholar
Ким, Дж. Р., Юн, Дж. Х. и Пак, Д.W. (2002). Каталитическая переработка смеси полипропилена и полистирола. Polym. Деграда. Stab. 76, 61–67. DOI: 10.1016 / S0141-3910 (01) 00266-X
CrossRef Полный текст | Google Scholar
Киран, Н., Экинчи, Э. и Снейп, К. Э. (2000). Переработка пластиковых отходов пиролизом. Ресурс. Консерв. Recycl. 29, 273–283. DOI: 10.1016 / S0921-3449 (00) 00052-5
CrossRef Полный текст | Google Scholar
Кунвар, Б., Мозер, Б. Р., Чандрасекаран, С.Р., Раджагопалан, Н., Шарма, Б. К. (2016). Каталитическая и термическая деполимеризация малоценного бытового полиэтилена высокой плотности. Energy 111, 884–892. DOI: 10.1016 / j.energy.2016.06.024
CrossRef Полный текст | Google Scholar
Леконт, Х.А., и Лиггат, Дж. Дж. (2006). Механизм разложения звеньев диэтиленгликоля в терефталатном полимере. Polym. Деграда. Stab. 91, 681–689. DOI: 10.1016 / j.polymdegradstab.2005.05.028
CrossRef Полный текст | Google Scholar
Ли, К.Х. (2012). Влияние типов цеолитов на каталитическую очистку воскового масла пиролиза. J. Anal. Прил. Пирол . 94, 209–214. DOI: 10.1016 / j.jaap.2011.12.015
CrossRef Полный текст | Google Scholar
Ли С., Йошида К. и Йошикава К. (2015). Применение отработанного пластикового пиролизного масла в дизельном двигателе с прямым впрыском: Для небольшой несетевой электрификации. Energy Environ. Рез . 5:18. DOI: 10.5539 / eer.v5n1p18
CrossRef Полный текст
Ли, С.Ю., Юн, Дж. Х., Ким, Дж. Р. и Пак, Д. У. (2001). Каталитическая деструкция полистирола над природным клиноптилолитовым цеолитом. Polym. Деграда. Stab. 74, 297–305. DOI: 10.1016 / S0141-3910 (01) 00162-8
CrossRef Полный текст | Google Scholar
Лин, Ю. Х., Янг, М. Х., Йе, Т. Ф. и Гер, М. Д. (2004). Каталитическое разложение полиэтилена высокой плотности на мезопористых и микропористых катализаторах в реакторе с псевдоожиженным слоем. Polym. Деграда. Stab. 86, 121–128.DOI: 10.1016 / j.polymdegradstab.2004.02.015
CrossRef Полный текст | Google Scholar
Лопес А., Марко Д. И., Кабальеро Б. М., Ларесгоити М. Ф., Адрадос А. и Торрес А. (2011). Пиролиз муниципальных пластиковых отходов II: влияние состава сырья в каталитических условиях. Управление отходами . 31, 1973–1983. DOI: 10.1016 / j.wasman.2011.05.021
CrossRef Полный текст | Google Scholar
Лопес, Г., Олазар, М., Артеткс, М., Амутио, М., Элорди, Дж., И Бильбао, Дж. (2009). Активация паром пиролитического полукокса шин при различных температурах. J. Anal. Прил. Пирол . 85, 539–543. DOI: 10.1016 / j.jaap.2008.11.002
CrossRef Полный текст | Google Scholar
Ma, C., Yu, J., Wang, B., Song, Z., Xiang, J., Hu, S., et al. (2017). Каталитический пиролиз огнестойкого ударопрочного полистирола на различных твердых кислотных катализаторах. Топливный процесс. Technol. 155, 32–41. DOI: 10.1016 / j.fuproc.2016.01.018
CrossRef Полный текст | Google Scholar
Марсилла, А., Бельтран, М. И., Эрнандес, Ф., и Наварро, Р. (2004). Дезактивация HZSM5 и HUSY при каталитическом пиролизе полиэтилена. Заявл. Катал. A Gen. 278, 37–43. DOI: 10.1016 / j.apcata.2004.09.023
CrossRef Полный текст | Google Scholar
