Токарный станок по дереву самодельный из фанеры
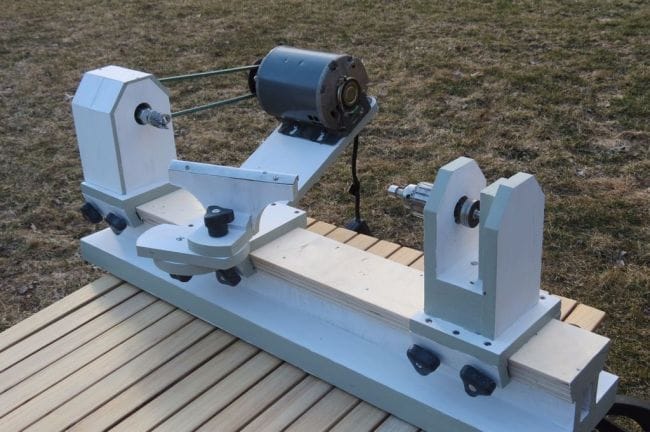
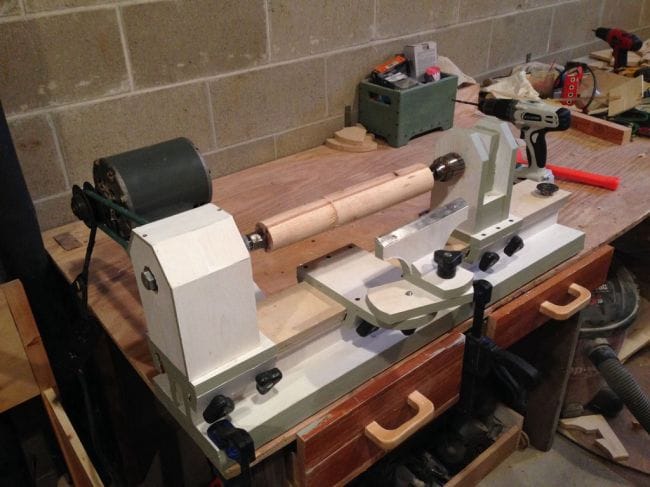
В этой статье, рассмотрим очередную модель токарного станка по дереву. 15-летний мастер-самодельщик изготовил станок из лома. Для изготовления мастер использовал следующие
Инструменты и материалы:
-Фанера;
-Клей;
-Циркулярная пила;
-Карандаш;
-Линейка;
-Струбцины;
-Торцовочная пила;
-Сверлильный станок;
-Шуруповёрт;
-Ленточнопильный станок;
-Болты с гайками и шайбами;
-Подшипники;
-Шурупы;
-Металлическая пластина;
-Электродвигатель;
-Шкив;
-Барашковый винт;
-Ротор электродрели с патроном;
-Петля;
-Краска;
-Кисточка;
-Конус металлический;
-Ремень;
Шаг первый: основание
Основание станка выполнено из клееной 12 мм фанеры. Отрезает три фанерных прямоугольника. Склеивает их. Торцует край.
По всей длине основания делает два параллельных паза.
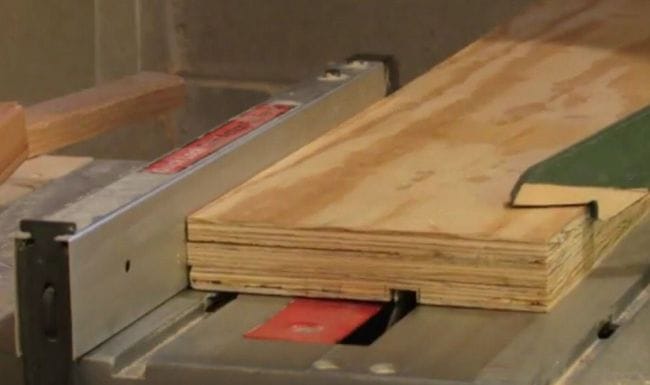
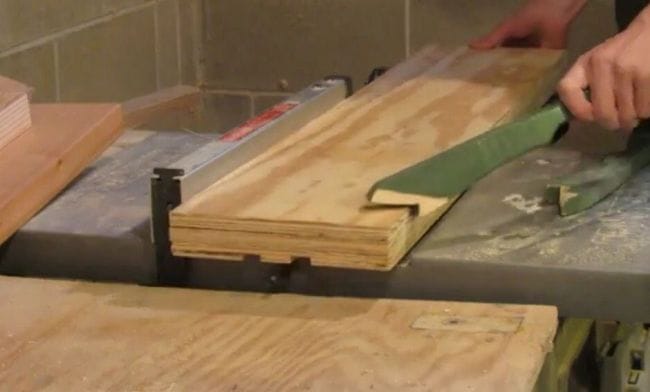
В эти пазы, на всю длину, должны вставляться фанерные стойки. Сверху их будет установлена направляющая. Отрезает две стойки.
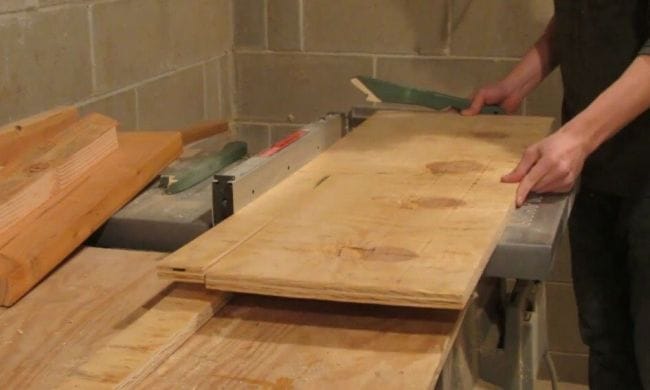
Отрезает две детали для направляющей. Склеивает их. Торцевые части отрезает под углом 20°. Делает на направляющей два паза.
Склеивает основание.
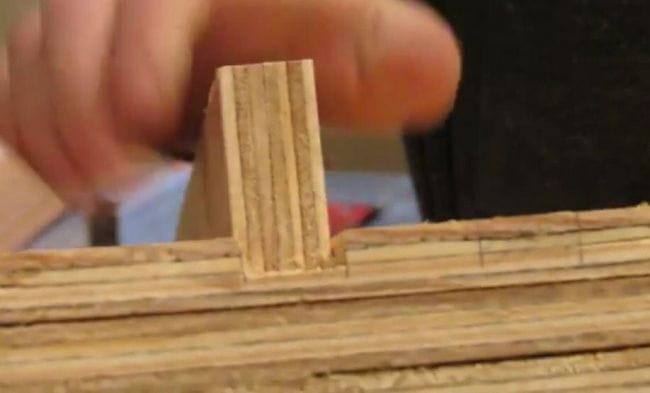
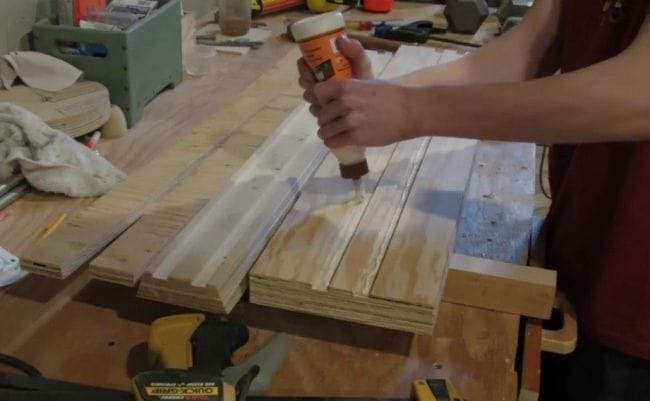
Шаг второй: передняя бабка
Из фанеры изготавливает переднюю бабку. Отрезает два прямоугольных куска фанеры. Вырезает у них полукругом верхнюю часть. Сверлит отверстие для подшипника. Устанавливает подшипник в отверстие на клей.
Вырезает три фанерных квадрата. Склеивает их. По бокам этого квадрата будут крепится две детали передней бабки.
Шаг третий: нижняя часть бабки
Отрезает две прямоугольных заготовки (зажимы). Торцовые части заготовок отрезаны под углом 20°. Посередине заготовок сделан паз. В пазе делает два отверстия, для установки гайки и шайбы и сквозные отверстия под болт. Гайку и шайбу приклеивает клеем. В паз зажимов прикручивает металлическую полоску. Изготавливает платформу по ширине направляющей. Прикручивает к платформе, с двух сторон, зажимы. платформа с зажимами свободно перемещается по направляющей. Для фиксации достаточно закрутить болты на зажимах. металлическая пластинка прижимается к направляющей, и платформа фиксируется.
Шаг четвертый: сборка передней бабки
К блоку прикручивает две части с подшипниками.
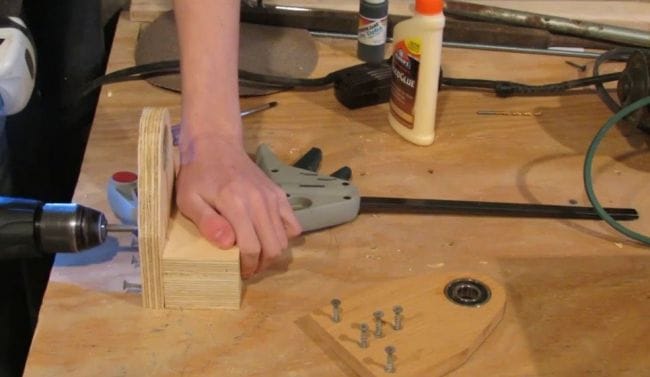
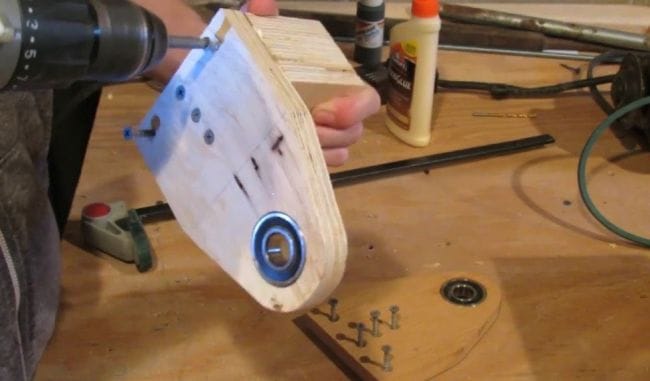
Прикручивает бабку к платформе.

