Газобетон. Особенности материала, характеристики и применение
Этот уникальный материал широко используется в домостроении. Он подходит для возведения всех типов стен, в том числе и несущих. Отличные звукоизоляционные свойства, пожаробезопасность, морозостойкость и легкий вес позволяют применять его при строительстве промышленных баз, животноводческих ферм, жилых домов. Газобетонные блоки не подвержены гниению по сравнению с древесиной. Кладка осуществляется намного быстрее, чем из кирпича, при этом и цена газобетона существенно ниже. В статье рассмотрим основные характеристики газобетона и этапы строительства из него.
Содержание:
- Технология производства газобетона
- Свойства газобетонных блоков
- Размеры блоков газобетона
- Инструмент для обработки газобетонных блоков
- Качественные критерии материала
- Строительство дома из газобетона
Технология производства газобетона
Ячеистая структура составляет почти 85% объема всего блока, поэтому данный материал отличается весьма легким весом.
В металлических емкостях или формах протекают основные химические реакции. Смесь подвергается вибрации, способствующей схватыванию. После затвердения, все неровности с поверхности снимаются стальной струной. Пласт разделяется на блоки, и затем они отправляются в автоклавную установку. Конечная калибровка готовых блоков осуществляется фрезерной машиной.
Прежде чем купить газобетон, надо поинтересоваться с применением какой обработки он был произведен.
- Автоклавная обработка. Данный этап значительно улучшает технические характеристики газобетона. Здесь в течение 12 часов при высоком давлении проводится обработка паром, температура которого составляет почти 200°С.
Такой процесс нагрева делает текстуру более однородной, тем самым улучшая прочностные свойства (не менее 28 кгс/м²). Его удельная теплопроводность составляет 0,09-0,18 Вт (м∙К), что позволяет возводить стены в один ряд (400 см) практически в любых климатических условиях, но исключая северные районы.
- Неавтоклавная технология заключается в естественном затвердении смеси. В этом случае его вполне можно произвести своими руками, так как здесь не требуется специального оборудования. Прочность блоков при таком производстве не превышает 12 кгс/м².
Свойства газобетонных блоков
- Легкость. Блок D500 размерами 30х25х60 см весит около 30 кг, для кладки того же объема потребуется 22 кирпича, вес которых в два раза больше ≈ 80 кг.
- Теплопроводность. Ячеистая структура создает теплоизоляционный эффект. Также данный материал способен сохранять тепло, а в летний сезон – приятную прохладу.
Здесь следует отметить, что теплопроводность блока толщиной 375 мм равнозначен кладке из кирпича более чем в полметра.
- Пожаробезопасность. Сырье, используемое в производстве, имеет минеральное происхождение, по своим свойствам – не горючее. Поэтому блоки способны выдержать воздействие открытого пламени в течение 3 часов.
- Морозоустойчивость.
- Прочность. Высокий показатель прочности на сжатие достигается путем его прохождения через автоклавную установку. Например, прочность блока D500 равна 28-40 кгс/см³. Такие параметры позволяют использовать его при возведении несущих стен строения до 5 этажей.
- Экономичность. Благодаря большим габаритам и легкому весу этапы строительства осуществляются быстрее, чем из других материалов. Такие монтажные работы может выполнить даже один человек.
Эти характеристики снижают затраты на транспортировку и расходы на устройство фундамента.
- Легкость обрабатывания. Придать ему любую форму можно при помощи ручных средств, например, ножовки или пилы. Блок легко режется, сверлится. Выполнить штробление, забить гвоздь или проделать рабочее отверстие под розетку не составит труда. Это свойство материала позволит воплотить в жизнь интересные и оригинальные проекты из газобетона любой сложности.
- Экологичность. Новые технологии дают возможность производить этот материал из сырья, не выделяющего токсичных веществ. По экологической чистоте он уступает лишь древесине, но при этом не подвержен горению, гниению, воздействию насекомых.
Размеры блоков газобетона
Газобетонные блоки бывают перегородочными и стеновыми. К первым относятся блоки толщиной от 75 до 200 мм, а ко вторым – от 250 мм и более. Перегородочные предназначаются для межкомнатных стен, внутренних ненесущих конструкций. А стеновой газобетон применяют для возведения несущих стен здания или иного сооружения.
- Блоки толщиной в 75 мм в основном используют в качестве утепления несущих черновых стен, например, из кирпича.
- С размерами 20 и 25 мм применяются для возведения стен хозяйственных или бытовых построек, не требующих особых энергосберегающих свойств (гаражи, сараи).
- Для кладки несущих стен подходят блоки, толщина которых составляет от 375 мм и выше. В этом случае для утепления постройки в определенных климатических регионах, будет достаточно только выполнить штукатурные работы на внешних стенах.
Также важно знать:
- Газобетонные блоки производятся с плотностью 350, 400, 450, 500, 600, 700, маркируются буквой D.
- Длина может составлять 600 и 625 мм.
- Ширина – 75, 100, 150, 200, 250, 300, 350, 375, 400, 500 мм.
- Высота – 200, 250 мм.
- Плотность на сжатие – от 1,0 до 7,5 мПа.
- Морозостойкость находится в диапазоне от 15 до 50.
- Усадка при высыхании не превышает 0,5 мм/м, данный параметр соответствует всем размерам блоков.
Инструмент для обработки газобетонных блоков
Этот пористый материал имеет низкую плотность, поэтому его легко обрабатывать. И благодаря правильной геометрической форме кладка блоков производится без каких-либо затруднений. Не прикладывая больших усилий, газобетон позволяет выполнить штробление под коммуникации и воплотить самые сложные архитектурные замыслы.
Блокам можно придать любой наклон, скос. Для строительства небольших бытовок, хозяйственных построек используется обычная ножовка с лезвием по металлу или ручная пила. Такой инструмент идеально подходит для малых объемов, где необходимо только подкорректировать блоки для оконных и дверных проемов, угловые места.
Улучшить качество работ можно, применяя дополнительные приспособления:
- металлический уголок;
- линейка и карандаш;
- рубанок для плинтовки поверхностей стен.
Совет: цепные пилы не подходят для тонких и точных работ, потому что рез получается широкий и не очень аккуратный, соответственно кромки начинают крошиться.
- Также для работ применяется и электрическая сабельная пила. Разрезы получаются тоньше и точнее, по сравнению с цепным аналогом. Ею осуществляется подгон блоков по размерам, канавки, пазы, штробы под прокладку коммуникаций. Она может использоваться и как ручная пила непосредственно на месте.
- Ленточная пила применяется при проведении крупного строительства. Отличительные свойства этого инструмента – высокий показатель эффективности и ровные срезы.
- Резцы – ручной инструмент, которым идеально выполняется штробление канавок под прокладываемые электрические сети, трубы и другие коммуникации.
Качественные критерии материала
Этот материал хорошо зарекомендовал себя в области строительства.
Основные критерии, их плюсы и минусы:
- Усадка после строительства. Плюс — такой параметр равен примерно 0,2-0,5% и он практически незаметен, к примеру, усадка деревянного дома составляет почти 15%. Минусов нет.
- Эстетичность. Плюс — благодаря ровным стенам, отделка производится легко и быстро. Минус — без данных работ не обойтись, так как газобетонные блоки в кладке выглядят весьма некрасиво.
- Экологичность. Плюс — он состоит из песка, портландцемента, золы и малой доли алюминия. Минус — во многих европейских странах запрещают возводить жилые дома из газобетона из-за алюминиевой пудры.
- Пожаробезопасность.
Плюс — в составе отсутствуют горючие материалы, поэтому газобетон отличается повышенной стойкостью даже к отрытому пламени. Минусов нет.
- Срок службы. Плюс — крепкая структура не подвержена гниению и плесневению. Блок способен выдержать большое количество циклов заморозки/оттаивания. Минус — под воздействием постоянных неблагоприятных условий, например, влаги и сырости, теряет свои прочностные характеристики и начинает крошиться.
- Кладка блоков. Плюс — геометрически правильная форма и размеры блока позволяет осуществлять кладку очень быстро. Он легко обрабатывается – его можно разрезать обычной пилой, придавая любую конфигурацию. Минусов нет.
- Теплоизоляция. Плюс — кладка в два ряда обеспечит средние показания теплоизоляции. Минус — максимальный коэффициент этого параметра равен 0,12 Вт/м, поэтому строение нуждается в дополнительном утеплении.
- Экономичность. Плюс — низкая цена на блоки, дает возможность считать газобетон весьма доступным материалом для строительства.
Минус — затраты на более прочный фундамент, конечная отделка поверхности, утепление стен «съедают» сэкономленные финансы.
Строительство дома из газобетона
Расчет материала
Любые строительные работы начинаются с расчета материала. Продажа газобетонных блоков осуществляется в кубометрах, поэтому вычисления проводятся следующим образом.
Например, планируется возведение дома с размерами: 16х12 м и высотой 3 м. Сначала вычисляется площадь всех стен:
- (16+16+12+12)ˣ3=168 м² или
- 16ˣ2ˣ3+12ˣ2ˣ3=168 м².
Далее полученный результат умножается на толщину блока 0,3:
- 168ˣ0,3=50,4 м³ — данное количество блоков необходимо для возведения стен. Таким же образом вычисляются межкомнатные перегородки.
Фундамент
Более надежными основаниями для газобетона считаются:
- ленточный монолитный фундамент;
- незаглубленный фундамент из монолитной плиты;
- столбчатый фундамент.
Выбор осуществляется в зависимости от параметров грунта и от проекта самого дома. Но в любом случае необходима гидроизоляция и если запланирован подвал или цокольное помещение, то нужно предусмотреть и утепление стен.
Цоколь строящегося здания рекомендуется выполнить из кирпича, кубатура которого рассчитывается таким же методом, как и для блоков.
Клей для газобетона
- Минимальные отклонения размеров блоков (±1 мм) позволяют осуществлять кладку специальным клеевым раствором. Клей наносится толщиной не более 3 мм, поэтому теплопотери минимальны. Ведь потеря тепла происходит не только через поверхность материала, но и через кладочный шов.
- Тонкий слой клея повышает термическое сопротивление строения на 20-25%, по сравнению с песко-цементным раствором. К тому же, несмотря на высокую стоимость, тонкошовная кладка значительно сокращает расход этого материала. Использование клеевого раствора обеспечит чистоту на рабочем участке, придавая эстетичный вид строящемуся дому, зданию.
- Порошкообразная смесь состоит из кварцевого песка, портландцемента, минеральных и полимерных добавок. Его необходимо лишь затворить чистой водой (около 30°) и размешать – клеевой раствор готов к применению. Соотношение жидкости и порошка указывается на упаковке с клеем. Помните, увеличение воды снижает прочностные характеристики раствора.
- Перед применением клей тщательно перемешивается. Для его нанесения используется зубчатый шпатель. Корректировка положения блока может быть произведена в течение 10-15 минут. В затворенном виде раствор рекомендуется использовать в течение нескольких часов.
Технология укладки газобетонных блоков
Для работ потребуется: зубчатый шпатель, рубанок, ручная пила, клей, уровень, щетка и сами блоки.
- На блок наносится клеевой раствор и ровно выкладывается на подготовленную поверхность. При необходимости рубанком выравнивается блок, щеткой удаляются мелкие частицы и другие загрязнения.
Излишки раствора аккуратно убираются, но не затираются в швы.
- Обязательно проверяется каждый блок на вертикаль и горизонталь уровнем. Помните, разобрать кладку для корректировки невозможно, ее можно лишь сломать или разбить. Очень важно ровно выложить первый ряд, для этих целей желательно воспользоваться и песчано-цементным раствором, тем самым компенсируя все неровности.
- Работа начинается с угла, для точности кладки используется натянутая нить, в качестве маяков выступают промежуточные и угловые блоки. В процессе стройки следует соблюдать перевязку швов. Смещение ряда должно быть не менее 8 см по отношению к предыдущему. Требуемый размер блоку придается с помощью обычной ножовки.
- На ночь и при дождливой погоде горизонтальная поверхность кладки укрывается пленкой. Такие манипуляции следует проводить до тех пор, пока не будет монтирована крыша. Если стройка будет «зимовать», тогда изолируется вся конструкция.
youtube.com/embed/SEo1E9OBwSA?rel=1&autoplay=0&wmode=opaque» frameborder=»0″>
Чем облицевать дом из газобетона
Работы по облицовке придадут эстетичный вид фасаду и защитят стены. Их не выполняют сразу после завершения строительства – дому нужно дать время на усадку. Также следует помнить, что внешняя отделка осуществляется только по завершении внутренних работ. Оштукатуривание или заливка полов насыщают блоки влагой, поэтому ей необходимо дать выйти наружу.
- Оштукатурить и покрасить. К данным манипуляциям приступают только после высыхания кладки. Армирование сеткой позволит значительно увеличить срок эксплуатации облицовочного слоя. Штукатурка наносится тонким слоем и далее покрывается фасадной краской с использованием колера нужного оттенка.
- Облицевать кирпичом. Более респектабельный вид обретет построенное здание, если облицевать его кирпичом.
Такие работы можно проводить как параллельно строительству, так и после его окончания. Здесь важно придерживаться следующих правил:
- максимальная высота стены из штучного материала не должна превышать 15 м;
- данная кладка обязательно должна опираться на фундамент или на фундаментную балку;
- необходимо обустроить вентиляционный зазор, чтобы конденсат не скапливался в межслойном пространстве.
- Вентилируемый фасад. Такой способ облицовки обеспечит хорошую вентиляцию, защитит стены от осадков, придаст солидности строению. Крепежные элементы подбираются в зависимости от плотности блоков. При монтаже рекомендуется учитывать некоторые особенности:
- расстояние между стеной и устанавливаемым фасадом увеличивается с высотой дома. При монтаже панелей на высотных зданиях такой зазор может составлять и 20 см;
- вентиляционные отверстия совмещаются с цоколями и карнизами, при этом нижние лучше соединить с системами вентиляции и отвода влаги.
Суммарная площадь отверстий должна соответствовать расчету 75 см² на 20 м² стены;
- в качестве теплоизоляции рекомендуется применять жесткие материалы, плотность которых должна быть от 90 кг/м³ и выше. Они должны быть оснащены ветрозащитными и паропроницаемыми покрытиями.
Но то, что касается цвета, фактуры и стиля сайдинга, то выбор просто огромен и ограничивается лишь фантазией владельца строения: всевозможные расцветки, имитация пород древесины, металла, камня.
Внутренние работы
Особых требований к отделке внутренних помещений не предъявляется. Только для отапливаемых помещений с высокой влажностью таких как: ванная комната, парная, сауна, баня необходима качественная влагоизоляция.
- Оштукатуривание газобетонных блоков не отличается от обычных работ. Поверхность выравнивается, очищается, грунтуется и затем наносится штукатурка. Можно выполнить окрашивание водно-дисперсионной краской с добавлением колера требуемого оттенка.
Такие стены советуют оклеивать бумажными обоями – они повышают сопротивление воздухопроницаемости.
- Также отделка выполняется и гипсокартонными листами, которые могут монтироваться как на подготовленный каркас, так и приклеиваться напрямую к стенам, благодаря ровной поверхности блоков.
- Если в качестве облицовочного материала выбирается керамическая плитка, помните, она значительно уменьшит паропроницаемость стены. Этот вариант отделки оптимально подходит в том случае, когда внешняя поверхность стены оштукатурена. Следует отметить, что запрещена одновременная отделка внутренних и внешних поверхностей стен паропроницаемыми материалами.
Чтобы строящийся загородный дом, коттедж получился прочным, теплым, надежным и долговечным, требуется соблюдать технологию возведения на всех этапах работ. В противном случае есть вероятность, что все затраченные финансы и усилия окажутся напрасными. Не пренебрегайте советами опытных прорабов, а лучше обратитесь к специалистам, которые выполнят необходимые расчеты и создадут проект, соответствующий всем строительным нормам.
Технические характеристики газобетона YTONG
Наибольшее количества тепла покидает дом через наружную стену. Потерю можно предотвратить, используя при возведении стен дома блоки YTONG®. Благодаря наличию воздуха в порах газобетон YTONG® имеет превосходные теплоизоляционные характеристики.
Среди множества доступных на рынке стеновых материалов газобетон YTONG® характеризуется самой низкой теплопроводностью: коэффициент составляет 0,088- 0.11 Вт/м°C Помимо этого, стоит отметить, что в отличие от других материалов теплопроводность газобетона YTONG® одинакова низка во всех направлениях. Показатель теплоизоляции такой оштукатуренной конструкции внешней стены R= 3,65 м²*°С/Вт
Благодаря идеальной геометрии блоков, монтаж газобетонных блоков осуществляется на клеевой раствор для ячеистых бетонов. Клеевой шов при этом имеет ширину не более 2 мм, что сводит к нулю теплопотери через так называемые «мостики холода». Метод тонкошовной кладки позволяет нам сделать стену из блоков единым монолитом и добиться высокой энергоэффективности дома.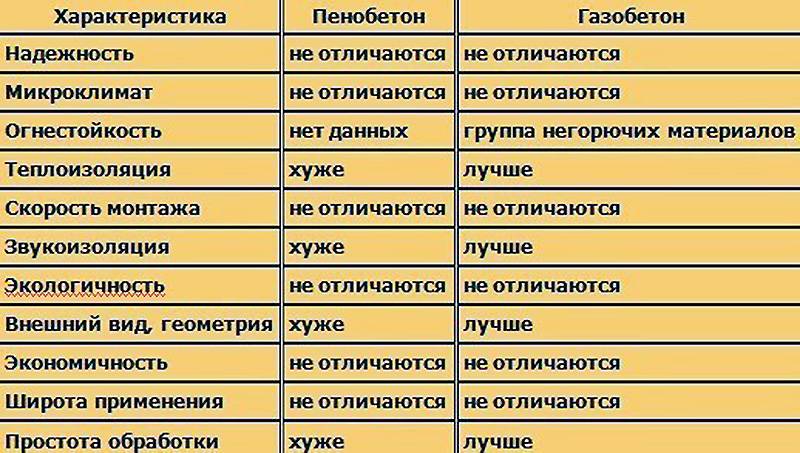
В отличии от классических теплоизоляционных материалов, так называемых эффективных утеплителей: минеральной ваты, пенополистирола, — срок службы блоков YTONG® практически неограничен. Долгий срок службы исключает необходимость периодической реставрации и обновления, обеспечивая дополнительную экономию средств. Благодаря пористой структуре материала YTONG® и беспрепятственному воздухообмену, одновременно с теплосберегающим эффектом достигается и требуемый уровень вентиляции помещений, необходимый для поддержания благоприятного микроклимата зданий. Показатели теплопроводности YTONG® (0,088-0,11) позволяют также в несколько раз сократить ширину стен и, соответственно, снизить трудозатраты при их возведении. Более того, отличные термоизоляционные свойства ячеистых блоков обеспечивают низкие эксплуатационные расходы по содержанию помещений, как благодаря экономии на отоплении зимой, так и с помощью сохранения прохлады в помещениях летом.
История производства газобетона. Классификация, свойства, характеристики.
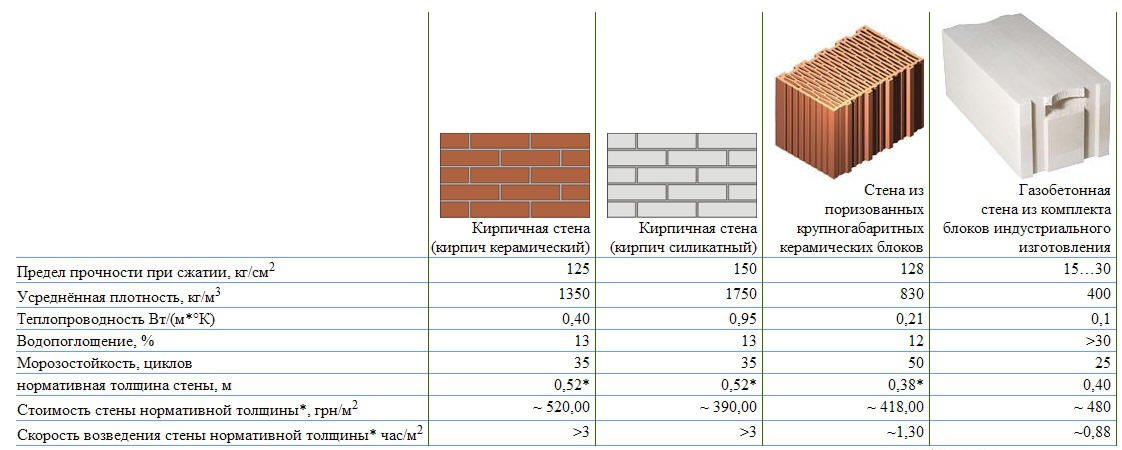
Газобетон получил широкое распространение в строительной сфере. Он был впервые создан в 1922 году в Швеции, удивив весь мир своими эксплуатационными характеристиками. Из газоблоков изготавливаются надежные и легкие конструкции, не требующие больших расходов на обслуживание. Именно поэтому в данной статье речь пойдет об истории газобетона – практичного и недорогого строительного материала.
Классификация газобетонов
История возникновения газобетона насчитывает множество классов, на которые был поделен этот строительный материал. Газоблоки классифицируются по нескольким параметрам, в том числе условиям твердения, и составу. По назначению газобетон делится на 3 типа:
-
Конструкционный;
-
Конструкционно-теплоизоляционный;
-
Теплоизоляционный.
По виду кремнеземистых и вяжущих компонентов материал также разделяется на несколько видов. В качестве связующих элементов при изготовлении газоблоков может применяться цемент, шлаки, известь, а также портландцемент и золы. В свою очередь, роль кремнеземистых компонентов выполняют природные материалы и вторичные продукты, например отходы ферросплавов.
Существует автоклавный и неавтоклавный газобетон. К первому типу относятся составы синтезного твердения, затвердевающие в среде насыщенного пара при сравнительно высоком давлении. К неавтоклавным материалам принято относить газобетоны гидратационного твердения – они застывают при электропрогреве, а также в естественных условиях.
Свойства газобетона
Богатство истории возникновения производства газобетона обусловлено его эксплуатационными свойствами. Ключевые особенности материала подробно описаны в таблице, представленной ниже.
Свойство |
Описание |
Легкость |
Стандартный строительный блок из ячеистого бетона весит около 30 кг. |
Низкая теплопроводность |
Газобетон – конструктивно-теплоизоляционный материал. Он позволяет уменьшить расходы на отопление помещений. |
Звукоизоляция |
В сравнении с кирпичной кладкой, звукоизоляционные свойства конструкций из газоблоков в 10 раз выше. Это обусловлено ячеистой пористой структурой газобетона. |
Пожаробезопасность |
Газоблоки изготавливаются из природного минерального сырья, что исключает опасность возгорания строительных блоков. |
Теплоаккумуляция |
Ячеистый бетон накапливает тепло, получаемое от солнечных лучей или отопления. Это позволяет сохранять прохладу в помещениях летом, а также экономить топливо в холодное время года. |
Морозостойкость |
В газобетоне есть резервные поры, в которые жидкости выталкиваются при замерзании. По этой причине материал не разрушается даже во время суровых морозов. |
Прочность |
По прочности газоблоки превосходят большинство аналогов. Они могут применяться при строительстве несущих стен, а также участвовать в кладке перегородок или стеновом заполнении высотных зданий. |
Конструкционность |
Точная геометрия газоблоков позволяет использовать клеевые растворы во время строительных работ. |
Простота обработки |
Материал поддается любым режущим инструментам. Простота обработки блоков упрощает разработку и реализацию уникальных архитектурных решений. |
Экономичность и практичность |
Большие габариты и малый вес материала способствует ускорению строительных работ. Также снижается стоимость возведения зданий – это обусловлено использованием клея вместо стандартных растворов. |
История газобетона гласит, что он получил широкое распространение еще и из-за экологичности. Современные газоблоки производятся из алюминиевой пудры, песка, цемента и извести. В процессе эксплуатации материал не выделяет токсичных веществ, поэтому его активно используют в жилом строительстве. Газобетон не подвержен гниению или старению, поэтому его применяют в качестве альтернативы дереву.
Газобетон: основные характеристики
Привлекательные эксплуатационные свойства газобетона обусловлены его техническими характеристиками. Среди них выделяется:
-
Вес и плотность. Технология изготовления способствует снижению веса газоблоков. При этом на массу строительных блоков может указать маркировка плотности, например D500, D600 или D700.
-
Теплопроводность. Коэффициент этого показателя у газобетона равен 0,13 Вт/м0С. Здания, построенные из газоблоков, быстро прогреваются.
-
Прочность. У строительных блоков марки D500 этот показатель не превышает 4 Мпа.
Чтобы укрепить конструкции, газоблоки используют совместно с кирпичом.
-
Срок службы. Большинство производителей предоставляют гарантию на 60-80 лет, что говорит о долговечности стройматериалов.
Отдельного внимания заслуживает несущая способность газобетона. С помощью этого материала можно возводить трехэтажные здания. Газоблоки пользуются большим спросом в малоэтажном строительстве.
Неармированные и армированные изделия
Существуют армированные и неармированные изделия из газобетона. Они активно используются в жилом и промышленном строительстве. В качестве армированных изделий производители представляют панели перекрытия и перемычки, применяющиеся для строительства многоквартирных домов. Среди преимуществ таких строительных элементов выделяется малый вес, повышенная прочность и точность геометрических размеров.
В качестве неармированных изделий из ячеистого бетона на рынке представлены строительные блоки. Причем большая часть такой продукции изготавливается с использованием управляемого автоклавного процесса. История появления автоклавного газобетона берет начало в Швеции. При этом автоклавный процесс был запатентован еще в 1924 году.
История появления технологии производства автоклавного газобетона
Автоклавный газобетон был создан Йоханом Акселем Эрикссоном – шведским изобретателем, который работал совместно с профессором Хенриком Крюгером. Только спустя 5 лет с момента, когда автоклавный процесс был запатентован, стартовало массовое производство строительного материала.
Первый бренд автоклавного газобетона появился в Швеции и назывался Ytong. В дальнейшем технология изготовления стройматериала была передана в другие регионы – Центральную Европу, Ближний Восток, Африку и Азию. В настоящее время лидером по производству автоклавного газобетона является Китай. Это обусловлено большим спросом на коммерческое пространство и жилье.
История производства ячеистых бетонов в СССР
История возникновения ячеистых бетонов в СССР началась в 1930-х годах. К 1950-м годам автоклавные материалы выпускались в промышленных масштабах. Еще через 10 лет производство такой продукции стало самостоятельно развивающимся научным направлением, которое хорошо финансировалось и опережало европейские наработки тех лет.
Уже к 1990 году были построены тысячи жилых, производственных и общественных объектов из ячеистого бетона. Несмотря на наличие собственных наработок, в СССР нередко полагались на европейские технологии. К 2011 году объемы производства ячеистого бетона в России выросли до 3,2 миллиона кубических метров в год. Во многом такие показатели обусловлены программой 1987 года, предусматривавшей строительство 250 новых заводов по производству автоклавных ячеистых смесей.
