Что лучше МДФ, ЛДСП или КДСП?
В 21 веке большим потребительским спросом пользуется мебель из ДСП. Древесно-стружечная плита — это уникальное изобретение немецкого предпринимателя Макса Химмельхебера, которое сделало жизнь обычных людей комфортной и позволило сберечь до 60% древесины, которая шла на утилизацию. Это не только забота о людях со средним достатком, но и образцовый пример бережного отношения к природным ресурсам.
Мебельные фабрики уже давно изготавливают корпусную, мягкую и кухонную мебель из ЛДСП, КДСП и МДФ. Эти материалы по некоторым характеристикам имеют схожие с натуральной древесиной свойства, а по некоторым параметрам даже превосходят ее.
Мебель из ЛДСП
ЛДСП — это ламинированная ДСП. При помощи ламинации ДСП улучшает свои свойства: становится более прочным и водостойким, что не скажешь об обычном ДСП.
Мебель из КДСП
КДСП — это кашированное ДСП. Разница между ЛДСП и КДСП состоит лишь в технологии нанесения декоративного покрытия: при кашировании оно приклеивается на ДСП, а при ламинировании — создается во время прессования за счет химических процессов и неотделимо от плиты-основы. Эксплатуационные свойства и характеристики одинаковые, но
Мебель из МДФ
МДФ — это мелкодисперсная фракция дерева. Структура МДФ однороднее, а прочность вдвое выше, чем у ЛДСП. И он лучше себя ведет во влажной среде, устойчивее к возгоранию. Но по стоимости дороже, чем ЛДСП.
Плюсы и минусы мебели из ЛДСП и мебели из МДФ
ЛДСП и МДФ — современные материалы, которые имеют как свои плюсы, так и свои минусы. Рассмотрим эксплуатационные свойства по основным параметрам — влагоустойчивость, безопасность, прочность, эстетичность, стоимость.
Влагоустойчивость
Структура ЛДСП больше подвержена проникновению влаги, чем МДФ. Почему так происходит? Из-за плотности плит, но это вовсе не означает, что МДФ совсем не боиться влаги.
Безопасность
ЛДСП более токсична, чем МДФ. Концентрация формальдегидов (Е 240) в ДСП выше, но в МДФ формальдегиды также присутствуют. Допустимым и безопасным материалом для изготовления мебели служат плиты, соответствующие ГОСТ 10632-2014. При выборе мебели для дома учтите, что российский ГОСТ предъявляет намного выше требований, нежели европейский. А значит
Прочность
У МДФ выше плотность в 2 раза, чем у ЛДСП. МДФ можно фрезеровать, делать наклонные отверстия. Материал лучше «держит» крепежные элементы.
Эстетичность
Цветовые решения как у МДФ, так и у ЛДСП стоят на одной нише — возможен любой цвет, по желанию клиента. А что касается изгибов и форм, то только из МДФ можно изготовить гнутые фасады.
Стоимость
МДФ заметно дороже, что обусловлено качественными параметрами материала. Однако, если судить по сроку службы, то МДФ служит дольше ЛДСП.
25.10.2017г.
mebel-eu.ru
Кашированная ДСП — www.mebeldok.com
Многие производители мебели используют в качестве основного материала кашированную древесностружечную плиту. Как правило, такие изделия имеют низкую стоимость и обладают привлекательным внешним видом. Но всё ли так хорошо? Давайте ознакомимся с технологией каширования, а также поговорим о достоинствах и недостатках ДСП, обработанной этим методом.
Что такое каширование?
Каширование – это процесс покрытия облицовочной поверхности, с нанесенным на нее заранее клеем, рулонным материалом в виде цельного полотна. Сначала полотно прикатывается вальцами, благодаря чему клей оставляют затвердевать. Это может происходить в емкости с грузом сверху, в холодном пакетном прессе или в обогреваемом короткотактном прессе. Последний способ затвердевания клея называется методом «Quickstep». Процесс каширования происходит при давлении 5-7 МПа и температурном диапазоне 20-150°С.