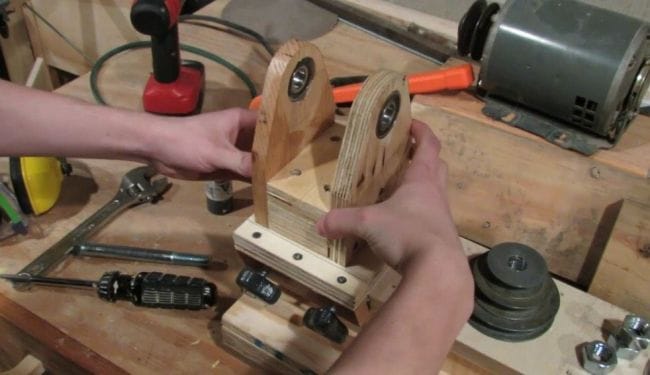
Устанавливает шкив.
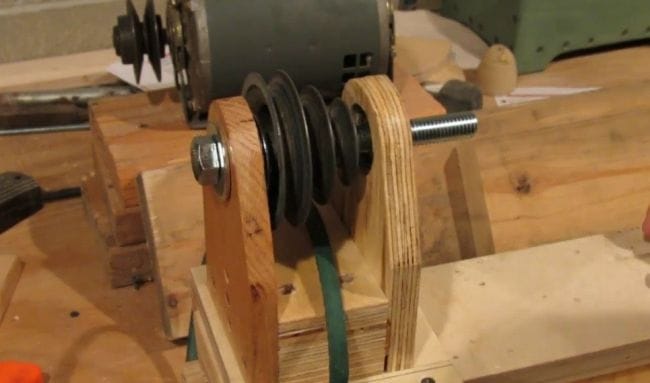
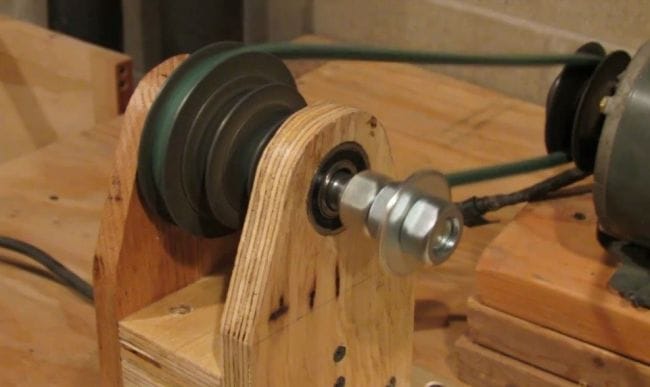
Шаг пятый: изготовление задней бабки и подручника
Принцип изготовления задней бабки такой же, как и передней. В качестве пиноли мастер использует ротор с патроном от дрели.
Подручник мастер изготавливает из фанеры со вставкой металлического уголка в верхней части.
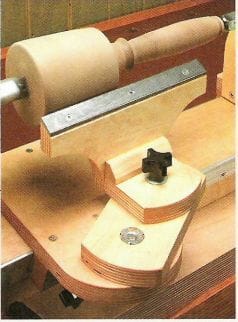
Шаг шестой: двигатель, защита бабок, шпиндель
Двигатель крепится на фанерной доске соединенной с основанием петлей.
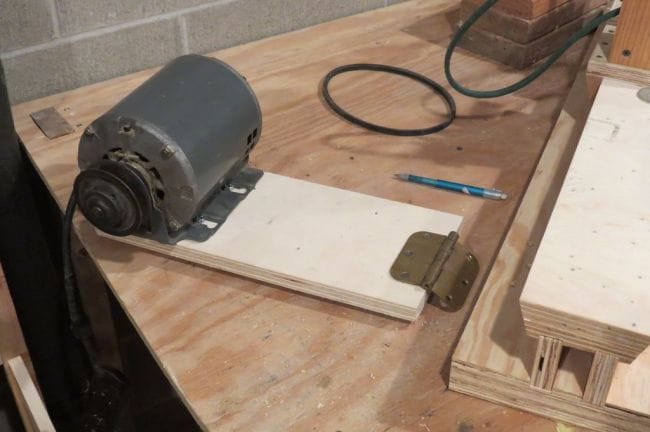
На заднюю и переднюю бабки устанавливает защиту.
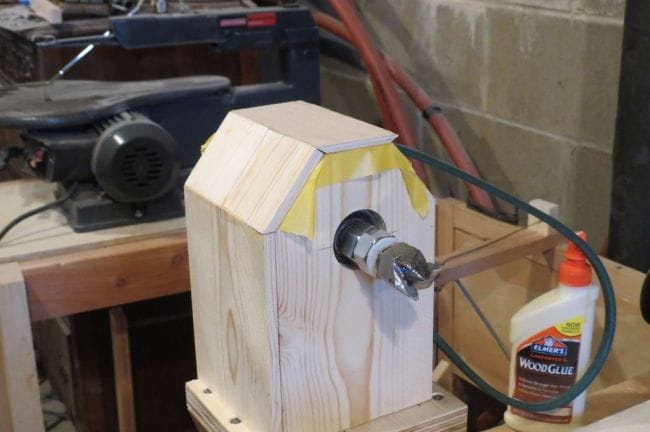
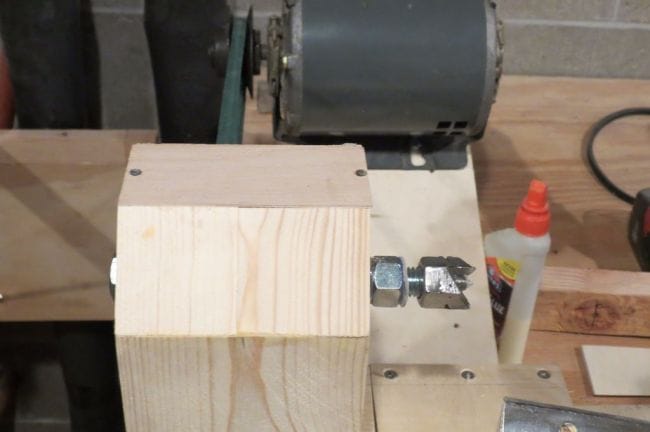
Шпиндель мастер изготовил, сварив две гайки и шайбу. Затем в гайках сделал «зубы».
Шаг седьмой: окраска
Красит части станка.
Станок готов. Осталось установить заготовку и попробовать его в работе.
Видео по изготовлению и сборке станка.
Источник
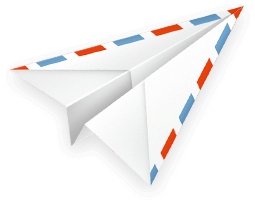
Получайте на почту подборку новых самоделок. Никакого спама, только полезные идеи!
*Заполняя форму вы соглашаетесь на обработку персональных данных
usamodelkina.ru
Идеальный ящик для инструмента, вырезанный лазером из фанеры своими руками
В прошлом году я начал приобретать точные вычислительные инструменты и решил построить ящик, в котором могу хранить их. Будучи стеснённым во времени, я решил, что вместо работы руками, я распилю все части при помощи лазера.
Эта инструкция рассчитана на сборку очень прочного ящика для инструментов из фанеры своими руками, состоящего из 9 отсеков. Выдвижные полки спроектированы таким образом, что они заблокированы в ящике и не могут быть вытащены полностью, так что вытянуть и уронить полку с дорогим инструментом, повредив его, не получится.
Замок можно встроить как для закрепления выдвижных ящиков, так и для того, чтобы запереть верхний отсек. Этот органайзер для инструментов выдержал год жесткого обращения, поскольку он постоянно перемещается между моей квартирой и местной мастерской.
Шаг 1: Материалы
Древесина:
- 2 листа балтийской берёзы 150*150 см и толщиной 0,6 см
- 1 лист балтийской берёзы 30*38 см и толщиной 0,15 см
Отделка:
- Сатиновый полиуретановый лак
Металличсеские изделия:
Вкладыши из пены:
Шаг 2: Несколько замечаний о дизайне
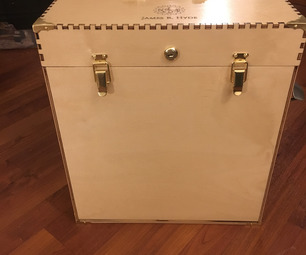
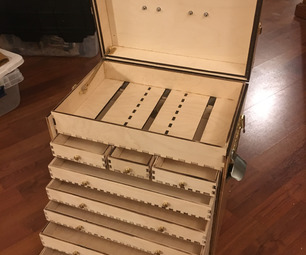
Для лучшей защиты в коробке применены двуслойные стенки. В то время как все внутренние части изготовлены из 0,6 см балтийской березы, все внешние стенки сделаны двуслойными. Это позволило встроить защиту от пыли в верхний отсек, а также добавить переднюю стенку, закрывающую все полки во время транспортировки. В инструкции внутренний слой, на который крепятся все полки, будет называться внутренним корпусом, а внешний слой, покрытый уретаном, будет называться внешним корпусом.
Также уделите внимания заметкам, встроенным в фотографии. Почти каждая фотография снабжена заметками, помогающими понять принцип изготовления ящика. Они должны очень помочь вам разобраться в правильном склеивании и сборке частей.
Шаг 3: Лазерная резка деталей
Прикреплённые файлы содержат все нужные проекты для распила: файлы *.ai для Illustrator и файлы *.dxf. Все деревянные детали вырезаются из балтийской березы толщиной 0,6 см. Все части были разрезаны при помощи лазерного резчика 150W GWeike LC6090 с установленной мощностью в 80% на 10 мм/с. Также я слегка зашлифовал все лицевые и внутренние поверхности наждачкой с зерном на 220. Уделите внимание шлифовке и ваши ящики будут выдвигаться значительно легче.
Шаг 4: Сборка внутреннего корпуса
Сначала мы соберём внутренний корпус. Начните с проверки того, что все подходит друг другу, также убедитесь, что понимаете, как всё собирается вместе. В зависимости от клея, который вы используете, сборка может быть завершена очень быстро. Не нужно обильно смазывать всё клеем — достаточно капнуть по одной капельке клея на каждый зубец. Избыточное количество клея лишь доставит хлопот в будущем, когда вам придется его отчищать.
Сперва соберите две верхние полки, в которых расположатся три выдвижных ящика. Приклейте разделители к полкам, а затем приклейте всю конструкцию к задней панели внутреннего корпуса. Затем прикрепите три оставшиеся секции полок к задней панели. Затем вы можете прикрепить боковые панели внутреннего корпуса.
Проще всего это сделать, если клей на всех полках еще влажный, или хотя бы подвижный. Наконец, можно прикрепить нижнюю панель внутреннего корпуса и переднюю панель, которая идёт поперек верхней части внутреннего корпуса (она образует переднюю часть верхнего отсека). Используйте много зажимов, чтобы стянуть все части вместе, пока клей сохнет.
Уберите весь лишний клей со всех соединений перед тем, как продолжите. Любые бугорки засохшего клея сделают затруднительным или даже невозможным вставку ящичков, когда мы приступим к этому шагу. Проще всего зачистить клей пока он еще мягок, я обычно убираю его при помощи долота или квадратного напильника.
Отшлифуйте дерево, чтобы убрать весь клей, выступающий на внешней части корпуса. Также убедитесь, что все зубцы утоплены друг в друга и не выступают. Это нужно для того, чтобы ничего не мешалось, когда мы будем соединять внешний и внутренний корпус.
Шаг 5: Собираем выдвижные ящички
Сборка ящичков очевидна. Зашлифуйте внешнюю поверхность, чтобы они могли легко войти во внутренний корпус. Заметьте, что на задней панели каждого ящичка есть небольшое отверстие примерно в 1 мм толщиной. Маленькие ящички имеют по одному отверстию, а большие по два. Отверстия отмечают место, на котором нужно установить блокирующий механизм.
Круговые механизмы вырезаны из задней панели корпуса, чтобы сохранить материал дерева. Блокирующие механизмы задержат ящичек в коробке, и вы не сможете полностью вытащить его, уронив оборудование на пол. Закрутите маленький винт (4 штуки длиной примерно 1,3 см) через заднюю стенку ящичка в блокирующий механизм. Затяните винт настолько, чтобы вы могли легко повернуть блокирующий механизм из горизонтального незаблокированного положения в вертикальное заблокированное.
Это позволит вам легко блокировать ящичек в коробке без необходимости всё разбирать. В прикреплённом видео показано, как ящички блокируются во внутреннем корпусе.
Шаг 6: Собираем крышку
Соберите крышку внутреннего корпуса и дайте ей высохнуть. Затем поверх внутренней крышки можно собрать внешнюю крышку. Проверьте, что все части подходят по размерам, и выложите их для склейки и быстрой сборки. Соберите внешнюю крышку поверх внутренней, нанесите клей на поверхность внутренней крышки, так чтобы обе поверхности крепко склеились.
Если у вас не получается собирать вещи быстро — используйте клей, который сохнет дольше, таким образом вы не испортите вашу заготовку. После склейки двух слоев, я поместил крышку над внутренним корпусом и убедился, что крышка хорошо прилегает и не требует дополнительной обработки.
Шаг 7: Сборка внешнего корпуса
Внешний корпус склеивается поверх внутреннего корпуса. Намажьте клеем заднюю и боковые стороны внешнего корпуса, а также нанесите клей на внутренний корпус. Отметьте для себя, что внешний корпус выше — дополнительное место внизу будет использоваться для хранения передней панели. Чтобы определить высоту для внутреннего корпуса, установите крышку и убедитесь, что внешний и внутренний корпуса сидят хорошо.
В основании коробки будут две панели. Внутренняя панель имеет длинное отверстие, оно закрепляет переднюю панель на нужном месте. Приклейте внутреннюю панель к внешней и быстро приклейте всю конструкцию к внутреннему\внешнему корпусу.
После того, как всё высохнет, установите ящички на место. При необходимости, зашлифуйте края ящичков — они будут двигаться более плавно. Закончите шаг шлифовкой передней части ящика, так чтобы все выдвижные ящички и полки были гладкими и ровными.
Шаг 8: Собираем переднюю панель