Газобетон в РФ
Новый этап производства газобетона начался в России, где с 1994 года появились импортные технологические линии. Выпускаемая в 1990-х годах продукция отличалась от «советской» повышенной плотностью и долговечностью. Постепенно автоклавные стеновые материалы вытеснили неавтоклавные ячеистые бетоны с рынка, став достойным конкурентом для силикатного кирпича и керамзитобетона.
На отечественных линиях в России выпускаются сравнительно тяжелые составы. Импортное оборудование позволяет изготавливать легкие и практичные ячеистые бетоны. Чаще всего в стране производятся газоблоки плотностью от 300 до 800 килограмм на кубический метр. При этом за последние годы в России сохраняется тенденция снижения плотности автоклавных газоблоков.
Тенденция развития технологии
Первые наработки, связанные с изготовлением газобетона, принадлежат Гоффману – известному инженеру из Чехии. Чтобы сделать материал пористым, в гипсовое или цементное основание добавлялись соли и кислоты. В 1889 году Гоффман получил патент на свое изобретение, однако дальнейшего развития в этой сфере не было.
Таким образом, шведский ученый Эрикссон не был первооткрывателем. Большой вклад в технологию изготовления ячеистых бетонов внесли специалисты из США. Вместо солей и кислот они использовали менее токсичные материалы – порошки цинка и алюминия. Вещества реагировали с известью, из-за чего выделялся водород, создающий ровные поры во всей структуре бетона. В дальнейшем эта технология лишь дорабатывалась, в результате чего мир получил легкий и прочный строительный материал.
Различия между газобетоном и газосиликатом
Оба материала относятся к разновидностям бетона. Тем не менее, газобетон отличается от газосиликата показателями морозоустойчивости и теплопроводности. Также различия заключаются в технологии производства. Для изготовления газоблоков используются портландцемент, известь, песок и вода. Газосиликат, в свою очередь, может изготавливаться без цемента, поскольку в качестве связующего вещества выступает исвестково-кремнеземистая смесь.
Пеноблок или газоблок — что лучше
Чтобы ответить на вопрос, какой из материалов лучше, следует обратить внимание на несколько факторов:
-
Автоклавный газоблок, имея меньшую плотность в сравнении с пеноблоком, может обладать большей прочностью.
-
Из-за отсутствия сообщений между порами, пеноблок менее восприимчив к увлажнению, чем газоблок.
-
В отличие от пенобетона, газобетон практически не усаживается.
-
Газобетон, без потери прочности, может находиться под воздействием открытого пламени в два раза дольше.
Таким образом, газобетон превосходит пенобетон по многим параметрам. По этой причине он пользуется большим спросом на рынке стройматериалов.
Газобетон или керамоблоки
В отличие от керамических блоков, газобетон обладает меньшим запасом прочности. В качестве стройматериала для несущих стен чаще используются керамоблоки, однако в малоэтажном строительстве можно воспользоваться и ячеистым бетоном. Чтобы понять, какой из перечисленных материалов стоит выбрать, рекомендуем ознакомиться со следующими факторами:
-
Строительство здания из керамических блоков обойдется дороже, чем возведение аналогичного объекта из ячеистого бетона;
-
Простота обработки – главное преимущество газоблоков, которым не обладает керамика;
-
По показателям звукоизоляции керамические блоки превосходят газобетон;
-
Газоблоки – лучший выбор для обеспечения теплоизоляции без использования дополнительных материалов.
Опираясь на перечисленные факты, можно сделать вывод, что при выборе стройматериала покупателю нужно руководствоваться собственными предпочтениями, бюджетом и поставленными перед ним задачами.
ГОСТы и СНиПы
Все ГОСТы и СНиПы, которым соответствует газобетон, представлены в таблице ниже.
ГОСТ 25485-89 |
«Бетоны ячеистые» |
ГОСТ 31359-2007 |
«Бетоны ячеистые автоклавного твердения. Технические условия» |
ГОСТ 21520-89 |
«Инструкция по производству изделий из ячеистого бетона» |
ГОСТ 31360-2007 |
«Изделия стеновые неармированные из ячеистого бетона автоклавного твердения» |
СН 277-80 |
«Инструкция по изготовлению изделий из ячеистого бетона» |
Заключение
Газобетон обрел широкую известность во многих странах мира. Этот практичный строительный материал используется для строительства объектов промышленного, жилого и коммерческого назначения. По эксплуатационным свойствам газоблоки превосходят многие аналоги, в том числе кирпичи и пеноблоки. Этот фактор, а также сравнительно низкая стоимость, делают газобетон универсальным.
Газобетонные блоки: технические характеристики и сведения
Информация о новых или малоизвестных стройматериалах обычно сводится к перечислению нескольких преимуществ, которых достаточно для использования продукции в тех или иных целях. Так и произошло 15 лет назад с газобетонными блоками, появление которых сопровождалось бурной рекламой, но по многих характеристикам этот материал не оправдал своих ожиданий. Сегодня же к вопросам выбора ячеистого бетона многие подходят с большей осторожностью, детально оценивая и рассчитывая их физико-технические свойства.
Прочность
Один из основных технических показателей, от которого зависит выбор материала. Например, марка D350 обладает прочностью не более 1,5 МПа, чего недостаточно для кладки стен с высокой нагрузкой. Однако, марки газобетонных блоков от уровня D400 и выше обладают прочностью 3 МПа.
Этого показателя также недостаточно для соответствия прочности кирпича, однако в некоторых случаях возможно применение таких блоков в качестве материала для наружных стен и при устройстве фундаментов.
Прочность газобетонных блоков нельзя рассматривать в отрыве от плотности и массы. Дело в том, что небольшие уступки в этом показателе камню и кирпичу могут компенсироваться скромным весом и небольшой плотностью. В итоге блок с объемным весом в 500 кг/м3 может обладать прочностью на сжатие до 35–40 кгс/см3. Конечно, это относится к блокам, прошедшим автоклавную обработку, но и при таком условии это сочетание эксплуатационных качеств можно назвать уникальным.
Вернуться к содержанию
Теплопроводность
Кирпичная кладка редко может похвастаться хорошими качествами теплопроводности. Особенно часто строители сталкиваются с «мостиками холода», наличие которых снижает теплосберегающую функцию дома.
В случае с газобетонными блоками за теплопроводность «отвечают» поры, то есть воздушные пузыри в структуре материала, на долю которых приходится около 80% массы. Разные марки обеспечивают разный коэффициент теплопроводности, но в среднем он варьируется от 0,9 до 1,14 Вт/м °С.
Важно отметить, что это значение подходит не только для выполнения базовой функции защиты от холода стенами. Газобетон в виде панелей может выступать и самостоятельным теплоизолятором, сокращая затраты на отопление до 30%.
Вернуться к содержанию
Размеры газоблоков
Выбор типоразмера и формы блока очень важен, так как существуют разные технические требования к толщине стен, а в некоторых случаях и к форме. Стандартный размер газобетонных блоков с маркой плотности D500 предусматривает следующие параметры: 25х62,5 см и толщину в 40 см. При этом вес блока составит 30,5 кг.
В показателях теплопроводности такой материал позволит заменить кладку на 64 см, состоящую из 28 кирпичей. Разумеется, встречаются и другие типоразмеры – например, 20х25 см при высоте в 60 см и массе около 20 кг.
Можно констатировать, что по сравнению с кирпичом, газоблоки имеют большие габариты. Именно это позволяет им справляться с физическими нагрузками, а также выполнять теплоизоляционную функцию. Но, увеличение размеров не влечет особых проблем с перевозкой материала и обращением с ним на стройплощадке, так как небольшой вес нивелирует этот недостаток.
Вернуться к содержанию
Масса
Вес блоков напрямую связан с двумя характеристиками – плотностью и габаритами. Минимальная масса доступных на современном рынке газобетонных блоков составляет 9,9 кг. На 1 м3 приходится порядка 68 блоков с такой массой.
Их параметры при этом следующие: 10 см по толщине, 25 см по высоте и 60 см по длине. И напротив, максимальный вес газобетонного блока в стандартной шкале типоразмеров составляет около 48 кг. Параметры такого блока следующие: 40 см по высоте, 25 см по толщине и 60 по длине. На 1 «куб» приходится около 17 шт таких блоков.
Вернуться к содержанию
Устойчивость к внешним воздействиям
Среди ячеистых бетонов, газоблоки – это не самый благоприятный материал с точки зрения абсорбирующей функции. По этой причине технологи рекомендуют предусматривать надежную гидроизоляцию при укладке блоков. Дело в том, что пористая структура способствует интенсивному впитыванию влаги, из-за чего материал разрушается, не говоря о других вредных процессах, связанных с накоплением влажности в ячейках.
По этой же причине материал не стоит использовать в кладке фундаментных стен. Однако, если хорошо выполнить гидроизоляцию, то газобетон станет неплохим решением для устройства стен подвального помещения.
На защиту от внешних воздействий также влияет расход газобетонных блоков и применяемого для их кладки раствора. Сегодня для этой цели используется специальный клей, который может обладать энергосберегающей функцией. Непосредственно на расход блоков оказывает влияние толщина слоя укладки, количество слоев стены или перегородки, а также типоразмер материала.
Противостояние морозам – еще одно свойство, которое следует учитывать. Газобетонные блоки в зависимости от марки обладают коэффициентом морозостойкости F75 – F100. Это значит, что материал способен выдерживать 75-100 циклов заморозки и последующего оттаивания.
Важно учитывать, что превышение этого количества в процессе эксплуатации вовсе не означает разрушения блоков. Производители гарантируют, что в рамках этого предела материал будет обеспечивать свои первоначальные технические функции. Примечательно, что газобетонные блоки технические характеристики которых предусматривают 100 циклов замораживания, превосходят по этому показателю рядовой кирпич в некоторых модификациях.
Газоблок является огнестойким стройматериалом и не способствует распространению пожара. Это еще одно качество ячеистого бетона, по которым он превосходит многие конкурирующие материалы. Обусловлено это свойство тем, что в основе блоков заложена неорганическая смесь, а роль искусственных добавок при пожаре незначительна.
Вернуться к содержанию
Звукоизоляционные характеристики
С одной стороны, известно, что тяжелые стройматериалы с высокой плотностью обеспечивают более надежный барьер перед шумом и звуками. Но в случае с легким газобетонным блоком следует рассматривать и другой аспект – наличие пор, которые также оказывают эффект шумоподавления.
Помимо этого, немаловажную роль в звукоизоляции играет толщина газобетонных блоков, которая может достигать нескольких десятков сантиметров. Согласно испытаниям производителей, стены и перегородки из газобетонных блоков способны обеспечивать звукоизоляцию в среднем от 47 до 55 дБ. Это относится к газобетону с плотностью 500-600 кг/м3, который использовался в стене толщиной 15 см с наличием отделочного цементно-песчаного покрытия толщиной 1 см.
Вернуться к содержанию
Усадка на высыхание
Это одно из самых неприятных явлений, с которым сталкиваются строители в работе с ячеистым бетоном. Сразу надо сказать, что данному процессу в наибольшей степени подвержен пенобетон, но и газобетонные блоки не избавлены от него.
В частности, этот показатель варьируется от 0,2 мм до 0,3 мм на 1 метр. Это некритический уровень, но его превышение вполне возможно по многим причинам и тогда появляются высокие риски образования трещин. Устранить последствия усадки, конечно, не составит труда обычной шпаклевкой, но лучше всего предупредить этот процесс.
Для этого необходимо изначально работать только с правильно просушенными блоками. Например, газобетонные блоки технические характеристики которых предусматривают высокую плотность, особенно важно хорошо просушить в самом ядре, оставив при этом несколько увлажненными внешние стороны.
Вернуться к содержанию
Применение газобетонных блоков
Несмотря на ограничения и негативные стороны от использования газобетона, его эксплуатация может быть оправдана на самых разных объектах. В первую очередь, это стены домов, и малоэтажных, и высотных – главное, правильно определиться с маркой материала и его прочностью.
Газобетон широко используется в качестве материала для внутренней отделки. Его легко обрабатывать, поэтому многие решают именно такие блоки применять в создании сложных конструкционных частей дома. Ценятся и теплоизоляционные качества газобетонных блоков, которые позволяют их использовать в утеплении стен, перегородок и фасадных конструкций.
При закладке или в монтаже технологических конструкций или элементов (подвалов, печей, фундаментов) с высокой ответственностью газобетон можно использовать только после тщательного анализа его технических качеств на предмет соответствия эксплуатационным требованиям проекта.
Не нашли ответов в статье? Больше информации по теме:
Газосиликатные блоки – основные свойства и характеристики. Технические характеристики газосиликатных блоков Блоки газобетонные прочность
В современных строительных технологиях большое значение придается выбору материала для возведения того или иного типа зданий. Одним из наиболее популярных строительных материалов сегодня считают газосиликатные блоки, которые отличаются рядом преимуществ и используются достаточно часто.
Их широкое применение обусловлено оптимальным балансом цены и качества – по большому счету никакой другой строительный материал не выдерживает эту пропорцию столь же выгодно.
Если разобраться, то вряд ли газобетон относится к современным стройматериалам – его разработали еще в конце 19 века. В начале прошлого столетия группа ученых даже запатентовала открытие нового чудо-материала, однако его свойства были далеки от тех, которыми отличается сегодняшний газосиликат.
В современном виде газосиликатный материал получили в конце 20 века – это бетон с ячеистой структурой, твердение которого происходит в автоклаве. Этот метод нашли еще в 30-х годах, и с тех пор он особых изменений не претерпел. Совершенствование характеристик происходило за счет внесения уточнений в технологию его получения.
Газобетон является одной из основ для производства газосиликатных блоков
Принцип изготовления
В качестве исходных ингредиентов для получения газобетона используются следующие вещества:
- песок;
- цемент;
- известь;
- гипс;
- вода.
Чтобы получить ячеистую структуру, в состав добавляют порцию алюминиевого порошка, который служит для образования пузырьков. После смешивания массу выдерживают нужное время, дожидаясь вспучивания, после чего разрезают на части и ставят в автоклав. Там масса отвердевает в паровой среде – эта технология является энергосберегающей и высокоэкологичной. При изготовлении газобетона не происходит выделения вредных веществ, которые могут нанести ощутимый вред окружающей среде или здоровью человека.
Свойства
Характеристики, которыми отличаются газосиликатные блоки, позволяют рассматривать их как стройматериал, который хорошо подходит для возведения зданий. Эксперты утверждают, что газобетон соединил в себе наилучшие качества камня и древесины – стены из него прочны и хорошо защищают от холода.
Пористая структура блоков гарантирует высокие показатели пожаробезопасности
Ячеистая структура объясняет маленький коэффициент теплопроводности – он гораздо ниже, чем у кирпича. Поэтому здания из газосиликатного материала не столь требовательны в плане утепления – в некоторых климатических поясах оно вообще не требуется.
Ниже мы приводим основные свойства газосиликата, благодаря которым он стал столь востребованным в строительной сфере:
- маленькая масса при внушительных размерах – это свойство позволяет ощутимо снизить расходы на монтаж. Кроме того, для погрузки, перевозки и возведения стен не требуется кран – достаточно обыкновенной лебедки. Скорость строительства по этой причине также гораздо выше, чем при работе с кирпичом;
- хорошая обрабатываемость – газосиликатный блок можно без проблем пилить, сверлить, фрезеровать, используя при этом обычный инструмент;
- высокая экологичность – специалисты говорят, что этот показатель у газобетона сравним с деревом. Материал не выделяет никаких вредных веществ и не загрязняет окружающую среду, при этом, в отличие от дерева, он не гниет и не подвержен старению;
- технологичность – газосиликатные блоки сделаны таким образом, чтобы с ними было удобно работать. Кроме маленькой массы, они отличаются удобной формой и технологическими выемками, захватами, пазами и т.п. Благодаря этому скорость работы с ними возрастает в 4 раза по сравнению с возведением зданий из кирпича;
- низкая теплопроводность газосиликатных блоков – она обусловлена тем, что газобетон на 80 процентов состоит из воздуха. В зданиях, которые построены из этого материала, снижаются расходы на отопление, к тому же можно на одну треть слабее их утеплять;
В доме из газосиликата в любое время года будет поддерживаться устойчивый микроклимат
- морозостойкость – в структуре есть специальные пустоты, куда вытесняется влага при замерзании. Если выдержаны все технические требования к изготовлению, морозостойкость газобетона превышает две сотни циклов;
- звукоизоляция – очень немаловажный параметр, поскольку сегодня уровень шума на улицах достаточно высок, а дома хочется отдохнуть в тишине. По причине пористой структуры газосиликат хорошо задерживает звук, выгодно отличаясь в этом плане от кирпича;
- пожаробезопасность – минеральные вещества, которые используются для изготовления газосиликата, не поддерживают горения. Газосиликатные блоки способны выдерживать воздействие огня на протяжении 3-7 часов, поэтому его используют для возведения дымоходов, шахт лифтов, огнестойких стен и т.п;
- высокая прочность – газосиликат выдерживает очень высокие сжимающие нагрузки, поэтому подходит для постройки зданий с несущими стенами высотой до трех этажей или каркасно-монолитных зданий без всяких ограничений;
- негигроскопичность – газобетон не впитывает воду, которая попав на него быстро высыхает, не оставляя никаких следов после себя. Это объясняется тем, что пористая структура не задерживает в себе влагу.
Результаты Голосовать
Где вы предпочли бы жить: в частном доме, или квартире?
Назад
Где вы предпочли бы жить: в частном доме, или квартире?
Назад
Основным недостатком газосиликата является недостаточная прочность на изгиб, однако специфика его использования такова, что практически исключает возможность изгибающих нагрузок, поэтому этот недостаток не играет большой роли.
Чем меньше в теле искусственного камня воздуха, тем выше его прочность и плотность
Марки газоблоков
Плотность газосиликатных блоков является основным критерием, который рассматривается при маркировке. В зависимости от ее величины стройматериал обладает разными наборами характеристик, что обуславливает сферу его применения.
Ниже мы рассмотрим различные марки газосиликата и то, как их используют в строительстве:
- D300 – наиболее подходящий стройматериал для возведения монолитных зданий. Плотность газосиликатных блоков этой марки составляет 300 кг/м 3 – она хорошо подходит для постройки стен малоэтажных домов в один слой или для двуслойных монолитных домов с высокой степенью теплоизоляции;
- D400 – его используют для постройки двухэтажных зданий и коттеджей, а также для теплоизоляции наружных несущих стен высотных зданий;
- D500 – это разновидность с наилучшей комбинацией утепляющих и конструкционных характеристик. По плотности она идентична бревну или деревянному брусу и применяется для возведения перегородок и внутренних стен зданий, проемов окон и дверей, а также оболочки армированных перемычек, стропил и ребер жесткости;
- D 600 – это газосиликатный блок с самой высокой плотностью, которая составляет 600 кг/м 3 , он используется там, где необходимо ставить прочные стены, подверженные высоким нагрузкам.
Ниже приводится таблица, иллюстрирующая другие параметры, которыми отличаются газосиликатные блоки разных марок.
В зависимости от плотности все газосиликатные блоки принято делить на конструкционные, конструкционно-теплоизоляционные и теплоизоляционные
Точность размеров
Газосиликаты могут иметь некоторые отклонения в своих габаритах. В зависимости от их величины различают три категории точности этого материала:
- Первая категория – она предназначена, чтобы класть блок насухо или на клей. В ней разрешается погрешность размеров по высоте, длине и толщине до полутора миллиметра, прямоугольности и углов – до двух миллиметров, ребер – до пяти миллиметров.
- Вторая категория применяется, чтобы класть газосиликатные блоки на клей. В ней погрешность по основным габаритам допускается до двух миллиметров, прямоугольность – до 3 миллиметров, углы – до 2 миллиметров и ребра – до 5 миллиметров.
- Третья категория газоблоков кладется на раствор, в ней погрешность по основным габаритам не более 3 миллиметров, по прямоугольности – менее 3 мм, углы – до 4 миллиметров, ребра – до 10 миллиметров.
Выбор газосиликата
При покупке газосиликатных блоков обычно оценивают три критерия, которые влияют на решение:
- функциональные характеристики – плотность, морозостойкость, коэффициент теплопроводности и т.п.;
- размеры одного блока;
- объем одного блока;
- стоимость.
Массовое применение газосиликатных блоков в строительстве свидетельствует о их огромной популярности. В плане соотношения цены и качества при замечательных характеристиках газобетонных блоков ничего наиболее оптимального, чем газосиликат пока что не придумали. Газобетон представляет собой ячеистый бетон автоклавного твердения – проверенный временем стройматериал, применяемый практически во всех видах конструктивных элементов сооружений и зданий самого разного назначения. Но откуда взялась технология производства ячеистого бетона, и когда он стал использоваться в своём современном виде? Разработки, направленные на получение нового многофункционального стройматериала велись ещё с конца ХIХ-го века. К началу ХХ-го несколько зарубежных ученых-экспериментаторов успели получить патент на изобретение так называемого «чудо-бетона», ведь в то время мир крайне нуждался в больших количествах искусственно производимого камня для строительства. Экспериментируя с составными элементами, методом проб и нередких ошибок был получен прототип современного газобетонного раствора. Однако свойства и характеристики газосиликатных блоков такими, как мы их знаем сейчас, в то время, конечно, не были. Современные газоблоки появились лишь в 90-тые годы. Это всем известные пенобетонные, полистеролбетонные и газобетонные блоки. Касательно последних — они бывают 2-ух видов: неавтоклавного и соответственно автоклавного способа затвердения. Неавтоклавные газобетоны неоднородны и довольно часто содержат в себе вредные воздухопоры, дающие большую усадку в ходе процесса эксплуатации. Газобетон, полученный в результате применения автоклавного метода, гораздо экологичнее и прочнее неавтоклавного (примерно в два раза). Метод по изготовлению ячеистого бетона предложен был в тридцатых годах и с тех пор, в принципе, мало изменился, хотя свойства газосиликатных блоков непрестанно улучшались и сфера его применения расширялась. Для его изготовления применяются песок, цемент, известь, гипсовый камень и обычная вода. В смесь из указанных материалов в незначительном количестве добавляется и алюминиевый порошок, который способствует образованию в смеси мелких воздушных ячеек, которые и делают материал пористым. Сразу после вспучивания, непродолжительной выдержки и разрезания массива на изделия необходимых размеров ячеистобетонную массу помещают в автоклав, где в паровой среде происходит ее твердение. Данная энергосберегающая технология не оставляет никаких отходов, которые загрязняли бы воздух, почву и воду. Газосиликатные блоки автоклавного твердения представляют собой материал, обладающий уникальными свойствами. Ведь в нем соединились наилучшие качества 2-ух древнейших строительных материалов: древесины и камня. В последние годы в связи с заметным повышением требований к теплоизоляционным качествам ограждающих конструкций в жилых и общественных зданиях одной из немногочисленных разновидностей бетонов, из коих возможно возведение по-настоящему теплоэффективных конструкций оптимальной толщины стали именно ячеистые бетоны. Характеристики и свойства газосиликатных блоков дают этому стройматериалу ряд весьма важных преимуществ:
Газосиликатные блоки лёгкий вес.
Вот, пожалуй, главное и неоспоримое преимущество газосиликата перед кирпичом. Вес газосиликатного блока находится в диапазоне 488 – 500-сот килограмм/м3, в зависимости от размера газобетонных блоков.
Обычный блок (по ГОСТу 21520-89) имеет марку плотности Д500 и размер 250 на 625 толщиной 400 мм и массу около 30,5 килограм и по теплопроводности может заменить стену толщиной в 64 см из двадцати восьми кирпичей, чей вес составляет сто двадцать килограмм. Большие размеры газосиликатных блоков при незначительном весе значительно сокращают затраты на монтаж и заметно уменьшают время строительства. Для осуществления подъема газобетона не нужен кран: с этим справятся несколько человек, либо можно воспользоваться обыкновенной лебедкой, следовательно, легкий вес такого ячеистого бетона позволяет снизить не только транспортно-монтажные работы, но и затраты на обустройство фундаментов. Газобетонные блоки гораздо легче, нежели пенобетон, поддаются обработке. Их можно пилить, сверлить строгать и фрезеровать при помощи обычного инструмента.
Блоки газосиликатные экологичность.
Поскольку газобетон автоклавного твердения получается из песка, цемента, извести и алюминиевой пудры, им не выделяется токсичных веществ, в результате по своей экологичности он приближен к дереву, однако при этом не склонен к гниению и старению. Газобетонные изделия совершенно безопасны для человека, в доме, выстроенном из него, дышится столь же легко, как и в возведённом из дерева.
Быстрота и экономичность при работе с газосиликатными блоками.
Благодаря такой характеристике газосиликатных блоков как их внушительные габариты (600 на (50-500) на 250 мм) при малом весе процесс строительства протекает быстро и легко. Скорость строительства при этом возрастает действительно существенно (раза в 4) и, соответственно, уменьшаются трудозатраты. В торцах некоторых видов газосиликатного блока сформированы специальные пазы и гребни, а также захватные карманы, предназначенные для рук. Совершенно не нужно 1-1,5 см раствора в кладке, вполне достаточно клеевого слоя в 3-5 миллиметров, наносимого зубчатой кельмой, дабы надежно укрепить блок. Блоки из газобетона обладают почти идеальной конфигурацией (поскольку допустимое отклонение их граней не превышает одного миллиметра), что и дает возможность использования технологии тонкошовной кладки, заметно снижает затраты на выполнение работ. Стоимость газосиликатных блоков бывает невысока по сравнению с тем же кирпичом, но клей для выполнения тонких швов примерно в два раза дороже цены песчано-цементного раствора, зато расход материала при производстве кладки газобетонного блока снижается примерно в шесть раз. В конечном итоге получаемая тонкошовная кладка даёт возможность втрое снизить затраты на кладочный раствор, кроме того, ввиду минимальной толщины соединительного клея уменьшаются мостики холода в стенах и дом получается теплее.
Газосиликатные блоки низкая теплопроводность.
Её обеспечивают пузырьки воздуха, которые занимают около 80-ти процентов материала. Действительно, именно благодаря им среди положительных качеств газобетонных блоков есть высокая теплоизоляционная способность, за счёт которой снижаются затраты на отопление процентов на 20-30 и можно отказаться от применения дополнительных теплоизолирующих материалов. Стены, которые выполнены из газосиликатных блоков, полностью отвечают новым СНиПовским требованиям, что предъявляются к теплопроводности стен общественных и жилых зданий. В сухом состоянии коэффициент теплопроводности у газобетона равен 0,12 Вт/м °С, при 12%-ной влажности — 0,145 Вт/м °С. В средней полосе России возможно возведение стен из газосиликатных блоков (плотностью не больше 500 килограмм/м3), чья толщина составляет 40 см.
Энергосбережение благодаря газосиликатным блокам.