Виды каширования:
- горячее (термокаширование),
- холодное,
- с использованием плоских прессов,
Процесс получения кашированной ДСП
Кашированной ДСП называют плиту, на которую нанесен клеевой состав и бумажно-смоляная пленка. Она встречается с отделкой лаком и без нее. Пленки на основе бумаг, используемые для отделки древесностружечной плиты, пропитаны смолами с пластификаторами (акриловыми эмульсиями). Такая пропитка дает возможность готовую плёнку смотать в рулон, что очень удобно при транспортировке. Кашированная ДСП иногда облицовывается пленкой с нанесенным на нее лаком, который выдерживает температуру затвердевания клея.
Способ облицовки плиты для потребителя не должен иметь значения, главное, чтобы она была сделана качественно. Каширование и ламинирование ДСП принципиально отличаются между собой тем, что в первом случае декоративное покрытие приклеивается к плите в последний момент, а при ламинировании – создается в момент прессования посредством протекающих химических процессов, и оно неотделимо от основы.
Достоинства и недостатки кашированной ДСП
Плита с такой поверхностью имеет ряд преимуществ перед аналогами:
- дешевизна,
- простота изготовления,
- привлекательный внешний вид.
Недостатки этой древесностружечной плиты:
- низкие эксплуатационные качества,
- короткий срок службы,
- низкая износостойкость,
- потеря первоначального внешнего вида через 1 — 2 года,
Как видите, кашированная ДСП имеет массу плюсов и минусов. Если ее применять во временных мебельных конструкциях, где неважна долговечность, то это отличный материал. Но следует помнить, что за такой плитой проблематично ухаживать – ее нельзя протирать мокрой тряпкой и прилагать большие усилия, подойдет лишь сухая уборка. Но выглядит первые годы плита, обработанная методом каширования, не хуже, чем ламинированная ДСП.
www.mebeldok.com
что это и как сделать самому
Каширование плит ДСП, ДВП и МДФ, цена – Дизайн-Колор – МДФ, ДСП, ЛДСП, ПВХ
Каширование — облицовывание пластей рулонными пленочными материалами с использованием вальцовых прессов и последующим отверждением клеевого слоя различными способами. На облицовываемую поверхность наносится клей, а затем прикатывается вальцами облицовочный материал, который непрерывно разматывается из рулона. После прикатывания клей может отверждаться различными способами: просто в стопе с верхним нагружением, в прессе и т.д. При использовании на линии каширования отвердителя приклеивание пленки достигается сразу после её прикатывания горячими валами. В общем случае каширование предусматривает следующие операции:
КАШИРОВАНИЕ ПЛИТ ДСП, ДВП и МДФ
- очистка кромок и пластей детали от пыли;
- нанесение клея на пласти детали;
- удаление влаги из клеевого слоя;
- размотка пленки из рулона и ее накатывание на пласти деталей;
- разделение (разрубание) непрерывного полотна пленки в разрывах между деталями;
- повторное прикатывание пленки;
- отверждение клеевого слоя.
С учетом того, что российским потребителям более доступны отечественные источники информации, мы постараемся придерживаться существующего принципа разделения, однако на примерах западноевропейского оборудования покажем и некоторые отступления от этой условной классификации.В отечественных источниках информации указывается, что «теплое каширование предусматривает промежуточный нагрев клеевого слоя для удаления из него влаги с целью снижения времени последующего отверждения клея и снижения разбухания верхнего слоя плиты из-за впитывания».
Хотелось бы уточнить, что в немецких источниках информации нет разделения на «теплое» и «горячее» каширование. При описании кашировального оборудования немецких фирм речь идет либо о холодном кашировании, либо о так называемом термокашировании, при котором производится предварительный нагрев самих плит перед нанесением на них клея с помощью инфракрасных излучателей (оборудование фирм «Бюркле», «Фриц») либо с помощью каландров («Хюммен»), а прикатывание пленки производится нагреваемыми валами (масляный нагрев или электронагрев).
Перед станком для нанесения клея могут дополнительно устанавливаться нагреваемые до 160-180 гр. C валы (в немецкой литературе – каландры). Они вдавливают в плиту мелкие частицы, не удаленные щеточным станком, «припаивают» частично отслоившиеся стружки ДСП за счет расплавления лигнина, выравнивают температуру на поверхности и нагревают пласти для ускорения выпаривания влаги.