Сперва, поместите внутреннюю переднюю панель на место и используйте отверстия в ней в качестве ориентиров для установки ручек для ящичков. Затем склейте две передних панели. Вы можете установить их в ящик, чтобы выровнять относительно друг друга. Затем аккуратно снимите склеенную панель и при необходимости зажмите в тиски.
Когда клей высохнет, отшлифуйте панель, чтобы она сидела хорошо. Также можно скруглить нижнюю часть панели при помощи наждака или рубанка. Такое скругление поможет упростить вставку панели, когда вы будете запирать ящик.
После сборки я обнаружил, что ручки выдвижных ящичков оказались длинноваты и не давали передней панели встать ровно относительно ящичков, поэтому мне пришлось немного срезать их.
Теперь, когда всё собрано вместе, зашлифуйте внешнюю часть ящика, чтобы придать ему опрятный вид.
Шаг 9: Прикрепляем металлические части и завершаем внешний вид ящика
Для установки крышки, я использовал петлю для фортепиано. Петля была слишком длинной, и я подрезал её по размеру коробки. Сверху я прикрутил ручку от гитарного усилителя Fender. По бокам были прикручены 4 застёжки. Тут я немного переборщил, так как хватило бы и двух застёжек на передней панели (но если вы собираетесь использовать ящик для переноса тяжелого инструмента, то лучше прикрутите 4 застёжки). Боковые ручки были прикручены на короткие винты — таким образом, я не задел внутренние ящички. На углы ящика были установлены латунные уголки, они защитят дерево от повреждений.
Замок — обычный замок от ящика стола. Я загнул язычок замка так, чтобы он цеплялся за скобу, прикрученную к внутренней части ящика. И наконец, я прикрутил сбоку открывалку для бутылок, ведь вы никогда не знаете, когда она вам пригодится. После установки всех этих деталей, открутите их, чтобы завершить обработку древесины.
Я нанёс 4 слоя сатинового полиуретанового лака. Дайте лаку высохнуть после каждого нанесения и слегка отполируйте его наждачкой с зерном на 220. Я залакировал только внешнюю часть ящика, внутри древесина осталась полностью нетронутой.
Дальше я вырезал лист дерева, который положу в верхний отсек. Он закроет отверстия механизма выдвижных ящичков. Я не заклеил его, так как мне в любой момент может понадобиться доступ к этой части ящика.
Теперь соберите всё обратно и подумайте, что вы хотите положить в ваш ящик.
Шаг 10: Опциональный. Вырезаем формы в пене
ЗАМЕТКА: Пена, используемая в ящиках механизмов — очень спорная тема. Основной проблемой является то, что она может выделять неопрен, который может способствовать порче и ржавлению приборов. Поэтому подумайте, какие приборы и инструменты будут находиться в вашем ящике и возможно, замените пену поролоном. Также, если вы захотите вырезать отверстия в пене при помощи лазера, помните, что это огнеопасно! Чтобы инструмент было проще доставать, сделайте зазоры между ним и пеной примерно в 2 см.
masterclub.online
Самоделные инструменты
Самоделные инструменты Перейти к содержаниюДоброго времени суток! Шлифовка – это довольно пыльный и грязный процесс, без которого не проходит ни одно изготовление самоделок из дерева или пластика. Сегодняшнее поделка поможет одним выстрелом поразить двух зайцев, а именно: поможет избавиться от крупнодисперсной и мелкодисперсной пыли…
Доброго времени суток! В сегодняшней статье мы поговорим о том, как можно сделать лобзиковый станок своими руками…
Всем привет. Из пенопласта можно сделать много интересных вещей: объёмные буквы и фигуры, модели судов и самолётов, арт объекты. Именно для таких целей я и
Read More
Захотелось собрать станочек для сверления печатных плат и прочей мелочёвки, варианты по типу цанговый патрон прямо на валу моторчика меня не устраивали. Нужно было что-то
Read More
Перевёл alexlevchenko для mozgochiny.ru Моё почтение! В сегодняшней статье мы немного доработаем сверлильный станок, превратив его в барабанную шлифмашинку. При изготовлении подобных самодельных шпинделей будут
Read More
Перевёл alexlevchenko для mozgochiny.ru Моё почтение! Любой начинающий мастер, получивший практический опыт, начинает искать, так называемые «короткие пути», которые помогут сэкономить время или облегчить и
Read More
Перевёл alexlevchenko для mozgochiny.ru Приветствую уважаемых МозгоЧинов! При работе с гравером или мини-дрелью нехватка дополнительного освещения особо ощутима. При изготовлении данной поделки автор использовал 3D-принтер
Read More
Перевёл alexlevchenko для mozgochiny.ru Приветствую уважаемых читателей! В сегодняшней статье речь пойдёт о различных струбцинах и зажимах.
Перевёл alexlevchenko для mozgochiny.ru Доброго времени суток. Распайка радиодеталей с 3-мя или более выводами требует определенной сноровки. Не додержишь – ничего не выпаяешь, передержишь –
Read More
Перевёл alexlevchenko для mozgochiny.ru Всем привет! Довольно часто возникает необходимость выкрутить/подковырнуть что-либо, но не будешь же ради этого постоянно таскать с собой различный инструмент? Для
Read More
Доброго времени суток! Прошу прощения за оффтоп, но читаю давно и несколько раз видел подобные посты. Надеюсь администрация не будет против такого сообщения. Очень нужны
Read More
Перевёл alexlevchenko для mozgochiny.ru Всем привет. В статье автор демонстрирует один из вариантов хранения инструментов в мастерской.
Перевёл alexlevchenko для mozgochiny.ru Всем привет! Сегодня у нас небольшая статья о том, как сделать простой лепестковый шлифовальный «барабан» своими руками. Часто в процессе шлифовки
Read More
Перевёл alexlevchenko для mozgochiny.ru Доброго времени суток! Измерение напряжения на плоских батарейках довольно хлопотное занятие, особенно это касается крошечных батареек для часов и слуховых аппаратов.
Read More
Перевёл alexlevchenko для mozgochiny.ru Доброго времени суток! Сегодня мы поговорим об прецизионных измерениях. Необходимость точного контроля температурного режима обуславливается различными процессами. Величина измеряемой температуры (в
Read More
Your browser doesn’t support canvas.
Мастер-классы | Как сделать | DIY | Handmade | Self made | Поделки | Своими руками | Карта сайта | Реклама
МозгоЧины — сообщество для энтузиастов технического творчества © 2010 – 2018mozgochiny.ru
чертежи, материалы, инструменты, сборка, настройка
Вопрос-ОтветСтанок ЧПУ с разным рабочим полем можно изготовить самостоятельно из фанеры. Этот материал стоит недорого, работать с ним легко, к тому же, он обладает высокой прочностью и может переносить большие нагрузки.
Станок ЧПУ с разным рабочим полем можно изготовить самостоятельно из фанеры. Этот материал стоит недорого, работать с ним легко, к тому же, он обладает высокой прочностью и может переносить большие нагрузки. Изделия из фанеры прочны и практичны. Работа по созданию станка проводится в несколько этапов: сначала делают чертежи, затем готовят материалы и инструменты, выпиливают необходимые элементы конструкции, собирают в виде конструкторов и настраивают станки.
Каждый этап требует внимательного подхода. ЧПУ из фанеры позволит обрабатывать дерево в домашних условиях, создавать мебель из фанеры. Готовый станок можно посмотреть на фото. Фанерная машина будет работать не хуже фабричного изделия. Возможности такого оборудования велики.
Чертежи
На начальном этапе рабочего процесса делают чертежи. Чертежи могут отличаться друг от друга в зависимости от того, какой тип оборудования с программным управлением был выбран, какое рабочее поле предусмотрено. Создавая чертёж будущему станку, заостряют внимание на следующих факторах:
- какие детали нужно будет сделать самостоятельно, а какие купить в готовом виде;
- какой толщины потребуется фанера;
- каким образом будут фиксироваться детали.
Элементы простой формы делают самостоятельно. К таким деталям относят: станину, столешницу, держатели, кожух, суппорт и некоторые другие. Элементы посложнее покупают готовыми. Люди, не имеющие опыта в создании чертежей, могут отыскать готовые чертежи, их можно найти в разных источниках, к примеру, в интернете. Там же есть чертежи мебели и схемы прочих фанерных изделий.