На сегодняшний день энергосбережение стало одним из важнейших показателей. Бывает, что пренебрежение данным параметром приводит к невозможности эксплуатации добротного дома из кирпича: владелец попросту не мог позволить себе финансово отапливать настолько большое помещение. При использовании газобетонного блока с весом 500 килограмм/м3, толщиной 40 см достигаются показатели по энергосберегающему параметру в пределах нормы. Использование газобетонных блоков плотностью более, чем 500 килограмм/м3 приводит к заметному ухудшению параметров (теплотехнические свойства понижаются на пятьдесят процентов при использовании блоков, имеющих плотность в 600-700 килограмм/м3). Газосиликатные блоки плотностью меньше, чем 400 килограмм/м3 можно применять в строительстве лишь в качестве утеплителя , ввиду их низких характеристик прочности.
Блоки газосиликатные морозостойкость.
Качества газобетонных блоков в плане морозостойкости позволяют им стать рекордсменами среди материалов, которые используются в малоэтажном строительстве. Отличная морозостойкость объясняется присутствием резервных пустот, в которые при замерзании вытесняется вода, при этом сам газосиликатный блок не разрушается. Если технология строительства из газобетона соблюдается неукоснительно, морозостойкость стройматериала превышает двести циклов.
Звукоизоляционные качества газобетонных блоков.
За счёт его ячеистой мелкопористой структуры, звукоизоляционные качества газосиликата во много раз выше, нежели у кирпичной кладки. При существовании воздушного зазора меж слоями газобетонных блоков, либо при выполнении отделки стеновой поверхности более плотными стройматериалами, обеспечивается звуковая изоляция примерно в 50 дБ.
Блоки автоклавного твердения пожаробезопасность.
Ячеистые газобетонные блоки не боятся огня. Дымоходы из газосиликатных блоков прокладывают сквозь любые деревянные конструкции без проведения разделки, поскольку тепло они проводят плохо. А поскольку для получения газобетона применяется лишь минеральное сырье природного происхождения, газобетонные блоки принадлежат к группе не поддерживающих горение материалов и способны выдерживать одностороннее огненное воздействие на протяжении 3–7-ми часов. При использовании газобетонных блоков в связке с металлоконструкциями, либо в качестве обшивки они идеально подходят для возведения пожаростойких стен, лифтовых и вентиляционных шахт.
Блоки газобетонные прочность.
При низком объемном весе газосиликатного блока — 500 килограмм/м3 — он имеет довольно высокий показатель прочности на сжатие — в районе 28–40 кгс/см3 благодаря автоклавной обработке (для сравнения тот же пенобетон — всего 15 кгс/ см3). На практике прочность блока бывает таковой, что он может смело использоваться при постройке домов с несущими стенами до 3-ех этажей, либо без ограничения этажности — в каркасно-монолитных строительстве.
Газосиликатные блоки легкость и рациональность обработки.
Блоки из газобетона достаточно легко поддаются любой механической обработке: без проблем их можно пилить, сверлить, строгать, фрезеровать, применяя при этом стандартные инструменты, что используются для обработки древесины. Каналы под трубы и кабели можно прокладывать с помощью обычного ручного инструмента, а можно для ускорения процесса применять и электроинструмент. Ручная пила позволит легко придать газосиликату любую конфигурацию, что полностью решает вопросы с доборными блоками, а также внешней архитектурной выразительности сооружений. Каналы и отверстия для обустройства электропроводки, розеток, трубопроводов и т.д. можно прорезать, используя электродрель.
Блоки газосиликатные размеры.
Процесс по изготовлению блоков автоклавного твердения гарантирует высокоточные размеры — обычно 250 на 625 миллиметров при различной толщине в 50 – 500 миллиметров (+- миллиметр). Отклонения, как видите, настолько минимальны, что только что выложенная стена являет собой поверхность, которая абсолютно готова для нанесения шпаклевки, являющейся основой под обои или покраску.
Негигроскопичность газобетонного блока.
Хотя автоклавный газобетонный блок является высокопористым материалом (его пористость способна доходить до 90-та процентов), материал не является гигроскопичным. Попав, например, под дождь, газобетон, в отличие от той же древесины довольно быстро высыхает и совершенно не коробится. По сравнению же с кирпичом газобетон совершенно не «всасывает» воду, так как капилляры его прерываются особыми сферическими порам.
Газобетонные блоки применение.
Самые легкие по весу газосиликатные блоки, имеющие плотность в 350 килограмм/м³ используются в качестве утеплителя . Газобетонные блоки плотностью четыреста кг/м³ идёт на постройку несущих стен и перегородок в малоэтажном домостроении. Имеющие высокие прочностные свойства газосиликатные блоки — 500 килограмм/м³ — применимы для строительства как нежилых, так и жилых объектов, достигающих более 3-ех этажей в высоту. И, наконец, те газосиликатные блоки, чья плотность равняется 700-та кг/м³ идеально подходят для возведения многоэтажных домов при армировании междурядьев, а также используются для создания легких перекрытий. Не требующие особого ухода газосиликатные блоки строители называют неприхотливыми и вечными. Блок автоклавного твердения отлично подходит для тех, кто стремится уменьшить себестоимость строительства. Стоимость газобетонных блоков невелика, к тому же на постройку дома из газосиликата нужно меньше отделочных и строительных материалов, нежели кирпичного. Да и работать с газосиликатными блоками достаточно просто, что снижает трудозатраты и ускоряет процесс возведения зданий — постройка из газосиликатных блоков ведётся в среднем раза в четыре быстрее, нежели при работе с кирпичом.
Блоки газосиликатные доставка и хранение.
Блоки газосиликата упаковываются производителем в довольно-таки прочную термоусадочную герметичную пленку, которая надежно предохраняет материал от влажностного воздействия. Потому нет необходимости заботиться о надлежащей защите газобетона от негативных атмосферных воздействий. Главной задачей покупателя, который самостоятельно перевозит газобетонные блоки становится защита их от разного рода механических повреждений. При транспортировке в кузове паллеты с установленными блоками должны жестко закрепляться мягкими стропами, которые призваны предотвращать поддоны с блоками от перемещений и трений. При выгрузке стройматериала также используются мягкие стропы. Если газобетонные блоки будут освобождены от защитной плёнки и станут храниться на открытой площадке, подвергаясь осадкам – учтите, что от повышенной влажности характеристики газобетонных блоков ухудшаются, потому этот материал следует держать под навесом или даже на закрытом складе.
Кладка из газобетонных блоков.
Работы по постройке зданий из газобетонных блоков могут производиться при температуре вплоть до – 50 градусов; при использовании специального морозостойкого клея. Поскольку газобетон – довольно легкий материал, он не вызывает выдавливания клея. В отличие от кирпичных стен, выполняемые из газобетона выкладывать можно без пауз. Согласно строительным нормативам для выкладывания наружных стен применяются газосиликатные блоки, имеющие толщину 375 — 400 миллиметров, для межкомнатных – не менее 250. Для того чтобы предотвратить проникновение влаги из подвала, кладку газосиликатных блоков следует вести на гидроизолирующий слой (к примеру, рубероид) — размеры его должны быть немного больше, чем ширина газобетонных блоков в кладке. 1-вый слой из газосиликатных блоков с целью выравнивания кладется на раствор, дабы компенсировать имеющиеся неровности фундамента. Начинают кладку газосиликатного блока с наивысшего по своим размерам зданиевого угла. Блоки при помощи уровня и молотка из резины выравниваются, шлифуются — с помощью терки, после чего кладка тщательно очищается от пыли. Укладке самого первого ряда газосиликатных блоков надо уделить особенное внимание, ведь от её ровности зависит удобство всей дальнейшей работы и конечное качество выполнения постройки. Контролировать укладку газосиликатных блоков можно при помощи уровня и шнура. Следующий ряд кладки газосиликатных блоков начинается с любого из углов. С тем чтобы обеспечить максимальную ровность рядов, не забывайте использовать уровень, а при большой длине стены – ещё и маячные промежуточные блоки. Производится укладка рядов с обязательной перевязкой газосиликатных блоков – то есть смещением каждого последующего ряда относительно предыдущих. Минимальной величиной смещения становится 10 сантиметров. Клей, который выступает из швов, не затирают, а удаляют с помощью мастерка. Блоки из газосиликата со сложной конфигурацией и доборные изготавливаются ножовкой для блоков.
Внутренние перегородки из газосиликатных блоков.
Независимо от того, какую из современных конструкций перегородок вы решите применить в собственном доме (к примеру, перегородки из металлопрофилей и гипсокортонных листов), вам все равно нужно будет делать какую-либо сэндвич-систему с применением утеплителя, дабы добиться оптимального уровня шумоизоляции. А, как известно, любая из сэндвич-систем по трудоемкости гораздо выше и дороже, нежели кладка из газосиликатных блоков. Проблему с перегородками легко решает газобетонный блок. Для возведения внутренних перегородок берутся газобетонные блоки, имеющие толщину в 75 и 100 миллиметров и плотность в 500. Стена в результате получается довольно-таки прочной, тепло- и шумоизолированной, но вместе с тем легкой.
Армирование при кладке из газосиликатных блоков.
При обустройстве стен в малоэтажных жилых домах из газобетонных блоков применяется арматура, которая назначается по спецрасчету, в соответствии с определённым проектом. Как правило, армирование производится через два — четыре ряда кладки; дополнительно арматура устанавливается и в углах зданий.
Газобетонные блоки, таким образом, представляет собой поистине экономичный и эффективный стройматериал, чьи свойства позволяют в кратчайшие сроки сооружать постройки различного назначения. Выпускаются газосиликатные блоки в двух видах: стеновые и перегородочные. И те, и другие сертифицированы согласно ГОСТ. Изготавливается этот высокоэкологичный материал по передовым технологиям с использованием самого современного оборудования, что обеспечивает газосиликатному блоку высочайшее качество и постоянство важных технических характеристик. Если вы заинтересованы в его покупке, обращайтесь в компанию Атрибут-С , ведь мы знаем о газобетоне всё и предлагаем своим покупателям только качественные газосиликатные блоки, изготовленные по всем технологическим нормам и имеющие безупречные характеристики прочности, теплоизоляции, долговечности и др. Атрибут-С обеспечит вас любыми объёмами газобетонных блоков и, что немаловажно, помимо продажи мы предлагаем вам ещё и быструю доставку газосиликатных блоков с бережной разгрузкой. Вы по достоинству оцените наш безупречный сервис и цены на газосиликатные блоки, которые заметно ниже, чем у многих подобных организаций в Московском регионе. Заказать газосиликатные блоки с доставкой легко, вам всего лишь нужно связаться с нами по телефону 8-499-340-35-47, или же отправить заявку на адрес Этот e-mail адрес защищен от спам-ботов, для его просмотра у Вас должен быть включен Javascript . Можете не сомневаться, вам обязательно ответят и обговорят все условия оплаты и доставки газосиликатных блоков. А если у вас появились вопросы – пишите и получите все интересующие вас ответы.
Дополнительная информация о газобетонных блоках:
Блоки из газосиликата пользуются широким спросом в жилом и промышленном строительстве. Этот стройматериал по многим параметрам превосходит бетон, кирпич, натуральную древесину и др. Он изготавливается из экологически чистого сырья, отличается легкостью, огнеупорностью, простотой в эксплуатации и транспортировке. Применение этого легкого материала позволяет сократить расходы на обустройство тяжелого усиленного фундамента и тем самым удешевить строительство здания.
Что такое газосиликатные блоки
Газосиликатный блок представляет собой легкий и прочный стеновой материал, который изготавливается из ячеистого бетона. Изделия имеют пористую внутреннюю структуру, что положительно сказывается на их тепло- и шумоизоляционных свойствах. Такой стройматериал может применяться в различных сферах строительной индустрии — для возведения дачных и загородных домов, автомобильных гаражей, хозяйственных сооружений, складских комплексов и др.
Как производятся газосиликатные блоки
Существуют две основные технологии производства газосиликатных строительных блоков.
- Неавтоклавная . При таком методе производства застывание рабочей смеси происходит в естественных условиях. Неавтоклавные газосиликатные блоки выделяются более низкой стоимостью, но имеют некоторые важные отличия от автоклавных. Во-первых, они менее прочны. Во-вторых, при их высыхании усадка происходит почти в 5 раз интенсивнее, чем в случае с автоклавными изделиями.
- Автоклавная . Для автоклавного производства газосиликата требуется больше энергетических и материальных ресурсов, из-за чего повышается конечная стоимость изделий. Изготовление осуществляется при определенном давлении (0,8-1,2 МПа) и температуре (до 200 градусов Цельсия). Готовые изделия получаются более прочными и устойчивыми к усадке.
Виды блоков
В зависимости от плотности, состава и функционального назначения блоки из газосиликата делятся на три основные категории.
- Конструкционные . Обладают высокими прочностными характеристиками. Плотность изделий составляет не менее 700 кг/м 3 . Применяются при строительстве высотных сооружений (до трех этажей). Способны выдерживать большие механические нагрузки. Теплопроводность составляет 0,18-0,2 Вт/(м·°С).
- Конструкционно-теплоизоляционные . Блоки с плотностью 500-700 кг/м 3 используются при обустройстве несущих стен в малоэтажных зданиях. Отличаются сбалансированным соотношением прочностных и теплоизоляционных характеристик [(0,12-0,18 Вт/(м·°С)].
- Теплоизоляционные . Отличаются повышенными теплоизолирующими свойствами [(0,08-0,1 Вт/(м·°С)]. Из-за низкой плотности (менее 400 кг/м 3) не подходят для создания несущих стен, поэтому применяются исключительно для утепления.
Типоразмеры и вес
Стеновые блоки из газосиликата имеют стандартные размеры 600 х 200 х 300 мм. Габаритные характеристики полублоков составляют 600 х 100 х 300 мм. В зависимости от компании-производителя типоразмеры изделий могут несколько различаться: 500 х 200 х 300, 588 х 300 х 288 мм и др.
Масса одного блока зависит от его плотности:
- конструкционные блоки весят 20-40 кг, полублоки — 10-16 кг;
- конструкционно-теплоизоляционные блоки и полублоки — 17-30 кг и 9-13 кг соответственно;
- теплоизоляционные блоки весят 14-21 кг, полублоки — 5-10 кг.
Состав газосиликатных блоков
Газосиликат — это экологически безопасный стройматериал, который изготавливается из нетоксичного сырья натурального происхождения. В состав блоков входит цемент, песок, известь и вода. В качестве пенообразователя применяется алюминиевая крошка, которая способствует увеличению коэффициента пустотности блоков. Также при производстве материала применяется поверхностно-активное вещество — сульфонол С.
Характеристики материала
Строительные блоки из газосиликата обладают следующими характеристиками.
- Теплоемкость . Изделия, изготовленные по автоклавной технологии, имеют коэффициент теплопроводности 1 кДж/(кг·°С).
- Теплопроводность . Конструкционно-теплоизоляционный газосиликат имеет среднюю теплопроводность около 0,14 Вт/(м·°С), тогда как для железобетона этот параметр достигает отметки 2,04.
- Звукопоглощение . Газосиликатные блоки значительно уменьшают амплитуду внешних шумов, индекс звукопоглощения для этого материала равен 0,2.
- Морозостойкость . Материал с плотностью 600 кг/м 3 выдерживает до 35 циклов замораживания и оттаивания (что соответствует индексу F35). Изделиям с более высокой плотностью присвоен класс морозостойкости F50.
Преимущества и недостатки газосиликатных блоков
Основными достоинствами газосиликата являются следующие.
- Легкость . Блоки из газосиликата весят почти в 5 раз меньше, чем бетонные изделия тех же размеров. Это облегчает строительные работы и позволяет сократить расходы на транспортировку стройматериала.
- Эффективная тепло- и звукоизоляция . За счет наличия внутренних микропор достигаются высокие тепло- и шумоизоляционные характеристики газосиликата. Это позволяет создать комфортный микроклимат внутри помещений.
- Экологичность . В составе стройматериала не содержатся опасные токсины и канцерогены, которые могут причинить вред окружающей среде и человеческому здоровью.
- Огнеупорность . Газосиликат производится из негорючего сырья, поэтому не разрушается при интенсивном нагревании и не способствует распространению пламени при пожаре.
На сколько критичны недостатки
Как и любой другой стройматериал, газосиликат имеет некоторые недостатки.
- Низкий запас прочности . Материал с низкой плотностью (300-400 кг/м 3) имеет сравнительно невысокие прочностные характеристики. Поэтому при строительстве необходимо в обязательном порядке выполнять работы по армированию стен.
- Гладкие поверхности . Лицевые части газосиликатных блоков имеют гладкую поверхность с низким коэффициентом шероховатости. Из-за этого ухудшается адгезия с отделочными материалами, что усложняет процесс отделки стен штукатуркой и другими покрытиями.
- Низкая влагостойкость . Из-за увеличенной пористости материал чувствителен к повышенной влажности. Вода и водяной пар проникают во внутренние микропоры и при замерзании увеличиваются в объеме, разрушая блоки изнутри. Поэтому стены из газосиликата нуждаются в дополнительной гидроизоляции.
Где применяют газосиликатные блоки
Газосиликатные блоки используются в жилом и промышленном строительстве. Этот материал применяется не только для постройки несущих элементов зданий, но и для повышения теплоизоляции, а также для защиты инженерных сетей (в частности, отопительных).
Область применения газосиликата определяется его характеристиками, в первую очередь плотностью.
- Изделия, плотность которых составляет 300-400 кг/м 3 , имеют низкий запас прочности, поэтому они используются преимущественно для утепления стен.
- Газосиликат с плотностью 400 кг/м 3 пригоден для возведения одноэтажных домов, гаражей, служебных и хозяйственных пристроек. За счет более высокой прочности материал способен выдерживать значительные нагрузки.
- Блоки с плотностью 500 кг/м 3 оптимальны в соотношении прочностных и теплоизоляционных свойств. Их часто используют для строительства коттеджей, дачных домов и других построек высотой до 3 этажей.
Наиболее прочными являются газосиликатные блоки с плотностью 700 кг/м 3 . Их применяют для возведения высотных объектов жилого и промышленного значения. Но из-за увеличенной плотности уменьшается коэффициент пористости материала и, следовательно, его теплоизоляционные свойства. Поэтому стены, построенные из таких блоков, требуют дополнительного утепления.
Процесс строительства и испытания блоков.
В строительной сфере применяются изделия из газосиликата. Процесс производства блоков осуществляется при высоком давлении, а также в естественных условиях. Благодаря пористой структуре они хорошо удерживают тепло. Популярен газосиликатный блок D500, характеристики которого обеспечивают возможность использования данного материала при возведении домов. В результате применения блоков увеличенных размеров сокращается цикл постройки здания. Рассмотрим основные технические характеристики, которые нужно учитывать при выборе материала.
Что представляют собой блоки газосиликатные
Блочные изделия из газосиликата – современный строительный материал, изготовленный из следующего сырья:
- портландцемента, являющегося вяжущим ингредиентом;
- кварцевого песка, вводимого в состав в качестве заполнителя;
- извести, участвующей в реакции газообразования;
- порошкообразного алюминия, добавляемого для вспенивания массы.
При смешивании компонентов рабочая смесь увеличивается в объеме в результате активно протекающей химической реакции.
Газосиликатные блоки широко применяются в сфере строительства
Формовочные емкости, заполненные силикатной смесью, застывают в различных условиях:
- естественным образом при температуре окружающей среды. Процесс отвердевания длится 15-30 суток. Полученная продукция отличается уменьшенной стоимостью, однако имеет недостаточно высокую прочность;
- в автоклавах, где изделия подвергаются нагреву при повышенном давлении. Пропаривание позволяет повысить прочностные характеристики и удельный вес газосиликатной продукции.
Изменяются показатели плотности и прочности в зависимости от способа изготовления. Указанные характеристики материалов определяют область использования.
Блоки делятся на следующие типы:
- изделия конструкционного назначения. Они обозначаются маркировкой D700 и востребованы для строительства капитальных стен, высота которых составляет не более трех этажей;
- теплоизоляционно-конструкционную продукцию. Марка D500 соответствует данным блокам. Они применяются для сооружения внутренних перегородок и строительства несущих стен небольших зданий;
- теплоизоляционные изделия. Для них характерна повышенная пористость и уменьшенная до D400 плотность. Это позволяет использовать газосиликатный материал для надежной теплоизоляции стен.
Цифровой индекс в маркировке блоков соответствует массе одного кубического метра газосиликата, указанной в килограммах. С возрастанием плотности материала снижаются его теплоизоляционные свойства. Изделия марки D700 постепенно вытесняют традиционный кирпич, а продукция с плотностью D400 не уступает по теплоизоляционным свойствам современным утеплителям.
Газосиликатные блоки превосходят по механической прочности пенобетон
Блоки газосиликатные – плюсы и минусы материала
Изделия из газосиликата обладают комплексом серьезных достоинств. Главные плюсы газосиликатных блоков:
- уменьшенная масса при увеличенных объемах. Плотность газосиликатного материала в 3 раза меньше по сравнению с кирпичом и примерно в 5 раз ниже, если сравнивать с бетоном;
- увеличенный запас прочности, позволяющий воспринимать сжимающие нагрузки. Показатель прочности для газосиликатного блока с маркировкой D500 составляет 0,04 т/см³;
- повышенные теплоизоляционные свойства. Материал успешно конкурирует с отожженным кирпичом, теплопроводность которого трехкратно превышает аналогичный показатель газосиликата;
- правильная форма блоков. Благодаря уменьшенным допускам на габаритные размеры и четкой геометрии, кладка блоков осуществляется на тонкий слой клеевого раствора;
- увеличенные габариты. Использование для возведения стен зданий крупногабаритных силикатных блоков с небольшим весом позволяет сократить продолжительность строительства;
- хорошая обрабатываемость. При необходимости несложно придать газосиликатному блоку заданную форму или нарезать блочный материал на отдельные заготовки;
- приемлемая цена. Используя блочный газосиликат для возведения коттеджа, частного дома или дачи, несложно существенно снизить сметную стоимость строительных мероприятий;
- пожаробезопасность. Блоки не воспламеняются при нагреве и воздействии открытого огня. Они относятся к слабогорючим строительным материалам, входящим в группу горючести Г1;
- высокие звукоизоляционные свойства. Они обеспечиваются за счет пористой структуры. По способности поглощать внешние шумы блоки десятикратно превосходят керамический кирпич;
- экологичность. При изготовлении газосиликатной смеси не используются токсичные ингредиенты и в процессе эксплуатации не выделяются вредные для здоровья компоненты;
- паропроницаемость. Через находящиеся внутри газосиликатного массива воздушные ячейки происходит воздухообмен, создающий благоприятный микроклимат внутри строения;
- морозостойкость. Газосиликатные блоки сохраняют структуру массива и эксплуатационные характеристики, выдерживая более двухсот циклов продолжительного замораживания с последующим оттаиванием;
- теплоаккумулирующие свойства. Газосиликатные блоки – энергосберегающий материал, который способен накапливать тепловую энергию и постепенно отдавать ее для повышения температуры помещения.
Область применения зависит от плотности материала
Несмотря на множество достоинств, газосиликатные блоки имеют слабые стороны. Главные недостатки материала:
- повышенная гигроскопичность. Пористые газосиликатные блоки через незащищенную поверхность постепенно поглощают влагу, что разрушает структуру и снижает прочность;
- необходимость использования специального крепежа для фиксации навесной мебели и оборудования. Стандартные крепежные элементы не обеспечивают надежной фиксации из-за ячеистой структуры блоков;
- недостаточно высокая механическая прочность. Блочный материал крошится под нагрузкой, поэтому требует аккуратного обращения при транспортировке и кладке;
- образование плесени и развитие грибковых колоний внутри и на поверхности блоков. Из-за повышенного влагопоглощения создаются благоприятные условия для роста микроорганизмов;
- увеличенная величина усадки. В реальных условиях эксплуатации под воздействием нагрузок блоки постепенно усаживаются, что вызывает через некоторое время образование трещин;
- пониженная адгезия с песчано-цементными штукатурками. Необходимо использовать специальные отделочные составы для оштукатуривания газосиликата.
Несмотря на имеющиеся недостатки, газосиликатные блоки активно используются для сооружения капитальных стен в области малоэтажного строительства, а также для возведения теплоизолированных стен многоэтажных строений и для теплоизоляции различных конструкций. Профессиональные строители и частные застройщики отдают предпочтение газосиликатным блокам благодаря весомым преимуществам материала.
Газосиликатный блок D500 – характеристики стройматериала
Конструкционно-теплоизоляционный блок марки D500 используется для различных целей:
- сооружения коробок малоэтажных строений;
- обустройства межкомнатных перегородок;
- усиления дверных и оконных проемов.
Газосиликатные блоки обеспечивают хорошую теплоизоляцию помещения
Приняв решение приобрести блочный силикат с маркировкой D500, следует детально ознакомиться с эксплуатационными свойствами популярного строительного материала. Остановимся на главных характеристиках.
Прочностные свойства
Класс прочности материала на сжатие изменяется в зависимости от метода изготовления блоков:
- газосиликат марки D500, полученный автоклавный методом, характеризуется показателем прочности B2,5-B3;
- класс прочности на сжатие для аналогичных блоков, произведенных по неавтоклавной технологии, составляет B1,5.
Прочность блоков D500 достигает 4 МПа, что является недостаточно высоким показателем. Для предотвращения растрескивания газосиликатного материала выполняется усиление кладки сеткой или арматурой. Относительно невысокий запас прочности позволяет использовать блочный стройматериал в сфере малоэтажного строительства. При возведении многоэтажных зданий газосиликатные блоки применяются совместно с кирпичом для теплоизоляции возводимых стен.
Удельный вес
Плотность газосиликатных блоков – важный эксплуатационный показатель, характеризующий пористость блочного массива. Плотность обозначается маркировкой в виде латинской буквы D и цифрового индекса. Цифра в маркировке характеризует массу одного кубометра газосиликата. Так, один кубический метр газосиликата с маркировкой D500 весит 500 кг. Зная маркировку изделий по плотности, размеры блоков и их количество, несложно рассчитать нагрузку на фундаментную основу.
Газосиликатные блоки — экологичный материал
Теплопроводные характеристики
Теплопроводность газосиликатных блоков – это способность передавать тепловую энергию. Значение показателя характеризует коэффициент теплопроводности газосиликатных блоков.
Величина коэффициента изменяется в зависимости от концентрации влаги в материале:
- коэффициент теплопроводности сухого газосиликатного материала марки D500 составляет 0,12 Вт/м⁰С;
- при увеличении влажности до 5% теплопроводность блоков D500 увеличивается до 0,47 Вт/м⁰С.
В строениях, построенных из газосиликатных блоков, благодаря пониженной теплопроводности материала, круглогодично поддерживается благоприятный микроклимат.