Традиционно считается, что при кашировании невозможно придать поверхности плиты структурный рисунок (имитация древесных пор, апельсиновой корки и др.), что кашированная плита может быть только гладкой. Однако немецкое оборудование современных линий каширования позволяет получать на выходе текстурный рисунок. Лидирующие позиции на европейском рынке оборудования для каширования занимают немецкие фирмы «Бюркле», «Фриц» и «Хюммен».
Установки холодного и горячего каширования, производимые фирмой «Бюркле», обеспечивают высочайшее качество отделки.Фирма выпускает 3 основных типа линий каширования:
- линии холодного каширования EFA
- линии термокаширования FFA II для полноформатных плит
- линии термокаширования дверей EFA T
Фирма «Фриц» специализируется на линиях термокаширования с предварительным нагревом пластей перед нанесением клея и прикатыванием пленки вальцами с внешним электронагревом.
При кашировании с использованием клеев-расплавов EVA производится также подогрев облицовочного материала, улучшающий адгезию и позволяющий повысить производительность.
В основу классификации линий каширования «Фриц» положен тип используемого клея. Соответственно выпускают 4 основных вида линий каширования:
- для дисперсионных клеев
- для мочевинно-формальдегидных клеев
- для клеев-расплавов EVA
- для полиуретановых клеев-расплавов
Фирма «Хюммен» специализируется на линиях каширования, работающих с мочевинно-формальдегидным клеем. В 70-е годы фирма «Хюммен» в сотрудничестве с фирмами-производителями клеев и мебели приступила к разработке технологии каширования с использованием мочевинно-формальдегидной смолы. Принципиально новым здесь было то, что клей представлял собой двухкомпонентную систему из химически реагирующей смолы и отвердителя, нанесение которых производится раздельно. Мочевинно-формальдегидные смолы значительно дешевле традиционно использовавшихся клеев ПВА и обеспечивают более высокое качество поверхности. Первая установка каширования с использованием мочевинно-формальдегидного клея была выпущена фирмой «Хюммен» в 1978 г.
На сегодняшний день каширование с использованием мочевинного клея является высокоэффективным способом облицовывания с годовой производительностью несколько млн. кв.м ДСП с одной установки. Фирма «Хюммен» поставляет сегодня установки с рабочей шириной от 1300 мм до 2600 мм для изготовления плит и для мебельной промышленности. Кроме того, фирмой проектируются и производятся кашировальные установки для производства стройматериалов, бумаги и пластика, а также для текстильной промышленности. На установках фирмы «Хюммен» наряду с мочевинно-формальдегидным клеем используются также клеи ПВА и различные клеи-рас
sitytreid.ru
Кашированная ДСП — Мебельная фабрика «БОЛИВАР»
Многие производители мебели используют в качестве основного материала кашированную древесностружечную плиту. Как правило, такие изделия имеют низкую стоимость и обладают привлекательным внешним видом. Но всё ли так хорошо? Давайте ознакомимся с технологией каширования, а также поговорим о достоинствах и недостатках ДСП, обработанной этим методом.
Что такое каширование?
Каширование – это процесс покрытия облицовочной поверхности, с нанесенным на нее заранее клеем, рулонным материалом в виде цельного полотна. Сначала полотно прикатывается вальцами, благодаря чему клей оставляют затвердевать. Это может происходить в емкости с грузом сверху, в холодном пакетном прессе или в обогреваемом короткотактном прессе. Последний способ затвердевания клея называется методом «Quickstep». Процесс каширования происходит при давлении 5-7 МПа и температурном диапазоне 20-150°С.
Виды каширования:
- горячее (термокаширование),
- холодное,
- с использованием плоских прессов,
- с использованием вальцовых прессов.
Процесс получения кашированной ДСП
Кашированной ДСП называют плиту, на которую нанесен клеевой состав и бумажно-смоляная пленка. Она встречается с отделкой лаком и без нее. Пленки на основе бумаг, используемые для отделки древесностружечной плиты, пропитаны смолами с пластификаторами (акриловыми эмульсиями). Такая пропитка дает возможность готовую плёнку смотать в рулон, что очень удобно при транспортировке. Кашированная ДСП иногда облицовывается пленкой с нанесенным на нее лаком, который выдерживает температуру затвердевания клея.