рабочий стол

макет станка
Подготовка материала и инструментов
Мебельные станки из фанеры с ЧПУ подходят только для работы в домашних условиях. Для начала готовят фанерный лист любого сорта, разной толщины. Столы, станины и суппорты изготавливают из фанерного листа толщиной 10мм, для станков, на которых планируется изготавливать крупные заготовки, берется фанера толщиной 20 мм. Кожухи, стопоры и прочие элементы выпиливают из фанеры толщиной 6 мм. Кроме материала, потребуются следующие инструменты и детали:
- подшипники и фиксаторы;
- валы;
- винты;
- шкивы;
- дрель или сверло;
- ремни передачи вращения;
- кабели;
- алюминиевый уголок;
- направляющие;
- острый нож;
- контроллер;
- лобзик или натяжная пила;
- наждачка.
Также, следует приготовить клей. Для работы с фанерой подойдет обычный ПВА. Для установки на корпус металлических деталей используют эпоксидную смолу. В качестве дополнительного оборудования приобретается шаговый мотор, вместо него может использоваться мотор от отработавшего сканера или принтера.
В процессе работы для соединения отдельных элементов используют шипы и пазы, которые предварительно смазывают клеем. При нанесении ПВА используют ватную палочку. Важно, чтобы в местах соединения не было щелей. Гвозди и саморезы для соединения элементов не годятся.
Как выпиливать детали
Фанерные детали выпиливают вручную, если их толщина не превышает 4 мм. Для этих целей подойдет ручной лобзик либо натяжная пила. Листы побольше, толщиной от 6 мм, допустимо пилить электрическим лобзиком, также подойдет дисковая пила. С тонкими листами (2 мм) можно работать ножом.
Пилу или лобзик ведут по линии разреза медленно, при быстром движении края изделия будут грубыми. Вырезая мелкие детали, лучше оставить запасное место, чтобы не ошибиться с размером. Отверстия в фанерных деталях проделывают с помощью сверлильного станка или сверла, также можно воспользоваться дрелью.
Выпиленное изделие следует обрабатывать, чтобы в ходе эксплуатации отдельные элементы не расслоились. Отшлифовка производится с помощью наждачной бумаги. Движения начинают от углового края фанерной детали по направлению волокон. Сами углы обрабатывают отдельно. Отверстия тоже требуют шлифовки, это делают той же наждачкой. Чтобы повысить устойчивость изделия к перепадам температур, поверхности обрабатывают грунтовкой. По завершении работы фанеру окрашивают.
Сборка деталей
Когда все детали будут готовы, их собирают наподобие конструктора. Сборка осуществляется с большой осторожностью, поскольку фанера представляет собой хрупкий материал, при неосторожном подходе она может растрескаться. В процессе сборки пазо-шипового соединения на фанерном полотне по всей длине проходятся клеем ПВА.
Болтовые соединения дополняют шайбами и граверами, чтобы они не разболтались и не раскрутились в ходе работы на станках. Все кабели размещают в ПВХ гофре. Станину и стол нужно устанавливать по уровню. Контроллер должен находиться отдельно, его помещают в шкаф. Сборку деталей можно осуществлять, глядя на фото, также в данном случае поможет схема.
Настройка
После сборки фрезера приступают к настройке станков. Следует тщательно проверить, как перемещаются движущиеся детали, как функционирует передающий механизм. Также следует отрегулировать положение включателей и выключателей, настроить показания датчиков.
На этапе настройке осуществляют следующие функции:
- установка нулевого показателя устройства;
- осевая калибровка движения суппорта, стола;
- диагностика точности обработки информации на датчиках.
Когда все будет готово, останется установить программу. Программное обеспечение для работы со станками могут создать не все, поэтому его покупают у специалистов, после чего устанавливают на оборудование. Произведя настройки можно приступать к работе на новом станке.
Фрезерный станок из фанеры разного рабочего поля можно изготовить самостоятельно. Для этого требуется подготовить нужный материал, инструменты и детали. В процессе работы необходимо следовать правилам. Готовый мебельный ЧПУ станок позволит проводить фрезерные работы в домашних условиях. Станок ЧПУ своими руками обойдется гораздо дешевле фабричного.
К изделиям самодельного производства следует подходить со всей ответственностью, они должны быть изготовлены согласно всем правилам.
Фрезером можно будет создавать большое количество деталей для изготовления мебели.
vseochpu.ru
Шлифовальный станок своими руками из фанеры
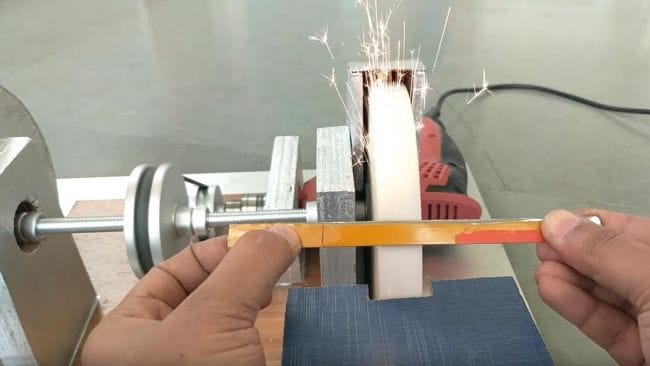
Если у вас до сих пор нет шлифовального станка, то предлагаю вам изготовить его самостоятельно! Данный станок состоит из двух абразивных кругов, а это значит что можно поставить одновременно круг более крупнозернистый и с мелкими зёрнами, для финишной шлифовки. Приводом данного станка будет служить обычная дрель или шуруповёрт с регулятором оборотов.