Морозоустойчивость
Способность газосиликатных блоков воспринимать температурные перепады, связанные с глубоким замораживанием и оттаиванием, характеризует маркировка. Показатель морозоустойчивости для изделий D500 составляет F50. По сравнению с другими видами композитного бетона это достаточно неплохой показатель. На морозостойкость влияет концентрация влаги в блоках. С уменьшением влажности материала морозоустойчивость блоков возрастает.
Срок эксплуатации
Газосиликат отличается продолжительным периодом использования. Структура газосиликатного массива сохраняет целостность на протяжении более полувека. Изготовители блоков гарантируют срок службы изделий в течение 60-80 лет при условии защиты блоков от впитывания влаги. Оштукатуривание материала позволяет продлить срок службы.
Пожарная безопасность
Газосиликатные блоки – пожаробезопасный стройматериал с огнестойкостью до 400 ⁰С. Испытания подтверждают, что покрытая штукатуркой газосиликатная стена способна выдержать воздействие открытого огня на протяжении трех-четырех часов. Блоки подходят для сооружения пожароустойчивых стен, перегородок и дымоходов.
Заключение
Блочный газосиликат – проверенный материал для строительства малоэтажных зданий. Характеристики блоков позволяют обеспечивать устойчивость возводимых строений и поддерживать внутри зданий комфортный микроклимат.
Рекомендуем также
Узнаем что лучше — керамический блок или газобетон: сравнение, свойства и характеристики
Собственный дом должен быть долговечным, красивым и комфортным, чтобы зимой не мерзнуть и летом не париться. Выполнение этих условий зависит не только от соблюдения технологии проведения работ, но и от правильного выбора стенового материала.
Особенности
Традиционными материалами для возведения стен являются дерево, глиняный кирпич и газосиликатные блоки. Современная строительная промышленность предлагает вниманию застройщиков новые варианты, позволяющие ускорить сроки строительства, при сохранении несущей способности и теплоизоляционных качеств наружных стен жилых построек.
Речь идет о поризованных керамических блоках или газобетоне, а что лучше приобрести, знают не все. Чтобы сделать правильный выбор, следует ознакомиться с их свойствами, оценить достоинства и недостатки.
Газобетонный блок. Способы производства и эксплуатационные качества
Чтобы разобраться в достоинствах и недостатках газобетона, необходимо выяснить, что он собой представляет.
Для его производства используются вяжущие и кремнеземистые компоненты, вода и алюминиевая пудра. В качестве вяжущих компонентов применяются:
- известь;
- цемент;
- зола;
- шлаки;
- смесь перечисленных вяжущих.
Кремнеземистым наполнителем выбирают кварцевый песок, золу и другие промышленные отходы, пригодные для вторичного использования. Упрощенно процесс изготовления выглядит так: вяжущие и кремнеземистые компоненты смешивают с водой до определенной консистенции, добавляют алюминиевую пудру и заливают смесь в формы.
Алюминиевая пудра вступает в реакцию с вяжущим компонентом, с выделением водорода. В процессе газообразования пузырьки водорода в огромном количестве заполняют материал, от чего он приобретает отличные эксплуатационные свойства: легкость, низкую теплопроводность и экологическую чистоту.
Нюансы производства
Газобетон производят автоклавным и гидратационным способами. Уже по названию понятно, что для получения конечного продукта в первом случае сформованные блоки подвергаются обработке высоким давлением и температурой в специальных аппаратах — автоклавах. При этом само изделие приобретает повышенную прочность, отличается правильными геометрическими размерами, а процесс обработки значительно ускоряется.
Гидратационный, или естественный способ твердения, имеет большую продолжительность. В некоторых случаях для его ускорения применяется увеличение температуры до 100 градусов. По прочности такой газобетон уступает автоклавному.
Показатели
Приобретая газобетон, свойства и характеристики материала обязательно учитывают. По показателям прочности и плотности материал может быть:
- теплоизоляционным;
- конструкционно-теплоизоляционным;
- конструкционным.
Наименее плотным является теплоизоляционный газобетон. Его нельзя применять для кладки наружных стен и перегородок. Но он обладает наименьшей теплопроводностью и отлично зарекомендовал себя в качестве утеплителя. Его плотность равна 300-400 кг/м3.
Плотность конструкционно-теплоизоляционного бетона варьируется в пределах от 500 до 800 кг/м3. Он наиболее популярен среди строителей, обладая достаточно низкой теплопроводностью и одновременно высокой несущей способностью. Это позволяет использовать его для возведения наружных стен и не тратить дополнительные средства на их утепление.
Для конструкционного газобетона характерна самая высокая плотность, от 900 до 1200 кг/м3, что делает его отличным стеновым материалом. Однако в силу своей повышенной плотности, он обладает меньшей пористостью и, соответственно, высокой теплопроводностью. При возведении структурных элементов из конструкционного газобетона требуется дополнительное утепление либо увеличение толщины наружных стен.
Точность размеров
Разница в способах изготовления сказывается на точности геометрических размеров газобетонных блоков. По этому параметру изделия из этого материала делятся на три категории:
- К первой категории относят блоки, отклонения от заданных размеров которых не превышают 1,5 мм.
- Во второй категории допускаются отклонения не более 2 мм и отбитые углы.
- В третьей категории повреждения углов могут достигать 10 мм, при допустимом отклонении наружных размеров не более 4 мм.
Блоки первой и второй категории укладываются на специальный клей. Изделия, отнесенные к третьей категории, кладут только на раствор. При этом мостики холода образуются в большем количестве, чем при кладке блоков первых двух категорий.
Экономия на стоимости материалов приведет к ухудшению теплоизоляционной способности наружных стен или к дополнительным расходам на их утепление. Поэтому из блоков этой категории рекомендуется возводить хозяйственные постройки: гаражи, мастерские, сараи.
Плюсы газобетона
Как и любому строительному материалу, газобетону свойственны свои плюсы и минусы. Сравнивая их, можно вывести баланс, позволяющий застройщику сделать свой выбор.
К безусловным плюсам газобетона относятся:
- Малый вес. Нагрузка на фундамент от газобетонных стен значительно ниже, чем от кирпичных или стен из керамических изделий.
- Один газобетонный блок при укладке в стену заменит два керамических. Это позволит закончить возведение элементов в более сжатые сроки.
- Точная геометрия блоков, изготовленных в автоклаве, способствует более качественной кладке. Не тратится время на их выравнивание в процессе строительства.
- Показатель экологичности немного уступает дереву. Можно сказать, что после деревянных стен газобетонные — самые экологически чистые.
- По огнестойкости не уступает кирпичу и керамическим блокам.
- Материал легко обрабатывается, принимает любую форму, практически без отходов.
- Морозостойкость достаточно высокая, достигает 100 циклов замораживания и оттаивания.
- Паропроницаемость. Газобетон хорошо впитывает влагу и так же хорошо отдает ее в сухое помещение, что способствует поддержанию комфортного микроклимата.
- Прочность газобетона достаточна для возведения двухэтажных зданий.
- Материал можно изготовить своими руками при наличии исходных материалов, некоторого оборудования и ознакомления с соответствующей инструкцией. При этом будет получен материал гидратационного твердения, обладающий пониженной плотностью и малопригодный для многоэтажной постройки.
- Отличные показатели теплопроводности. Снижаются затраты на утепление и отопление.
- Цену газобетона можно считать невысокой (от 2900 до 3100 руб/м3), если сравнивать ее со стоимостью кирпича и керамических блоков.
- Производителей достаточно, чтобы выбрать материал подходящего размера по умеренной цене. Например, популярны блоки газобетонные 600х300х200 см.
Итого, в активе у рассмотренного материала не менее 13 достоинств.
Минусы газобетона
Но есть и недостатки, причем достаточно серьезные:
- Паропроницаемость, которая учитывается в плюсах, является также и минусом. В условиях низких температур накопленная в порах блоков влага замерзает и может стать причиной их разрушения.
- Материал отличается значительной хрупкостью, что необходимо учитывать при погрузке и транспортировке.
- По окончании строительства материал дает усадку. Величина ее сравнительно не велика, не более 0,3 мм на квадратный метр, но с учетом хрупкости в стенах при усадке обязательно появляются трещины.
- После окончания возведение стен из газобетонных блоков обязательным условием является устройство армированного пояса. Это добавляет трудоемкости всему процессу и требует участия квалифицированных специалистов.
- Чтобы защитить стены от впитывания влаги, требуется выполнение качественных и правильно выполненных отделочных работ.
- Одним из минусов является недостаточная механическая прочность газобетонных стен, при креплении к ним радиаторов и трубопроводов отопления. Без специальных приспособлений это сделать невозможно. Стены не выдерживают тяжести приборов. По этой же причине устройство перекрытий выполняется только из дерева и по деревянным балкам. Это снижает показатели звукопроницаемости и усложняет отделку потолков.
Свойства керамических блоков
Керамическим блокам также свойственны достоинства и недостатки. Правильнее назвать их поризованными керамическими блоками.
Исходным материалом при их производстве служит глина. При формовке камней в глину подмешивают опилки, которые выгорают при обжиге, образуя поры. Благодаря микропористой структуре теплоизоляционные свойства керамических блоков значительно превосходят обыкновенный кирпич и мало чем отличаются от газобетона.
Выпускаются различных размеров, лицевые и рядовые, с гладкой и рифленой поверхностью.
Достоинства керамики
Не все знают, что лучше — керамический блок или газобетон. Из положительных качеств первых отмечают следующие:
- Объем одного блока соответствует 14 обыкновенным кирпичам, но значительно легче их, что способствует ускорению процесса кладки.
- Относительно небольшой вес не передает значительных нагрузок на фундамент.
- Тычковые поверхности блоков образуют между собой стык гребень/паз, что позволяет с высокой точностью позиционировать их в ряду и снижает расход кладочного состава, поскольку заполнения стыков не требуется.
- Материал отличается высокой долговечностью. Производители гарантируют минимум 50 лет.
- Керамические блоки отличаются повышенной звукоизоляцией, благодаря своей ячеистой структуре.
- Экологичностью не уступает газобетону, поскольку изготавливается без применения ядовитых и токсичных материалов.
- Обладает повышенной огнестойкостью.
- Низкая теплопроводность. Хорошо удерживает тепло.
- Способность к насыщению влагой не превышает 10 процентов.
Недостатки керамических изделий
Среди минусов при строительстве домов из керамических блоков самым главным считают высокую стоимость изделий. Дом, возведенный из подобного материала, обойдется владельцу на 15 % дороже сходного по объему здания из газобетона.
Кроме этого, при строительстве домов из керамических блоков среди минусов отмечают следующие:
- Согласно ГОСТу, допускаются отклонения от размеров по ширине и высоте от +1 до –5 мм. Это отрицательно сказывается на качестве кладки.
- Ввиду особой прочности, материал трудно поддается обработке. Режется только болгаркой с алмазным кругом.
- Внутренние перегородки, образующие ячеистую структуру блока, достаточно хрупкие, что следует учитывать при их транспортировке и погрузочно-разгрузочных работах.
Сравнительные характеристики газобетонных и керамических блоков
Чтобы определиться с выбором лучшего материала для строительства, следует прибегнуть к сравнению газобетона и керамических блоков, размеры для строительства которых отличаются. Технические и эксплуатационные характеристики представлены в табличной форме:
Наименование характеристик | Различия и совпадения характеристик. Выбор лучшего варианта. |
Затраты времени на строительство | Размеры обоих материалов достаточно велики, что позволяет значительно ускорить процесс возведения стен, по сравнению с кладкой обычным кирпичом. Керамический блок труднее поддается обработке, это различие не является определяющим. |
Теплопроводность | Оба материала отличаются хорошими показателями. Но керамические блоки более плотные. Немного уступает в этом отношении газобетон. |
Прочностные характеристики | По этому параметру газобетон значительно уступает керамическим блокам. |
Рекомендации по толщине стен | Чтобы уравновесить этот показатель, стены из керамических блоков должны быть толще на 200 мм. |
Нуждаются ли стены в обязательной отделке | Газобетонные стены однозначно требуют последующей отделки, как по технологическим требованиям, так и с точки зрения эстетичности. Облицовочные керамические блоки отделки не требуют. |
Способность впитывать влагу | В силу своей пористости газобетон впитывает значительно больше влаги, чем керамические блоки. Это серьезный минус. |
Способность к усадке | Более всего ей подвержен газобетон. Усадка способствует появлению трещин в газобетонных стенах, чего не скажешь о керамике. |
Различия в применении | Стены и перегородки возводятся из обоих материалов. Однако в отличие от керамического материала в линейке газобетонных изделий отсутствуют облицовочные блоки. |
Отличие в стоимости | Одноэтажный дом из керамических блоков обойдется его владельцу как минимум на 15 % дороже стоимости, отраженной в смете дома из газобетона. Двух- и трехэтажные особняки их керамических блоков далеко не каждому по карману. Т. е. цена газобетона ниже. |
Возможность изготовления своими руками | Керамические блоки однозначно изготавливаются только промышленным путем. Газобетонные, без автоклава, можно изготовить самостоятельно. |
Отличия при выполнении кладки стен | Особых отличий нет. Газобетонные блоки положено армировать через каждые четыре ряда. После окончания кладочных работ изделия обязательно усиливаются армированным каркасом. При возведении стен из керамических блоков этого не требуется. |
Вывод
Как видно из приведенной таблицы, ответить на вопрос: какой материал лучше — газобетон или керамический блок, что выбрать из них, — сложно. Каждый имеет свои положительные и отрицательные стороны. Выбор остается за застройщиком.
Заключение
Те, кого больше волнует прочность и влагостойкость будущего дома, могут остановить свой выбор на керамических блоках. Те, кто считает этот материал слишком дорогим для себя, выберут газобетон. Дополнительно, задаваясь вопросом, что лучше — керамический блок или газобетон, рекомендуется проконсультироваться и со специалистом.
Свойства газобетонных блоков — достоинства и недостатки
Имеют ли газобетонные блоки недостатки? В последнее время этот вопрос интересует многих. Материал становится все более популярным, а спрос на него растет в геометрической прогрессии. На современном строительном рынке изделия из газобетона все увереннее занимают лидирующие позиции. Какие именно плюсы и минусы имеют свойства газобетонных блоков, в каких конкретных технологических процессах по строительству их использование оптимально, а в каких существует альтернатива. Как не переплатить за материал и работу, и не раскаиваться о содеянном в последствии.
Блок: 1/3 | Кол-во символов: 558
Источник: https://stavba.ru/materialy/gazobeton/svojstva-gazobetona.html
Средняя плотность
Пористая структура материала обеспечивает низкую плотность и малый вес при достаточной конструкционной прочности. Это главное достоинство всех ячеистых бетонов. Соответствие заявленным значениям плотности определяется по методике, утвержденной ГОСТ.
Она включает в себя лабораторные испытания образцов как смеси, приготовленной в идеальных условиях лаборатории, так и заводской смеси и готового продукта. Маркируется плотность или объемный вес буквой D и цифрами.
Узнать вес материала любой марки очень просто: цифра – это масса куба материала. То есть, 1 куб. м газобетона с D800 весит 800 кг.
Следующей мы рассмотрим теплопроводность газобетона в сравнении с деревом, пенобетоном и др. важные нюансы.
О положительных качествах гаобетона рассказывает это видео:
Блок: 3/12 | Кол-во символов: 786
Источник: http://stroyres.net/beton/gazobeton/haratkeristiki-i-fizicheskie-svoystva.html
Когда выбираешь стеновой материал для своего дома, приходится иметь дело с различными, даже противоречивыми мнениями о его свойствах
Любой из пользователей forumhouse.ru, кто стоит перед проблемой выбора стенового материала для своего будущего дома сталкивается с огромным потоком самой противоречивой информации. Не миновала данная участь и такой широко известный материал как газобетон.
Но, прежде чем мы перейдём к мифам и легендам о газобетоне, необходимо понять, что же это за материал.
Что же это такое газобетон?
Директор компании «Газобетон ЭкоСтрой» Эдуард Галлямов.
– Автоклавный газобетон относится к типу ячеистых легких бетонов и производится из кварцевого песка, извести, цемента и воды с добавлением газообразующего реагента, в роли которого выступает алюминиевый порошок или паста. Можно сказать, что по своей сути автоклавный газобетон является искусственным камнем, в котором в результате химической реакции, при взаимодействии газообразующего реагента с другими элементами смеси, образуются небольшие мелкодисперсные воздушные полости.
Автоклавированием – называется процесс, происходящий при нагреве и под давлением выше атмосферного. Так как при этих условиях достигается увеличение скорости реакции и больший выход конечного продукта.
Эдуард Галлямов:
– Особенностью газобетона автоклавного твердения, в отличие от обычного пенобетона, является как раз его заводское производство на высокоточном автоматизированном оборудовании с применением процесса автоклавирования при высоком давлении и температуре в среде перегретого пара. Особенностью этих блоков является их высокая геометрическая точность до 2мм, которая позволяет вести кладку блоков на клей.
Одним из главных преимуществ газобетона в строительстве является его технологичность, быстрая и легкая установка. Газобетон может шлифоваться и нарезаться по размеру на месте с помощью стандартных ручных пил.
Сегодня заводы выпускают в основном газобетонные блоки 3х модификаций:
- D400 B2.5
- D500 B3.5
- D600 B3.5-5
- Газобетонные блоки плотностью D400 прочностью B2.5 имеют низкий коэффициент теплопроводности и достаточную прочность, рекомендуются для строительства частных домов до 3х этажей.
- Газобетонные блоки плотностью D500 прочностью B3.5 имеют коэффициент теплопроводности чуть выше и достаточно высокую прочность, позволяющую укладывать плиты перекрытия прямо на блок с цементным раствором, рекомендуются для строительства частных домов до 5ти этажей.
- Строительство домов более высокой этажности рекомендуется на железобетонных несущих конструкциях с поэтажным бетонированием перекрытий.
- Газобетонные блоки плотностью D600 прочностью B5 имеют более высокий коэффициент теплопроводности и высокую прочность, применяются в основном в строительстве домов с навесными конструкциями вентилируемых фасадов.
Мифы и легенды о газобетоне
Миф первый
Так как при изготовлении газобетона применяется алюминий, то дома построенные из этого материала нельзя назвать экологически чистыми, а известь, содержащаяся в газобетоне, приводит к ржавлению металлической арматуры.
Разобраться в этом вопросе нам помогут представители компании «Кселла-Аэроблок-Центр» бренд YTONG – технический специалист Искров Никита и руководитель отдела маркетинга Дмитрий Бондаренко.
Дмитрий Бондаренко:
– Да, действительно, при производстве газобетона используется алюминиевая паста, но в результате химической реакции в газобетоне не остается металлического алюминия, вступая в реакцию, он окисляется и в итоге образуется оксид алюминия — совершенно безвредное химическое соединение, которое широко используется в посуде и хозяйстве.
Алюминиевая паста добавляется для того, чтобы при реакции с гашеной известью в имеющейся массе компонентов для производства газобетона, образовался водород, который как раз способствует образованию мелких пор и «поднятию» материала.
Алюминий совершенно безвредный материал ведь из него даже изготавливают детскую посуду.
Известь и другие компоненты, такие как песок, вода и алюминиевая паста не содержатся в конечном продукте в чистом виде, они лишь используются при изготовлении. При автоклавной обработке происходит реакция синтеза силикатов, и образуются минералы, которые определяют такие свойства газобетона как долговечность. Тем более что газобетон, приготовленный на цементе и извести имеет щелочную реакцию, что как мы знаем, как раз наоборот препятствует коррозии металла.
Миф второй
Довольно часто приходится слышать высказывание, что газобетон, в отличие от пенобетона, боится воды, а также он гигроскопичен и накапливает влагу, что делает этот материал непригодным для использования кладки стен во влажных помещениях.
Дмитрий Бондаренко:
– Г азобетон обладает незначительной гигроскопичностью, и при высокой влажности в неотапливаемых помещениях стены из ячеистого бетона могут набрать до 10% влаги от своего веса, но в теплый периодвлажность постепенно снижается.
Гигроскопичность – это свойство материалов поглощать – сорбировать влагу из воздуха.
Следует помнить, что сегодня большинство производителей газобетонных блоков производят блоки с закрытыми порами, которые препятствуют распространению влаги.
Также интересно мнение специалистов компании «Билд фаст текнолоджи» бренд DRAUBER начальника отдела продаж Бушина Алексея иглавного технолога Лободенко Евгения.
Лобоенко Евгений:
– Все строительные материалы боятся прямого попадания влаги. Тем не менее, газобетон, впитав влагу, хорошо её и отдаёт. Также на рынке отделочных строительных материалов существует достаточное разнообразие грунтовых гидрофобных пропиток, которые предотвращают попадание влаги в газобетон, при этом, не изменяя его основной характеристики – теплопроводности.
Для защиты газобетона от атмосферных воздействий, достаточно нанести гидрофобные пропитки которые будут препятствовать попаданию влаги в строительный материал. Дальнейшая наружная отделка газобетонной кладки остается на усмотрение хозяина дома, ее можно, и оставить в таком состоянии, а можно для большей эстетичности произвести отделку.
Миф третий
Газобетон требует обязательной защиты от атмосферных воздействий при помощи наружной отделки.
Дмитрий Бондаренко:
– Это, пожалуй, одно из самых популярных заблуждений. Для примера возьмём дом, построенный в Риге, из газобетонных блоков и который вот уже более 70 лет стоит без наружной отделки, и атмосферные воздействия ему нипочем.
Качественный газобетон с большим процентным содержанием тоберморита – долговечный материал, обладающий морозостойкостью 100 циклов, и который может использоваться без наружной отделки целые десятилетия.
Эдуард Галлямов:
– Важно чтобы на построенном из газобетона доме была установлена кровля и закрыты окна, что в значительной степени защищает стены от внешнего воздействия осадков, тогда дом без отделки может стоять несколько лет.
Миф четвёртый
Газобетон является хрупким материалом,идля возведения здания необходимо строительство монолитного ленточного фундамента или цокольного этажа из обычного тяжелого бетона, что влечет за собой немалые расходы.
Дмитрий Бондаренко:
– Строительство дома из газобетона впрочем, как и из любого другого материала требует ответственного подхода. И если при строительстве есть хоть малейшее сомнение в жесткости фундамента, то необходимо принять меры по усилению его конструктивных особенностей.
Одним из наиболее надежных видов фундамента для дома из газобетона является железобетонная плита, обеспечивающая минимальность и равномерность усадочных деформаций. Также основанием для дома может служить монолитный ленточный фундамент на песчанойподушке или столбчатый фундамент, обвязанный монолитным железобетонным поясом.
Так как газобетон обладает низкой устойчивостью к деформирующим нагрузкам на изгиб, то монолитный фундамент минимизирует деформационные нагрузки и предотвращает появление трещин в газобетонных стенах.
Миф пятый
Перейдём к пятому мифу, – который гласит, что для возведения двух-трехэтажного дома нужен газобетон плотность не менее чем 500-600 килограмм на кубометр.
Искров Никита:
– Несущая способность газобетона оценивается не плотностью, а классом прочности на сжатие. Для строительства несущих стен пригоден только конструкционно-теплоизоляционный, либо конструкционный газобетон. Согласно ГОСТ, конструкционно-теплоизоляционным газобетоном является газобетон класса по прочности на сжатие не ниже B1,5 и марки по средней плотности — не выше D700.
Если газобетон марки по средней плотности D400 обладает прочностью на сжатие ниже B1,5, то, конечно же, из него не рекомендуется строить несущие стены, его можно применить, например, в заполнение каркаса.
Миф шестой
Одним из самых распространённых мифов о газобетоне является утверждение, что кладка газобетонного блока на специальный клей дороже, чем на раствор.
Дмитрий Бондаренко:
– Это заблуждение, связано, прежде всего, с тем, что при одинаковом объеме мешка, цементный раствор стоит дешевле, чем клей. Но на практике, кладка на клею требует значительно меньших денежных затрат.
Например: толщина клеевого шва составляет 1-3 мм, толщина цементного раствора составляет 12мм, нетрудно посчитать, что расход клея составляет чуть более 15 кг на 1м3 , а цементного раствора более 156 кг на 1м3.
Кладка газобетонных блоков на наш клей в 7 раз прочнее аналогичной кладки на цементном растворе. Так же, кладка на клей выполняется в разы быстрее по сравнению с цементным раствором.
Бушин Алексей:
– Тонкие швы сокращают не только строительные затраты, но и расходы на поддержание оптимального теплового режима в жилом помещении.
Так как основная часть тепла теряется через «мостики холода» — разрывы в материале стен. А при тонкошовной кладке толщина швов составляет всего 1 – 3 мм.
Миф седьмой
Дом из газобетона недостаточно тёплый и обязательно требует дополнительного утепления.
Бушин Алексей:
– Газобетонный дом при соответствующей толщине стен не нуждается в дополнительном утеплении. В доме из газобетона всегда будет сохраняться благоприятный микроклимат, летом будет прохладно, а зимой потребуется минимальное время для прогрева такого дома с максимальным сохранением тепла.
Например, для Московского региона коэффициент термосопротивления должен быть не менее 3,16 кв.м*С/Вт, и стена из газобетона D 400 толщиной 37,5 см будет соответствовать этим требованиям.
Газобетон благодаря своей пористой структуре сам является утеплителем. Чем меньше плотность, тем меньше и теплопроводность. Дом, построенный из газобетона плотностью D600, будет иметь коэффициент по теплопроводности выше, чем у дома, построенного из газобетона плотностью D400. Соответственно газобетон плотностью D400 будет дольше сохранять тепло в доме.
Эдуард Галлямов:
– Дом из газобетона лучше дышит, чем дом из кирпича, так как у газобетона паропроницаемость в 3 раза лучше, чем у кирпича. Стены из кирпича требуют дополнительного утепления, потому что строить дом из кирпича толщиной стены в 90 см экономически нецелесообразно, а стена из газобетона в 40 см уже не требует дополнительного утепления.
Что в конечном итоге позволяет построить застройщику относительно недорогой, долговечный, экологичный и красивый дом из газобетона.
Узнать больше о строительстве каменных домов пользователи forumhouse.ru могут в этом разделе нашего форума. Подробный рассказ нашей форумчанки о строительстве дома из газобетона можно прочитать здесь. Детальное описание с множеством фотографий всех этапов возведения дома из газобетона доступно по этой ссылке. А ознакомившись с нашим видеосюжетом Вы наглядно увидите, как за полгода можно своими силами построить дом из газобетона и полностью подготовить к проживанию первый этаж.
Блок: 2/2 | Кол-во символов: 11858
Источник: https://www.forumhouse.ru/articles/house/5246
Теплопроводность
Показатель указывает на то количество тепла, которое пропускает опытный образец толщиной в 1 м за единицу времени. Для конструкционных и теплоизоляционных бетонов значения будут разными. Коэффициент теплопроводности газобетона позволяет определить, какой толщины должны быть стены того или иного здания, чтобы обеспечить должный уровень утепления.