Способ облицовки плиты для потребителя не должен иметь значения, главное, чтобы она была сделана качественно. Каширование и ламинирование ДСП принципиально отличаются между собой тем, что в первом случае декоративное покрытие приклеивается к плите в последний момент, а при ламинировании – создается в момент прессования посредством протекающих химических процессов, и оно неотделимо от основы.
Достоинства и недостатки кашированной ДСП
Плита с такой поверхностью имеет ряд преимуществ перед аналогами:
- дешевизна,
- простота изготовления,
- привлекательный внешний вид.
Недостатки этой древесностружечной плиты:
- низкие эксплуатационные качества,
- короткий срок службы,
- низкая износостойкость,
- потеря первоначального внешнего вида через 1 — 2 года,
- проблематична в уходе.
Как видите, кашированная ДСП имеет массу плюсов и минусов. Если ее применять во временных мебельных конструкциях, где неважна долговечность, то это отличный материал. Но следует помнить, что за такой плитой проблематично ухаживать – ее нельзя протирать мокрой тряпкой и прилагать большие усилия, подойдет лишь сухая уборка. Но выглядит первые годы плита, обработанная методом каширования, не хуже, чем ламинированная ДСП.
xn--44-6kcdf9auxw.xn--p1ai
Ламинирование и каширование дсп. технология лдсп
Ламинированная ДСП
Ламинированная древесно-стружечная плита (ЛДСП) является одним из самых популярных материалов для изготовления мебели и стеновых панелей. Технология производства и себестоимость материала невысоки, а разнообразие расцветок и фактуры велико. Это и обусловило её популярность и широту применения.
История изобретения
Ламинированная ДСП была изобретена во второй половине девятнадцатого века, в далёком 1887 году. Автором новинки считается американский предприниматель Эрнст Хаббард. Он первым догадался смешать отходы деревообрабатывающего производства – стружки и опилки – с казеиновым клеем и отформовать полученную смесь в геометрически безупречные плиты. Первые ДСП были ламинированы шпоном дерева дорогих поделочных пород, и оказались доступными далеко не каждому потребителю. Первыми покупателями изделий из ламинированной ДСП были весьма состоятельные люди.
Но постепенно технология её производства становилась совершенней и дешевле. В 1926 году немец Фройденберг рассчитал оптимальное соотношение между составными частями ДСП – связующим материалом с одной стороны и стружками и опилками – с другой. Согласно этим расчетам, связующего материала должно быть от 3 до 10 процентов – в зависимости от класса ДСП. Позже эти расчеты были откорректированы и уточнены. По современной технологии связующим материалам отводится 6-8 процентов объёма ДСП.
Технология производства: изготовление ДСП
Главный материал для наполнения древесно-стружечных плит – стружка и опилки – берётся не только из отходов деревообрабатывающего производства, но и производится из низкосортной древесины на специальных рубильных станках, измельчающих крупные куски дерева на стружку толщиной 0,2 – 0,5 мм и длиной не более 40 мм. Причём в наружные слои плит укладывается стружка наименьших размеров. Частицы, предназначенные для наружного слоя, подвергаются дополнительному размельчению в дробилках (уменьшение ширины) и мельницах (уменьшение толщины). Эта операция особенно важна при производстве ламинированной ДСП, так как при её производстве к качеству поверхности предъявляются повышенные требования.
Заготовленная сырая стружка по системе механических или пневматических транспортёров поступает в бункера-хранилища. Оттуда по мере необходимости подаётся в сушилки. Просушивание стружки для разных слоёв ДСП осуществляется в разных сушилках: для внешнего слоя на выходе достаточно содержание влаги в 4-6 процентов, а вот для внутреннего требования более жёсткие – 2-4 процента. Сушилки для стружки обычно бывают конвективными барабанного типа. После просушивания стружка просеивается на сите для отделения более мелких фракций, предназначенных для наружного слоя.
Затем стружка поступает в смеситель – агрегат для обволакивания частиц сырья связующим составом. Процент связующего для внутреннего и внешнего слоя неодинаков. Для внутреннего он составляет около 60 процентов, для внешнего – 53-55. Это одна из наиболее сложных операций при изготовлении ДСП, так как при недостатке связующего стружка плохо склеивается, а при избытке происходит перерасход материала и, как следствие, плиты получается более низкого качества.