Что необходимо для изготовления станка.
- Шуруповёрт с регулятором оборотов
- Зубчатый ремень
- Два абразивных круга с мелкими и крупными зёрнами
- Длинная резьба с гайками
- Шайбы металлические
- Два подшипника
- Кусок фанеры (подставка) 45-35 см
- Два куска фанеры по меньше
- Вспомогательный инструмент
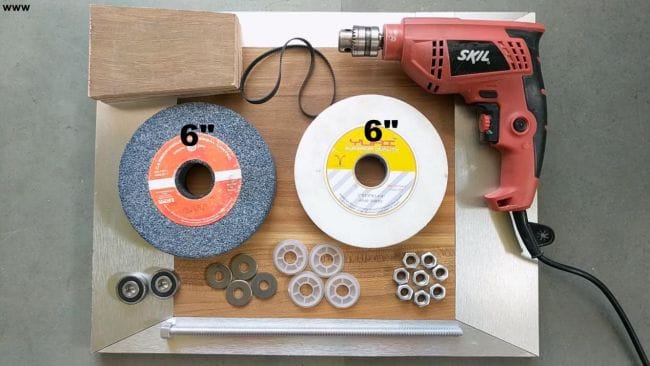
Изготовление станка
Внимание! Все размеры необходимо подбирать самостоятельно, в зависимости от того, какие детали вы будете использовать. В статье будет описана сама конструкция и инструкция по её изготовлению.
Первым делом из фанеры нужно вырезать два бруска, форма может быть квадратной или в виде пирамиды. Эти бруски будут выполнять роль держателей оси, на которую будут установлены абразивные круги, так что размеры и их высоту подбираем отталкиваясь от размеров используемых кругов. В фанере с помощью пера вырезаем два отверстия куда будут установлены подшипники, соответственно перо нужно подобрать по диаметру подшипников.
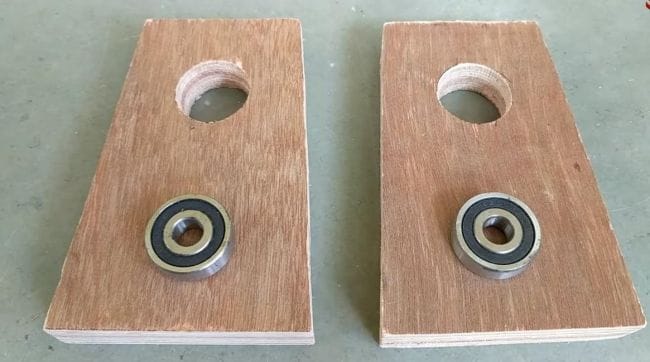
Затем эти отверстия промазываем суперклеем и впрессовываем в них подшипники.
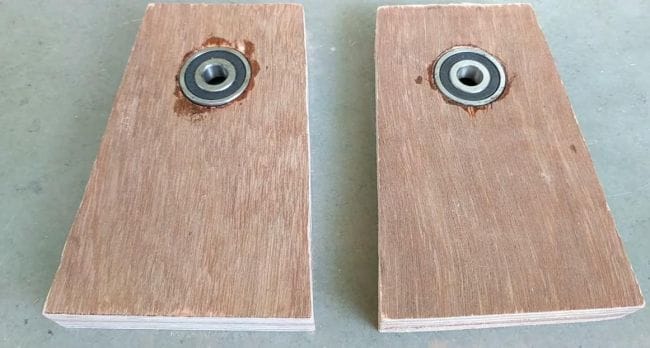
Подшипники подбираются очень просто, всё зависит от того, какую резьбу для оси вы будете использовать, желательно брать толщиной не менее 12 мм, соответственно диаметр внутреннего кольца подшипника должен быть примерно такой же.
Теперь приступаем к установки подставки оси. Для этого, как на фото ниже, делаем разметку, устанавливая бруски ровно друг на против друга, отступая от края основания примерно по 5-10 см. Сразу же делаем по два отверстия мелким сверлом, для шурупов.
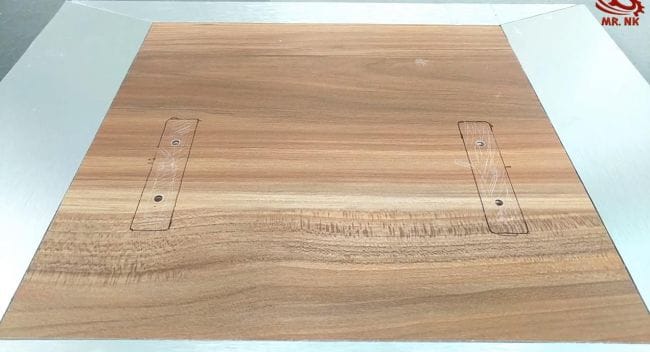
Обмазываем места разметки клеем ПВА и ставим на места подготовленные опоры. С обратной стороны фиксируем их шурупами.
Следующим шагом нужно будет изготовить два шкива для ремня. Для этого необходимо вырезать из толстой фанеры два круга, один 50 мм другой около 80 мм. Высверливать нужно коронками по дереву с направляющим сверлом, что бы у нас получилось дополнительно отверстие ровно по центры шкива.
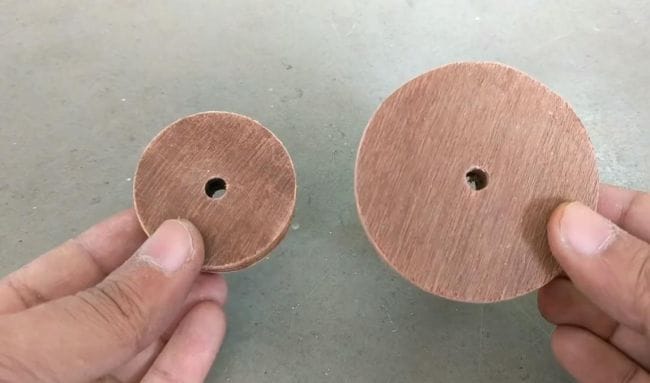
При помощи самодельного токарного станка, делаем посадочное место для ремня. Если токарного станка нет, можно зажать заготовку в дрели и так же сделать канавку, этот способ немного сложнее, но всё же осуществим.
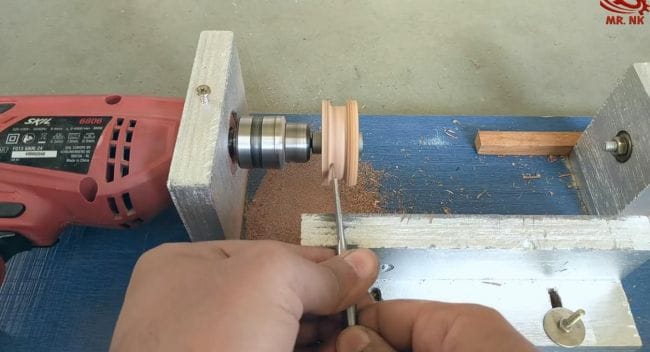
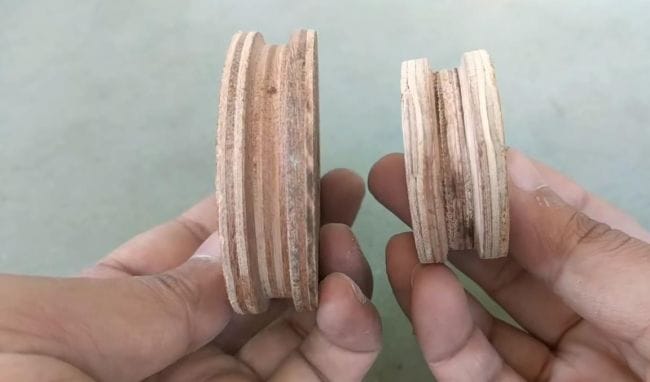
Далее берём резьбу и отпиливаем длинный кусок, что бы с обеих сторон стояк она выпирала по 8-12 см.
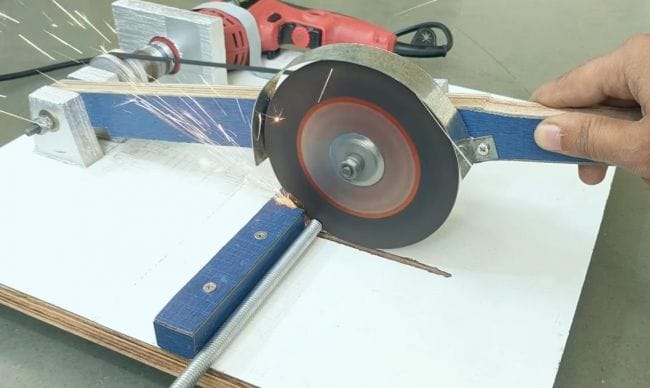
Теперь нужно установить ось на стойки, зафиксировать шкив и продеть ремень. С помощью гаек фиксируем большой шкив ровно по центру оси между стойками, а непосредственно ось крепим к подшипникам. Делать это нужно последовательно, сначала продев резьбу через один подшипник и накручивая гайки, устанавливать шкив и фиксировать ось.
Следующим шагом необходимо установить направляющую стойку, куда будет крепиться дрель (привод станка). Для этого в небольшом куске толстой фанеры, коронкой делаем отверстие чуть больше чем патрон на дрели, что бы дрель заходила в это отверстие и фиксировалась там своим пластиковым основание.
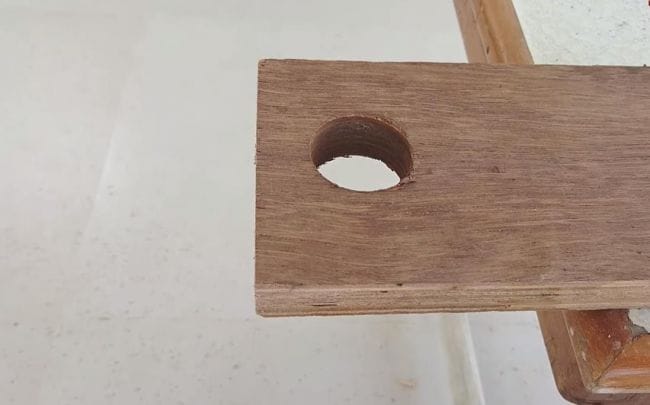
Затем отпиливаем лишнее. Должна получиться стойка, куда свободно будет фиксироваться дрель, высоту стойки нужно подбирать по размерам вашей дрели.
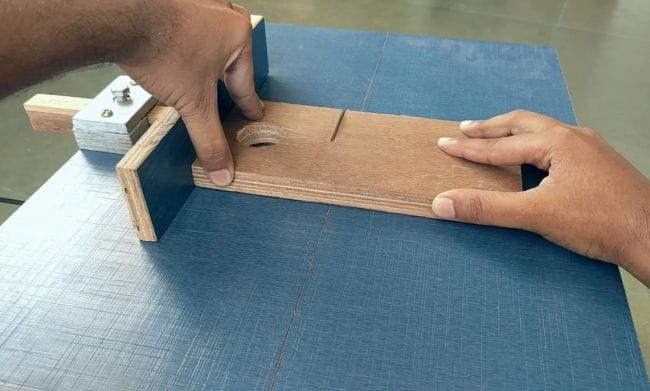
Теперь очерчиваем готовую стойку так, что бы она находилась с боку от шкива который установлен на оси и просверливаем два отверстия для шурупов. В патрон дрели будет крепиться шкив привода, поэтому нужно что бы оба шкива находились друг на против друга. Расстояние выбирать произвольно, по длине используемого ремня и по его натяжки.
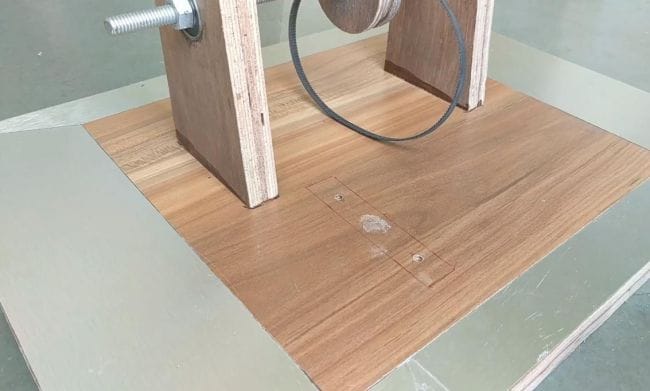
Затем промазываем место соединения клеем ПВА и ставим стойку на место. С обратной стороны фиксируем стойку шурупами.
Устанавливаем дрель в посадочное место.
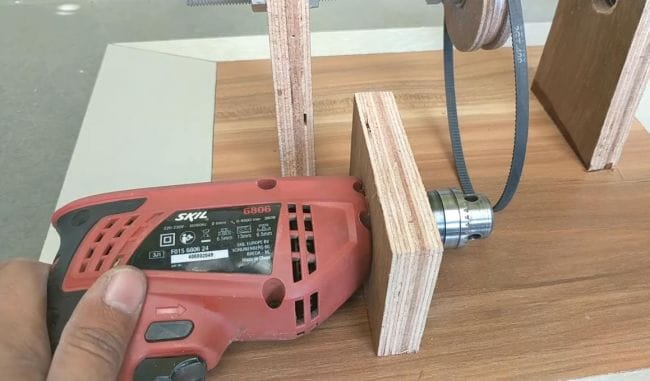
Во второй шкив вкручиваем болт и фиксируем его гайкой. Затем одеваем ремень и зажимаем шкив в патроне дрели.
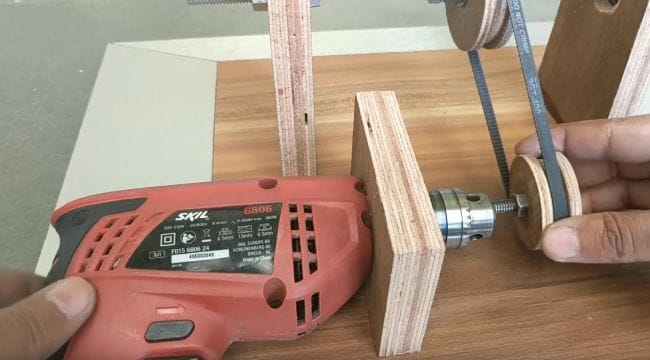
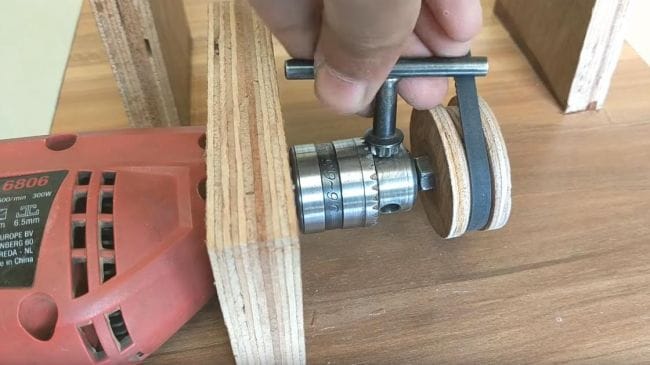
Далее фиксируем дрель при помощи скобы, вырезанной из жести.
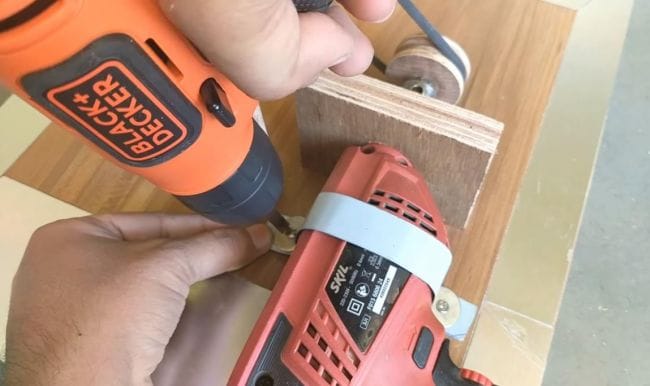
Регулятор оборотов (фиксированную кнопку) можно изготовить очень просто, для этого в небольшой брусок помещаем гайку и вкручиваем туда болт, эту конструкцию устанавливаем напротив кнопки дрели, по мере вкручивания болта, он будет давить на кнопку и мы получим непрерывные фиксированные обороты.