Следующая таблица расскажет вам более подробно о теплопроводности газобетона:
Теплоизоляционный | 200 | 0,048 |
250 | 0,06 | |
300 | 0,072 | |
350 | 0,084 | |
Конструкционно-теплоизоляционный | 400 | 0,096 |
450 | 0,108 | |
500 | 0,12 | |
600 | 0,14 | |
700 | 0,17 | |
800 | 0,19 | |
Конструкционный | 900 | 0,22 |
1000 | 0,24 | |
1100 | 0,26 | |
1200 | 0,28 |
Блок: 4/12 | Кол-во символов: 670
Источник: http://stroyres.net/beton/gazobeton/haratkeristiki-i-fizicheskie-svoystva.html
Видео: Как выбрать газосиликатные блоки
Блок: 4/4 | Кол-во символов: 40
Источник: https://srbu.ru/stroitelnye-materialy/20-gazobetonnye-bloki-nedostatki-i-zayavlennye-kharakteristiki.html
Паропроницаемость
Это качество позволяет материалу в какой-то мере впитывать влагу и отдавать ее при изменении температурного режима. Однако в отличие от дерева, где прохождение влаги зависит от направления волокон, в газобетоне влага одинаково накапливается и отдается с обеих сторон блока, то есть, как снаружи, так и внутри здания. Поэтому этот материал приходится защищать.
Однако паропроницаемость стен внутри помещения обеспечивает более здоровый микроклимат. Поэтому это качество газобетона стоит считать достоинством. Следующая таблица и посвящена такой характеристике газобетона.
Теплоизоляционный | 200 | 0,3 |
250 | 0,28 | |
300 | 0,26 | |
350 | 0,25 | |
Конструкционно-теплоизоляционный | 400 | 0,23 |
450 | 0,21 | |
500 | 0,2 | |
600 | 0,16 | |
700 | 0,15 | |
800 | 0,14 | |
Конструкционный | 900 | 0,12 |
1000 | 0,11 | |
1100 | 0,1 | |
1200 | 0,09 |
Блок: 5/12 | Кол-во символов: 812
Источник: http://stroyres.net/beton/gazobeton/haratkeristiki-i-fizicheskie-svoystva.html
Прочность
К главным прочностным характеристикам газобетона относится прочность на сжатие. Для любых ячеистых бетонов минимальная прочность должна соответствовать классу В1,5. Этот минимум разрешается для теплоизоляционных материалов.
Для остальных допустимые значения соответствуют классам В2,6–3, максимум В4. Обозначение указывает на то критическое давление в МПа, при котором материал разрушается, поэтому рассчитанная нагрузка на практике должна быть меньше.
Совсем невелика сопротивляемость газобетона нагрузке на изгиб. Из-за этого фасад из него очень быстро покрывается трещинками, поскольку реагирует на усадку фундамента и подвижки грунта.
Далее речь пойдет о звукоизоляционных, шумовых свойствах газобетона.
Блок: 6/12 | Кол-во символов: 718
Источник: http://stroyres.net/beton/gazobeton/haratkeristiki-i-fizicheskie-svoystva.html
Подведем итоги: разбор минусов газобетона
Основные недостатки газобетона заключаются в восприимчивости к влаге и завышенных показателях морозостойкости. Гигроскопичность бетона снижает теплотехнические свойства газобетонных блоков и приводит к деформациям, способствующим появлению дефектов отделки. Это ограничивает его применение в районах с повышенной влажностью, в сырых помещениях, а также при строительстве фасадов. Во избежание этого перед отделкой необходимо применение дорогостоящего комплекса мер по защите стройматериала от конденсата.
Реальная морозостойкость материала значительно ниже заявляемых значений, что делает нецелесообразным использование газобетона для жилых домов в районах с холодным климатом. Сильное снижение теплового сопротивления при увлажнении заставляет увеличивать толщину стен, что снижает преимущества газобетона по сравнению с другими стройматериалами.
Изъяны в механической прочности газобетона требуют строительства дорогостоящих видов фундамента и применения специальных крепежных элементов. Строительство домов с несколькими этажами не допускается или требует специальных упрочняющих операций. Наложение защитной или декоративной штукатурки вызывает осложнение из-за растрескивания.
Недостатки газобетона значительно ограничивают его применение при строительстве жилых домов и бань. В то же время преимущества позволяют широко применять его при возведении хозяйственных построек, ограждений и других строений.
При близком рассмотрении вопроса о заявленной низкой стоимости газобетона и гарантированной долговечности выходит, что эти характеристики оказываются значительно завышенными производителями.
При соблюдении норм в отношении показателей теплосопротивления заявленная производителями кладка толщиной в 380 мм является недостаточной. Игнорирование нормативов ведет к повышенному расходу энергии на отопление и кондиционирование. Для того чтобы здание соответствовало всем стандартам, толщину кладки необходимо увеличить как минимум до 640 мм. При этом максимальная толщина газоблока составляет 500 мм.
Еще одним недостатком газобетонной кладки является необходимость возведения монолитного ленточного фундамента, использование которого ведет к существенному удорожанию строительных работ. Без такого фундамента риск появления усадочных деформаций и возникновения массивных трещин в кладке значительно возрастает.
При изучении вышеописанных фактов напрашивается вывод, что такие достоинства свойства газобетонных блоков, как высокие показатели теплоизоляции и несущая способность перекрытий из газобетона, являются значительно преувеличенными и носят исключительно навязчивый рекламный характер. В защиту газосиликата хочется сказать, что на данный момент идеальных стройматериалов не существует, и каждый из них имеет как свои минусы, так и неоспоримые достоинства. Хотя, например, если сравнить свойства газобетонных блоков со свойствами арболита, то у последнего явное преимущество!
По материалам: http://ostroymaterialah.ru/smesi/gazobeton-nedostatki.html
http://o-cemente.info/vidi-betonnih-smesej/gazobetonnye-bloki-dostoinstva-i-ned.html
Блок: 3/3 | Кол-во символов: 3091
Источник: https://stavba.ru/materialy/gazobeton/svojstva-gazobetona.html
Звукоизоляция
Пористая структура гасит звук при прохождении сквозь нее. Газобетон, благодаря своим звукоизолирующим свойствам, является неплохим звукоизолятором, однако это качество ГОСТ не регулирует.
Для наиболее часто используемых в частном строительстве материалов эти показатели таковы.
120 | 180 | 240 | 300 | 360 | |
D500 | 36 | 41 | 44 | 46 | 48 |
D600 | 38 | 43 | 46 | 48 | 50 |
Для стен между квартирами индекс изоляции должен достигать 50, а, значит, толщина стены из бетона марки D600 должна быть 36 см. Для перегородок внутри квартиры индекс должен быть не ниже 41, то есть, толщина стены должна быть 18 см.
Блок: 7/12 | Кол-во символов: 639
Источник: http://stroyres.net/beton/gazobeton/haratkeristiki-i-fizicheskie-svoystva.html
Недостатки холодоустойчивости
Типы кладки стен из газобетона.
Высокая морозостойкость газобетонных блоков в фасадных стенах на практике не подтверждается. Это во многом объясняется водопоглощением и накоплением воды в порах материала. При этом вода при низких температурах в полостях замерзает, а, расширяясь, создает внутреннее напряжение в блоках. Фактическая морозостойкость газобетонных блоков не превышает 25 циклов (норма — не менее 50 циклов). Это ограничивает применение газобетона для фасадных стен или требует дополнительной защиты.
Не всегда положительно сказывается и свойство газобетона, связанное с малой инерцией нагрева. Это хорошо, когда надо отопить помещение. Так, газобетонные блоки обеспечивают подъем температуры внутри помещения от 0 до 20 градусов за 1,5-2 часа, что по сравнению с другими материалами считается очень быстрым. Но беда в том, что и остывание помещения при прекращении обогрева происходит с той же скоростью.
Блок: 7/9 | Кол-во символов: 949
Источник: https://ostroymaterialah.ru/smesi/gazobeton-nedostatki.html
Морозостойкость
Определяет количество полных циклов замораживания и оттаивания, которое может перенести материал без разрушения. Газобетон – пористый бетон с очень высоким уровнем водопоглощения, поэтому его показатели по морозостойкости не слишком велики.
Регулируется этот параметр по его назначению и предполагаемым условиям эксплуатации:
- F15 – для перегородок и внутренних стен;
- F25 – для наружных стен.
Блок: 8/12 | Кол-во символов: 408
Источник: http://stroyres.net/beton/gazobeton/haratkeristiki-i-fizicheskie-svoystva.html
Пожаробезопасность
Газобетон является одним из наиболее безопасных материалов: он относится к классу негорючих веществ. Он не поддерживает горения и не образует дыма при воздействии открытого огня и температуры.
Блок: 9/12 | Кол-во символов: 212
Источник: http://stroyres.net/beton/gazobeton/haratkeristiki-i-fizicheskie-svoystva.html
Усадка
- Автоклавный газобетон отличается не только точной геометрией, но и ее неизменностью. По ГОСТ усадка блоков допускается не более чем 0,5 мм/м.
- У неавтоклавного газобетона показатели хуже – до 2–3 мм/м.
Блок: 10/12 | Кол-во символов: 208
Источник: http://stroyres.net/beton/gazobeton/haratkeristiki-i-fizicheskie-svoystva.html
Экологичность
Ячеистые бетоны относятся к самым экологичным строительным материалам, коэффициент их – 2. Для сравнения дереву присвоен показатель 1.
Однако это справедливо только по отношению к неавтоклавному газобетону. Автоклавный требует повышенного расхода энергии при производстве, что несколько ухудшает его показатели. Однако безвредность готового изделия для человека и окружающей среды абсолютна.
Газобетон – строительный материал, полностью оправдывающий себя в своей области. При этом разнообразие свойств бетонов разной категории значительно эту область расширяет.
Поделитесь с друзьями в социальных сетях:
И подписывайтесь на обновления сайта в Контакте, Одноклассниках, , Google Plus или .
Блок: 12/12 | Кол-во символов: 721
Источник: http://stroyres.net/beton/gazobeton/haratkeristiki-i-fizicheskie-svoystva.html
Количество использованных доноров: 5
Информация по каждому донору:
- http://stroyres.net/beton/gazobeton/haratkeristiki-i-fizicheskie-svoystva.html: использовано 9 блоков из 12, кол-во символов 5174 (23%)
- https://ostroymaterialah.ru/smesi/gazobeton-nedostatki.html: использовано 2 блоков из 9, кол-во символов 1772 (8%)
- https://srbu.ru/stroitelnye-materialy/20-gazobetonnye-bloki-nedostatki-i-zayavlennye-kharakteristiki.html: использовано 1 блоков из 4, кол-во символов 40 (0%)
- https://www.forumhouse.ru/articles/house/5246: использовано 1 блоков из 2, кол-во символов 11858 (53%)
- https://stavba.ru/materialy/gazobeton/svojstva-gazobetona.html: использовано 2 блоков из 3, кол-во символов 3649 (16%)
(PDF) Материалы, производство, свойства и применение легкого пористого бетона: Обзор
становится возможным с заменой
объема гидроцементовснижает выбросы углекислого газа.
(Awang and Noordin, 2002) [22] провели исследование для
по изучению влияния щелочно-стойкого стекловолокна на прочность
на сжатие легкого пенобетона.
Щелочно-стойкое стекловолокно было добавлено к пенобетонной смеси
с использованием трех разных процентных соотношений (0.2%, 0,4%, 0,6%).
Экспериментальные данные показывают, что увеличение содержания волокна на
может дать более прочный пенобетон. Результаты испытаний
на сжатие, расщепление и изгиб
прочности пенобетона, армированного стекловолокном, показывают, что
значительно увеличивается при увеличении процентного содержания стекловолокна
. (Na Ayudhya, 2011) [23] исследовали прочность на сжатие и растяжение
автоклавного газобетона
(AAC), содержащего перлитный заполнитель и полипропиленовое волокно
, подвергнутых воздействию высоких температур.К смеси добавляли
полипропиленовых (ПП) волокон с содержанием 0, 0,5, 1, 1,5 и 2%
по объему. Результаты показали
, что прочность на сжатие и растяжение при растяжении
без нагрева для волокна из ПП, содержащего ААС, на
не выше, чем у волокон без ПП. Кроме того,
присутствие волокна PP не было более эффективным для
остаточной прочности на сжатие, чем прочность на разрыв
при расщеплении.(Салман и Хассан, 2010) [9] говорят, что плотность
и прочность на сжатие газобетона уменьшается с
увеличением процентного содержания алюминиевого порошка (Al). Добавление
Al также увеличивает объем газобетона.
Это было между (13,3-50,8)% и (18,7-61,3)% для отверждения на воздухе
и паром соответственно, когда Al был в пределах (0,1-
0,4)%. Результаты испытаний показали, что наилучшее процентное содержание
Al составляет 0,2% от веса цемента, что дает плотность
1389 кг / м3 и прочность на сжатие 0.26 МПа для отверждения на воздухе
и 1431 кг / м3 и 0,55 МПа для отверждения паром.
IV. ПРЕИМУЩЕСТВА И ОБЛАСТИ ПРИМЕНЕНИЯ
ЛЕГКИЙ БЕТОН
ПЕРИОДИЧЕСКИЙ
Ячеистый бетон считается более прочным
по сравнению с традиционными изоляционными материалами, особенно
с учетом потенциального химического / пожарного воздействия, такого как
на производственных объектах [24]. Легкий бетон
имеет очевидные преимущества более высокого отношения прочности к весу,
лучшей способности к деформации при растяжении, более низкого коэффициента теплового расширения
и улучшенных тепло- и звукоизоляционных характеристик
из-за наличия воздушных пустот в бетоне [25]. [26].
Снижение собственного веса конструкции
материалов с использованием легкого бетона может привести к уменьшению на
поперечного сечения бетонных конструктивных элементов
(колонны, балки, плиты и фундамент). Также уменьшение статической нагрузки на
может снизить передаваемую нагрузку до
ифундаментов и несущей способности почвы [4], [27].
Впоследствии стальная арматура может быть минимизирована за счет
легкости.Блоки AAC могут быть уместны в
разных частях здания; его можно использовать как в ненесущих несущих стенах
, так и в несущих стенах [17]. Автоклавные газобетонные блоки
могут применяться в строительстве
инженерных (компенсация фундамента, засыпка трубопровода
, изоляция кровли и т. Д.), Но также можно получить результаты применения
на объектах инфраструктуры (таких как мост
и т. Д.) засыпка водопропускных труб, уширение дороги, устранение неровностей
неровностей моста на насыпи мягкого основания [28].
V. ВЫВОДЫ
Легкий пенобетон отличается от обычного бетона
некоторыми материалами и свойствами смеси. Газобетон
легкий бетон не содержит грубых заполнителей,
и обладает многими преимуществами, такими как низкая плотность с более высокой прочностью на
по сравнению с обычным бетоном,
с улучшенной тепло- и звукоизоляцией, уменьшенной статической нагрузкой
в массе приводят к ряду преимуществ в уменьшении
элементов конструкции и уменьшении передаваемой нагрузки на фундаменты
и несущей способности.Пенобетон
отличается по агенту образования воздушных пустот по сравнению с автоклавным газобетоном
. Воздушные пустоты во вспененном бетоне
, образованные пенообразователем, эта операция является физической обработкой
. Против воздушных пустот в автоклавном газобетоне
, образованных добавлением алюминиевого порошка к другим материалам
и взаимодействием между ними, и эта операция
представляет собой химическую обработку.Воздушные пустоты — это
однородного распределения внутри легкого пенобетона
. Прочность на сжатие пенобетона
может быть увеличена до структурной прочности по сравнению с
пенобетона из автоклавного пенобетона. Легкий пористый бетон
учитывает экономию материалов и расход
побочных продуктов и отходов, таких как зола-унос
.
ССЫЛКИ
[1] A.М. Невилл и Дж. Дж. Брукс, Concrete Technology, второе издание
, Prentice Hall, Pearson Education, 2010, стр. 351-352.
[2] Л. Б. Йен, «Исследование проникновения воды в пенобетон», M.S.
диссертация, Национальный университет Сингапура, 2006.
[3] З. Ли, Advanced Concrete Technology, Хобокен, Нью-Джерси:
John Wiley & Sons, 2011, стр. 219-220.
[4] Сулейман С.Х. Водопроницаемость и карбонизация вспененного бетона
, М.S. thesis, University Tun Hussein Onn Malaysia,
2011.
[5] KC Brady, GRA Watts и MR Jones, Спецификация для пенобетона
, Великобритания: Highway Agency, 2001.
[6] F. Зулкарнайн и М. Рамли, «Характеристики смеси пенобетона
с дымом кремнезема для общего жилищного строительства»,
European Journal of Technology and Advanced Engineering
Research, vol. 1, вып. 2. С. 18-28, 2011.
[7] KJ Byun, HW Song и SS Park, «Разработка конструкционного легкого пенобетона
с использованием вспененного полимера
», ICPIC-98, 1998.
[8] КАМ Гелим, «Механические и физические свойства золы уноса
Пенобетон»МС. дипломная работа, факультет гражданского строительства и инженерии окружающей среды
, Университет Тун Хусейн Онн
Малайзия (UTHM), 2011.
[9] М. М. Салман и С.А. Хассан, «Эмпирические формулы для
оценки некоторых физических свойств газобетона, полученного
путем добавления алюминиевого порошка», Journal of Engineering and
Development, vol. 14, вып. 4, 2010.
[10] Р. Боггелен. Безопасное дозирование алюминия на заводах AAC. Aircrete
Europe B.V., Oldenzaal, Нидерланды [Интернет]. В наличии:
http: // aircrete-
europe.ru/images/download/D.R.van_Boggelen_Safe_aluminium
_dosing_in_AAC_plants.pdf
[11] Э. К. Намбьяр и К. Рамамурти, «Характеристики пенобетона с воздушными пустотами
», Цемент и бетон
Research, vol. 37, нет. 2, pp. 221-230, 2007.
[12] Дж. Ньюман, Б.С. Чу, П. Оуэнс, Advanced Concrete
Technology Processes, Elsevier Ltd, 2003, часть 2, стр. 2 / 7-2 / 9.
[13] Соми С. Влияние влаги на свойства автоклавного газобетона
, М.С. Диссертация, Университет Восточного Средиземноморья,
Северный Кипр, 2011.
[14] Э. Р. Доминго, «Введение в автоклавный газобетон
, включая проектные требования с использованием расчетов на прочность», M.S. диссертация,
Государственный университет Канзаса, Манхэттен, Канзас, 2008.
156
Журнал материаловедения и инженерии Vol. 2, № 2 декабрь 2014 г.
© 2014 Инжиниринг и Технологии Издательство
СТРУКТУРА И СВОЙСТВА ПЕРИОДИЧЕСКОГО БЕТОНА: ОБЗОР
Ячеистый бетон относительно однороден по сравнению с обычным бетоном, поскольку он не содержит фазы крупного заполнителя, но демонстрирует значительные различия в своих свойствах.Свойства газобетона зависят от его микроструктуры (система пустот-паста) и состава, на которые влияют тип используемого вяжущего, методы порообразования и отверждения. Хотя изначально газобетон задумывался как хороший изоляционный материал, интерес к его структурным характеристикам возродился в связи с его меньшим весом, экономией материала и возможностью крупномасштабного использования отходов, таких как пылевидная топливная зола. Целью данной статьи является классификация исследований свойств газобетона с точки зрения физических (микроструктура, плотность), химических, механических (прочность на сжатие и растяжение, модуль упругости, усадка при высыхании) и функциональных (теплоизоляция, перенос влаги). , долговечность, огнестойкость и звукоизоляция) характеристики.(А)
- Наличие:
- Корпоративных авторов:
Эльзевир
The Boulevard, Langford Lane
Kidlington, Оксфорд объединенное Королевство OX5 1 ГБ - Авторов:
- НАРАЯНАН, N
- Ramamurthy, K
- Дата публикации: 2000
Язык
Информация для СМИ
Предмет / указатель терминов
Информация для подачи
- Регистрационный номер: 00799821
- Тип записи: Публикация
- Агентство-источник: Транспортная исследовательская лаборатория
- Файлы: ITRD
- Дата создания: 6 октября 2000 г. 00:00
Характеристики легкого ячеистого бетона и влияние на механические свойства
Abstract
В этом исследовании изучалась структура пор и ее влияние на механические свойства легкого ячеистого бетона (LCC), чтобы понять более подробные характеристики такой структуры.В рамках исследования отдельно использовались сканирующие электронные микроскопы окружающей среды (ESEM) и промышленная камера для макросъемки высокого разрешения (HD) для захвата и сравнения изображений образцов. Физические свойства структуры поры, включая площадь поры, размер, периметр, подходящий эллипс и дескрипторы формы, были изучены на основе технологии обработки изображений и программных приложений. В лаборатории были приготовлены образцы трех различных плотностей (400, 475 и 600 кг / м 3 ).Во-первых, было исследовано влияние плотности на характеристики поровой структуры; Кроме того, были испытаны механические свойства (прочность на сжатие, модуль упругости и коэффициент Пуассона, прочность на изгиб и предел прочности при растяжении LCC). Были проанализированы взаимосвязи между характеристиками пор, плотностью и механическими свойствами. На основании результатов лабораторных испытаний — сравнений, проведенных между образцами с высокой плотностью и образцами с низкой плотностью — было обнаружено существенное различие в размере пузырьков, толщине и неравномерности пор.Кроме того, увеличение плотности сопровождается улучшением механических свойств, и основными влияющими факторами являются толщина твердой части и форма пузыря. Чем толще твердая часть и более правильные поры LCC, тем лучше механические свойства.
Ключевые слова: легкий ячеистый бетон (ЛКБ), пористая структура; Обработка изображения; дескрипторы формы; механические свойства
1. Введение
Легкий ячеистый бетон (LCC) представляет собой пористый материал с типичной плотностью от 300 до 1800 кг / м 3 [1,2,3,4,5,6], который содержит однородная структура воздушных пузырьков в смеси.Другие академические термины, описывающие этот материал, — пенобетон [7], пенобетон низкой плотности или ячеистый легкий бетон и т. Д. [8,9]. Впервые он был запатентован в 1923 г. [10] как материал для заполнения пустот. Текстурная поверхность и микроструктурные ячейки делают его широко используемым в областях теплоизоляции [11], звукопоглощения [12] и огнестойкости [13]. Он также используется для заполнения опор мостов [14], фундаментов зданий [15,16] и буферных систем аэропорта [17]. За последние 30 лет LCC широко использовался для заливки насыпей [4], ремонта канав, подпорных стен [18], засыпки опор моста [19], плитных конструкций бетонных полов [20] и изоляции жилищ [21].В настоящее время LCC быстро продвигается как строительные материалы для гражданского строительства с высокой текучестью, низким содержанием цемента и высокой теплоизоляцией [13,22].
Легкий ячеистый бетон широко используется в строительстве в разных странах, таких как Германия, США, Бразилия, Великобритания и Канада [23]. Хотя есть ограниченные исследования относительно практического применения LCC в гражданском строительстве, несколько проектов строительства дорог были выполнены с LCC из-за его преимуществ, упомянутых выше.Например, LCC использовался в качестве материала основания в промышленной зоне в Великобритании для замены исходного слоя, состоящего из торфа. Иллинойс также применяет LCC в дорожном строительстве, чтобы обеспечить решение проблемы мягкой органической подстилающей почвы, и это приносит пользу подрядчику за счет снижения удельных затрат, сокращения времени строительства и более высокого качества материала [19]. LCC также можно найти в Канаде, и он использовался в качестве материала основания для автобусных полос сельской дороги и шоссе [24].
Свойства LCC для применения в гражданском строительстве были глубоко изучены.Важнейшей задачей при производстве LCC является контроль природы, размера и распределения пор, поскольку характеристики пор являются ключевым фактором для определения плотности и прочности LCC [7,21,23,25]. За последние несколько лет было проведено множество исследований, направленных на улучшение природы LCC и его использования в строительных приложениях [9,26,27,28,29,30]. Эти исследования сосредоточены на взаимосвязи между микроструктурой и механическими свойствами LCC. В большинстве исследований анализировалась взаимосвязь микроструктуры с прочностью на сжатие и модулем упругости, которые являются важными факторами для применения LCC в строительстве инфраструктуры.Эти поры LCC состоят из межслоевых пор / пространств, пор геля, капиллярных пор и воздушных пустот с размерами пор, варьирующимися от нанометрового масштаба до миллиметрового [31]. Nguyen et al. [32] изучали влияние пористой структуры и свойств раствора на поведение геополимерного пенобетона. Результаты показали, что размер пор оказывает сильное влияние на сопротивление разрушению материала. Batool et al. [33] изучили особенности распределения размеров пор в LCC на основе цемента. Результаты показали, что чем уже распределение пор, тем больше проводимость и меньше плотность.Исследование показало, что прочность LCC уменьшается с увеличением пустот [34,35]. Некоторые исследователи также исследовали модели прогнозирования прочности на сжатие. Эти результаты в основном основаны на искусственной нейронной сети [36], машине экстремального обучения и эмпирических моделях, основанных на регрессионном анализе [37]. Кирсли и Уэйнрайт [28] исследовали взаимосвязь между пористостью и прочностью на сжатие. Они представили математические модели, отражающие влияние пористости на прочность материала на сжатие.Wee et al. [38] предложили параметр коэффициента интервала для характеристики системы воздушных пустот в бетоне. Это может быть напрямую связано со средним размером воздушных пустот. Результаты показали, что уменьшение коэффициента зазора и увеличение среднего размера воздушных пустот привело к снижению прочности на сжатие. Кроме того, Намбиар и Рамамурти [5] вместе с Хилалом и соавт. [1] исследовали структуру пор внутри LCC и продемонстрировали, что пористость недостаточна для регулирования характеристик LCC.Другие характеристики пор, такие как размер пор, распределение по размерам, форма и толщина ячеек, также следует учитывать для более детального понимания материала LCC.
Хотя LCC применялся в дорожном строительстве, полное и подробное руководство по LCC все еще отсутствует. Механические свойства LCC при низкой удельной плотности (от 400 до 600 кг / м 3 ) требуют тщательного изучения. Взаимосвязь между микроструктурой и механическими свойствами LCC также требует дальнейшего анализа.
Для получения микроструктуры LCC широко использовались электронные микроскопы (EM), такие как вторичная электронная (SE) и рентгеновская компьютерная томография (CT X-ray) [1,39,40,41,42 , 43]. SE можно использовать для получения изображений с деталями поверхности, а компьютерную томографию можно использовать для просмотра трехмерной внешней формы образцов. Самым большим преимуществом ЭМ является то, что они имеют более высокое разрешение и большее увеличение (до 2 миллионов раз). Хотя у них также есть ряд недостатков: они дороги; подготовка образцов часто бывает более сложной; требования к пространству высоки, а операторам требуется дополнительное обучение и опыт.Все эти упомянутые выше недостатки ограничивают их гибкость в использовании. По сравнению с ЭМ, хотя оптический микроскоп (ОМ) имеет значительно более низкое разрешение, он дешев в приобретении, прост в эксплуатации и мал в переноске. Некоторые исследователи использовали камеру, подключенную к оптическому микроскопу, для получения изображений пенобетонных смесей и идентифицировали воздушные пустоты диаметром более 20 мкм [1,40]. Это означает, что ОМ можно использовать для фиксации микроструктуры LCC.