В последнее время всё большее распространение получают смесители так называемого «факельного» типа, которые производят более качественный продукт. В таких смесителях связующий состав распыляется с помощью форсунок и направляется на взвешенные с помощью пневматики в воздухе стружку и опилки. При перемешивании связующее вещество равномерно оседает на поверхности древесных частиц. Такие смесители – техника довольно тонкая и нуждается в точной настройке, чтобы соотношение между связующим составом, стружкой и отвердителем было оптимальным. Затем полученная смесь с помощью механических присп
nkkconsult.ru
что это и как сделать самому
На сегодняшний день ДСП – один из самых экономичных материалов, применяемый при изготовлении предметов интерьера. При правильном оформлении и конструировании мебель из него выглядит как отличная имитация изделий из натуральной древесины. Но обычная плита выглядит достаточно неказисто, поэтому несколько десятилетий назад придумали способы облицовки поверхности ДСП декоративными материалами.
Технология каширования ДСП и МДФ
Одним из способов облицовки поверхности ДСП является процесс его каширования. В переводе с немецкого языка («kaschieren») обозначает «оклеивание бумагой». Данная технология подразумевает процесс нанесения и закрепления на облицовочную поверхность непрозрачной пленки методом склеивания или припрессовывания двух поверхностей (лайнера и основы). С помощью специального кашировального оборудования к основе приклеивается предварительно подготовленная бумага, картон, меламиновая пленка для облицовки или фольга. Таким образом покрывают древесностружечные плиты, MDF, оклеивают оконные профиля пленкой ПВХ, изготавливают кашированный картон в производстве полиграфической продукции.
Каширование МДФ – это процесс покрытия необработанной поверхности МДФ пленкой или облицовочной бумагой для улучшения внешнего вида внутренней стороны фасадов или столешниц. Технология каширования ДСП и МДФ не имеет различий по используемым материалам и технологическому процессу. Стоит отметить, что изделия из МДФ обладают высокими показателями экологичности и благодаря специфической технологии производства являются более прочными в отличие от изделий из ДСП.
Различие в технологиях ламинирования и каширования
Ламинирование – технологический процесс нанесения декоративного покрытия под воздействием давления и температуры. Технология ламинирования ДСП, несмотря на дороговизну, считается более надежным способом производства ЛДСП, чем изготовление по технологии каширования.
Между процессом ламинирования и каширования ДСП есть определенное различие. Заключается оно в том, что при ламинировании декоративное покрытие создается с помощью прессования химическим путем и является составляющим плиты, а в процессе каширования готовая твердая бумажно-смоляная пленка приклеивается к плите. За счет нанесения клея кашированные поверхности получаются более мягкими и несколько уступают по прочности поверхностям, изготовленным по технологии ламинирования.
Каширование ДСП (MDF) в домашних условиях
Есть два варианта имитации технологии каширования ДСП «своими руками».
- Нанесение пленки-самоклейки на поверхность плиты. Необходимо снять слой защитной бумаги с обратной стороны пленки и приклеить ее к поверхности плиты. Важно не допускать образования пузырьков воздуха под пленкой. Убрать их можно с помощью мягкой тряпки или пластикового шпателя.
- Приклеивание полимерной пленки с использованием универсального клея. Клей наносят на плиту, выдерживают небольшой промежуток времени, а после аккуратно приклеивается пленка. Для лучшего прилегания стоит придавить прессом или прокатить валиком.
Из вышеперечисленных вариантов каширования ДСП (МДФ) в домашних условиях первый вариант гораздо быстрее, второй — надежнее, так как самоклейку приходится периодически подклеивать или приобретать новую, что сказывается отрицательно на семейном бюджете. Поэтому выбор за вами.
mebelvictoria.com
как их делают, заводы и линии, ГОСТ, как сделать их своими руками при помощи пленки или альтернативных методов
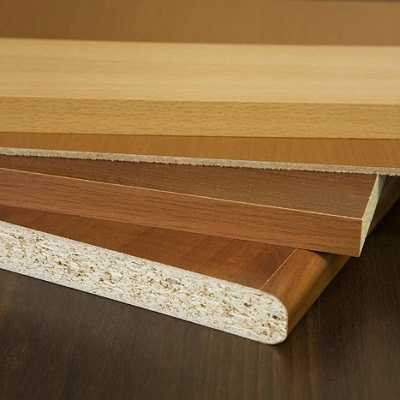
Ламинированная древесностружечная плита (ЛДСП) – это основной компонент для производства корпусной мебели, который достоверно имитирует натуральную древесину, но обходится во много раз дешевле.