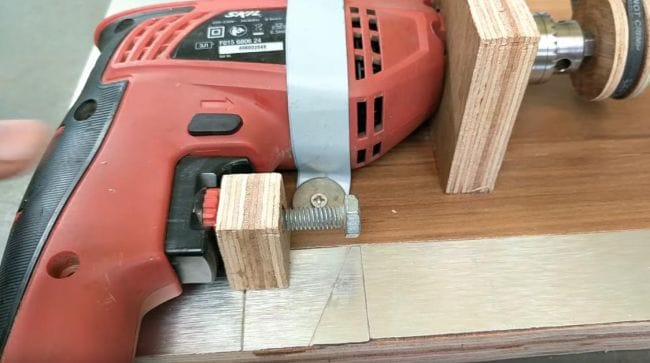
Теперь устанавливаем абразивные круги. Для этого вставляем в круг направляющие пластиковые шайбы и одеваем его на ось, фиксируем гайкой.
Тоже самое проделываем с другой стороной..
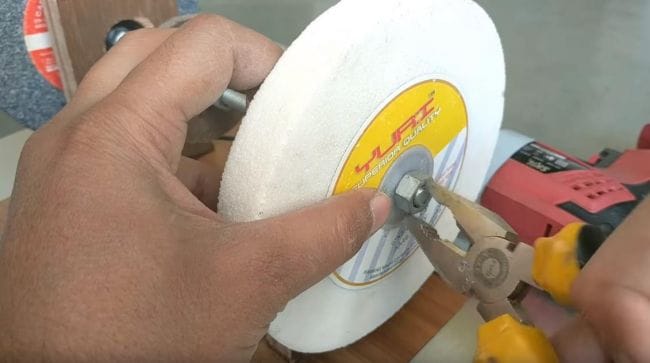
На против рабочей области делаем не сквозные отверстия и вставляем туда шпильки необходимой длины.
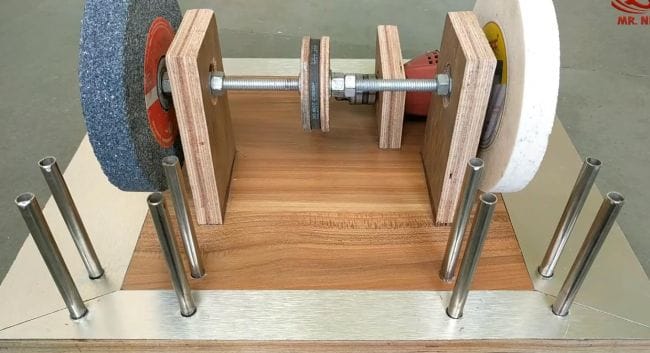
Затем вырезаем подставку из фанеры примерно такую, как на фото ниже. После чего делаем в ней так же не сквозные отверстия и надеваем на шпильки.
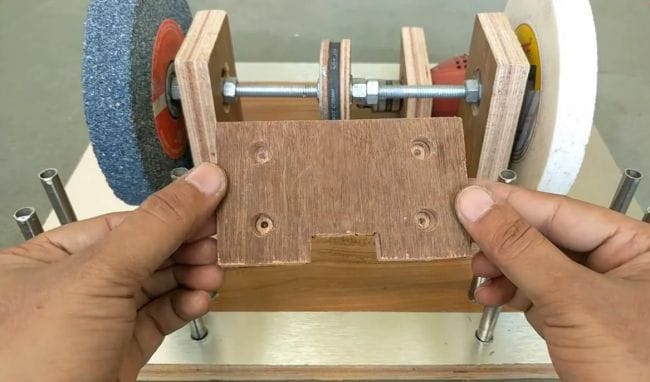
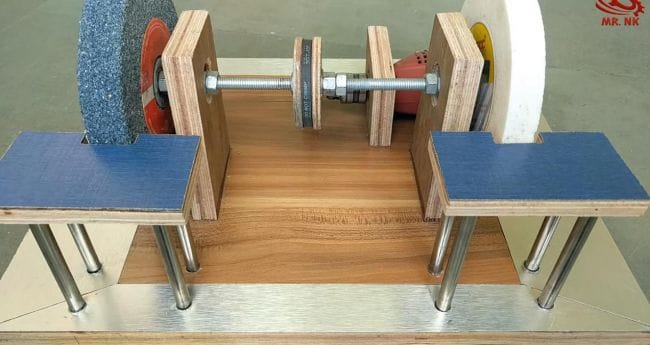
Отверстия нежно в подставке и на основании нужно делать по заранее подготовленному лекалу, что бы отверстия совпадали.
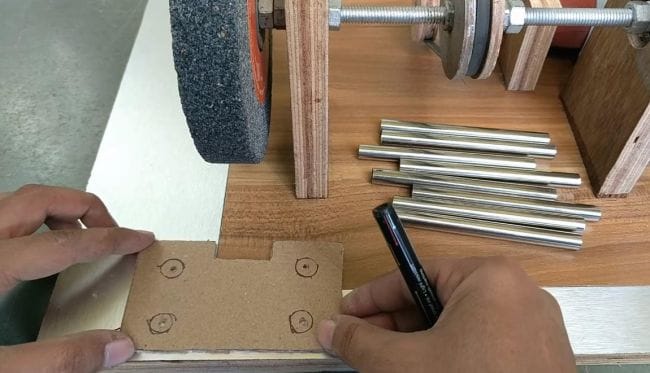
Затем делаем из тонкой фанеры защитный кожух. Делается он очень просто, вырезаются два полукруга немного больше что диаметр абразива и длиная полоска из листового алюминия или жести, всё это соединяется вместе и получается кожух. Крепим его как на фото ниже и проводим покрасочные работы для придания эстетического вида.
В Принципе станок готов к использованию.
Получился вполне функциональный станок, с двумя абразивами и регулировкой оборотов. Стоимость такого станка не высокая, учитывая что все детали корпуса можно найти у себя в запасах, включаю старую дрель и абразивы.
Всем спасибо за внимание, пока!
Видео самоделки:
Источник
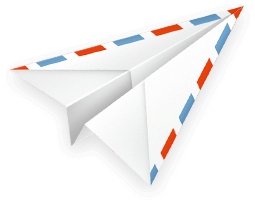
Получайте на почту подборку новых самоделок. Никакого спама, только полезные идеи!
*Заполняя форму вы соглашаетесь на обработку персональных данных
Становитесь автором сайта, публикуйте собственные статьи, описания самоделок с оплатой за текст. Подробнее здесь.usamodelkina.ru
Поделки из фанеры лобзиком (Рисунки для выпиливания)
Выпиливание лобзиком – занятие весьма увлекательное, особенно если в результате трудов должна получиться первоклассная поделка. Всегда приятно любоваться плодами ручных работ, потребовавших много времени и сил для своего появления на свет. В данной статье мы собрали самые интересные эскизы для выпиливания лобзиком из фанеры и дерева. Созданные при помощи данных шаблонов модели и узоры, станут отличным подарком дорогому человеку и чудесным элементом дизайна интерьера.
Сборные поделки
Всегда приятно оживить интерьер своего дома, оригинальным изделием ручной работы, сделанным, ко всему прочему, своими руками. Помимо сладкого чувства гордости за свои старания, процесс выпиливания имеет множество положительных сторон, к которым относиться развитие моторики рук, релаксация и повышение концентрации внимания. Благо существует огромное множество вариантов изделий, что можно сделать лобзиком: от банальных разделочных досок, до царских шкатулок с фантастической резьбой.Чтобы занятие не обременяло и приносило только положительные эмоции, необходимо, чтобы создаваемая поделка не просто нравилась Вам своим внешним видом, но и соответствовала Вашему мастерству выпиливания лобзиком. Мало приятного, когда сложная детализированная модель идет вкривь на сложном узоре, после долгих часов усердной работы.
Эскизы, представленные в данной статье, разгруппированы на сложные и простые, чтобы Вы наслаждались процессом и просто, выпиливали лобзиком забавные поделки. Распечатать чертежи большинства моделей можно в формате А4, после чего перенести контур на обрабатываемый материал.
Простые
Представленные ниже поделки не отличаются большой сложностью изготовления, но не рекомендуются тем, кто впервые взял в руки лобзик. Тонкие детали, встречающиеся в данных моделях, могут стать камнем преткновения любого новичка. Чтобы немного отточить свои навыки, рекомендуем заглянуть на специальную страницу, где представлены отличные рисунки для выпиливания лобзиком для начинающих.Поделки, имеют достаточно простой узор и вполне могут быть повторены человеком с минимальным опытом выпиливания, и парой-тройкой завершенных работ за плечами. Конечно, каждый учиться по-разному, освоить что-либо у одного, может получиться в разы быстрее чем у другого. Здесь каждый должен ответить для себя, хватит ли у него опыта сделать выбранное изделие с надлежащим качеством или стоит потренироваться на более простых контурах.
Пересмотрев сотни всевозможных эскизов, мы собрали десяток самых интересных, и вы попали по адресу, если серьезно намерены изготовить поделки из фанеры лобзиком своими руками. Легкие чертежи, помогут Вам создать красивые изделия для украшения дома, на радость себе и близким.
Вешалка
Ваза
Автор: Людмила Пелымская
Новогодняя елка