В этом исследовании корреляция между характеристиками пор и механическими свойствами LCC была исследована с использованием как технологии обработки изображений, так и экспериментальных подходов.Влияние локальных характеристик пор на физические свойства было исследовано на образцах LCC с различной плотностью на уровне микроструктуры. Для этого был изготовлен набор образцов LCC с низкой плотностью с использованием пенообразователя Provoton. Как правило, поры в LCC закрываются с помощью методов предварительного вспенивания или смешанного вспенивания [1,4]; Образцы LCC, использованные в этом исследовании, были получены с использованием метода предварительного вспенивания.
Характеристики пор, включая распределение пор в образцах LCC, были описаны с помощью сканирующего электронного микроскопа окружающей среды (ESEM), который использовался для получения четких изображений.Машинное обучение использовалось для определения пор, а затем метод сегментации водораздела [44] был использован для сегментации и идентификации пор неправильной формы. Наконец, были получены характеристики пор (площадь, размер и форма). Для удобного и быстрого захвата структуры пор была разработана система промышленных HD-камер (IHDCS), которая использовалась вместо ESEM для получения образцов изображений пористой структуры в этом исследовании.
Были испытаны механические свойства LCC с различной плотностью, включая прочность на сжатие, модуль упругости, прочность на изгиб и прочность на растяжение при раскалывании.Затем была исследована взаимосвязь между механическими свойствами и характеристиками пор (то есть площадью пор, распределением по размерам и формой).
2. Подготовка образцов LCC и механические испытания
2.1. LCC образцы
LCC материалы с различной плотностью готовятся для исследования влияния характеристик пор на механические свойства. CEMATRIX Inc. Canada (Калгари, Альберта, Канада) предоставила все тестируемые образцы LCC, которые были различной плотности.Плотность образцов, используемых в этом исследовании, составляет 400 кг / м 3 , 475 кг / м 3 и 600 кг / м 3 , и каждый образец обозначается как D400, D475 и D600 соответственно. Вспененные образцы создаются методом предварительного вспенивания, при котором предварительно вспененные пены добавляются в базовую смесь цементного раствора до достижения заданной плотности. Базовые смеси были составлены путем смешивания портландцемента общего назначения, шлака NewCem марки 80 [45] и воды. Состав представляет собой 80% цемента на 20% шлака по массе, а отношение воды к вяжущему равно 0.5. Плотность базовой смеси 1823 кг / м 3 3 .
показывает образцы LCC с разной плотностью. В исследовании использовались образцы двух типов: цилиндрические и балочные. Здесь эти образцы, которые используются для измерения характеристик структуры пор, получают путем нарезки образцов пучка. Сначала для захвата изображений образцов использовался модуль промышленной HD-камеры, подключенный к компьютеру, а затем были изучены характеристики пор, такие как количество, площадь, периметр и дескрипторы формы (округлость, соотношение сторон, округлость и плотность). .После этого все образцы были разрезаны на 10-миллиметровые кубы для получения изображений с помощью сканирующего электронного микроскопа для получения изображений ESEM высокого разрешения с оптимизированным размером образца. Изображения, полученные с помощью ESEM, который представляет собой FEI Quanta 250 FEG в лаборатории Watlab Университета Ватерлоо, также использовались для изучения характеристик пор. Результаты изображений ESEM сравнивались с результатами изображений промышленных HD-камер.
Образцы легкого ячеистого бетона различной плотности.
2.2. Метод испытания механических свойств LCC
LCC — относительно новый материал, и в настоящее время в Канаде отсутствуют стандарты испытаний для него.Большинство лабораторных испытаний были выполнены в соответствии со стандартными процедурами, указанными в стандартах ASTM или AASHTO. В связи с отсутствием стандартных протоколов испытаний для LCC, методы испытаний, которые были разработаны для других материалов, которые аналогичны LCC в различных контекстах, были приняты на основе передовой практики или мнений экспертов. В этом исследовании напряжение сжатия, модуль упругости и коэффициент Пуассона, прочность на изгиб и прочность на разрыв LCC при раскалывании были протестированы в лаборатории Центра дорожных и транспортных технологий (CPATT) Университета Ватерлоо с использованием системы испытаний материалов.Перед тестированием образцы выдерживали в течение 28 дней во влажной камере Университета Ватерлоо.
Прочность на сжатие была измерена на четырех цилиндрических образцах Φ 75 мм × 150 мм (диаметр × высота), указанных в стандарте ASTM C495 / C495M — Стандартный метод испытаний прочности на сжатие легкого изоляционного бетона [46] для каждой плотности.
Модуль упругости и коэффициент Пуассона были измерены в соответствии со стандартом ASTM C469 / C469M — Стандартный метод испытаний статического модуля упругости и коэффициента Пуассона бетона при сжатии [47].Стандартный размер образца Φ 150 мм × 300 мм. Всего было протестировано по три образца на каждую плотность.
Прочность на изгиб была испытана с использованием простых балок с нагрузкой в третьей точке, и стандарт использования был ASTM C78 / C78M [48]. Размеры образцов составляли 100 мм × 100 мм × 400 мм, по три образца на каждую плотность.
Прочность на растяжение LCC при раскалывании также была испытана в качестве стандарта ASTM C496 / C496M [49]. Были использованы четыре образца каждой плотности, размер цилиндрических образцов Φ 150 мм × 300 мм.
показывает экспериментальные установки LCC.
Экспериментальные стенды LCC. ( a ) Испытание на прочность при сжатии. ( b ) Испытание модуля упругости. ( c ) Испытание модуля на разрыв. ( d ) Испытание на растяжение при раскалывании.
3. Система захвата изображений и методология обработки изображений
3.1. Industrial HD Camera System (IHDCS)
Растровая электронная микроскопия подходит для анализа структуры пор и микроструктуры пенобетона [50].Он позволяет получать четкие фотографии пор и помогает анализировать характеристики пор. Большинство ESEM способны сканировать материалы изображений шириной от 1 см до 5 микрон; однако иногда он бывает недостаточно большим. Благодаря развитию технологий камеры для макросъемки представляют собой привлекательное решение по сравнению с традиционными большими ESEM, которые обычно используются в университетских центрах микроскопии. В этом исследовании была разработана система промышленных HD-камер (IHDCS) для удобного и быстрого захвата структуры пор.Система состоит из модуля захвата (модуль промышленной камеры для макросъемки HD), части освещения (светодиодный свет), части передачи (соединительные кабели) и компонента управления (ноутбук). Модуль захвата и осветительная часть закреплены на верхней части цилиндрической рамы и соединены с портативным компьютером кабелями. Модуль камеры для макросъемки HD, ZJHY-179-R-01 AF, производится китайской компанией Ceyuan Inc., его параметры показаны в. и отдельно показать систему захвата и захваченные изображения.
Промышленная система захвата изображений для макросъемки высокой четкости.
Изображения образцов, захваченных IHDCS.
Таблица 1
Параметры модуля промышленной HD-камеры.
Название | Параметр и описание | Название | Параметр и описание | ||||||
---|---|---|---|---|---|---|---|---|---|
Размер модуля Фокус | 38 мм × 38 мм × 6 мм | Чувствительность | 4 TBD | 4 TBD | Ф / НО | 2.5 | |||
Расстояние до объекта | 5 см-бесконечность | EFL | 4,16 мм | ||||||
Power Тип датчика | Питание по шине USB | BFL | 3,4 мм | IMD | 80 ° | ||||
Размер активной матрицы | 3264 × 2448 | ТВ-искажение | <1,2% | ||||||
Размер пикселя | 1,4 мкм × 1,4 мкм | ИК-фильтр | 650 ± 10 нм | 650 ± 10 нм | Максимальное изображение15 кадров в секунду | 3264 × 2448, 2592 × 1944 | Фиксированный узор шума | <0.03% | |
30 кадров в секунду | 1920 × 1080, 1280 × 720 |
показывает изображения пор образцов, захваченных IHDCS, с разной плотностью. Можно заметить, что по сравнению с образцами с высокой плотностью (D600) размер пузырьков образцов с низкой плотностью (D400 и D475) более изменчив. Чаще всего пузырьки большого размера образуются путем слияния соседних пузырьков небольшого размера.
3.2. ESEM Imaging Method
В этом исследовании для более детального изучения характеристик пор образцов используются изображения с помощью сканирующего электронного микроскопа (ESEM) для изучения размеров пор и распределения LCC.Образцы представляют собой кубики размером 1 см. показывает вторичные электронные изображения образцов LCC, выполненные ESEM. На этих изображениях идентифицированы многочисленные сферические поры разного размера в каждом образце. По сравнению с пузырями более четкие края на изображении ESEM. Подобно результатам IHDCS, размеры пор образцов D400 и D475 более изменчивы по сравнению с D600. В частности, много пузырьков в D400 соединяются, образуя неправильные пузырьки. Кроме того, толщина между порами у D600 явно больше, чем у D400 и D475.
ESEM-изображения с разной плотностью.
3.3. Методология обработки изображений
Программное обеспечение FiJi ImageJ [51] использовалось для обработки изображений сфотографированных LCC. FiJi — это пакет для обработки изображений, в который входит множество плагинов, облегчающих научный анализ изображений. В этом исследовании плагин Trainable Weka Segmentation (TWS) использовался для сегментации структуры пор LCC. TWS — это проект с открытым исходным кодом, который сочетает в себе набор алгоритмов машинного обучения с набором выбранных функций изображения для создания сегментации на основе пикселей.Во-первых, отдельно были выделены поры и сплошная область образца LCC, которые использовались для обучения и получили подходящий классификатор. После того, как классификатор был получен, его использовали для классификации пор и твердой области и получили результат сегментации TWS, который представляет собой 8-битное цветное изображение. Затем было выбрано пороговое значение на основе метода Оцу [52] для преобразования изображения в двоичное изображение. На двоичном изображении черные части представляют собой пустоты или поры, а белые части представляют твердую часть.Кроме того, для повышения качества сегментации изображений использовался метод сегментации водораздела. Таким образом, контактирующие поры могут быть успешно сегментированы. Составное изображение исходной сегментации и результата сегментации водораздела использовалось для проверки эффекта сегментации (более подробную информацию можно найти в разделе). Результат сегментации водораздела был использован для получения характеристик поры для последующего анализа.
Процедура обработки изображения.
4. Результаты и анализ
4.1. Анализ характеристик поры ESEM
На основе программного обеспечения ImageJ легко получить параметры поры, такие как площадь, периметр, первичная ось и вторичная ось наиболее подходящего эллипса и дескрипторов формы (округлость, округлость и плотность). Во-первых, была рассчитана сила взаимосвязи между каждыми двумя параметрами, и результаты показаны в.
Тепловая карта результата коэффициента корреляции.
Тепловая карта полезна для отображения дисперсии по нескольким переменным, отображения того, похожи ли какие-либо переменные друг на друга, а также для определения наличия между ними каких-либо корреляций.Число в каждой ячейке показывает коэффициент корреляции каждых двух параметров. Диапазон значений от -1,0 до 1,0. Если корреляция равна 1,0, это показывает идеальную положительную взаимосвязь. Если корреляция равна -1,0, это также означает идеальную отрицательную корреляцию двух параметров. Независимо от идеальной отрицательной или положительной корреляции, все они показывают, что параметры имеют сильную корреляцию. Когда корреляция равна нулю, это означает, что между двумя параметрами нет никакой связи. В этом исследовании результаты корреляции были преобразованы в неотрицательные значения, которые использовались для рассмотрения корреляции между различными параметрами.Поскольку результаты для разных образцов имеют стабильную тенденцию, в качестве примера показан результат D475. В, расходящийся цветовой градиент, определяемый тремя оттенками (от синего до белого и красного), сделал нижнюю и верхнюю границы диапазона визуально различимыми. Увеличение оттенков красного означает более сильную корреляцию между двумя параметрами. Напротив, увеличение оттенков синего означает более слабую корреляцию. Очевидно, что параметры площади поры, периметра, большой и малой оси сильно коррелируют между собой. Их наименьшее значение коэффициента корреляции равно 0.88. Это означает, что тренды площади пор, периметра, большой и малой оси очень согласованы. Целесообразно принять тенденцию изменения площади пор, чтобы представить таковые из трех других параметров. Хотя дескрипторы формы (округлость, округлость и твердость) имеют высокую корреляцию между собой, максимум корреляции составляет менее 0,8. Это означает, что тенденция изменения дескрипторов формы имеет определенные отличия. Тенденцию изменения дескрипторов форм лучше рассматривать отдельно.Поэтому типичные свойства — площадь пор, округлость и твердость — были учтены в последующих анализах.
4.1.1. Размер пор и толщина твердой детали
показывает размер пор образцов с различной плотностью. а ясно показывает, что образцы D400 и D475 имеют аналогичное распределение, которое отличается от такового для D600. Во-первых, количество пор D400 и D475 более чем в два раза больше, чем у D600. Порядок номеров пор — D400> D475> D600.Хотя в образцах D400 и D475 пор больше, чем в D600, большинство из них имеют небольшой размер. b показывает, что более 70% пор в D400 и D474 имеют размер менее 200 мкм, в то время как процентное содержание D600 составляет лишь около 36%. С другой стороны, в D400 и D475 также имеется значительное количество пор размером более 200 мкм. К тому же номер такой же, как в D600. Следовательно, разница в размере пор у D400 и D475 выше, чем у D600.
Блок-диаграмма и совокупный частотный анализ Эквивалентного радиуса.( a ) Рамочная диаграмма эквивалентного радиуса. ( b ) Суммарная частота радиуса поры.
представляет результаты средней толщины твердой части в образцах. Для получения средней толщины твердой части, во-первых, по результатам сегментации водораздела были инвертированы бинарные изображения образцов, которые использовались для расчета общей площади твердых частей. На инвертированных двоичных изображениях белые области представляют собой поры, а черная область — сплошная часть, как показано на рисунке а.Затем перевернутое изображение было скелетонизировано, как показано на b. Можно получить каркас твердой части, который считался примерно равным длине твердой части. После получения общей площади и длины твердой части была рассчитана средняя толщина, и результаты показаны в c.
Средняя толщина твердых деталей. ( a ) Инвертированное двоичное изображение. ( b ) Каркас твердой части. ( c ) Средняя толщина твердых частей и соотношение площадей как функция плотности образца.
Как видно из c, средняя толщина имеет положительную корреляцию с плотностью. Это означает, что при низкой плотности образца средняя толщина твердой части будет тонкой, и наоборот. По сравнению с образцами с более высокой плотностью (D600) средняя толщина твердой части в образцах с низкой плотностью (D400, D475) уменьшается примерно на 40%. Небольшое значение толщины означает большую площадь пор. Красная кривая в c показывает тенденцию соотношения площадей пор с различной плотностью LCC. Понятно, что соотношение площадей уменьшается с увеличением плотности.Соотношение площадей имеет отрицательную корреляцию с плотностью образца.
4.1.2. Дескрипторы формы
Дескрипторы формы включают округлость, округлость и твердость. Круглость используется для описания того, насколько близко должна быть пора к истинному кругу, и определяется как отношение площади объекта к площади круга с таким же периметром. Округлость похожа на округлость, но разница в том, что округлость не учитывает локальные неровности. Округлость определяется как отношение площади объекта к площади круга с большой осью.Плотность используется для измерения плотности пор. Он определяется как отношение площади объекта к площади выпуклой оболочки объекта. показывает результаты дескрипторов формы с разной плотностью.
Данные дескрипторов формы образцов разной плотности.
Каждая точка обозначает пору. По сравнению с двумя другими образцами, D475 имеет лучшее распределение дескрипторов формы, за ним следует D600, а наихудшее — D400.
При сравнении результатов округлости трех образцов, округлость половины пор D475 находится между 0.621 и 0,732, тогда как у D400 и D600 отдельно от 0,438 до 0,589 и от 0,588 до 0,73. Высокое значение округлости означает, что пора ближе к истинному кругу. Таким образом, образец D475 имеет лучшую структуру пены, что хорошо по его механическим свойствам.
Результаты округлости показывают аналогичную тенденцию с округлостью. Разница в том, что значения округлости обычно выше, чем значения округлости, поскольку округлость не учитывает влияние локальных неровностей поры.Следовательно, округлость содержит больше информации о форме поры, и в этом исследовании округлость используется для оценки формы круга поры.
Результаты твердости образцов D475 и D600, очевидно, более значимы, чем у D400. Когда пора становится твердой, площадь поры и область выпуклой оболочки сближаются, в результате чего значение твердости равно единице. Таким образом, это означает, что поры в D475 и D600 ближе к истинному кругу, чем у D400. Кроме того, более высокое значение твердости также указывает на то, что в образце меньше соприкасающихся пор.Это согласуется с фотографиями образца, показанными на. В этом исследовании плотность в основном используется для оценки соприкасающихся пор.
4.2. Анализ результатов обработки изображений ESEM и IHDCS
Имеется шесть параллельных образцов каждой плотности, полученных IHDCS, и результаты испытаний характеристик пор показаны в. а показывает результаты соотношения площадей и средней толщины как функции плотности LCC. Соотношение площадей пор и средней толщины твердых частей сильно коррелирует с плотностью LCC.Увеличение плотности сопровождается увеличением средней толщины твердой части и уменьшением доли площади пор. Можно заметить, что существуют линейные зависимости для отношения площадей и средней толщины, где отношение площадей отрицательно коррелирует с плотностью, а средняя толщина положительно коррелирует с плотностью.
Результаты характеристики пор на основе IHDC. ( a ) Соотношение площадей и средняя толщина как функция плотности образца на основе изображений IHDCS.( b ) Дескрипторы формы образцов разной плотности на основе изображений IHDCS.
b показывает результаты округлости и твердости. Образец D475 имеет лучшие средние результаты по округлости и твердости, что означает, что форма пор в D475 более правильная и ближе к истинной окружности. Кроме того, по сравнению с двумя другими образцами с разной плотностью, D475 содержит меньше соприкасающихся пор. С другой стороны, у D400 худшие результаты по округлости и прочности.Это означает, что из-за увеличения содержания пузырьков расстояние между пузырьками уменьшается, и соседние поры легче контактируют друг с другом. В результате образуются новые поры неправильной формы, что снижает округлость и плотность. Чтобы проверить точность результатов обработки изображений, результаты IHDCS сравниваются с результатами ESEM, и результаты показаны в.
Сравнительный анализ результатов физических параметров между ESEM и IHDCS.
представляет результаты сравнения ESEM и IHDCS.В целом результаты IHDCS и ESEM претерпели схожие изменения. В частности, абсолютное значение отношения площадей пор и результаты твердости IHDCS и ESEM очень близки. Следовательно, IHDCS можно использовать для анализа соотношения площадей пузырьков LCC и состояния соприкосновения пузырьков, что позволяет получить заключение, согласующееся с выводом ESEM. С другой стороны, результаты среднего расстояния и округлости IHDCS и ESEM различаются, хотя и показывают одинаковые вариации. Результаты IHDCS больше, чем у ESEM, а отклонения среднего расстояния и округлости отдельно от 19.От 65 до 30,58 мкм и от 0,126 до 0,179. Основные причины различий в результатах заключаются в следующем: с одной стороны, по сравнению с ESEM, IHDCS получает изображения с более низким разрешением, а края идентифицированных пузырей относительно гладкие, что приводит к более высокому значению округлости; с другой стороны, изображения, полученные с помощью IHDCS, имеют больший диапазон, чем у ESEM, и каждая плотность учитывает шесть параллельных выборок. Это означает, что IHDCS получил больше образцов пузырьков, чем ESEM. Это может быть причиной разницы в результатах среднего расстояния между IHDCS и ESEM.Кроме того, результаты IHDCS, в которых учитывалось больше выборок, более репрезентативны, чем результаты ESEM.
4.3. Механический анализ
Прочность на неограниченное сжатие (UCS), модуль упругости (MoE), модуль разрыва (MoR) и предел прочности при расщеплении как функция плотности отдельно показаны на a – d. Увеличение плотности сопровождается увеличением механических свойств, что свидетельствует о положительной корреляции между механическими свойствами и плотностью. Значения механических свойств были аппроксимированы линейными функциями, как показано на этих рисунках.
Механические свойства в зависимости от плотности образца. ( a ) UCS как функция плотности образца. ( b ) MoE как функция плотности образца. ( c ) MoR как функция плотности образца. ( d ) STS как функция плотности образца.
Партия с целевой плотностью 400 кг / м 3 имела самые низкие механические свойства, и это, вероятно, отражало тот факт, что была слабая структура пены, когда образцы с низкой плотностью, с другой стороны, образцы с более высокой плотностью могли иметь лучшую или более прочную структуру пены.
Сочетая предыдущий анализ характеристик пор на ESEM и IHDC-изображении, можно выделить три возможных фактора, влияющих на механические свойства LCC. Соотношение площадей пор — очевидный фактор. Это сильно отрицательно связано с плотностью, поэтому существует крайне отрицательная связь между соотношением площадей пор и механическими свойствами LCC. Если у образцов большая доля площади пор, это означает, что образцы имеют менее твердую часть в поперечном сечении. Это также означает, что средняя толщина между порами мала.Уменьшение твердой части приводит к ухудшению механических свойств, поскольку твердая часть LCC является основной частью, несущей нагрузку.
Еще одним фактором является форма поры. Результаты округлости и твердости показали, что D475 и D600 имеют лучшую форму пор, чем D400. По сравнению с D400, формы пузырьков в D475 и D600 ближе к истинному кругу, и, кроме того, оба пузырька содержат менее соприкасающиеся пузырьки. Пузырьки регулярной формы и меньшее количество соприкасающихся пузырьков благоприятно влияют на общие механические свойства образца.Следовательно, механические свойства D475 и D600 лучше, чем D400.
Хотя округлость и прочность D475 немного лучше, чем у D600, его механические свойства не лучше, чем у D600. Основные причины: с одной стороны, по сравнению с D475, D600 имеет большую толщину сплошного материала, что улучшает механические свойства; кроме того, распределение его частиц по размеру более концентрированное, чем у D475, что также лучше с точки зрения его механических свойств.
Некоторые инженерные свойства пенобетона для устойчивого технологического развития
Дурак Дж. М. и Л. Вейкинг, (1998): Свойства вспененного бетона на основе летучей золы с воздушным отверждением для производства кирпичной кладки. В: Стр.
A, Dhanasekar M, Lawrence S, редакторы. Труды Пятой австралийской конференции масонства, 1998 г., Гладстон, Квинсленд, Австралия. п. 129-38.
Иден Н. Б., Мантроп А. Р., Миелл С. А., Шиманек П. Х. и К. Л. Уотсон (1980): Автоклавный газобетон из сланцевых отходов, Часть 1-Некоторые отношения свойств / плотности. Int J Lightweight Concr 1980; 2: 95-100.
Фаладе Ф. Потенциал латерита как мелкозернистого заполнителя при производстве пенобетона. Гражданские и экологические исследования, Том 3, № 10, 2013 г., www.iiste.org ISSN 2224-5790 (Бумага) I 2225-0514 (Онлайн).
Кирсли, Э. П. и Х. Ф. Мостерт, (1997): Пенобетон в развивающихся сообществах, Материалы симпозиума FIP 1997: Конкретный путь к развитию, Йоханнесбург, Южная Африка, март 1997 г.
Общество бетона юга Африки, 1997, стр. 735 — 745.
Лушику, М. Д. и Э. П. Кирсли (2004): Влияние состава материала на свойства сухого торкретбетона. Журнал Южноафриканского института гражданского строительства, том 46 (2) 2004 г., стр. 2–8.
Огинни, Ф.А., 2014: Применение технологии пенобетона на континенте: уроки развития инфраструктуры в Африке. Британский журнал прикладной науки и технологий 5 (4): 417-424, 2015 г., статья №.БЖАСТ.2015.040 ISSN: 2231-0843. SCIENCEDOMAIN international www.sciencedomain.org.
Pospisil F, Jambor J, and J. Belko, (1992): Снижение веса ячеистого пенобетона. В: Виттманн Ф. Х., редактор. Достижения в области автоклавного газобетона. А.А. Балкема, 1992. с. 43-52.
Потгитер, Дж. Х., Потгитер, С. С., Лубсер, М., Кирсли, Э. П., Стридом, К. А., де Ваал, Д. и С. Пол (2003): Использование летучей золы для обработки отходов производства ферросплавов.Материалы 11-й Международной конференции по химии цемента, май 2003 г., Дурбан, Южная Африка, стр. 2148–2155.
Путтаппа К.Г., Рудреш В., Ибрагим А., Мутху К.Ю., Рагхавендра Х.С. Механические свойства пенобетона. Международная конференция по строительству и строительным технологиям, ICCBT 2008 — A — (43) — стр. 491-500.
Рамамурти К. и Н. Нараянан, (1999): Влияние летучей золы на свойства пенобетона. В кн .: Материалы Международной конференции по отходам как вторичным источникам строительных материалов.Нью-Дели: BMTPC, 1999. стр. 276-82.
Руднаи, Г. (1963): Легкие бетоны, Будапешт: Akademiai Kiado. Short A и W. Kinniburgh (1963): Легкие бетоны. Издательство «Азия», 1963.
Институт бетона, (2013): Пенобетон. Опубликовано Институтом бетона, Мидранд, 2013 г. © Институт бетона P.O. Box 168, Halfway House, 1685 Block D, Lone Creek, Waterfall Park, Bekker Road, Midrand T 011 315 0300 • F 011 315 0315.
Valore RC. (1954). Ячеистый бетон, часть 1, состав и способы производства, ACI j; 50: 773-96.
Уотсон К. Л., Иден Н. Б. и Дж. Р. Фаррант (1977): Автоклавированные аэрированные материалы из сланцевого порошка и портландцемента. Precast Concr 1977: 81-5.
Уотсон К. Л. (1980): Автоклавный газобетон из сланцевых отходов, Часть 2 — Некоторые отношения свойства / пористости. Int J. Lightweight Concr 1980; 3: 121-3.
Что такое автоклавный газобетон?
Ячеистый бетон — это растущий строительный материал, особенно для зданий, которым требуется сертификация LEED.
Этот тип сборного железобетона, состоящего из натурального сырья, является строительным стандартом с середины 1920-х годов.
Предложение этого материала в качестве строительного материала может увеличить ваш доход — если у вас есть подходящее оборудование для его эффективного производства.
Давайте подробнее рассмотрим, как производится автоклавный газобетон и преимущества его использования.
Производство газобетона автоклавного типа
Этот материал, изобретенный шведским архитектором Йоханом Эрикссоном, стал побочным продуктом продолжающейся индустриализации, которую мир наблюдал с начала до середины 1900-х годов.