Дешевизна обусловлена использованием отходов деревообработки — стружки.
Производство ЛДСП имеет несколько основных технологий.
Далее мы расскажем:
- что такое ЛДСП;
- чем производство ЛДСП отличается от производства ДСП;
- какие документы регламентируют качество ЛДСП в России;
- какое оборудование применяют для ламинирования;
- как изготавливают кромочную ленту;
- как ламинируют ДСП самостоятельно.
Что это такое?
ЛДСП – это обычная древесностружечная плита, о которой мы рассказывали тут, облицованная декоративным покрытием.
Покрытие может быть, как одноцветным и гладким, так и разноцветным или имитирующим текстуру древесины.
Основные характеристики, такие как:
- прочность на изгиб;
- способность удерживать шуруп;
- плотность;
- классы влагостойкости;
- класс эмиссии формальдегида;
- горючесть
полностью соответствуют этим же характеристикам исходного материала.
Толщина ламинированного материала зависит от его назначения. Для изготовления корпусной мебели чаще всего берут ЛДСП толщиной 16 мм, однако крышки столов часто делают из плиты толщиной 25–38 мм.
ЛДСП для облицовки стен, пола и потолка изготавливают из ДСП толщиной 8–12 мм.
Ламинирующий слой с объемным рисунком увеличивает толщину древесно-стружечной плиты, ведь такой рисунок создают с помощью прессования основного слоя, продавливая на нем контуры рисунка.
Наружная пленка лишь повторяет контуры этого рисунка.
Как делают ЛДСП?
Для изготовления ЛДСП используют обычные шлифованные древесностружечные плиты, поэтому их выпускают на заводе по производству ДСП, подключив участок ламинирования.
Причем для покрытия исходного материала ламинирующей пленкой применяют 3 технологии:
- ламинирование;
- каширование;
- гладкое ламинирование.
Ламинирование
При ламинировании на основу наклеивают 1–2 слоя специально подготовленной бумаги, причем первый слой — основу — делают максимально толстым, чтобы в нем можно было продавить рисунок.
Толщина основы, в зависимости от глубины рисунка, может достигать 0,5–1 мм, толщина второго слоя составляет десятые, а то и сотые доли мм.
Поверх этих слоев укладывают еще один, изготовленный из прозрачной бумаги и смеси различных смол, которые при нагреве превращаются в прочную пленку, надежно защищающую декоративную поверхность.
На подготовленную поверхность ДСП укладывают основной слой и придавливают его горячим штампом с подходящим рисунком.
Температура поверхности штампа составляет 150–220 градусов, благодаря чему пропитывающая основной слой смола смешивается со смолой, склеивающей стружку в ДСП и, бумага становится неотделимой частью плиты.
Затем таким же образом наклеивают декоративный слой с подходящим рисунком и наружный слой, обеспечивающий защиту плиты от повреждений.
На некоторых предприятиях все слои покрытия сначала соединяют друг с другом, затем сушат и, только после этого крепят к ДСП.
При такой технологии покрытие делают в виде ленты. Рисунок на нем формируют с помощью цилиндра с установленной матрицей, аналогично формированию рисунка при кашировани.
Разница с кашированием в том, что ленту крепят без клея, прогревая пропитывающие бумагу смолы до расплавления и смешивания со смолой в ДСП.
Каширование
При кашировании сначала подготавливают облицовочный материал, для чего все слои укладывают по порядку и пропечатывают на них рисунок с помощью холодного пресса.
При этом незастывшая смола различных слоев смешивается, благодаря чему покрытие превращается в широкую и длинную ленту.
Если для печати рисунка применяют цилиндрический штамп, то возникает возможность делать ленты любой длины.