McNeill, I.C., и Bounekhel, M. (1991). Исследования термической деструкции сложных полиэфиров терефталата: 1. Поли (алкилентерефталаты). Полимерная деградация. Stab. 34, 187–204. DOI: 10.1016 / 0141-3910 (91)-C
CrossRef Полный текст | Google Scholar
Макнил, И.К., Зульфикар М. и Кусар Т. (1990). Подробное исследование продуктов термической деструкции полистирола. Polym. Деграда. Stab. 28, 131–151. DOI: 10.1016 / 0141-3910 (90)
-O
CrossRef Полный текст | Google Scholar
Миандад Р., Баракат М. А., Абуриазаиза А. С., Рехан М., Исмаил И. М. И. и Низами А. С. (2017b). Влияние видов пластиковых отходов на жидкое пиролизное масло. Внутр. Биодетериор. Биодеград . 119, 239–252. DOI: 10.1016 / j.ibiod.2016.09.017
CrossRef Полный текст | Google Scholar
Миандад Р., Баракат М. А., Абуриазаиза А. С., Рехан М. и Низами А. С. (2016a). Каталитический пиролиз пластиковых отходов: обзор. Process Safety Environ. Защитить . 102, 822–838. DOI: 10.1016 / j.psep.2016.06.022
CrossRef Полный текст | Google Scholar
Миандад Р., Баракат М. А., Рехан М., Абуриазаиза А. С., Исмаил И. М. И. и Низами А. С. (2017a). Пластмассовые отходы превращаются в жидкое масло путем каталитического пиролиза с использованием природных и синтетических цеолитных катализаторов. Waste Manag. 69, 66–78. DOI: 10.1016 / j.wasman.2017.08.032
PubMed Аннотация | CrossRef Полный текст | Google Scholar
Миандад Р., Кумар Р., Баракат М. А., Башир К., Абуриазаиза А. С., Низами А. С. и др. (2018). Неиспользованное преобразование пластиковых отходов в углеродно-металлические LDO для адсорбции конго красного. J Colloid Interface Sci. 511, 402–410. DOI: 10.1016 / j.jcis.2017.10.029
PubMed Аннотация | CrossRef Полный текст | Google Scholar
Миандад, Р., Низами, А.С., Рехан, М., Баракат, М.А., Хан, М.И., Мустафа, А. и др. (2016b). Влияние температуры и времени реакции на конверсию отходов полистирола в жидкое пиролизное масло. Управление отходами . 58, 250–259. DOI: 10.1016 / j.wasman.2016.09.023
PubMed Аннотация | CrossRef Полный текст | Google Scholar
Миандад Р., Рехан М., Низами А. С., Баракат М. А. Э. Ф. и Исмаил И. М. (2016c). «Энергия и продукты с добавленной стоимостью от пиролиза пластиковых отходов», в Переработка твердых отходов для производства биотоплива и биохимии , ред.П. Картикеян, К. Х. Субраманиан, С. Мутху (Сингапур: Springer), 333–355.
Google Scholar
Miskolczi, N., Bartha, L., and Deak, G. (2006). Термическое разложение полиэтилена и полистирола в упаковочной промышленности на различных катализаторах до топливоподобного сырья. Polym. Деграда. Укол . 91, 517–526. DOI: 10.1016 / j.polymdegradstab.2005.01.056
CrossRef Полный текст | Google Scholar
Мукерджи, М.К., и Тамотаран, П.С. (2014). Испытания на производительность и выбросы нескольких смесей отработанного пластикового масла с дизельным топливом и этанолом на четырехтактном двухцилиндровом дизельном двигателе. IOSR J. Mech. Гражданский Eng . 11, 2278–1684. DOI: 10.9790 / 1684-11214751
CrossRef Полный текст
Нилешкумар, К. Д., Яни, Р. Дж., Патель, Т. М., и Ратод, Г. П. (2015). Влияние смеси пластикового пиролизного масла и дизельного топлива на производительность одноцилиндрового двигателя CI. Внутр. J. Sci. Technol. Eng .1, 2349–2784.