Изначально он был изготовлен с использованием процесса, включающего квасцы сланца; однако позже было обнаружено, что радиоактивный газ был побочным продуктом материала.
Начиная с 1975 года, в качестве заменителей использовались более безопасные вяжущие (песок, известь, алюминиевый порошок).
Материал требует производства промышленного оборудования.
В автоклавных системах используется процесс парового давления для упрочнения пенобетона после его формирования.
Кварцевый песок в смеси реагирует с гидроксидом кальция из-за огромного давления.
В результате этой реакции образуется гидрат силиката кальция, который является веществом, придающим газобетону его уникальные свойства.
Преимущества автоклавного газобетона
Материал имеет несколько уникальных характеристик, которые дают ему преимущество перед традиционным бетоном, в том числе:
- Огнестойкость.
- Уменьшенный вес.
- Эффективность нагрева и охлаждения.
- Долговечный.
- Экологичность и возможны баллы LEED.
- Изоляция (которая со временем экономит деньги ваших клиентов).
Автоклавный газобетон более хрупкий, поэтому рабочим следует обращаться с ним с особой осторожностью.
Автоклавы для пенобетона по индивидуальному заказу
Ваши потребности и технические характеристики — это план, который мы используем при проектировании и создании вашей автоклавной системы.
У индивидуальной автоклавной системы для газобетона есть несколько преимуществ, в том числе:
- Произведено в США.. Многие автоклавы, используемые для производства автоклавного ячеистого бетона в США, были произведены в европейских странах. Производство вашей автоклавной системы здесь, в США, резко сокращает время производства и транспортные расходы, связанные с доставкой автоклава на ваш объект.
- Повышенная производительность. Если производство автоклавных систем отвечает вашим уникальным потребностям, то в дальнейшем сводится к минимуму необходимость адаптировать или настраивать стандартную систему в соответствии с вашими спецификациями, что может увеличить ваши общие расходы.
- Специализированный ремонт. Нет никого, кто лучше подходил бы для обслуживания и / или ремонта вашего автоклава, чем те, кто построил его с нуля.
Вы можете получить все необходимое для вашей автоклавной системы для газобетона в нашем универсальном центре — от проектирования самой системы до трубопроводов, автоматизации и погрузочно-разгрузочных работ — для перемещения вашего газобетона на протяжении всего производственного процесса.
Мы производим каждый компонент вашего автоклава.Это также означает, что вы в надежных руках при ремонте, который потребуется вашей системе в будущем.
Требуется ли обновление вашей системы автоклавного газобетона?
Автор: Джеффри Липпинкотт
Что такое легкий бетон?
Размещено 25 апреля 2019 г.
Первое современное использование легкого бетона (LWC) было зарегистрировано в 1917 году, когда Американская корпорация аварийного флота начала строить корабли с этой смесью из-за ее высокой прочности и характеристик.С тех пор LWC стал обычным строительным материалом для возведения прочных несущих стен, мостов и канализационных систем.
Что такое легкий бетон?
Легкий бетон — это смесь, состоящая из легких крупных заполнителей, таких как сланец, глина или сланец, которые придают ему характерную низкую плотность. Конструкционный легкий бетон имеет плотность от 90 до 115 фунтов / фут3, тогда как плотность обычного бетона составляет от 140 до 150 фунтов / фут3.Это делает легкий бетон идеальным для строительства современных конструкций, требующих минимальных поперечных сечений в фундаменте. Он все чаще используется для строительства гладких фундаментов и стал жизнеспособной альтернативой обычному бетону.
Тем не менее, более высокая прочность на сжатие от 7000 до 10000 фунтов на квадратный дюйм может быть достигнута с помощью легкого бетона. Однако это может снизить плотность смеси, так как требует добавления в бетон большего количества пуццоланов и водоредуцирующих добавок.
Различия между обычным и легким бетоном
В отличие от традиционного бетона, легкий бетон имеет более высокое содержание воды. Использование пористых заполнителей увеличивает время высыхания; следовательно, чтобы решить эту проблему, заполнители предварительно замачивают в воде перед добавлением в цемент.
Как упоминалось ранее, нормальный бетон может весить от 140 до 150 фунтов / фут3 из-за наличия более плотных заполнителей в их естественном состоянии.В результате многие считают, что обычный бетон дешевле, чем LWC. Однако проекты, выполненные из обычного бетона, требуют дополнительного материала для каркаса, облицовки и стальной арматуры, что в конечном итоге увеличивает общую стоимость. Таким образом, LWC остается экономичным строительным материалом, особенно для крупных проектов.
Практическое применение легкого бетона
Одним из самых популярных сооружений, построенных из легкого бетона, является здание Банка Америки в Шарлотте, штат Нью-Йорк.C. Это показывает, как LWC можно использовать для создания внушительных конструкций, особенно с учетом того, что вероятность передачи статической нагрузки с одного этажа на другой значительно снижается.
Таким образом,LWC идеально подходит для создания дополнительных полов поверх старых или даже новых конструкций, поскольку снижает риск обрушения. Таким образом, его можно использовать для успешного строительства мостов, настилов, балок, опор, сборных железобетонных конструкций и многоэтажных зданий с пониженной плотностью. Например, использование LWC на мосту через реку Вабаш позволило строителям снизить плотность строительства на 17% и сэкономить 18% с точки зрения затрат, что составило колоссальный 1 доллар.7 миллионов.
Из-за низкой теплопроводности и более высокой термостойкости LWC теперь широко используется для изоляции водопроводных труб, стен, крыш и т. Д. Он защищает сталь от коррозии, образуя защитный слой, который также защищает стальные конструкции от гниения. LWC также обычно используется для строительства межгосударственных полос и полос движения без увеличения статической нагрузки на существующие конструкции.
Виды легкого бетона
Бетон из легкого заполнителя
Этот вид легкого бетона производится с использованием пористых и легких заполнителей, включая глину, сланец, сланец, вулканическую пемзу, ясень или перлит.В смесь также могут быть добавлены более слабые заполнители, что влияет на ее теплопроводность; однако это может снизить его силу.
Легкий заполнитель идеально подходит для сборных бетонных блоков или стальной арматуры. Однако более плотные сорта показывают лучшие результаты сцепления между сталью и бетоном, а также улучшенную защиту от коррозии стали.
Пенобетон или пенобетон
Этот тип легкого бетона также известен как газобетон или пенобетон, поскольку он создается путем введения больших пустот в массу раствора или бетона.Пустоты обычно вводятся в результате химической реакции или с использованием воздухововлекающего агента.
Газобетон или пенобетон не требует выравнивания, обладает соответствующей теплоизоляцией и самоуплотняется. Это делает его идеальным для использования в труднодоступных местах и канализационных системах.
Бетон без мелких фракций
Эта форма бетона разработана путем удаления из смеси мелких заполнителей; в результате получается бетон, который состоит только из больших пустот и крупных заполнителей.Вот почему бетон No-Fines имеет лучшую изоляцию и относительно меньшую усадку при высыхании.
БетонNo-Fines лучше всего подходит для несущих стен и может использоваться как для внутренних, так и для наружных конструкций. Однако этот тип легкого бетона не следует использовать с железобетоном, особенно из-за его более низкой плотности и содержания цемента.
Плюсы и минусы легкого бетона
Легкий бетон — это гибкий и легко транспортируемый строительный материал, который требует небольшой поддержки со стороны таких материалов, как сталь или дополнительный бетон.Это делает его рентабельным, особенно для крупных строительных проектов.
Кроме того, из-за своей низкой теплопроводности и огнестойкости LWC является идеальным материалом для изоляции от тепловых повреждений.
Несмотря на меньшую плотность, конструкции, построенные из LWC, вряд ли обрушатся. Фактически, LWC менее склонен к усадке по сравнению с обычным бетоном, а также демонстрирует повышенную устойчивость к гниению и заражению термитами.
Однако LWC также имеет несколько ограничений.Поскольку он имеет более высокое содержание воды, он высыхает дольше. Более того, добавление слишком большого количества воды может привести к образованию слоев цементного молочка, в то время как уменьшение количества воды для устранения этого ограничения может привести к более слабой смеси.
Поскольку LWC также очень пористый, правильно уложить смесь сложно. Еще одна проблема с LWC заключается в том, что цемент имеет тенденцию отделяться от заполнителей при неправильном смешивании.
В двух словах
Легкий бетон — это экономичная альтернатива обычному бетону, особенно потому, что он не снижает прочности конструкции.Более высокая пористость LWC также влияет на его теплопроводность, что делает его пригодным для проектов, требующих изоляции от теплового повреждения.
Контактная информация Specify Concrete по любым вопросам или проблемам, которые могут у вас возникнуть по поводу использования бетона.
Свойства и долговечность блоков кладки из автоклавного газобетона
Свойства и долговечность блоков из автоклавного газобетона9
А. Чайпанич2, П. Чиндапрасирт2 1 Университет Чиангмая, Чиангмай, Таиланд; 2 Университет Кхон Каен, Кхон Каен, Таиланд
9.1
Введение
В этой главе описываются различные свойства и долговечность каменных блоков из автоклавного ячеистого бетона (AAC) и содержатся следующие разделы: типы легкого бетона, история, использование, производство, механизм AAC, физические свойства, механические свойства. свойства, микроструктура, характеристики, теплопроводность и долговечность AAC. Раздел «Типы легкого бетона» описывает различные типы легкого бетона и различные производственные процессы, используемые при изготовлении легкого бетона, такого как пенобетон и пенобетон, с особым вниманием к AAC.Также упоминается использование AAC в качестве кирпичных блоков. Механизм, участвующий в производстве AAC, в зависимости от используемого метода порообразования и гидратации AAC, описан в разделе, посвященном механизму. В разделе физических свойств описывается объемная плотность AAC и его отношение к воздушным пустотам. Раздел механических свойств описывает прочность на сжатие и изгиб AAC, взаимосвязь с физическими свойствами и продуктами гидратации. Раздел микроструктуры описывает размер сформированных пор и морфологию микроструктуры AAC, охарактеризованную с помощью сканирующей электронной микроскопии (SEM), в то время как другой раздел характеризации включает использование методов дифракции рентгеновских лучей и термогравиметрического анализа.В этой главе также обсуждается теплопроводность. В разделе «Долговечность» этой главы описывается сопротивление замораживанию-оттаиванию AAC.
9.2
Типы легкого бетона
Легкий бетон можно классифицировать в соответствии с его удельным весом или плотностью, которая обычно колеблется от 320 до 1920 кг / м3, в соответствии с Руководством Комитета 213 ACI по конструкционным легким заполненным бетоном (ACI 213 , 2001). По диапазону прочности существует три различных типа легкого бетона, которые представляют собой бетоны с низкой плотностью (0.7e2,0 МПа), бетоны средней прочности (7e14 МПа) и конструкционные бетоны (17e63 МПа). Плотность этих бетонов находится в диапазоне 300e800 кг / м3, 800e1350 кг / м3 и 1350ez1920 кг / м3 соответственно. С начала 1900-х годов в Соединенных Штатах Америки используется легкий бетон, экологически чистые кирпичи и блоки для каменной кладки. http://dx.doi.org/10.1016/B978-1-78242-305-8.00009-7 Авторские права © 2015 Elsevier Ltd. Все права защищены.
216
Экологичные кирпичи и блоки для каменной кладки
и легкий бетон использовались в многоэтажных зданиях, длиннопролетных мостах, морских платформах и крупных сооружениях (Mindess, Young, & Darwin, 2003).Ряд преимуществ использования легкого бетона низкой плотности в строительстве обусловлен его низкой плотностью, низкой теплопроводностью, низкой усадкой и высокой термостойкостью, а также снижением статической нагрузки, более низкой стоимостью перевозки и более быстрым темпом строительства (Wongkeo, Thongsanitgarn , Pimraksa, & Chaipanich, 2012). Для производства легкого бетона можно использовать несколько способов, в основном с использованием легкого заполнителя или легкой матрицы. Легкий заполнитель, который можно использовать, варьируется от натурального заполнителя пемзы до искусственного агломерированного заполнителя, такого как спеченная зола (Mindess et al., 2003). Обсуждение облегченного заполнителя выходит за рамки этой главы и не будет обсуждаться более подробно. В центре внимания будет легкая цементная матрица, заполненная воздухом, которую иногда называют газобетоном или пенобетоном. Джаст и Миддендорф (2009) упростили классификацию различного пенобетона или пенобетона, который может производиться, и сделав это пенобетоном AAC или пенобетоном с воздушным отверждением. Поэтому в основном газобетон бывает двух видов: пенобетон и пенобетон.В качестве вспенивающих агентов можно использовать различные виды моющих средств, смолистого мыла, клеящих смол или белков, таких как кератин (Narayanan & Ramamurthy, 2000a). Пену можно добавлять механическими или физическими методами, как сообщают Just & Middendorf (2009). Пена, образованная механически, использует метод взбивания пенообразователя вместе, в то время как физический метод относится к добавлению уже вспененного раствора непосредственно в процессе смешивания. Было обнаружено, что последний метод дает более регулярные и стабильные поры, чем первый, который создает поры неправильной формы (Just & Middendorf, 2009).Этот пенобетон обычно отверждается на воздухе. AAC — это класс легкого бетона, который сначала создается путем создания пузырьков газа в свежем бетоне, а затем отверждается паром под высоким давлением, известным как автоклавирование. Автоклавный метод вентиляции обычно используется при производстве блоков из кирпичной кладки. Это связано с тем, что пенобетон, иногда называемый ячеистым бетоном, полученный этим методом, имеет равномерно сформированную ячеистую структуру из воздушных пустот размером 0,1-1 мм, образующихся в цементном тесте или растворах (Mindess et al., 2003).
9,3
Автоклавный газобетон (AAC) История и использование в качестве кирпичных блоков
Первое коммерческое производство AAC было в 1923 году в Швеции. С тех пор он используется более чем в 40 странах Европы, Америки, Австралии, Ближнего и Дальнего Востока. Современное использование AAC в Соединенных Штатах началось в 1990 году для жилых и коммерческих зданий (журнал Masonry, 2008; Kocí, Madera, & Cerný, 2012; Radhi, 2011). Кладочные блоки из AAC могут быть изготовлены в виде сборных строительных блоков и используются в жилищном строительстве, больницах, офисных зданиях и университетских помещениях (Hess, Kincl, Amasay, & Wolfe, 2010.). Каменные блоки из AAC имеют много преимуществ по сравнению с обычным бетоном: меньший вес (обычно весит от одной шестой до одной трети обычного бетона), более низкие затраты на строительство и обеспечивают тепловую и звукоизоляцию (Hendry, 2001; Hess et al., 2010; Клингнер, 2008). Теплоизоляция
Свойства и долговечность блоков из автоклавного газобетона
217
Рисунок 9.1 Примеры стандартного блока AAC.
собственности AAC сделало бы здания более энергоэффективными, как сообщалось в тематическом исследовании в Объединенных Арабских Эмиратах, где было обнаружено, что использование AAC снижает потребление энергии в жилом секторе примерно на 7% (Radhi, 2011).Благодаря высокой пористой структуре с содержанием воздуха 60–70%, AAC обладает способностью гасить энергию механической вибрации, обеспечивая отличную звукоизоляцию, поэтому использование AAC было бы очень подходящим для таких мест, как школы, отели и квартиры (Краткий обзор технологий, 2010 г.) . Конструкция и технические характеристики блоков для каменной кладки AAC регулируются Кодексом Объединенного комитета по стандартам кладки и стандартом ASTM C1386. Стандартный размер кирпичного блока AAC больше по сравнению с блоком бетонного блока (CMU); длина кирпичного блока AAC составляет 610 мм по сравнению с длиной 410 мм блока CMU (Hess et al., 2010). Хотя он больше по размеру, он легче, поэтому большой размер блока AAC сопоставим с блоком CMU среднего размера с точки зрения веса (Hess et al., 2010). Стандартный блок имеет толщину 50–375 мм, высоту 200 мм и длину 610 мм (Klingner, 2008). Стандартный блок AAC показан на рисунке 9.1. В целом, благодаря этим желаемым свойствам AAC, особенно его легким, тепловым и акустическим свойствам, каменный блок AAC является идеальным строительным материалом для стен во многих жилых и офисных зданиях.
9,4
Производство и механизм автоклавного газобетона
AAC обычно изготавливается из кварцевого песка, извести, цемента и алюминиевого порошка (Kurama, Topcu, & Karakurt, 2009). Гипс и зола также могут использоваться при производстве газобетонных смесей (Klingner, 2008). Алюминиевый порошок используется как воздухововлекающий (аэрирующий) или порообразующий агент и является наиболее часто используемым агентом (Narayanan & Ramamurthy, 2000a). Он основан на реакции алюминия с растворимыми щелочами в цементе с образованием небольших пузырьков водорода, как в уравнении (8.1) (Mindess et al., 2003). Это заставляет материал подниматься в форме, и после отверждения
218
Экологически эффективные кирпичи и блоки
в течение 45 минут изделия нарезаются проволокой на кусочки необходимого размера (Technology Brief, 2010). Al þ 2OH þ 2h3 O / AlðOHÞ 4 þ h3
(8.1)
Гидрат алюмината кальция (C3AH6) также может быть образован с газообразным водородом в результате реакции порошка алюминия с гидроксидом кальция, как можно увидеть в уравнении (8.2). ) (Курама и др., 2009). После этого газобетон автоклавировали в течение 8–12 часов (Technology Brief, 2010). 2AlðSÞ þ 3CaðOHÞ2 ðSÞ þ 6h3 O / 3CaO: Al2 O3: 6h3 O þ h3 ðgÞ
(8.2)
Автоклавное отверждение паром под высоким давлением используется для повышения прочности пенобетона на сжатие. Продукты AAC готовы к использованию в течение 24 часов (прочность обычно эквивалентна 28 дням отверждения при комнатной температуре). Было обнаружено, что структура фаз C-S-H изменяется под воздействием высокой температуры и давления при отверждении в автоклаве.В портландцементе вместо аморфного гидрата силиката кальция (C-S-H) образуется гидрат адикальция силиката (a-C2SH), что приводит к снижению прочности (Mindess et al., 2003). Однако в присутствии кремнезема a-C2SH превращается в тоберморит (C5S6H5) при продолжительном нагревании (Mindess et al., 2003; Yazici, 2007). Дополнительный диоксид кремния может быть доступен за счет использования пуццоланового материала в качестве дополнительного вяжущего материала. Фаза тоберморита имеет больший объем структуры, чем фаза a-C2SH, что вызывает уменьшение пористости и, как следствие, увеличение прочности на сжатие.Образование тоберморита при высокотемпературном отверждении будет зависеть от соотношения CaO / SiO2, а также от температуры, как сообщили Меллер, Кирицис и Холл (2009) и Тейлор (1997). Типичные условия, ранее использовавшиеся для AAC, находятся в диапазоне продолжительности 8–16 часов и давлении в диапазоне 4–16 МПа (Narayanan & Ramamurthy, 2000a; RILEM, 1993). h3 O
ðC3 S þ C2 SÞ / C-S-H þ CH þ S
Кремнезем
Портландцемент h3 O
CH S / C-S-H þ / C5 S6 H5
(8.3)
(8,4)
Тоберморит
9,5
Физические свойства газобетона в автоклаве
Объемная плотность образцов AAC цементного остатка (BA) была описана Wongkeo et al. (2012) путем сравнения добавления алюминиевого порошка. Насыпная плотность автоклавного легкого бетона без замены БА снизилась до 23,47% при добавлении алюминия (Al). Таким образом, было обнаружено, что добавка алюминия оказывает значительное влияние на объемную плотность автоклавного бетона.Более того, насыпная плотность зольного остатка AAC по сравнению с портландцементом AAC увеличилась с 2% до 7%, когда
Свойства и долговечность блоков из автоклавного газобетона
219
BA использовались для замены портландцемента на 10% и 30% соответственно. Увеличение объемной плотности шлакового шлака связано с образованием фазы тоберморита при использовании БА. Wongkeo & Chaipanich (2010) сообщают об объемах проницаемых пустот, полученных при использовании всех трехкомпонентных дымовых газов из портландцемента и золы кремнезема.Было обнаружено, что объем проницаемых пустот во всех образцах шлакового зольного остатка (BA) AAC уменьшался с увеличением содержания BA и добавления микрокремнезема (SF) из-за уменьшения газообразного водорода. Удельный вес БА ААК увеличивался с увеличением содержания БА. Когда SF был добавлен в количестве 2,5% и 5%, удельный вес BA AAC с SF увеличился. Таким образом, показано, что объем проницаемых пустот напрямую влияет на удельную массу всего шлакового зольного остатка.
9,6 9.6.1
Механические свойства автоклавного газобетона Прочность на сжатие
Известно, что на прочность на сжатие влияет ряд факторов, таких как внешние и внутренние факторы.Внешние факторы — это условия испытаний и отверждения, в то время как внутренние факторы включают смесь, такие как содержание воды, используемый цемент и тип заполнителя, а также их содержание, а также используемые аэрированные агенты. Пористость в результате создается этими вовлеченными факторами и напрямую влияет на результат прочности на сжатие. Следовательно, плотность продукта напрямую связана с прочностью на сжатие. Сообщается, что уменьшение плотности за счет образования крупных микропор вызывает значительное падение прочности на сжатие (CEB, 1977).Сообщается, что прочность на сжатие находится в диапазоне 3,9–8,5 МПа при плотности AAC 700 кг / м3, но снижается до 1,3–2,8 МПа при плотности 400 кг / м3 (CEB, 1977; Narayanan & Ramamurthy, 2000а). Прочность на сжатие бетона AAC, по данным Huang, Ni, Cui, Wang и Zhu (2012), составляет 4,0 МПа при плотности 610 кг / м3. В то время как Серхат Баспинар, Демир, Кахраман и Горхан (2014) сообщили о прочности на сжатие AAC в диапазоне 1,91–5,10 МПа, когда диапазон плотности составлял 590–780 кг / м3, Albayrak et al.(2007) обнаружили, что прочность на сжатие AAC находится в диапазоне от 1,1 до 5,0 МПа и в диапазоне плотности от 270 до 500 кг / м3, что свидетельствует об увеличении прочности с увеличением плотности. Хотя условия в автоклаве были разными для каждого используемого метода, в целом можно увидеть, что прочность на сжатие снижается с уменьшением плотности AAC, и, по-видимому, существует прямая связь между прочностью на сжатие AAC с его плотностью. Таблица 9.1 суммирует результаты прочности на сжатие и условия автоклавирования из предыдущих опубликованных работ.Метод автоклавирования существенно влияет на прочность на сжатие, когда при более высоких температурах и давлении достигается стабильная форма тоберморита (Narayanan & Ramamurthy, 2000a). Используемые типы цемента приводят к разной прочности на сжатие (Mindess et al., 2003). Обычный портландцемент типа I даст более слабый силикат кальция
220
Таблица 9.1
Обзор результатов прочности на сжатие Метод условий Плотность (кг / м3)
Связующее
Температура (C)
Давление (МПа)
Время (ч)
Мостафа (2005)
1.1e3.0 1.8e3.7 1.9e3.6 2.0e3.6
NA NA NA NA
C, L, AS
183
1
2 6 12 24
Albayrak et al. (2007)
1.25e3.25
270e533
Ze
200
1.5
12
Huang et al. (2012)
4.0
610.2
C, SCT, BFS, G
NA
1.35
8
Keriene et al. (2013)
2,24
451
C, L
176
0.8
20
Серхат Баспинар и др. (2014)
1.9e3.7
590e650
C, L, FA
NA
0,4
8
3.9e5.1
740e780
C, L, FA, NA
0,8
8
Цемент, Lelime, шлак с воздушным охлаждением, цезеолит, медные хвосты SCTeskarn, доменный шлак BFS, гегипс, зола FAe, дым SF-кремнезема, NA Не доступен.
Экологически эффективные кирпичи и блоки для каменной кладки
Прочность на сжатие (МПа)
Авторы
Свойства и долговечность блоков кладки из автоклавного газобетона
221
Прочность на сжатие (МПа)
140002
8 0
10 20 Зольность шламов (%)
30
Рисунок 9.2 Прочность на сжатие золы автоклавного газобетона. По материалам Wongkeo et al. (2012).
гидрат (a-C2SH), что привело к снижению прочности. Но когда присутствует дополнительный диоксид кремния, a-C2SH превращается в тоберморит (C5S6H5), что увеличивает прочность на сжатие AAC (Taylor, 1997; Yazici, 2007). Следовательно, химический состав используемого аморфного связующего оказывает значительное влияние на прочность на сжатие AAC. Было обнаружено, что прочность на сжатие шлакового зольного остатка с содержанием БА до 30% возрастает с увеличением содержания БА (Wongkeo et al., 2012), как показано на Рисунке 9.2. Повышенная прочность на сжатие является результатом образования фазы тоберморита в условиях автоклава, когда тоберморит образовывался при высокой температуре (выше 100 ° C) с CaO / SiO2 в диапазоне 0,8–1,0 (Meller et al., 2009; Taylor , 1997). Дополнительное содержание кремнезема было получено из BA, что привело к изменению соотношения CaO / SiO2, таким образом достигнув подходящего соотношения CaO / SiO2 для образования тоберморита. Фаза тоберморита имеет больший объем структуры, чем фаза a-C2SH, что вызывает уменьшение пористости и увеличение прочности на сжатие по сравнению с контрольным портландцементом AAC (Richardson, 2008; Yazici, 2007).AAC с использованием тройного цемента, состоящего из портландцемента, зольного остатка и микрокремнезема, исследовали на прочность при сжатии. Было обнаружено, что прочность на сжатие всего AAC шлака увеличивается с увеличением содержания BA и SF (Wongkeo & Chaipanich, 2010). Как правило, можно увидеть, что удельный вес имеет прямую связь с прочностью на сжатие. При добавлении SF происходит более сильная пуццолановая реакция, которая приводит к увеличению плотности зольного остатка AAC.Следовательно, ранняя прочность на сжатие шлакового зольного остатка с SF была значительно улучшена. Более того, когда Wongkeo & Chaipanich (2010) сравнили результаты прочности на сжатие образцов, отвержденных на воздухе и в автоклаве, было обнаружено, что прочность на сжатие зольного остатка AAC с добавлением SF и отвержденного в автоклаве выше, чем у соответствующих 7- и 14-дневных образцов, отвержденных на воздухе. зольный бетон. Это способствует лучшей пуццолановой реакции при автоклавировании, в результате чего образуются фазы тоберморита.Было обнаружено, что прочность на сжатие, отвержденная на воздухе в течение 28 дней, аналогична прочности на сжатие из шлакового остатка, подвергнутого автоклавированию в течение шести часов. Был сделан вывод, что одним из основных факторов, влияющих на рост прочности, являются воздушные пустоты в бетоне. Как правило, прочность на сжатие AAC через 24 часа может достигать такой же прочности, как и у бетона с нормальным отверждением через 28 дней (Mindess et al., 2003). Прочность на сжатие AAC после 8 и 12 часов автоклавирования, о которых сообщают Narayanan & Ramamurthy (2000b), оказалась выше, чем у соответствующих бетонных смесей, по сравнению с таковыми в условиях влажного отверждения через 28, 90 и 150 дней.