Многие небольшие предприятия, производящие ламинат с объемной текстурой, предпочитают не тратиться на дорогостоящее оборудование, необходимое для изготовления ленты, а покупать уже готовый материал.
Готовую ленту отправляют в сушилку, затем сматывают в рулоны, которые поставляют на участок каширования. Там облицовочный материал обрезают по размеру и укладывают на смазанную специальным клеем плиту, затем придавливают прессом и прогревают до тех пор, пока клей полностью не полимеризуется.
Благодаря этой технологии облицовка проходит быстрее, ведь не приходится прогревать каждый слой покрытия отдельно, поэтому предприятие может производить больше продукции.
Минус этой технологии в том, что приклеенная облицовка держится гораздо слабей, чем настоящее ламинирование.
Гладкое ламинирование
Эта технология сходна с кашированием, однако является полноценным ламинированием, ведь при нагреве смола покрытия и плиты смешиваются, образуя единый материал. Кроме того, на участке подготовки ленты нет пресса для создания рисунка.
Для создания гладкой поверхности достаточно уложить 2 слоя, нижний из которых будет сделан из бумаги, а верхний — из специальной пленки, которая при нагреве образует прочное и прозрачное покрытие.
Благодаря тому, что крупные производители ЛДСП постоянно ищут способы увеличения технологичности производства и снижения затрат, в этот процесс постоянно вносят различные изменения, суть которых производители держат втайне. Ведь любое улучшение качества ламинирующего покрытия, равно как и снижение затрат, делает их продукцию более конкурентоспособной.
Документы, регламентирующие качество
Основной документ, регламентирующий качество и характеристики ЛДСП в России – это ГОСТ Р 52078-2003, который вы сможете найти по этой ссылке.
Существует и международный стандарт EN 14322:2004, который во многом сходен с российским. Его вы можете найти здесь.
Эти стандарты отличаются от принятых в отношении ДСП только требованиями к ламинирующему покрытию. Во всем остальном они полностью идентичны.
Кроме того, существуют различные ТУ (технические условия), которые разрабатывают как производители ламинированных древесностружечных плит, так и производители мебели. В ТУ прописывают те требования, которые не вошли в общепринятые стандарты или по каким-то причинам выбиваются из них.
К примеру, в ТУ могут быть прописаны нестандартные размеры продукции, а также указан подробный состав клея, отличающийся от того, что предприятие использует при производстве обычного ДСП.
Оборудование: завод и его составляющие
В большинстве случаев для ламинирования ДСП используется многофункциональное устройство, которое называют ламинатор. Его основа – мощный пресс с паровым или масляным нагревом плиты, а также с возможностью установки матриц с необходимым рисунком.
Ламинатор может быть большим, способным обрабатывать листы максимального размера, а также средним или маленьким. Если установлен большой пресс, то после охлаждения ламинированный лист поступает на раскроечный станок, полностью аналогичный тому, что применяют при производстве ДСП.
Кроме того, ламинатор бывает одно- или двухсторонним, то есть наклеивать пленку только с лицевой стороны или одновременно обрабатывать лицевую и заднюю плоскости.
Прессы среднего размера предназначены для ламинирования уже нарезанных плит, размер которых соответствует требованиям ГОСТ Р 52078-2003 и EN 14322:2004.
Малый пресс предназначен для ламинирования готовых деталей, например, входных и межкомнатных дверей или мебельных элементов. Поэтому предприятию следует выбирать ламинатор исходя из ассортимента продукции.
Кроме того, вместе с большим или средним ламинатором нередко используют линию по укладке ленты, которая также выполняет несколько функций:
- определяет качество подготовки поверхности ДСП к дальнейшей обработке;
- укладывает ленту на плиту и правильно ориентирует ее;
- обрезает излишки ленты.
На предприятиях, где установлены малые ламинаторы, эту операцию обычно выполняет специально подготовленный работник высокой квалификации, укладывающий и обрезающий ленту вручную. Чаще всего так поступают на мебельных фабриках, когда приходится изготавливать детали, которые по каким-то причинам нельзя вырезать из целого листа.
Похожим образом поступают и на крупных деревообрабатывающих цехах или производствах, изготавливающих не только мебель, но и различную столярную продукцию.