Google Scholar
Низами А.С., Оуда О.К.М., Рехан М., Эль-Маграби А.М.О., Гарди Дж., Хассанпур А. и др. (2016). Потенциал природных цеолитов Саудовской Аравии в технологиях рекуперации энергии. Energy 108, 162–171. DOI: 10.1016 / j.energy.2015.07.030
CrossRef Полный текст | Google Scholar
Низами А. С., Рехан М., Вакас М., Накви М., Оуда О. К. М., Шахзад К. и др. (2017a). Заводы по переработке отходов: создание возможностей для экономики замкнутого цикла в развивающихся странах. Биоресурсы. Technol. 241, 1101–1117. DOI: 10.1016 / j.biortech.2017.05.097
PubMed Аннотация | CrossRef Полный текст | Google Scholar
Низами, А.С., Шахзад, К., Рехан, М., Оуда, О.К.М., Хан, М.З., Исмаил, И.М.И. и др. (2017b). Создание завода по переработке отходов в Макке: путь вперед в преобразовании городских отходов в возобновляемые источники энергии. Заявл. Энергия . 186, 189–196. DOI: 10.1016 / j.apenergy.2016.04.116
CrossRef Полный текст | Google Scholar
Обали, З., Сезги, Н. А., Догу, Т. (2012). Каталитическое разложение полипропилена на мезопористых катализаторах, содержащих оксид алюминия. Chem. Англ. J . 207, 421–425. DOI: 10.1016 / j.cej.2012.06.146
CrossRef Полный текст | Google Scholar
Огава Т., Куроки Т., Идэ С. и Икемура Т. (1982). Восстановление производных индана из отходов полистирола. J. Appl. Polym. Sci. 27, 857–869. DOI: 10.1002 / app.1982.070270306
CrossRef Полный текст | Google Scholar
Панда, А.К. и Сингх Р. К. (2013). Экспериментальная оптимизация процесса термокаталитического разложения отработанного полипропилена до жидкого топлива. Adv. Энергия Eng . 1, 74–84.
Google Scholar
Петерсон, Дж. Д., Вязовкин, С., и Уайт, К. А. (2001). Кинетика термической и термоокислительной деструкции полистирола, полиэтилена и полипропилена. Macromol. Chem. Phys. 202, 775–784. DOI: 10.1002 / 1521-3935 (20010301) 202: 6 <775 :: AID-MACP775> 3.0.CO; 2-G
CrossRef Полный текст | Google Scholar
Рамли М. Р., Осман М. Б. Х., Арифин А. и Ахмад З. (2011). Сшитая сеть полидиметилсилоксана посредством механизмов присоединения и конденсации (RTV). Часть I: синтез и термические свойства. Polym. Деграда. Укол . 96, 2064–2070. DOI: 10.1016 / j.polymdegradstab.2011.10.001
CrossRef Полный текст | Google Scholar
Ратнасари Д. К., Нахил М. А. и Уильямс П. Т. (2017). Каталитический пиролиз пластиковых отходов с использованием ступенчатого катализа для производства углеводородных масел бензинового ряда. J. Anal. Прил. Пиролиз 124, 631–637. DOI: 10.1016 / j.jaap.2016.12.027
CrossRef Полный текст | Google Scholar
Рехан М., Миандад Р., Баракат М. А., Исмаил И. М. И., Альмилби Т., Гарди Дж. И др. (2017). Влияние цеолитных катализаторов на жидкое масло пиролиза. Внутр. Биодетериор. Биодеград. 119, 162–175. DOI: 10.1016 / j.ibiod.2016.11.015
CrossRef Полный текст | Google Scholar
Рехан, М., Низами, А.С., Шахзад, К., Оуда, О.К. М., Исмаил, И. М. И., Алмилби, Т. и др. (2016). Пиролитическое жидкое топливо: источник возобновляемой энергии в Мекке. Источники энергии A 38, 2598–2603. DOI: 10.1080 / 15567036.2016.1153753