9.6.2
Прочность на изгиб
Сообщается, что изгибная прочность бетона AAC находится в диапазоне 0,15e0,35 (Valore, 1954). Однако, казалось бы, соотношение будет варьироваться в зависимости от материалов и условий испытаний. Например, Wongkeo et al. (2012) сообщили, что изгибная прочность находится в диапазоне 2,7-3,2 МПа, а отношение изгибной прочности к прочности на сжатие составляет от 0,24 до 0,27 в зависимости от смеси (будь то только портландцемент или пуццолан, например поскольку зольный остаток используется в качестве дополнительного вяжущего материала).
9,7
Микроструктура газобетона в автоклаве
Микроструктура AAC состоит из макропор и микропор и на нее влияет метод порообразования (Narayanan & Ramamurthy, 2000a). Размеры пор, которые первоначально образуются в результате реакции алюминия со щелочами цемента, несколько больше по размеру, как правило, в диапазоне 0,1-1,0 мм (Ioannou, Hamilton, & Hall, 2008; Mindess et al., 2003). . Размеры пор, создаваемых химически прореагировавшим агентом, таким как алюминий, или методами вспенивания, поэтому достаточно велики, чтобы их можно было увидеть и легко увидеть.Сообщается, что образование макропор происходит в процессе аэрации, в то время как микропоры появляются в стенке макропор (Alexanderson, 1979). Петров и Шлегель (1994) суммировали размер макропор и микропор как более 60 мм для первого и 50 нм или менее для последнего (Alexanderson, 1979). Также сообщалось о размерах макропор 50-500 мм (0,05-0,5 мм), образовавшихся во время аэрации (Alexanderson, 1979). Было обнаружено, что микроструктура AAC, охарактеризованная с помощью SEM, показывает, что AAC состоит из этих двух различных типов пор.Крупные поры, наблюдаемые и сообщаемые в нескольких опубликованных работах, обычно имеют круглую форму и поэтому могут иметь размер в диапазоне 0,05–1,0 мм (Alexanderson, 1979; Ionnou et al., 2008; Mindess et al., 2003; Нараянан и Рамамурти, 2000а). Между продуктами гидратации видны микропоры, которые образуются между стенками. СЭМ-микрофотографии также показывают форму таких продуктов гидратации, которые образуются после автоклавирования. Более распространенные пластинки тоберморита обычно обнаруживаются, когда в смеси достаточно кремнезема.Микроструктура AAC также будет зависеть от образующихся продуктов гидратации, которые, следовательно, во многом зависят от используемых типов и методов цемента.
Свойства и долговечность блоков из автоклавного газобетона
223
Отношение CaO / SiO2 0,83 является оптимальным для получения тоберморита 1,1 нм (Meller et al., 2009; Richardson, 2008). Было обнаружено, что портландцемент с BA и SF в зольной пыли AAC приводит к увеличению содержания реактивного SiO2 в системе и способствует образованию тоберморита (Wongkeo & Chaipanich, 2010).Образующаяся структура тоберморита придаст более плотную микроструктуру всей матрице, чем слабокристаллическое волокно, подобное C-S-H, которое в противном случае образовалось бы в нормальном портландцементе AAC.
9.8 9.8.1
Характеристики автоклавного газобетона Дифракция рентгеновских лучей
Основным продуктом реакции ААС было обнаружено и подтверждено методом дифракции рентгеновских лучей (XRD), что это группа тоберморита (Matsui et al. др., 2011; Нараянан и Рамамурти, 2000b; Вонгкео и др., 2012). Образование тоберморита будет зависеть от цементных композиций с подходящим количеством диоксида кремния и условий автоклавирования, таких как температура, как сообщают Taylor (1997) и Meller et al. (2009). Wongkeo et al. Сообщили о рентгеновских дифрактограммах зольного остатка и AAC портландцемента. (2012). Таким образом, можно наблюдать сравнение рентгеновских дифрактограмм зольного цемента AAC и портландцемента AAC, показывая различные фазы, представленные в каждом бетоне. Следы XRD портландцемента и зольного цемента AAC показали некоторые незначительные пики C3S и C2S, которые представляют собой фазы дегидратированного силиката кальция из портландцемента.Более того, тоберморит (xCaOSiO2.zh3O) можно обнаружить только в зольном остатке AAC, но не был обнаружен в портландцементе, где вместо него были обнаружены фазы Ca (OH) 2 и a-C2SH (Ca2SiO4,3h3O). Кроме того, было обнаружено, что интенсивность пиков Ca (OH) 2 снижается с увеличением содержания БА. Это связано с пуццолановой реакцией и эффектом разбавления. Сообщалось также о других гидратированных фазах, таких как эттрингит, гидрогранат и C2SH, в дополнение к CSH, Ca (OH) 2 и тобермориту, обнаруженным в цементно-песчаном и цементно-зольном пепле AAC (Narayanan & Ramamurthy, 2000b).Кус и Карлссон (2003) провели рентгеноструктурный анализ ААС, подвергшегося естественному и искусственному выветриванию, и обнаружили фазы, поскольку основными пиками в связующем (если рассматривать только его часть) являются кальцит, ангидрит и тоберморит. Пик кальцита со временем увеличивается. Это вызвано карбонизацией, при которой Ca (OH) 2 превращается в карбонат кальция. Хотя тоберморит и кальцит обычно присутствуют в системе CaO и SiO2, при наличии Al и SO3 также могут быть обнаружены другие второстепенные фазы, такие как моносульфат и каотит (Matsui et al., 2011).
9.8.2
Термогравиметрический анализ
Результаты термогравиметрического анализа (ТГА) цементного остатка золы наносятся на график в виде производных термогравиметрических кривых (ДТГ) для идентификации обнаруженных фаз Wongkeo et al. (2012). Обнаруженные фазы представляют собой гидрат силиката кальция (C-S-H) при температуре
224
Eco-ef ‑ ef ‑ ‑ циальные кирпичи и блоки
z71e86 C, гидроксид кальция (Ca (OH) 2) при z446e476 C и карбонат кальция (CaCO3) при z697e708 C.Было обнаружено, что интенсивность кривых C-S-H увеличивается с увеличением содержания БА. Это связано с увеличением присутствия фазы тоберморита, образующейся при увеличении содержания БА, что соответствует повышенной прочности образцов на сжатие. Кроме того, можно увидеть, что Ca (OH) 2 уменьшается с увеличением содержания BA из-за пуццолановой реакции, которая использовалась в реакции образования тоберморита, а также из-за эффекта разбавления, когда было использовано использование дополнительных вяжущих материалов, таких как зольный остаток. используется для замены части портландцемента.Результаты TGA для тройного цемента AAC-бетона из портландцемента, зольной пыли и микрокремнезема были опубликованы Wongkeo & Chaipanich (2010). Результаты были нанесены на график как производные, показывающие кривые DTG для трехкомпонентного цементного бетона AAC по сравнению с образцами, отвержденными на воздухе в течение 28 дней. В трехкомпонентном цементном растворе AAC кривые DTG показали наличие фаз C-S-H (фаза тоберморита), Ca (OH) 2 и CaCO3. Потеря веса фазы тоберморита была приписана дегидратации слабосвязанной молекулярной межслоевой воды (Alarcon-Ruiz, Platret, Massieu, & Ehrlacher, 2005).Считается, что эттрингит и C2ASH8 не образовывались в бетоне AAC из-за замещения Al на Si в тетраэдрическом участке тоберморита (Wongkeo & Chaipanich, 2010). Сообщалось, что это оказывает значительное влияние на химическое поведение цементного теста, включая поведение катионного и анионного обмена, растворимость и реакции, которые могут привести к задержке образования эттрингита (Shaw, Henderson, & Komanschek, 2000). Кроме того, образование групп C-A-S-H (гидрогранат) не происходит при температуре ниже 200 ° C, но вместо этого образуется тоберморит, когда кристаллизация тоберморита ускоряется, а стабильность тоберморита увеличивается, когда доступен оксид алюминия (Meller et al., 2009; Мостафа, 2005). Тоберморитовая фаза автоклавного шлака увеличивалась с увеличением содержания БА до 20%. Было обнаружено, что фаза Ca (OH) 2 уменьшается с увеличением содержания БА из-за усиления пуццолановой реакции БА и SF и эффекта разбавления.
9,9
Теплопроводность зольного цементного автоклавного газобетона
Теплопроводность бетона AAC напрямую зависит от его физических свойств. Сообщается, что теплопроводность зольного цемента AAC несколько увеличивается при использовании зольного остатка в качестве дополнительного вяжущего материала в бетоне (Рисунок 9.3), поскольку содержание БА увеличило общую удельную массу или объемную плотность бетона (Wongkeo & Chaipanich, 2010; Wongkeo et al., 2012). Пористая структура легких заполнителей, плотность бетона и цементная матрица влияют на теплопроводность бетона (Corinaldesi et al., 2011; Topcu & Uygunoglu, 2007). Таким образом, теплопроводность BLWC имела тенденцию к увеличению из-за уменьшения объема проницаемых пустот с увеличением содержания BA (Wongkeo & Chaipanich, 2010).Albayrak et al. (2007) сообщили, что прочность на сжатие и теплопроводность бетона AAC снижаются с уменьшением
Свойства и долговечность блоков из автоклавного газобетона
225
Теплопроводность (Вт / мК)
0,70
0,65
0,60
0,55
0,50 0
10 20 Зольность шлака (%)
30
Рисунок 9.3 Теплопроводность шлакового газобетона автоклавного твердения.По материалам Wongkeo et al. (2012).
насыпной плотности. Albayrak et al. (2007) обнаружили теплопроводность AAC в диапазоне 1,1e5,0 МПа и диапазоне плотности 270e500 кг / м3, показывая увеличение прочности с увеличением плотности. Несколько других исследователей (Blanco, Garcia, Mateos, & Ayala, 2000; Demirboga, 2003, 2007; Demirboga & Gul, 2003) также сообщили, что снижение теплопроводности связано с уменьшением плотности бетона. Jerman, Keppert, Vyborny, & Cerny (2013) показали, что теплопроводность зависит от плотности AAC, а также от содержания влаги (Рисунок 9.4), где увеличение влажности и плотности приводит к увеличению теплопроводности. Следовательно, известно, что теплопроводность увеличивается с увеличением плотности как обычного бетона, так и бетона AAC. Теплопроводность AAC может составлять всего 0,08 Вт / м · K при 25 C. Однако прочность на сжатие, как следствие, составляет 1,0
300 кг / м3
Теплопроводность [Вт / мК]
0,9
y = 0,1414e1,2666x R2 = 0,9174
0,8
500 кг / м3 350 кг / м3
0.7 0,6 0,5
y = 0,2811x + 0,0878 R2 = 0,972
0,4 0,3
y = 0,1049e0,6911x R2 = 0,9404
0,2 0,1 0,0 0
0,5
1 1,5 Содержание влаги [кг / кг]
2
2,5
Рисунок 9.4 Зависимость теплопроводности автоклавного газобетона от влажности. Джерман и др. (2013) напечатано с разрешения Elsevier.
226
Экологичные кирпичи и блоки для каменной кладки
очень низкие (2.05 МПа) (Jerman et al., 2013). Когда AAC с зольным остатком используется в качестве дополнительного вяжущего материала, теплопроводность находится в диапазоне 0,58–0,61 Вт / м · К (Wongkeo et al., 2012). С другой стороны, когда зольный остаток используется в качестве заполнителя, теплопроводность бетона AAC, как сообщается, находится в пределах 0,220–0,361 Вт / м · К и, как было обнаружено, уменьшается с увеличением содержания BA, используемого в качестве замены песка (Kurama et al. др., 2009). Было обнаружено, что теплопроводность всего зольного бетона AAC с SF выше, чем у контрольного бетона с портландцементом, и увеличивается с увеличением SF (Wongkeo & Chaipanich, 2010).Это связано с уменьшением объема проницаемых пустот и плотности микроструктуры в матрице цементного теста. Сообщалось, что небольшие изменения теплопроводности тройного портландцемента, зольной пыли и микрокремнезема аналогичны в диапазоне 0,61–0,65 Вт / м К. Таким образом, наблюдается прямая зависимость между теплопроводностью. и объемная плотность бетона AAC.
9,10
Долговечность автоклавного пенобетона
Поскольку в АБК есть пустоты, которые являются большими из-за образования начальной реакции аэрации, ожидается, что он будет морозоустойчивым (Mindess et al., 2003). Однако степень насыщения важна для реакций замораживания-оттаивания (Roulet, 1983), поскольку пенобетон подвержен проникновению жидкости и газа из-за своей высокой пористости, которая может вызвать повреждение бетона (Narayanan & Ramamurthy, 2000a; RILEM, 1993). Сообщается, что максимальная степень насыщения находится в диапазоне 20-40%. При более высокой степени насыщения бетон станет хрупким и полностью расколется (Roulet, 1983). Джерман и др. (2013) сообщили о морозостойкости AAC с использованием метода масштабирования, при котором образцы должны были пройти 25 и 50 циклов замораживания по 8 часов при 15 ° C и оттаивания в течение 8 часов при 20 ° C.Они тестировали образцы в различных условиях, принимая во внимание характер различных сред, таких как сухость, влажность 10% и полное насыщение. Были протестированы условия сухости и влажности 10%, так как они лучше подходят для реалистичных условий эксплуатации здания по сравнению с полностью насыщенными условиями. Потеря массы и потеря прочности на сжатие образцов, испытанных в этих условиях, нанесены на график, как показано на рисунках 9.5 и 9.6. Интересно, что сухие образцы не показывают признаков потери массы или потери прочности на сжатие после 25 циклов.Более высокий процент потери массы был обнаружен в образцах с влажностью 10% и в образцах, насыщенных капиллярной водой. С другой стороны, результаты для сухих образцов после 50 циклов показали некоторую потерю массы (0,36–0,50%) и незначительную потерю прочности на сжатие (макс. 0,10%). В образцах с содержанием влаги 10% потеря массы находится в диапазоне 1,3-1,5%, в то время как потеря прочности на сжатие выше у образца P1,8-300 (16,3%), но кажется приемлемой при 6-8%. для образцов П2-350 и П4-500. Для образцов, насыщенных капиллярами, потеря прочности на сжатие и потеря массы намного более серьезны после 50 циклов замораживания / оттаивания, особенно в P1.8-300 и P2-350, у которых потеря прочности на сжатие составляет 46,0% и 45,7% соответственно. Эти образцы, однако, имеют очень низкую прочность на сжатие первоначально 2,05 и 2,24 МПа (Jerman et al., 2013). The
Свойства и долговечность блоков из автоклавного пенобетона
Потеря массы (%)
20 15
(a)
Сухой образец (без потерь) Образец с содержанием влаги 10% Капиллярно-водонасыщенный образец
10 5
25 Потеря прочности на сжатие (%)
25
20 15
227
(b)
Сухой образец (без потерь) Образец с содержанием влаги 10% Образец, насыщенный капиллярной водой
10 5 0
0 P1.8–300
P2–350
P1.8–300
P4–500
P2–350
P4–500
Газобетон в автоклаве
Газобетон в автоклаве
25
Потеря массы ()
20 15
(a)
Сухой образец Образец с содержанием влаги 10% Капиллярно-водонасыщенный образец
10 5
Потеря прочности на сжатие (%)
Рисунок 9.5 (a) Потеря массы и (b) прочность на сжатие потеря ACC при 25 циклах.По материалам Jerman et al. (2013).
70 60 50
(б)
Сухой образец (без потерь) Образец с влажностью 10% Капиллярно-водонасыщенный образец
40 30 20 10 0
0 P1.8-300
P2-350
P4-500
Автоклавный газобетон
P1.8-300
P2-350
P4-500
Автоклавный газобетон
Рисунок 9.6 (a) Потеря массы и (b) потеря прочности на сжатие ACC при 50 циклы.По материалам Jerman et al. (2013).
P4-500 имеет прочность на сжатие 4,0, что дает меньшую потерю массы на 1,5% и меньшую потерю прочности на сжатие на 16,6%. В обеих сериях испытаний при 25 и 50 циклах результаты показывают, что степень водонасыщения оказывает значительное влияние на сопротивление замораживанию-оттаиванию бетона из AAC. Был сделан вывод, что для сухих и 10% -ных образцов замораживание-оттаивание допустимо в диапазоне прочности на сжатие 1,8–4,0 МПа (Jerman et al., 2013). Это, по-видимому, согласуется с работой Тикальского, Посписила и Макдональда (2004) по достижению хорошей морозостойкости при содержании влаги менее 16% в бетоне из AAC с объемной плотностью в диапазоне 500-600 кг / м3 и прочностью на сжатие. 1e2 МПа.Следовательно, при рассмотрении сопротивления замораживанию-оттаиванию бетона AAC решающими факторами, которые могут существенно повлиять на характеристики AAC, являются наличие воздушных пустот, степень насыщения и прочность на сжатие.
9.11
Выводы и будущие тенденции
Хотя в этой главе основное внимание уделяется свойствам и долговечности AAC, которая представляет собой обзор прошлых и недавних исследовательских работ по этой теме, будущие тенденции
228
Eco -эффективные кирпичи и блоки для каменной кладки
с использованием AAC будут во многом зависеть от применения AAC и спецификаций, требуемых строительной отраслью, а также тех, которые установлены стандартами.Исследования будут в значительной степени сосредоточены на новых науках и технологиях, ведущих к созданию инновационных продуктов AAC, с учетом требований спецификации, применения, экономических и экологических аспектов. Таким образом, при производстве AAC следует использовать новые технологии и новые материалы. Например, можно использовать другой и более подходящий источник диоксида кремния, и, если он является экологически чистым и экономичным, тем лучше. Вероятно, это причина того, почему исследования пуццолановых материалов были столь успешными и привлекли множество интересов.Следует также обратить внимание на новое рентабельное производство, не в последнюю очередь на новые материалы, такие как наноразмерные или новые отходы и побочные продукты, которые могут улучшить механические свойства и долговечность AAC.
9.12
Источники дополнительной информации и советов
Narayanan & Ramamurthy (2000a) рассмотрели работы по AAC, в которых описан ряд свойств AAC. Wongkeo и Chaipanich (2010) и Wongkeo et al. (2012) сообщили о работах по использованию пуццоланов в качестве бинарных и тройных смешанных цементов, а также о результатах механических свойств AAC.Бетон Миндесс и др. (2003) — также полезная книга для чтения, чтобы дать общее представление о легком бетоне в целом и классификации легкого бетона. Опубликованные работы Meller et al. (2009), Taylor (1997) и Richardson (2008) — другие полезные источники для чтения по гидратации силиката кальция и продуктов гидратации при различных температурах и давлении.
Ссылки ACI Committer 213. (2001). Руководство для конструкционного легкого заполнителя бетона. Фармингтон-Хиллз: Американский институт бетона.Аларкон-Руис, Л., Платре, Г., Масье, Э., и Эрлахер, А. (2005). Использование термического анализа для оценки влияния температуры на цементное тесто. Исследование цемента и бетона, 35, 609e613. Албайрак, М., Йорукоглу, А., Карахан, С., Атлихан, С., Арунтас, Х. Ю., и Гиргин, И. (2007). Влияние цеолитовой добавки на свойства автоклавного газобетона. Строительство и окружающая среда, 42, 3161e3165. Александерсон, Дж. (1979). Связь структуры и механических свойств автоклавного газобетона.Исследование цемента и бетона, 9, 507e514. Баспинар, С.М., Демир, И., Кахраман, Э., и Горхан, Г. (2014). Потенциал использования золы вместе с микрокремнеземом в производстве автоклавного газобетона. KSCE Journal of Civil Engineering, 18, 47e52. Бланко, Ф., Гарсия, П., Матеос, П., и Аяла, Дж. (2000). Характеристика и свойства легкого бетона, изготовленного из ценосфер. Исследование цемента и бетона, 30, 1715e1722. CEB. (1977). Автоклавный газобетон. Пособие по дизайну и технологии.Строительная пресса.
Свойства и долговечность блоков из автоклавного газобетона
229
Коринальдези В., Маццоли А. и Морикони Г. (2011). Механические свойства и теплопроводность растворов, содержащих частицы отработанной резины. Материалы и дизайн, 32, 1646e1650. Демирбога Р., Гуль Р. (2003). Влияние вспученного перлита, микрокремнезема, летучей золы на теплопроводность легкого бетона. Исследование цемента и бетона, 33, 723e727.Демирбога Р. (2003). Влияние минеральных добавок на теплопроводность и прочность раствора на сжатие. Энергетика и строительство, 35, 189e192. Демирбога Р. (2007). Теплопроводность и прочность на сжатие бетонной заделки с минеральными добавками. Строительство и окружающая среда, 42, 2467e2471. Хендри, А. В. (2001). Кладка стен: материалы и конструкции. Строительные и строительные материалы, 15, 323e330. Гесс, Дж. А., Кинкл, Л., Амасай, Т., и Вулф, П. (2010). Эргономическая оценка каменщиков кладки бетонных блоков и автоклавного газобетона.Прикладная эргономика, 41, 477e483. Хуанг, X., Ni, W., Cui, W., Wang, Z., & Zhu, L. (2012). Приготовление автоклавного газобетона из медных хвостов и доменного шлака. Строительные и строительные материалы, 27, 1e5. Иоанну И., Гамильтон А. и Холл К. (2008). Капиллярное поглощение воды и н-декана автоклавным газобетоном. Исследование цемента и бетона, 38, 766e771. Джерман, М., Кепперт, М., Выборный, Дж., И Черни, Р. (2013). Гигрические, термические и прочностные свойства автоклавного газобетона.Строительные и строительные материалы, 41, 352e359. Just, A., & Middendorf, B. (2009). Микроструктура высокопрочного пенобетона. Характеристики материалов, 60, 741e748. Кериене Дж., Клигис М., Лаукайтис А., Яковлев Г., Спокаускас А. и Алекневичюс М. (2013). Влияние добавки многослойных углеродных нанотрубок на свойства неавтоклавированных и автоклавных газобетонов. Строительные и строительные материалы, 49, 527e535. Клингнер, Р. Э. (2008). Правильно использовать автоклавный газобетон.Журнал MASONRY: голос масонской индустрии. http://www.masonrymagazine.com/6-08/autoclaved. html. Коси В., Мадера Дж. И Черны Р. (2012). Системы наружной теплоизоляции для ограждающих конструкций зданий AAC: расчетный анализ, направленный на увеличение срока службы. Энергетика и строительство, 47, 84e90. Курама, Х., Топчу, И. Б., и Каракурт, К. (2009). Свойства автоклавного газобетона, полученного из зольного остатка. Журнал технологий обработки материалов, 209, 767e773. Кус, Х., И Карлссон, Т. (2003). Микроструктурные исследования автоклавного газобетона, подвергшегося естественному и искусственному выветриванию. Исследование цемента и бетона, 33, 1423e1432. Мацуи К., Кикума Дж., Цунашима М., Исикава Т., Мацуно С., Огава А. и др. (2011). Дифракция рентгеновских лучей с временным разрешением на месте образования тоберморита в автоклавном газобетоне: влияние реакционной способности источника кремнезема и добавления алюминия. Исследование цемента и бетона, 41, 510e519. Меллер, Н., Кирицис, К., и Холл, К. (2009).Минералогия гидрокерамической системы CaOeAl2O3eSiO2eh3O (CASH) от 200 до 350 C. Исследования цемента и бетона, 39, 45e53. Миндесс, С., Янг, Дж. Ф. и Дарвин, Д. (2003). Конкретный. США: Pearson Education. Мостафа, Н. Ю. (2005). Влияние воздушно-охлаждаемого шлака на физико-химические свойства автоклавного газобетона. Исследование цемента и бетона, 35, 1349e1357.
230
Экологичные кирпичи и блоки для каменной кладки
Нараянан Н. и Рамамурти К. (2000a). Структура и свойства газобетона: обзор.Цемент и бетонные композиты, 22, 321e329. Нараянан, Н., и Рамамурти, К. (2000b). Микроструктурные исследования ячеистого бетона. Исследование цемента и бетона, 30, 457e464. Петров И. и Шлегель Э. (1994). Применение автоматического анализа изображений для исследования конструкции автоклавного газобетона. Исследование цемента и бетона, 24, 830e840. Радхи, Х. (2011). Жизнеспособность стен из автоклавного пенобетона для жилого сектора в Объединенных Арабских Эмиратах. Энергетика и строительство, 43, 2086e2092.Ричардсон, И. Г. (2008). Силикат кальция гидраты. Исследование цемента и бетона, 38, 137e158. Рекомендуемая практика RILEM. (1993). Автоклавный газобетон — свойства, испытания и проектирование. E&FN SPON. Руле, К. А. (1983). Расширение газобетона от мороза — определение критического насыщения. В Ф. Х. Виттманне (ред.), Протоколы автоклавного газобетона, влажности и свойств (стр. 157e169). Амстердам: Эльзевир. Шоу, С., Хендерсон, К. М. Б., и Команшек, Б. У. (2000).Механизмы дегидратации / перекристаллизации, энергия и кинетика гидратированных минералов силиката кальция: исследование in situ TGA / DSC и синхротронного излучения SAXS / WAXS. Химическая геология, 167, 141e159. Тейлор, Х. Ф. У. (1997). Цементная химия. Нью-Йорк: Краткий технологический обзор Тейлора и Томаса Телфорд Сервисез Лтд. (2010). Кирпичные блоки из автоклавного газобетона. Информация о ресурсах от Международного института масонства. Доступно по адресу: http://www.imiweb.org/design_ tools / tech_briefs / 01.02% 20AAC% 20MASONRY% 20UNITS.pdf Дата обращения 14.04.2014. Тикальский П. Дж., Посписил Дж. И Макдональд В. (2004). Метод оценки морозостойкости выполненного пенобетона. Исследование цемента и бетона, 34, 889e893. Топчу, И. Б., & Уйгуноглу, Т. (2007). Свойства автоклавного бетона на легком заполнителе. Строительство и окружающая среда, 42, 4108e4116. Валор Р. К. (1954). Ячеистый бетон. Физические свойства. Журнал Американского института бетона, 25, 817e836. Вонгкео, В., и Чайпанич, А.(2010). Прочность на сжатие, микроструктура и термический анализ легкого конструкционного бетона, подвергнутого автоклавному и воздушному отверждению, на основе зольного остатка угля и микрокремнезема. Материаловедение и инженерия A, 527, 3676e3684. Wongkeo, W., Thongsanitgarn, P., Pimraksa, K., & Chaipanich, A. (2012). Прочность на сжатие, изгибная прочность и теплопроводность автоклавного бетонного блока, изготовленного с использованием золы в качестве заменителя цемента. Материалы и дизайн, 35, 434e439.