Ламинатор можно использовать не только для ламинирования, но и для обычного приклеивания, поэтому нет смысла тратиться на специальную линию.
Нередко среднюю и малую плиту после охлаждения подают на раскроечный станок, который отрезает 1–2 мм плиты, формируя ровную кромку. Такой станок оснащают дисковыми пилами большого диаметра с напайками из твердых сплавов или с алмазным напылением.
Перемещают плиты по всей линии с помощью ленточных транспортеров и вакуумных подъемников, причем все операции происходят в автоматическом режиме.
Стоимость оборудования зависит от многих факторов, поэтому большинство предприятий, выпускающих такие линии и отдельные станки, озвучивают цену только после предоставления заказчиком конкретных требований по конфигурации и производительности.
На Алиэкспресс и других площадках можно встретить отдельные устройства и целые линии с указанием примерной стоимости без учета доставки и монтажа.
Средний односторонний ламинатор для плит размером 1220*2440 мм можно приобрести за 100–200 тысяч долларов США, а линия подачи ламинирующей ленты шириной 60–120 см обойдется в 18–25 тысяч долларов США.
Кромочная лента
При изготовлении ЛДСП ламинируют только лицевую и обратную поверхности, а кромки остаются без покрытия. Поэтому предприятия, выпускающие ЛДСП, вместе с ней поставляют и кромочную ленту, которую используют для самостоятельного ламинирования торцов.
Цвет ленты полностью соответствует цвету плиты, поэтому после наклейки ленты вся плита становится одноцветной.
Ленту для кромления, то есть оклейки кромок, делают заметно тоньше, чем ту, что применяют при облицовке древесностружечных плит на производстве. Ведь в условиях мебельной мастерской невозможно создать настолько высокое давление и большинство мастеров обходится обычным утюгом, прогревая им уложенную на кромку ленту.
Как ламинировать ДСП самостоятельно?
Не всегда ЛДСП, которую можно приобрести в магазинах, подходит по цвету или рисунку, поэтому можно облицевать плиту самостоятельно.
Для этого хорошо подойдут различные виды декоративных пленок, которые продают в строительных магазинах.
Пленки бывают самоклеящимися и обычными.
Для нанесения самоклеящейся пленки с нее снимают тонкое защитное покрытие и укладывают на очищенный от грязи и пыли лист ДСП, затем прокатывают валиком, удаляя пузырьки воздуха.
Для нанесения обычной пленки применяют специальный клей, рекомендованный производителем пленки, затем выжидают 2–5 минут и аккуратно накладывают пленку, не допуская появления складок.
Такие способы позволяют наклеивать на ДСП лишь те рисунки, которые есть в магазине, поэтому можно использовать метод, который применяли во времена СССР, когда ЛДСП была в огромном дефиците.
На очищенную от пыли и грязи поверхность ДСП наносили тонкий слой грунтовки (ПВА, разбавленный водой в соотношении 5:1). Затем на листах альбомной бумаги делали желаемый рисунок и с обратной стороны грунтовали ПВА.
Через 2–4 дня, когда клей полностью застыл, листы с рисунком раскладывали на поверхности ДСП так, чтобы собрать рисунок воедино. Затем каждый лист прогревали с помощью утюга.
Если все листы были правильно уложены и прогреты, то после охлаждения они образовывали сплошной рисунок, полностью покрывавший всю поверхность плиты.
Однако сдвиг любого из листов приводил к нарушению рисунка и портил всю картину, поэтому для большей надежности старались достать не альбомную, а типографскую бумагу, которая превосходила плиту по размерам.
Готовый рисунок покрывали мебельным или паркетным лаком в 2–3 слоя и получали самодельный ламинат с невысокой прочностью покрытия, зато с необходимым рисунком.
Видео по теме
На этом видео можно увидеть работу завода по производству ЛДСП:
Вывод
Производство ЛДСП – это сложный процесс, включающий в себя много операций, поэтому для превращения обычных древесностружечных плит в ламинированные необходим участок с хорошим оборудованием.
Прочитав статью, вы узнали, как происходит процесс ламинирования и можно ли его сделать самостоятельно.
Вконтакте
Google+
Одноклассники
rcycle.net