Письменный набор


Автор: Людмила Пелымская
Ключницы
Простая и оригинальная ключница из фанеры лобзиком, в форме таксы и пазла, создаст уют и оживит дизайн Вашей прихожей.

Салфетница
Салфетница №2


Собака (Пазл)
Шкатулка


Разделочная доска


Шкатулка (Дракон)
Сложные
Создание настоящих произведений искусства требует большого опыта и терпения. Именно этими качествами, в большей степени, должен обладать умелец, решивший выпилить следующие изделия лобзиком.Главным отличием следующих поделок от приведенных выше, является большее количество деталей и их высокая детализация. Если чувствуете, что Ваша техника выпиливания ручным лобзиком недостаточно отточена, лучшим вариантом будет практика на более простых моделях. Конечно, можно набить руку и при работе со сложными шаблонами, но в том случае если Вас не смущает большой процент неудач и порчи материала.
Бабочка


Ваза
Автор: Людмила Пелымская
Благородный олень
Лев

Трицератопс


Пегас


Губка Боб
Собака
Трофейная голова оленя


Мотоцикл с коляской
Паровоз

Родстер MG TC
Детализированная машинка из фанеры, выпиленная лобзиком, станет классным элементом интерьера и прекрасным подарком автолюбителям всех возрастов.
Узоры
Хорошая поделка из фанеры не обязательно должна быть объемной или иметь практическое применение. В некоторых случаях достаточно аккуратно-выпиленного красивого ажурного рисунка. Такую работу, покрытую морилкой и парой слоев лака, можно легко повесить на стену или использовать в качестве подставки под небольшие декоративные предметы.Представленные картинки для вырезания лобзиком по фанере могут использоваться как самостоятельные изделия, или в качестве детали для Вашей личной сборной поделки. Все зависит от фантазии.
Сохраните эту страницу в своей соц. сети и вернитесь к ней в удобное время.instrumentoria.ru
Струбцина из фанеры своими руками
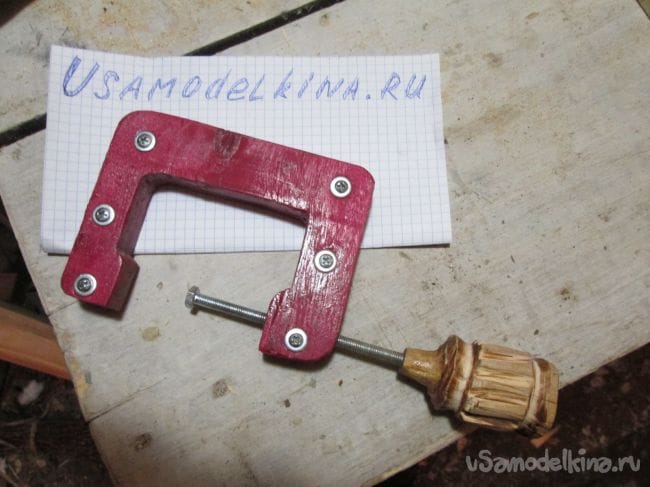
Всем привет любителям самоделок и тем, кто случайно сюда попал. Как то раз понадобилось склеить фанеру в домашних условиях, но под рукой никакого груза не было, чтобы все это зафиксировать на пару часов для склеивания. Недолго думая, я решил, что справиться с данной задачей мне поможет струбцина. Но вот незадача, ее тоже нет. Именно это меня натолкнуло на то, чтобы сделать струбцину своими руками, что поможет сэкономить время, деньги и набраться опыта с столярных изобретениях, что лишним никогда не будет.
Для того, чтобы сделать самодельную струбцину из фанеры, понадобится:
* Лист фанеры
* Болт длиной 120 мм с гайкой
* Клей ПВА
* 6 саморезов с пресс-шайбой
* Электродрель или шуруповерт
* Электрический лобзик
* УШМ или в простонароде «болгарка»
* Шлифовальный наждачный диск
* Сверло 3мм и 6мм
* Баллон краски
* Деревянный брусок
* Угольник строительный
* Пила по-дереву
Вот и все, что поможет сделать струбцину своими руками, думаю ни у кого не составит труда найти все составляющие.
Ну а теперь сам процесс сборки, но перед этим я предлагаю посмотреть видео, в котором наглядно показывается изготовление данной самоделки.
Шаг первый.
Первым делом необходимо найти лист фанеры, толщина которого будет составлять 8 мм, тоньше применять фанеру не советую, так как жесткости в такой будет недостаточно и она просто может сломаться.
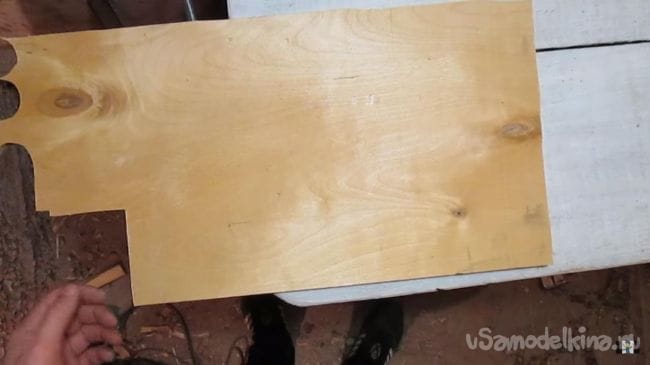
Располагаем фанеру на верстаке и отмечаем размеры будущей струбцины, а точнее ее половины, так как она будет состоять из двух частей, вырезанных из фанеры.