CrossRef Полный текст | Google Scholar
Rizzarelli, P., Rapisarda, M., Perna, S., Mirabella, E.F., La Carta, S., Puglisi, C., et al. (2016). Определение полиэтилена в смесях биоразлагаемых полимеров и в компостируемых мешках-носителях методами Py-GC / MS и TGA. J. Anal. Прил.Пиролиз 117,72–81. DOI: 10.1016 / j.jaap.2015.12.014
CrossRef Полный текст | Google Scholar
Саптоади, Х., Пратама, Н. Н. (2015). Использование отработанного масла из пластмасс в качестве частичного заменителя керосина в кухонных плитах под давлением. Внутр. J. Environ. Sci. Dev . 6, 363–368. DOI: 10.7763 / IJESD.2015.V6.619
CrossRef Полный текст | Google Scholar
Саркер М. и Рашид М. М. (2013). Отработанная смесь пластиков из полистирола и полипропилена в легкое топливо с использованием катализатора Fe2O3. Внутр. J. Renew. Energy Technol. Рез . 2, 17–28.
Google Scholar
Со, Й. Х., Ли, К. Х. и Шин, Д. Х. (2003). Исследование каталитической деструкции полиэтилена высокой плотности методом анализа углеводородных групп. J. Anal. Прил. Пирол . 70, 383–398. DOI: 10.1016 / S0165-2370 (02) 00186-9
CrossRef Полный текст | Google Scholar
Серрано Д. П., Агуадо Дж. И Эскола Дж. М. (2000). Каталитическая конверсия полистирола над HMCM-41, HZSM-5 и аморфным SiO 2 –Al 2 O 3 : сравнение с термическим крекингом. Заявл. Катал. B: Окружающая среда. 25, 181–189. DOI: 10.1016 / S0926-3373 (99) 00130-7
CrossRef Полный текст | Google Scholar
Серрано Д. П., Агуадо Дж. И Эскола Дж. М. (2012). Разработка передовых катализаторов для переработки полиолефиновых пластмассовых отходов в топливо и химические вещества. ACS Catal. 2, 1924–1941. DOI: 10.1021 / cs3003403
CrossRef Полный текст | Google Scholar
Шах, Дж., И Ян, М. Р. (2015). Влияние полиэтилентерефталата на каталитический пиролиз полистирола: Исследование жидких продуктов. J. Taiwan Inst. Chem. Англ. 51, 96–102. DOI: 10.1016 / j.jtice.2015.01.015
CrossRef Полный текст | Google Scholar
Сиддики, М. Н., и Редви, Х. Х. (2009). Пиролиз смешанных пластиков для восстановления полезных продуктов. Топливный процесс. Technol. 90, 545–552. DOI: 10.1016 / j.fuproc.2009.01.003
CrossRef Полный текст | Google Scholar
Шрининси В., Саэроджи М. Г., Трисунарьянти В., Армунанто Р. и Фалах И. И. (2014).Производство топлива из пластиковых отходов LDPE на природном цеолите на основе металлов Ni, Ni-Mo, Co и Co-Mo. Proc. Environ. Sci. 20, 215–224. DOI: 10.1016 / j.proenv.2014.03.028
CrossRef Полный текст | Google Scholar
Syamsiro, M., Cheng, S., Hu, W., Saptoadi, H., Pratama, N. N., Trisunaryanti, W., et al. (2014). Жидкое и газообразное топливо из пластиковых отходов путем последовательного пиролиза и каталитического риформинга на природных цеолитных катализаторах Индонезии. Waste Technol. 2, 44–51. DOI: 10.12777 / Wastech.2.2.44-51
CrossRef Полный текст | Google Scholar
Текин, К., Акалин, М. К., Кади, К., и Карагез, С. (2012). Каталитическое разложение отработанного полипропилена пиролизом. Дж. Энергия Инс . 85, 150–155. DOI: 10.1179 / 1743967112Z.00000000029