Высота будущей струбцины 130 мм, а ширина 100 мм, также стоит уделить внимание толщине губок, как верхней, так и нижней. Нижняя губка имеет толщину 30 мм, так как в нее будет потом вмонтирована гайка и здесь будет большая нагрузка, а верхняя толщиной 20 мм, что вполне будет достаточно.
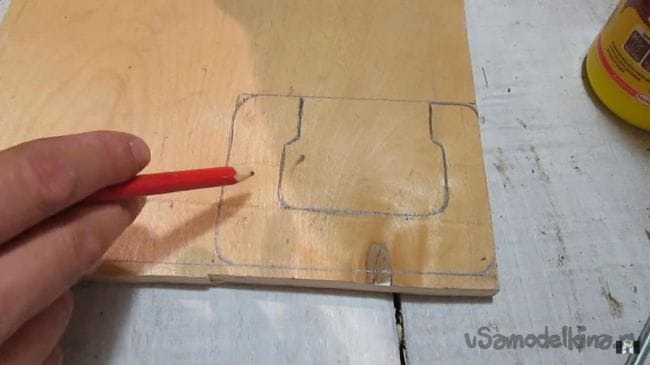
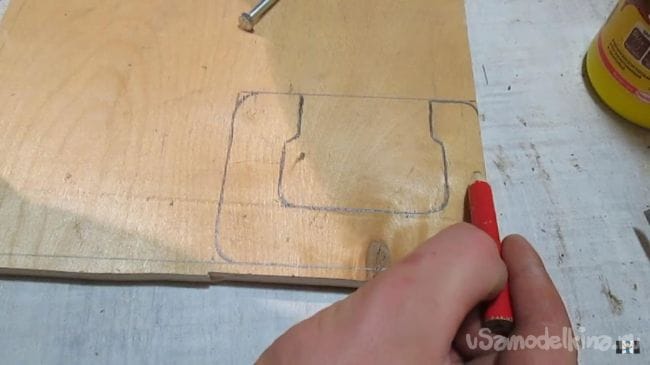
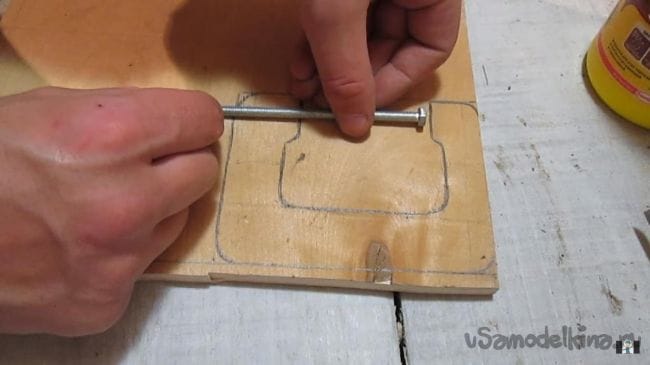
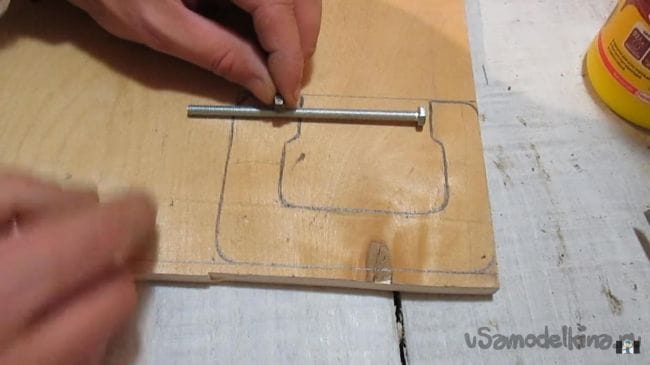
После нанесения эскиза можно выпиливать две одинаковых детали, с этой задачей хорошо справляется электролобзик с пилкой с мелким зубом, что позволяет получать аккуратный рез.
Шаг второй.
После того, как две детали, выпиленные по шаблону готовы, переходим к их обработке. Но перед этим их необходимо скрепить саморезами, которые позволят сделать две совершенно одинаковые детали. Перед закручиванием саморезов нужно просверлить отверстия сверлом 3 мм, иначе фанера может расколоться, что нам совсем не нужно.
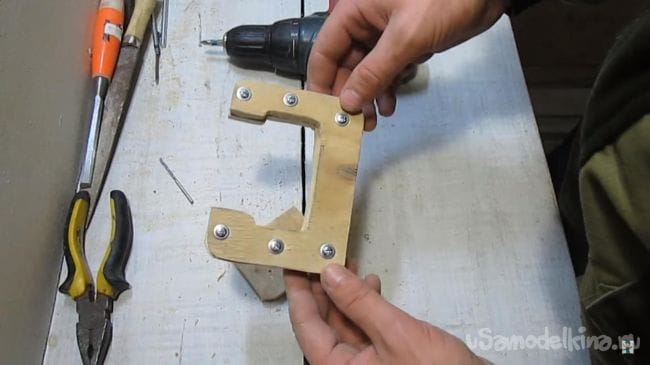
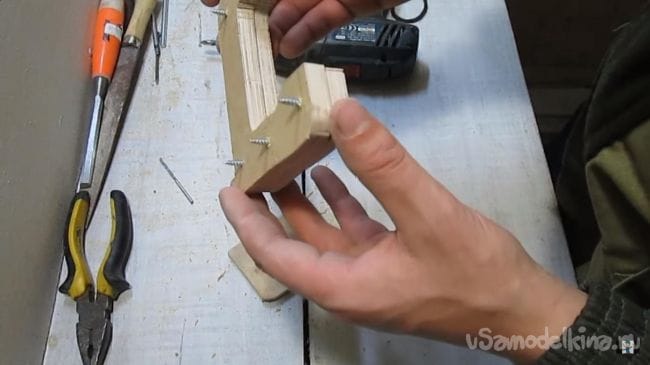
Теперь переходим в шлифовке деталей. Данный способ шлифования при помощи болгарки я не советую, так как это совсем небезопасно, если же у вас есть шлифовальная машинка или специальный станок для этих дел, то конечно же разумнее будет обработать эти две детали на них, нежели использовать УШМ.
Шаг третий.
Закончив шлифовку, переходим к подвижной части струбцины, в данном случае это болт с гайкой. Для возможности зажимать детали побольше я принял решение использовать болт длиной 120 мм. Раскручиваем саморезы и при помощи ножовки делаем небольшой пропил.
Делается это для того, чтобы при сверлении отверстия оно было строго по центру и без перекосов, по крайней мере так должно быть в теории. После того, как надпилы сделаны, можно скручивать и сверлить отверстие под болт.
Далее нужно сделать паз под гайку той же ножовкой.
Шаг четвертый.
Теперь собираем все детали в единой целое, промазываем клеем ПВА две прилегающие поверхности, равномерно размазываем и ,не забыв установить болт с гайкой, закручиваем саморезы на свои места.
Почти все готово, осталось убрать излишки клея, дождаться когда он схватиться, а чтобы попросту не терять время, сделаем ручку для струбцины. Ручку было решено сделать из того, из чего раньше Папа Карло сделал буратино, а именно полено. Отпиливаем нужный кусочек и дальше при помощи острого ножа убираем излишки, придавая деревяшке округлую форму.
После того, как деталь чуточку стала похожа на рукоять, обрабатываем ее при помощи шлифовального круга, установленного на УШМ. Также делаем насечки для предотвращения проскальзывания в руке в момент затяжки болта.
Шаг пятый.
Самоделку можно считать готовой, но вот только со стороны того, что теперь она может выполнять заложенные в нее функции, то есть зажимать детали. Но как же эстетическая составляющая, этим то сейчас и займемся. Осталось в баллончике у меня немного красной краски, обматываем изолентой резьбу болта и красим наше готовое приспособление.
Дожидаемся пока краска высохнет, а затем тестируем струбцину. Как показали тесты, самоделка полностью оправдала все мои ожидания, склеивать фанеру, используя данную самоделку удобно и быстро.
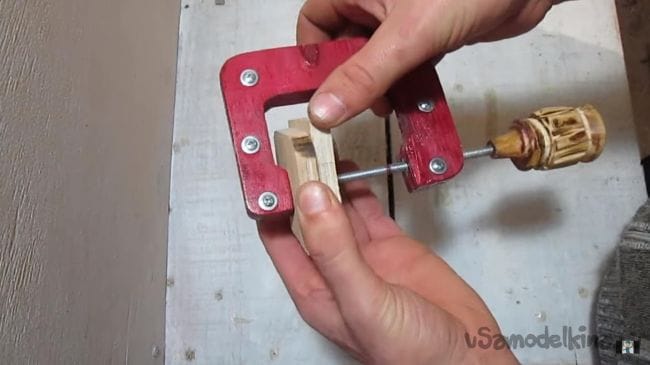

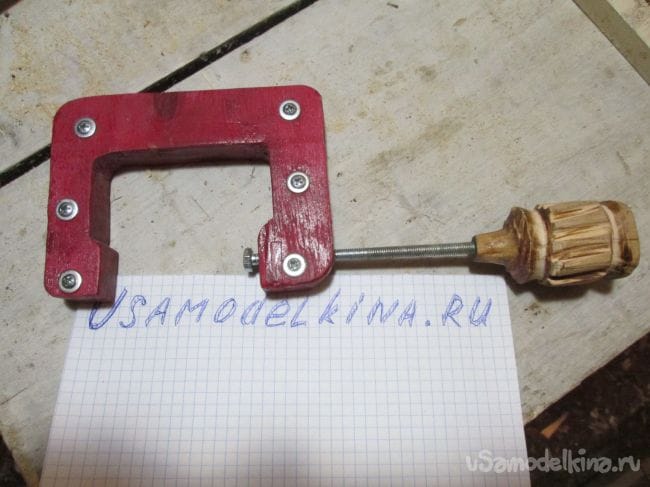
На этом у меня все, всем желаю творческих успехов и спасибо за внимание.
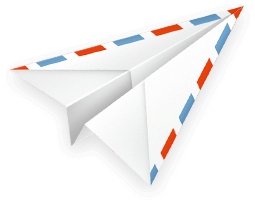
Получайте на почту подборку новых самоделок. Никакого спама, только полезные идеи!
*Заполняя форму вы соглашаетесь на обработку персональных данных
Становитесь автором сайта, публикуйте собственные статьи, описания самоделок с оплатой за текст. Подробнее здесь.usamodelkina.ru