CrossRef Полный текст | Google Scholar
Тилакаратне Р., Тессонье Дж. П. и Браун Р. К. (2016). Превращение метокси- и гидроксильных функциональных групп фенольных мономеров над цеолитами. Green Chem. 18, 2231–2239. DOI: 10.1039 / c5gc02548f
CrossRef Полный текст | Google Scholar
Уэмичи Ю., Хаттори М., Ито Т., Накамура Дж. И Сугиока М. (1998). Поведение дезактивации цеолита и катализаторов кремнезема-оксида алюминия при разложении полиэтилена. Ind. Eng. Chem. Res. 37, 867–872. DOI: 10.1021 / ie970605c
CrossRef Полный текст | Google Scholar
Уэмичи, Ю., Накамура, Дж., Ито, Т., Сугиока, М., Гарфорт, А.А. и Дуайер Дж. (1999). Превращение полиэтилена в бензиновые топлива путем двухступенчатой каталитической деградации с использованием диоксида кремния – оксида алюминия и цеолита HZSM-5. Ind. Eng. Chem. Res. 38, 385–390. DOI: 10.1021 / ie980341 +
CrossRef Полный текст | Google Scholar
Укей, Х., Хиросе, Т., Хорикава, С., Такай, Ю., Така, М., Адзума, Н. и др. (2000). Каталитическое разложение полистирола на стирол и конструкция пригодного для повторного использования полистирола с диспергированными катализаторами. Катал.Сегодня 62, 67–75. DOI: 10.1016 / S0920-5861 (00) 00409-0
CrossRef Полный текст | Google Scholar
Вакас М., Рехан М., Абуриазаиза А. С. и Низами А. С. (2018). «Глава 17 — Биопереработка сточных вод на основе микробной электролизной ячейки: возможности и проблемы», журнал в прогрессе и последние тенденции в микробных топливных элементах , ред. К. Датта и П. Кунду (Нью-Йорк, Нью-Йорк: Elsevier Inc.), 347 –374. DOI: 10.1016 / B978-0-444-64017-8.00017-8
CrossRef Полный текст
Уильямс, П.Т. (2006). «Выход и состав газов и масел / парафинов от переработки отходов пластика». In Feeds Tock Recycling and Pyrolysis of Waste Plastics: преобразование пластиковых отходов в дизельное топливо и другое топливо , ред. Дж. Шейрс и В. Камински (Западный Суссекс: John Wiley & Sons Press), 285–309.
Google Scholar
Ву, К., и Уильямс, П. Т. (2010). Пиролиз – газификация пластмасс, смешанных пластмасс и реальных пластиковых отходов с катализатором Ni – Mg – Al и без него. Топливо 89, 3022–3032. DOI: 10.1016 / j.fuel.2010.05.032
CrossRef Полный текст | Google Scholar
Wu, J., Chen, T., Luo, X., Han, D., Wang, Z., and Wu, J. (2014). TG / FTIR-анализ поведения при совместном пиролизе PE, PVC и PS. Waste Manag. 34, 676–682. DOI: 10.1016 / j.wasman.2013.12.005
PubMed Аннотация | CrossRef Полный текст | Google Scholar
Сюэ, Ю., Джонстон, П., и Бай, X. (2017). Влияние режима контакта катализатора и газовой атмосферы при каталитическом пиролизе пластиковых отходов. Energy Conv. Manag. 142, 441–451. DOI: 10.1016 / j.enconman.2017.03.071
CrossRef Полный текст | Google Scholar
Йошиока, Т., Грауз, Г., Эгер, К., Камински, В., и Окуваки, А. (2004). Пиролиз полиэтилентерефталата в установке с псевдоожиженным слоем. Polym. Деграда. Stab. 86, 499–504. DOI: 10.1016 / j.polymdegradstab.2004.06.001
CrossRef Полный текст | Google Scholar
Zeaiter, J. (2014). Исследование процесса пиролиза отходов полиэтилена.